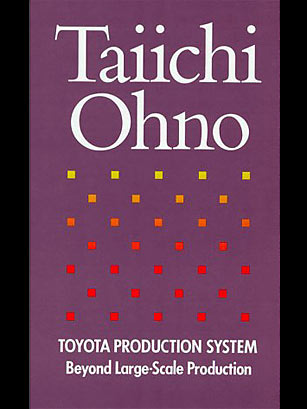
When you want to ensure that your product is profitable, you need to think about the manufacturing cost. For example, if you want to sell wooden tabletops furniture, you might need to purchase wood glue and other materials. You need to find a reliable supplier of the best quality raw material so that your end product will last. If you do not use high quality materials, you could be left with a broken item and lost revenue.
It is best to divide manufacturing cost into three major categories. Each of these types of costs will affect the final price of the product that you are selling. The unit cost is a key component of manufacturing costs. It's the cost it takes to produce an item. This number is a good way to begin, but it is not easy to determine.
It is a good idea to use the units-perhour (or unit-perunit ratio) as a guideline when choosing the most cost-effective manufacturing process. If you plan to make 5,000 wooden tables, the cost per unit can be calculated by adding up the hours required for each one.
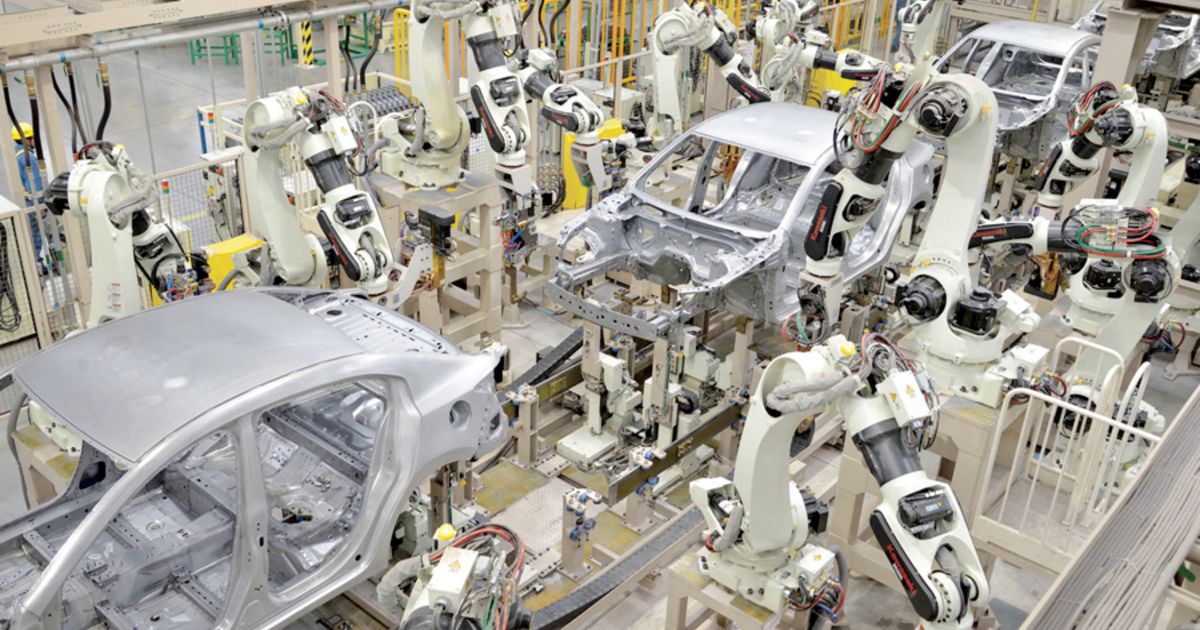
In addition to direct labor and manufacturing equipment, you'll also need to budget for administrative and general expenses. These can include advertising costs, office supplies, rent, and sales commissions. For regulatory compliance, you will have to spend a lot. Online inventory control software can be used to track and forecast production.
Direct labor costs are the wages paid to workers in a factory, and includes employees engaged in the actual preparation of the goods for manufacturing. They may also include maintenance staff, sanitation personnel, and bookkeepers. In general, the hourly wage for direct labor is around $150.
