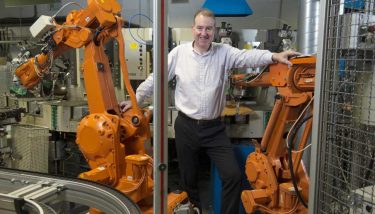
DFSS is a design technique that uses a variety to design a product. It is intended to reduce waste, improve quality and increase market share. This is a powerful method that will help you improve the quality of your products and services.
DFSS is a process that takes customer needs into account throughout the design process. This ensures the product or service that you design meets your customer's requirements. You can also guarantee that your product is high-quality when it's introduced to the market. DFSS is used often to design a product/service from scratch. You can also use it to create products and services to replace existing products.
The DFSS team will determine what the customer wants and needs in the initial phase. This might include gathering information about current processes, interviewing clients, and conducting customer surveys. The design team will then assess alternative products and designs in order to determine the best fit. This phase includes the development and classification of functional requirements, as well as substitute concepts. Depending on the complexity and scope of the project, additional steps may be necessary.
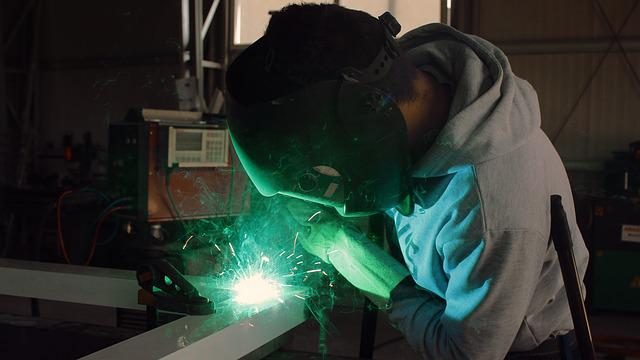
DFSS, a design methodology, is used to help companies design products or services efficiently and effectively. It can also be used to identify potential issues before they become serious problems. It can also help reduce waste and increase profitability. It's designed to enhance the effectiveness and efficiency of a product or service through identifying process parameters that can make it more effective.
There are several methods for implementing DFSS. DMADV is one of the most widely used methods. This involves a five step process. The process begins with the definition of the customer and their needs. Next, they create a design concept. This methodology has a strong engineering foundation and is often used in the development of completely new products and services. This includes a measurement phase and an analysis phase to determine the product's effectiveness.
The optimization step is the second phase. This involves evaluating the product's performance across multiple performance levels. This step is crucial for the development of new business procedures. This stage's goal is to reduce variation and ensure product stability over time.
The final stage involves the verification stage, which is often used to ensure that the product is stable. This is also used to confirm that the product's capabilities have been tested and verified over time. Validation testing is also part of this process. After the design is validated, validation testing is often completed.
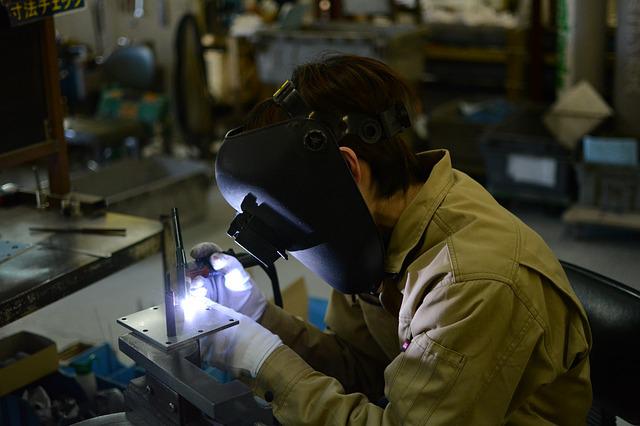
You will be able to implement DFSS successfully if you have a detailed process diagram that shows all the steps involved in the design. Also, you should have information on resources, timelines, milestones, and other details. It's also necessary to identify external involvement. To ensure the product meets customer needs, you may need to create a prototype. It is also beneficial to implement DFSS within an environment that offers clear rewards for achieving the goals of your project.
