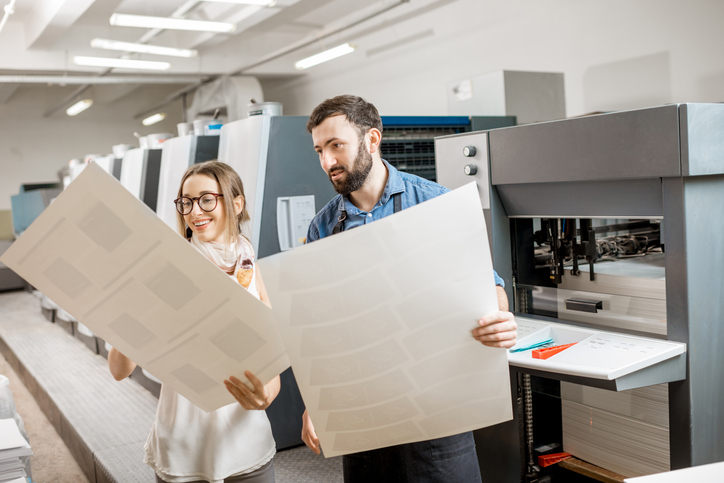
You will study microscopic forms and life processes as a microbiologist. This includes studying interactions between organisms as well as their interactions with one another. These microscopic organisms include bacteria, fungi, parasites, and algae. These life forms are what make up our food, our bodies, and it's not surprising that microbiologists have such an important role.
Education Required
Microbiologists study microscopic organisms and their processes. These microorganisms could include bacteria, yeast, parasites and algae. Microbiologists investigate how microscopic organisms behave and how they interact.
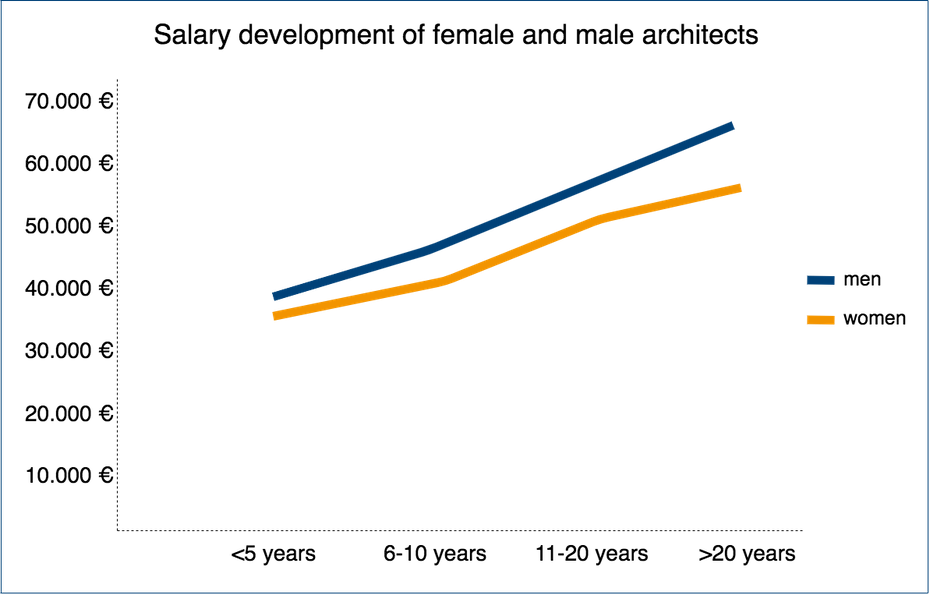
A microbiologist has to be detail-oriented and able to write and present research findings. They must also have the ability to manage and motivate their team. Because they often need to use complex math equations to calculate results it is important that they have a solid math background.
Doing job
Microbiologists are responsible for identifying and tracking microorganisms across a variety of environments. Their work can also help develop new medicines, vaccines, and ways to prevent disease. They also supervise lab work, conduct research, and write reports. They use advanced microscopes and specialist software to analyze and collect data. Their work demands attention to detail and they must be able collaborate with large research groups.
Microbiologists are microbiologists who study microbes. They can work in a clinical lab or in an environment. Environmental microbiologists study the interaction of microorganisms in soil and water. Industrial microbiologists examine how microbes affect crop growth and the efficiency of industrial processes. They may study microbial growth in pipes or oversee microbial activities during the manufacturing of cheese.
Salary
The average Microbiologist salary was $81,668 per year in 2004. That figure is expected rise to $121,130 by 2021. Microbiologists might choose to do research, but also to be a part of scientific publishing, pharmaceutical sales, or patent work. A steady increase in employment in this field is due to the growing demand for microbiologists.