Indirect costs, which are part manufacturing, include utilities bills and equipment maintenance. To calculate the unit-per-hour you need to include the costs of preparation, assembly and delivery. The manufacturing overhead account can be used to estimate your overhead for the next fiscal year and calculate the total cost of your operations.
Consider the direct and indirect materials used to make a product. These materials include wood, thread and cotton. The use of low quality materials can lead you to poor products. Food producers in certain countries will need testing to ensure your products are safe to eat.
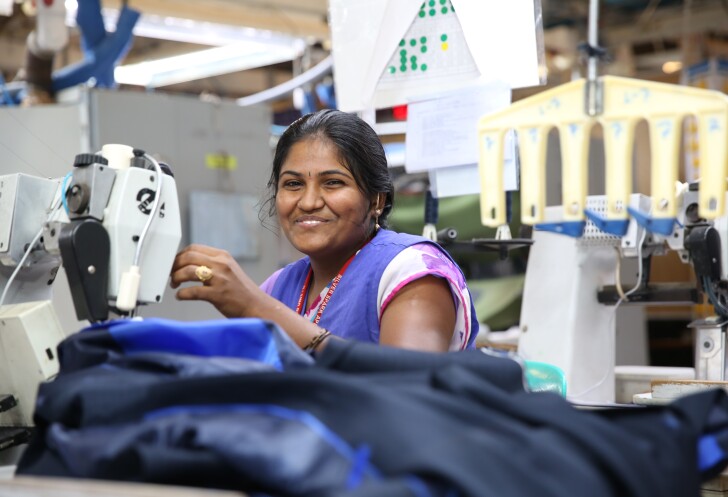
It is important to determine whether you should begin producing new products by knowing how much each unit costs. It's also a smart idea to figure out how much you should be charging for your products, so that your business is more profitable.
FAQ
What skills should a production planner have?
To become a successful production planner, you need to be organized, flexible, and able to multitask. Communication skills are essential to ensure that you can communicate effectively with clients, colleagues, and customers.
What are the 4 types of manufacturing?
Manufacturing refers the process of turning raw materials into useful products with machines and processes. Manufacturing involves many activities, including designing, building, testing and packaging, shipping, selling, service, and so on.
What is the responsibility for a logistics manager
A logistics manager makes sure that all goods are delivered on-time and in good condition. This is done using his/her knowledge of the company's products. He/she should ensure that sufficient stock is available in order to meet customer demand.
Statistics
- Job #1 is delivering the ordered product according to specifications: color, size, brand, and quantity. (netsuite.com)
- You can multiply the result by 100 to get the total percent of monthly overhead. (investopedia.com)
- In the United States, for example, manufacturing makes up 15% of the economic output. (twi-global.com)
- (2:04) MTO is a production technique wherein products are customized according to customer specifications, and production only starts after an order is received. (oracle.com)
- It's estimated that 10.8% of the U.S. GDP in 2020 was contributed to manufacturing. (investopedia.com)
External Links
How To
Six Sigma and Manufacturing
Six Sigma is defined as "the application of statistical process control (SPC) techniques to achieve continuous improvement." It was developed by Motorola's Quality Improvement Department at their plant in Tokyo, Japan, in 1986. Six Sigma's main goal is to improve process quality by standardizing processes and eliminating defects. Since there are no perfect products, or services, this approach has been adopted by many companies over the years. The main goal of Six Sigma is to reduce variation from the mean value of production. This means that you can take a sample from your product and then compare its performance to the average to find out how often the process differs from the norm. If you notice a large deviation, then it is time to fix it.
Understanding the nature of variability in your business is the first step to Six Sigma. Once you have this understanding, you will need to identify sources and causes of variation. You'll also want to determine whether these variations are random or systematic. Random variations occur when people do mistakes. Symmetrical variations are caused due to factors beyond the process. For example, if you're making widgets, and some of them fall off the assembly line, those would be considered random variations. However, if you notice that every time you assemble a widget, it always falls apart at exactly the same place, then that would be a systematic problem.
Once you've identified where the problems lie, you'll want to design solutions to eliminate those problems. It might mean changing the way you do business or redesigning it entirely. After implementing the new changes, you should test them again to see if they worked. If they didn't work, then you'll need to go back to the drawing board and come up with another plan.