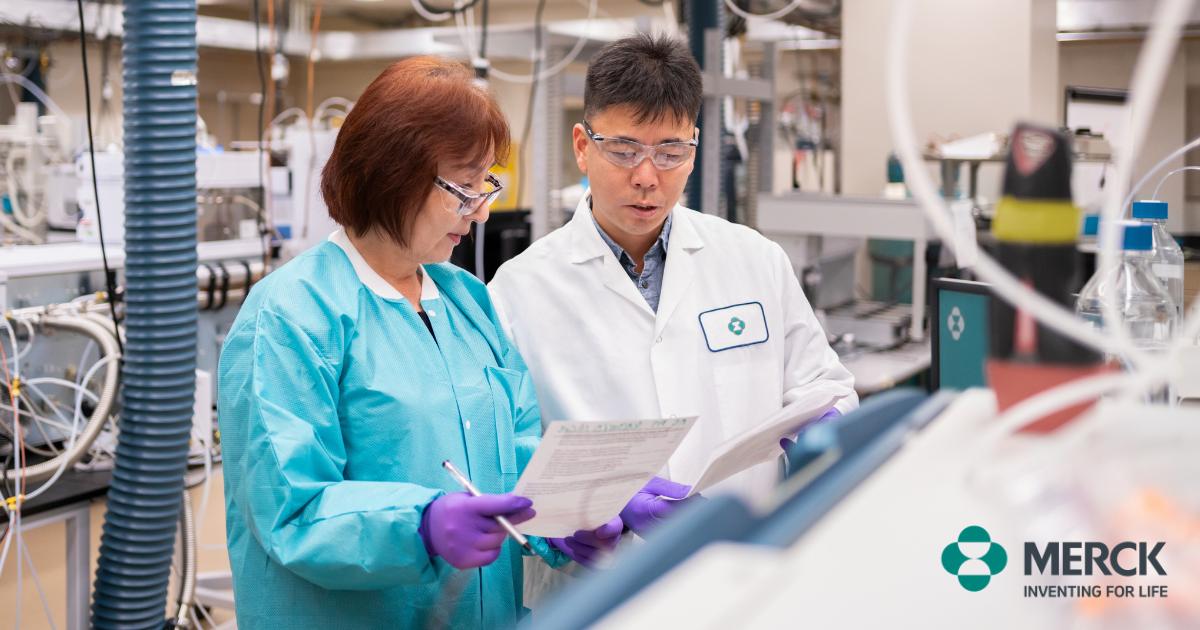
Material managers are responsible for purchasing and delivering materials. They typically come from either inventory or the management of raw materials. They are able to identify the different raw materials needed to create a product. They need to be resourceful in finding these raw materials. To get the best price, and delivery rate, they need to have good working relationships with vendors. A materials manager's salary is important. Below are some tips for getting the job.
Job description
Materials managers are responsible for managing stock and purchasing. He or she must have a thorough understanding of stock management and excellent problem-solving skills. A material manager manages inventory, budgets, as well as efficiencies. The job description of a material manager includes the management of inventory. This role also requires coordination of the supply chain and supervision for subordinates. This role requires an advanced degree. In addition, the materials manager must have experience in a similar role.
Materials managers typically have a bachelor's in business administration or a related field. However, if the position requires a supervisor, a master's degree in a related field is advantageous. An advanced degree is not always more valuable than on-the-job experience. However, education is a plus. A materials manager must have at least three years experience in an industrial or manufacturing setting before applying to a managerial job.
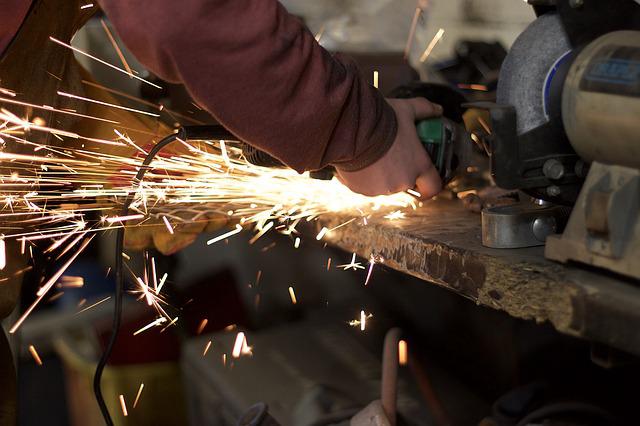
Responsibilities
Materials managers have the responsibility of evaluating current projects and determining which materials are required for the production process. He or she also keeps track of inventory through the company's supply chain management system, and may be responsible for maintaining stock of spare parts for repairing faulty products. They may also be responsible training employees in inventory control. These positions are important in many companies. However, not all of these require extensive training.