FAQ
What are the products and services of logistics?
Logistics refers to the movement of goods from one place to another.
They include all aspects associated with transport including packaging, loading transporting, unloading storage, warehousing inventory management customer service, distribution returns and recycling.
Logisticians ensure that the product is delivered to the correct place, at the right time, and under safe conditions. Logisticians assist companies in managing their supply chains by providing information such as demand forecasts, stock levels and production schedules.
They can also track shipments in transit and monitor quality standards.
How can we improve manufacturing efficiency?
First, identify the factors that affect production time. Next, we must find ways to improve those factors. You can start by identifying the most important factors that impact production time. Once you identify them, look for solutions.
What are the 7 Rs of logistics.
The acronym 7R's for Logistics stands to represent the seven basic principles in logistics management. It was developed by the International Association of Business Logisticians (IABL) and published in 2004 as part of its "Seven Principles of Logistics Management" series.
The acronym is composed of the following letters.
-
Responsible - ensure that actions are in compliance with legal requirements and do not cause harm to others.
-
Reliable: Have faith in your ability or the ability to honor any promises made.
-
Use resources effectively and sparingly.
-
Realistic - consider all aspects of operations, including cost-effectiveness and environmental impact.
-
Respectful - show respect and treat others fairly and fairly
-
Be resourceful: Look for opportunities to save money or increase productivity.
-
Recognizable - provide customers with value-added services.
What are manufacturing and logistic?
Manufacturing is the process of creating goods from raw materials by using machines and processes. Logistics manages all aspects of the supply chain, including procurement, production planning and distribution, inventory control, transportation, customer service, and transport. Logistics and manufacturing are often referred to as one thing. It encompasses both the creation of products and their delivery to customers.
What does warehouse mean?
A warehouse is a place where goods are stored until they are sold. It can be either an indoor or outdoor space. In some cases, it may be a combination of both.
Statistics
- Job #1 is delivering the ordered product according to specifications: color, size, brand, and quantity. (netsuite.com)
- According to a Statista study, U.S. businesses spent $1.63 trillion on logistics in 2019, moving goods from origin to end user through various supply chain network segments. (netsuite.com)
- It's estimated that 10.8% of the U.S. GDP in 2020 was contributed to manufacturing. (investopedia.com)
- In 2021, an estimated 12.1 million Americans work in the manufacturing sector.6 (investopedia.com)
- [54][55] These are the top 50 countries by the total value of manufacturing output in US dollars for its noted year according to World Bank.[56] (en.wikipedia.org)
External Links
How To
Six Sigma: How to Use it in Manufacturing
Six Sigma refers to "the application and control of statistical processes (SPC) techniques in order to achieve continuous improvement." Motorola's Quality Improvement Department developed it at their Tokyo plant in Japan in 1986. Six Sigma's basic concept is to improve quality and eliminate defects through standardization. Many companies have adopted this method in recent years. They believe there is no such thing a perfect product or service. The main goal of Six Sigma is to reduce variation from the mean value of production. This means that if you take a sample of your product, then measure its performance against the average, you can find out what percentage of the time the process deviates from the norm. If this deviation is too big, you know something needs fixing.
Understanding the nature of variability in your business is the first step to Six Sigma. Once you have a good understanding of the basics, you can identify potential sources of variation. This will allow you to decide if these variations are random and systematic. Random variations are caused when people make mistakes. While systematic variations are caused outside of the process, they can occur. For example, if you're making widgets, and some of them fall off the assembly line, those would be considered random variations. If however, you notice that each time you assemble a widget it falls apart in exactly the same spot, that is a problem.
Once you've identified the problem areas you need to find solutions. The solution could involve changing how you do things, or redesigning your entire process. After implementing the new changes, you should test them again to see if they worked. If they didn't work, then you'll need to go back to the drawing board and come up with another plan.