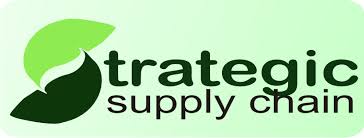
Logistics is an essential part of any supply chain. All products need to be moved from one location to the other. Logistics is an essential component in every company's operation in today’s fast-paced world. A highly trained workforce is essential for effective logistics. Logistic supply chains include the efficient and timely movement and information of goods, resources, and information. But what exactly is logistics? This article will explore some important aspects in logistic supply chain.
Logistics is the movement between point A and point B of products.
The process of moving goods from point A to B is called logistics. These tasks are managed by logistics professionals. When moving products from one place to the next, they must take into account many details. They must choose the most cost-effective shipping method, evaluate the product's weight, and ensure that the final price reflects the full shipment. They also need to consider customer satisfaction, warehousing and other factors that contribute to full loaded costs.
It is an essential part of a supply chain
The logistics process includes identifying problems within the supply chain and finding solutions. These problem areas are typically associated with waste and high costs. A product might be ordered in large quantities but then sits on a shelf for several days. This can lead to significant costs for transportation companies. Overproduction can also cause problems, as companies produce more products than they need. This causes wasted resources and can impact the market's pricing.
It requires a skilled workforce
For a logistics supply chain, it is essential to have a qualified workforce. The logistics facility will run smoothly if it has a skilled workforce. For exceeding expectations, employees should be recognized. Total Logistics Solutions consultants actually work in warehouses to understand how the process works from the user's point of view. It's also beneficial to understand your competition. It is worth hiring Total Logistics Solutions consultants to help make this happen.
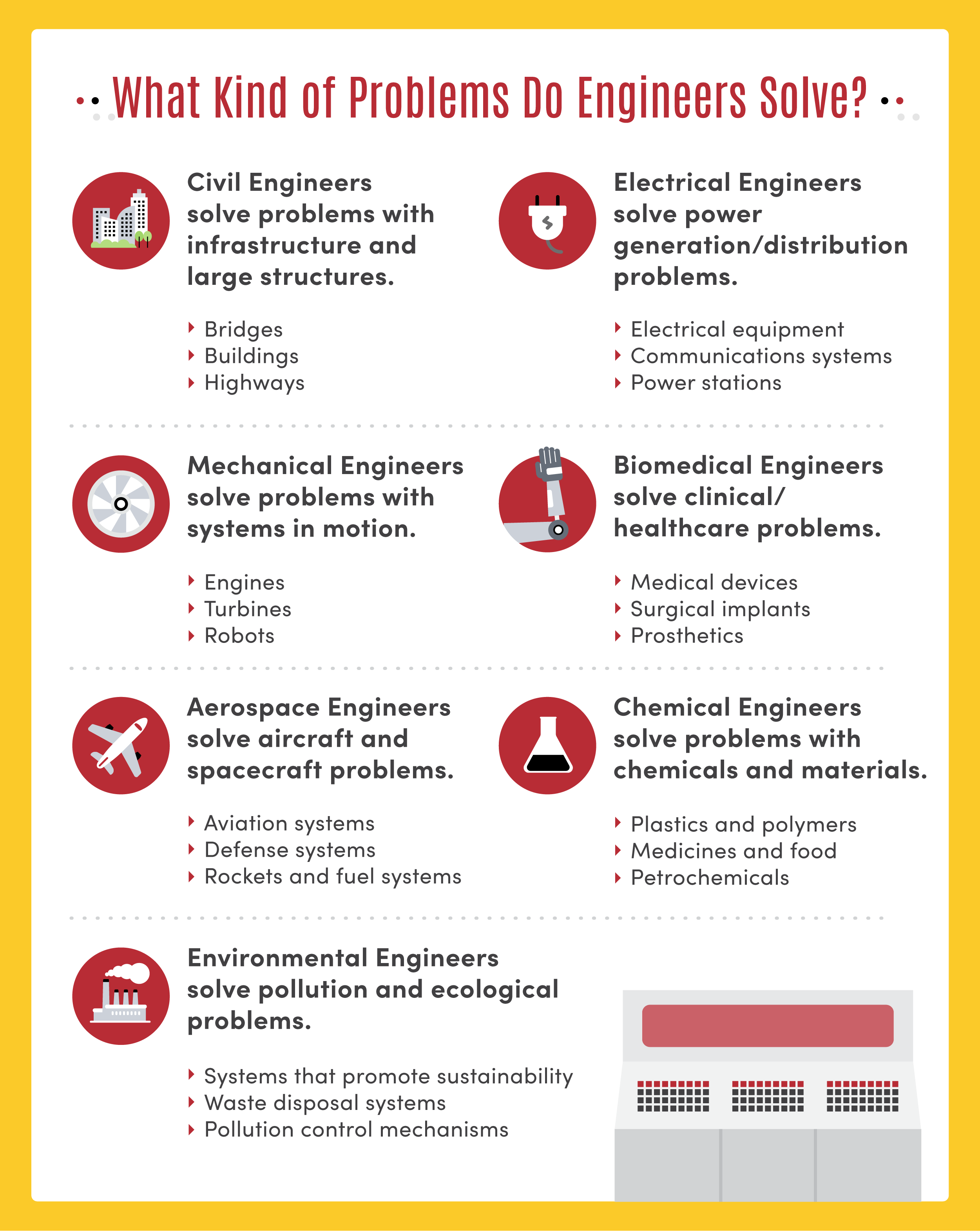
It requires technology
The logistics industry must be competitive. Technological advances are changing not only the industry's landscape but also how it operates. The logistics industry is changing with the advent of advanced analytics, additive manufacturing, automation, and other technological advances. As a result, autonomous vehicles will increase in warehouses. Warehouse management and warehousing strategies will also undergo significant changes. These advancements will ultimately make logistics more cost-effective and efficient for businesses.