Job description: A material manager oversees the procurement of materials for a company. The material manager also oversees the distribution and storage of these materials. Experience in logistics, inventory control, supply chain management and logistics are required for this job. Experience in these areas will be an advantage. They will also collaborate with the vendors, purchasing and production departments to identify requirements and plan distribution. This position requires a bachelor's in business and strong analytical skills.
Education is required
Consider the educational requirements for a job as a material manager if you're interested in this career. This position requires management skills and an understanding of logistics and receiving. As a material manger, you will work closely with QC employees and higher-ranking management. Plan functions and delegating to subordinates are some of the job duties. You must be able to evaluate the performance of your subordinates and foster harmonious work relationships.
Materials managers usually have a Bachelor's Degree in a related area. Some companies also require that a materials manager has at least two years' experience before hiring someone with that education. Higher-level positions may require additional education. Many material managers hold certifications, such as those offered by the American Purchasing Society (CPSCP) and the APICS (the Association of Purchasing Professionals).
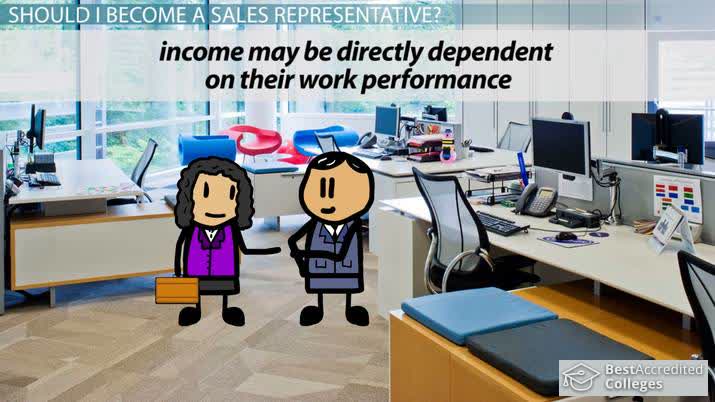
Salary
A Materials Manager's average annual salary is $78,500. This number is based on the salaries of 106 TurboTax users. This includes tips, taxable wages, bonuses and other compensation. The salary ranges from $25,000 to $168,000 depending on education and experience. Inflation is taken into account when the salary data are rounded annually. To learn more about the salary range for Materials Managers, click here.
You will need to have some management experience in order to be a materials manager. It is important to have an understanding of logistics, shipping, and receiving. If you're in the manufacturing industry, you should also have some understanding of the industry you'd like to work in. This will help you negotiate the most favorable prices with suppliers. The type of training and experience a materials manager has will determine the salary they earn.
FAQ
What are the 4 types of manufacturing?
Manufacturing is the process by which raw materials are transformed into useful products through machines and processes. Manufacturing involves many activities, including designing, building, testing and packaging, shipping, selling, service, and so on.
Are there any Manufacturing Processes that we should know before we can learn about Logistics?
No. You don't have to know about manufacturing processes before learning about logistics. Knowing about manufacturing processes will help you understand how logistics works.
What are manufacturing and logistic?
Manufacturing refers to the process of making goods using raw materials and machines. Logistics covers all aspects involved in managing supply chains, including procurement and production planning. Sometimes manufacturing and logistics are combined to refer to a wider term that includes both the process of creating products as well as their delivery to customers.
What is the distinction between Production Planning or Scheduling?
Production Planning (PP), or production planning, is the process by which you determine what products are needed at any given time. Forecasting demand is one way to do this.
Scheduling involves the assignment of dates and times to tasks in order to complete them within the timeframe.
How can manufacturing excess production be decreased?
In order to reduce excess production, you need to develop better inventory management methods. This would reduce the time spent on unproductive activities like purchasing, storing and maintaining excess stock. This could help us free up our time for other productive tasks.
A Kanban system is one way to achieve this. A Kanban board is a visual display used to track work in progress. In a Kanban system, work items move through a sequence of states until they reach their final destination. Each state represents an individual priority level.
As an example, if work is progressing from one stage of the process to another, then the current task is complete and can be transferred to the next. A task that is still in the initial stages of a process will be considered complete until it moves on to the next stage.