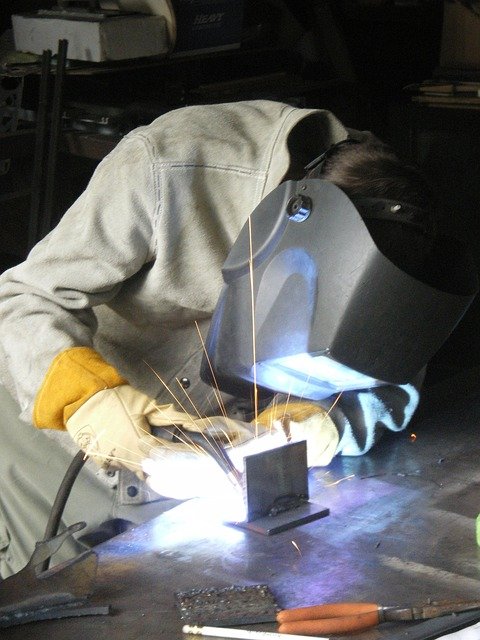
Most microbiologists work in research or labs, whether in an industrial setting or in academic institutions. Many of them work with dangerous organisms, so they must follow strict safety procedures to prevent contamination. Others may visit work locations or collect samples from the environment. Some might even travel occasionally.
FAQ
How can we reduce manufacturing overproduction?
Better inventory management is key to reducing excess production. This would reduce time spent on activities such as purchasing, stocking, and maintaining excess stock. This would allow us to use our resources for more productive tasks.
You can do this by adopting a Kanban method. A Kanbanboard is a visual tool that allows you to keep track of the work being done. A Kanban system allows work items to move through several states before reaching their final destination. Each state has a different priority level.
As an example, if work is progressing from one stage of the process to another, then the current task is complete and can be transferred to the next. A task that is still in the initial stages of a process will be considered complete until it moves on to the next stage.
This allows for work to continue moving forward, while also ensuring that there is no work left behind. A Kanban board allows managers to monitor how much work is being completed at any given moment. This data allows them adjust their workflow based upon real-time data.
Another way to control inventory levels is to implement lean manufacturing. Lean manufacturing focuses on eliminating waste throughout the entire production chain. Anything that does nothing to add value to a product is waste. Some common types of waste include:
-
Overproduction
-
Inventory
-
Packaging not required
-
Excess materials
Manufacturers can reduce their costs and improve their efficiency by using these ideas.
How does a production planner differ from a project manager?
The difference between a product planner and project manager is that a planer is typically the one who organizes and plans the entire project. A production planner, however, is mostly involved in the planning stages.
What are manufacturing and logistic?
Manufacturing refers the process of producing goods from raw materials through machines and processes. Logistics manages all aspects of the supply chain, including procurement, production planning and distribution, inventory control, transportation, customer service, and transport. As a broad term, manufacturing and logistics often refer to both the creation and delivery of products.
Statistics
- [54][55] These are the top 50 countries by the total value of manufacturing output in US dollars for its noted year according to World Bank.[56] (en.wikipedia.org)
- In the United States, for example, manufacturing makes up 15% of the economic output. (twi-global.com)
- In 2021, an estimated 12.1 million Americans work in the manufacturing sector.6 (investopedia.com)
- According to the United Nations Industrial Development Organization (UNIDO), China is the top manufacturer worldwide by 2019 output, producing 28.7% of the total global manufacturing output, followed by the United States, Japan, Germany, and India.[52][53] (en.wikipedia.org)
- It's estimated that 10.8% of the U.S. GDP in 2020 was contributed to manufacturing. (investopedia.com)
External Links
How To
Six Sigma and Manufacturing
Six Sigma is "the application statistical process control (SPC), techniques for continuous improvement." Motorola's Quality Improvement Department created Six Sigma at their Tokyo plant, Japan in 1986. The basic idea behind Six Sigma is to improve quality by improving processes through standardization and eliminating defects. Many companies have adopted Six Sigma in recent years because they believe that there are no perfect products and services. Six Sigma's primary goal is to reduce variation from the average value of production. If you take a sample and compare it with the average, you will be able to determine how much of the production process is different from the norm. If this deviation is too big, you know something needs fixing.
The first step toward implementing Six Sigma is understanding how variability works in your business. Once you understand this, you can then identify the causes of variation. You'll also want to determine whether these variations are random or systematic. Random variations occur when people do mistakes. Symmetrical variations are caused due to factors beyond the process. You could consider random variations if some widgets fall off the assembly lines. But if you notice that every widget you make falls apart at the exact same place each time, this would indicate that there is a problem.
Once you've identified the problem areas you need to find solutions. That solution might involve changing the way you do things or redesigning the process altogether. To verify that the changes have worked, you need to test them again. If they didn't work, then you'll need to go back to the drawing board and come up with another plan.