FAQ
What types of jobs can you find in logistics
There are many types of jobs in logistics. Here are some examples:
-
Warehouse workers - They load and unload trucks and pallets.
-
Transportation drivers – These drivers drive trucks and wagons to transport goods and pick up the goods.
-
Freight handlers - They sort and pack freight in warehouses.
-
Inventory managers - They oversee the inventory of goods in warehouses.
-
Sales representatives: They sell products to customers.
-
Logistics coordinators: They plan and manage logistics operations.
-
Purchasing agents are those who purchase goods and services for the company.
-
Customer service agents - They answer phone calls and respond to emails.
-
Shipping clerks – They process shipping orders, and issue bills.
-
Order fillers are people who fill orders based only on what was ordered.
-
Quality control inspectors - They check incoming and outgoing products for defects.
-
Others - There are many other types of jobs available in logistics, such as transportation supervisors, cargo specialists, etc.
What are the products of logistics?
Logistics is the process of moving goods from one point to another.
They include all aspects of transport, including packaging, loading, transporting, unloading, storing, warehousing, inventory management, customer service, distribution, returns, and recycling.
Logisticians ensure that the product is delivered to the correct place, at the right time, and under safe conditions. They assist companies with their supply chain efficiency through information on demand forecasts. Stock levels, production times, and availability.
They coordinate with vendors and suppliers, keep track of shipments, monitor quality standards and perform inventory and order replenishment.
What's the difference between Production Planning & Scheduling?
Production Planning (PP) refers to the process of determining how much production is needed at any given moment. Forecasting and identifying production capacity are two key elements to this process.
Scheduling refers to the process of allocating specific dates to tasks in order that they can be completed within a specified timeframe.
What is the responsibility of a manufacturing manager?
A manufacturing manager must ensure that all manufacturing processes are efficient and effective. They should also be aware of any problems within the company and act accordingly.
They should also be able communicate with other departments, such as sales or marketing.
They should be informed about industry trends and be able make use of this information to improve their productivity and efficiency.
What is production planning?
Production Planning is the creation of a plan to cover all aspects, such as scheduling, budgeting. Location, crew, equipment, props and other details. This document will ensure everything is in order and ready to go when you need it. This document should also include information on how to get the best result on set. This information includes locations, crew details and equipment requirements.
First, you need to plan what you want to film. You might have an idea of where you want to film, or you may have specific locations or sets in mind. Once you have identified the scenes and locations, you can start to determine which elements are required for each scene. Perhaps you have decided that you need to buy a car but aren't sure which model. To narrow your options, you can search online for available models.
After you've found the perfect car, it's time to start thinking about adding extras. Do you need people sitting in the front seats? You might also need someone to help you get around the back. Perhaps you would like to change the interior colour from black to white. These questions can help you decide the right look for your car. The type of shots that you are looking for is another thing to consider. You will be filming close-ups and wide angles. Maybe you want the engine or the steering wheels to be shown. These details will help identify the exact car you wish to film.
Once you have established all the details, you can create a schedule. A schedule will tell you when you need to start shooting and when you need to finish. A schedule for each day will detail when you should arrive at the location and when you need leave. It will help everyone know exactly what they have to do and when. Hire extra staff by booking them ahead of time. It's not worth paying someone to show up if you haven't told him.