This allows work to move forward and ensures that no work is missed. A Kanban board allows managers to monitor how much work is being completed at any given moment. This information allows them to adjust their workflow based on real-time data.
Lean manufacturing is another option to control inventory levels. Lean manufacturing focuses on eliminating waste throughout the entire production chain. Anything that does not contribute to the product's value is considered waste. The following are examples of common waste types:
-
Overproduction
-
Inventory
-
Unnecessary packaging
-
Material surplus
Manufacturers can increase efficiency and decrease costs by implementing these ideas.
What is the job of a logistics manger?
Logistics managers ensure that goods arrive on time and are unharmed. This is done through his/her expertise and knowledge about the company's product range. He/she must also ensure sufficient stock to meet the demand.
How does a production planner differ from a project manager?
A production planner is more involved in the planning phase of the project than a project manger.
Statistics
- According to a Statista study, U.S. businesses spent $1.63 trillion on logistics in 2019, moving goods from origin to end user through various supply chain network segments. (netsuite.com)
- You can multiply the result by 100 to get the total percent of monthly overhead. (investopedia.com)
- Job #1 is delivering the ordered product according to specifications: color, size, brand, and quantity. (netsuite.com)
- It's estimated that 10.8% of the U.S. GDP in 2020 was contributed to manufacturing. (investopedia.com)
- Many factories witnessed a 30% increase in output due to the shift to electric motors. (en.wikipedia.org)
External Links
How To
How to use lean manufacturing in the production of goods
Lean manufacturing is a management style that aims to increase efficiency and reduce waste through continuous improvement. It was developed by Taiichi Okono in Japan, during the 1970s & 1980s. TPS founder Kanji Takoda awarded him the Toyota Production System Award (TPS). Michael L. Watkins published the book "The Machine That Changed the World", which was the first to be published about lean manufacturing.
Lean manufacturing is often described as a set if principles that help improve the quality and speed of products and services. It emphasizes the elimination of defects and waste throughout the value stream. Lean manufacturing is called just-in-time (JIT), zero defect, total productive maintenance (TPM), or 5S. Lean manufacturing emphasizes reducing non-value-added activities like inspection, rework and waiting.
In addition to improving product quality and reducing costs, lean manufacturing helps companies achieve their goals faster and reduces employee turnover. Lean manufacturing is considered one of the most effective ways to manage the entire value chain, including suppliers, customers, distributors, retailers, and employees. Lean manufacturing practices are widespread in many industries. Toyota's philosophy is the foundation of its success in automotives, electronics and appliances, healthcare, chemical engineers, aerospace, paper and food, among other industries.
Five basic principles of Lean Manufacturing are included in lean manufacturing
-
Define Value- Identify the added value your company brings to society. What makes you stand out from your competitors?
-
Reduce waste - Get rid of any activity that does not add value to the supply chain.
-
Create Flow: Ensure that the work process flows without interruptions.
-
Standardize & Simplify - Make processes as consistent and repeatable as possible.
-
Build Relationships - Establish personal relationships with both internal and external stakeholders.
Although lean manufacturing has always been around, it is gaining popularity in recent years because of a renewed interest for the economy after 2008's global financial crisis. Many businesses have adopted lean manufacturing techniques to help them become more competitive. Economists think that lean manufacturing is a crucial factor in economic recovery.
Lean manufacturing is now becoming a common practice in the automotive industry, with many benefits. These include improved customer satisfaction, reduced inventory levels, lower operating costs, increased productivity, and better overall safety.
It can be applied to any aspect of an organisation. Because it makes sure that all value chains are efficient and effectively managed, Lean Manufacturing is particularly helpful for organizations.
There are three main types of lean manufacturing:
-
Just-in Time Manufacturing (JIT), also known as "pull system": This form of lean manufacturing is often referred to simply as "pull". JIT is a method in which components are assembled right at the moment of use, rather than being manufactured ahead of time. This strategy aims to decrease lead times, increase availability of parts and reduce inventory.
-
Zero Defects Manufacturing - ZDM: ZDM focuses its efforts on making sure that no defective units leave a manufacturing facility. If a part is required to be repaired on the assembly line, it should not be scrapped. This also applies to finished products that need minor repairs before being shipped.
-
Continuous Improvement: Continuous Improvement aims to improve efficiency by continually identifying problems and making adjustments to eliminate or minimize waste. Continuous improvement involves continuous improvement of processes and people as well as tools.