It is important to calculate the amount of filming days when you are creating your schedule. Some projects only take one or two days, while others may last weeks. When you are creating your schedule, you should always keep in mind whether you need more than one shot per day or not. Multiple shots at the same location can increase costs and make it more difficult to complete. If you aren't sure whether you need multiple shots, it is best to take fewer photos than you would like.
Budget setting is another important aspect in production planning. As it will allow you and your team to work within your financial means, setting a realistic budget is crucial. Remember that you can always reduce the budget later on if you run into unforeseen problems. However, you shouldn't overestimate the amount of money you will spend. If you underestimate how much something costs, you'll have less money to pay for other items.
Production planning is a complicated process. But once you understand how everything works together, it becomes much easier to plan future project.
What are the four types in manufacturing?
Manufacturing refers to the transformation of raw materials into useful products by using machines and processes. Manufacturing can include many activities such as designing and building, testing, packaging shipping, selling, servicing, and other related activities.
Statistics
- It's estimated that 10.8% of the U.S. GDP in 2020 was contributed to manufacturing. (investopedia.com)
- You can multiply the result by 100 to get the total percent of monthly overhead. (investopedia.com)
- According to a Statista study, U.S. businesses spent $1.63 trillion on logistics in 2019, moving goods from origin to end user through various supply chain network segments. (netsuite.com)
- In the United States, for example, manufacturing makes up 15% of the economic output. (twi-global.com)
- Job #1 is delivering the ordered product according to specifications: color, size, brand, and quantity. (netsuite.com)
External Links
How To
How to use Lean Manufacturing in the production of goods
Lean manufacturing is an approach to management that aims for efficiency and waste reduction. It was first developed in Japan in the 1970s/80s by Taiichi Ahno, who was awarded the Toyota Production System (TPS), award from KanjiToyoda, the founder of TPS. The first book published on lean manufacturing was titled "The Machine That Changed the World" written by Michael L. Watkins and published in 1990.
Lean manufacturing refers to a set of principles that improve the quality, speed and costs of products and services. It is about eliminating defects and waste from all stages of the value stream. The five-steps of Lean Manufacturing are just-in time (JIT), zero defect and total productive maintenance (TPM), as well as 5S. Lean manufacturing eliminates non-value-added tasks like inspection, rework, waiting.
Lean manufacturing not only improves product quality but also reduces costs. Companies can also achieve their goals faster by reducing employee turnover. Lean manufacturing has been deemed one of the best ways to manage the entire value-chain, including customers, distributors as well retailers and employees. Lean manufacturing can be found in many industries. For example, Toyota's philosophy underpins its success in automobiles, electronics, appliances, healthcare, chemical engineering, aerospace, paper, food, etc.
Lean manufacturing is based on five principles:
-
Define value - Find out what your business contributes to society, and what makes it different from other competitors.
-
Reduce Waste - Remove any activity which doesn't add value to your supply chain.
-
Create Flow - Make sure work runs smoothly without interruptions.
-
Standardize & simplify - Make processes consistent and repeatable.
-
Build relationships - Develop and maintain personal relationships with both your internal and external stakeholders.
Lean manufacturing is not a new concept, but it has been gaining popularity over the last few years due to a renewed interest in the economy following the global financial crisis of 2008. Many businesses have adopted lean manufacturing techniques to help them become more competitive. Many economists believe lean manufacturing will play a major role in economic recovery.
Lean manufacturing is now becoming a common practice in the automotive industry, with many benefits. These include higher customer satisfaction levels, reduced inventory levels as well as lower operating costs.
The principles of lean manufacturing can be applied in almost any area of an organization. This is because it ensures efficiency and effectiveness in all stages of the value chain.
There are three main types:
-
Just-in-Time Manufacturing: Also known as "pull systems", this type of lean manufacturing uses just-in-time manufacturing (JIT). JIT is a method in which components are assembled right at the moment of use, rather than being manufactured ahead of time. This approach aims to reduce lead times, increase the availability of parts, and reduce inventory.
-
Zero Defects Manufacturing: ZDM ensures that no defective units leave the manufacturing plant. If a part is required to be repaired on the assembly line, it should not be scrapped. This is true even for finished products that only require minor repairs prior to shipping.
-
Continuous Improvement (CI), also known as Continuous Improvement, aims at improving the efficiency of operations through continuous identification and improvement to minimize or eliminate waste. Continuous improvement involves continuous improvement of processes and people as well as tools.