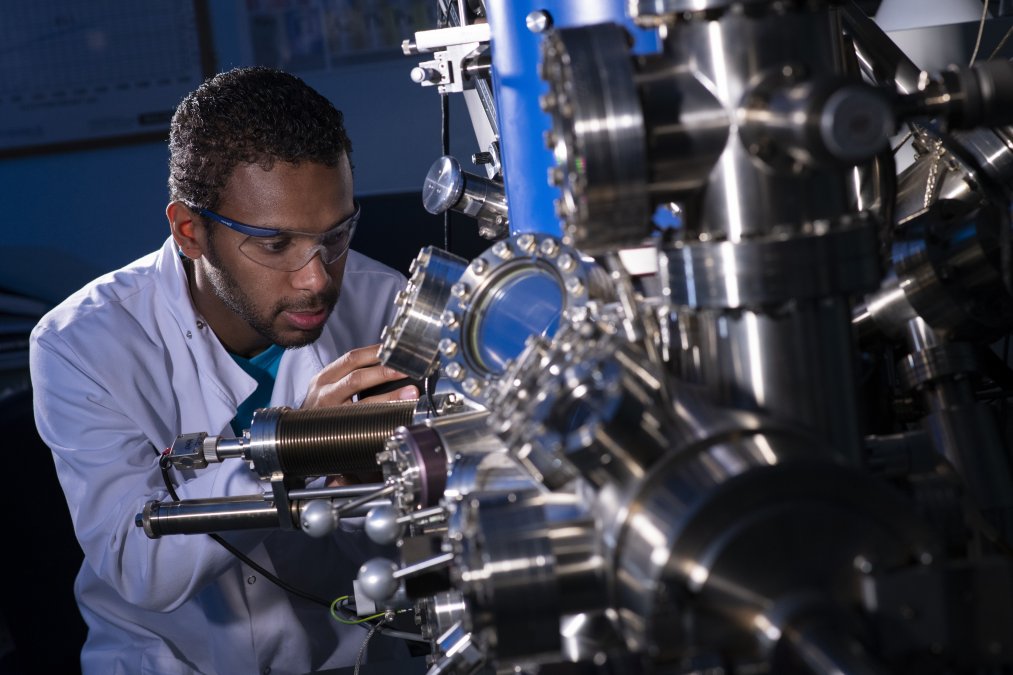
Art Byrne served as the CEO of Wiremold. He introduced several innovations that allowed the company to achieve its goal of reducing cost and increasing productivity. Byrne displayed a keen understanding and ability to motivate the entire team through this case study in lean manufacturing. Byrne encouraged all members of his team to practice the lean manufacturing techniques and invited them to join the kaizen project.
He developed a lean process that tracked the flow and quality of parts during manufacturing. He also introduced a variety of tools to reduce waste and increase productivity. He also introduced a laser-cutting machine that made it possible to produce small batches and save on tooling. His success was due a lean strategy, which included just a few simple steps.
He also developed a JIT (just in time) manufacturing process. This manufacturing method allowed the company's vehicles to be delivered quickly. This allowed for harmony in the manufacturing process which was key to reducing waste.
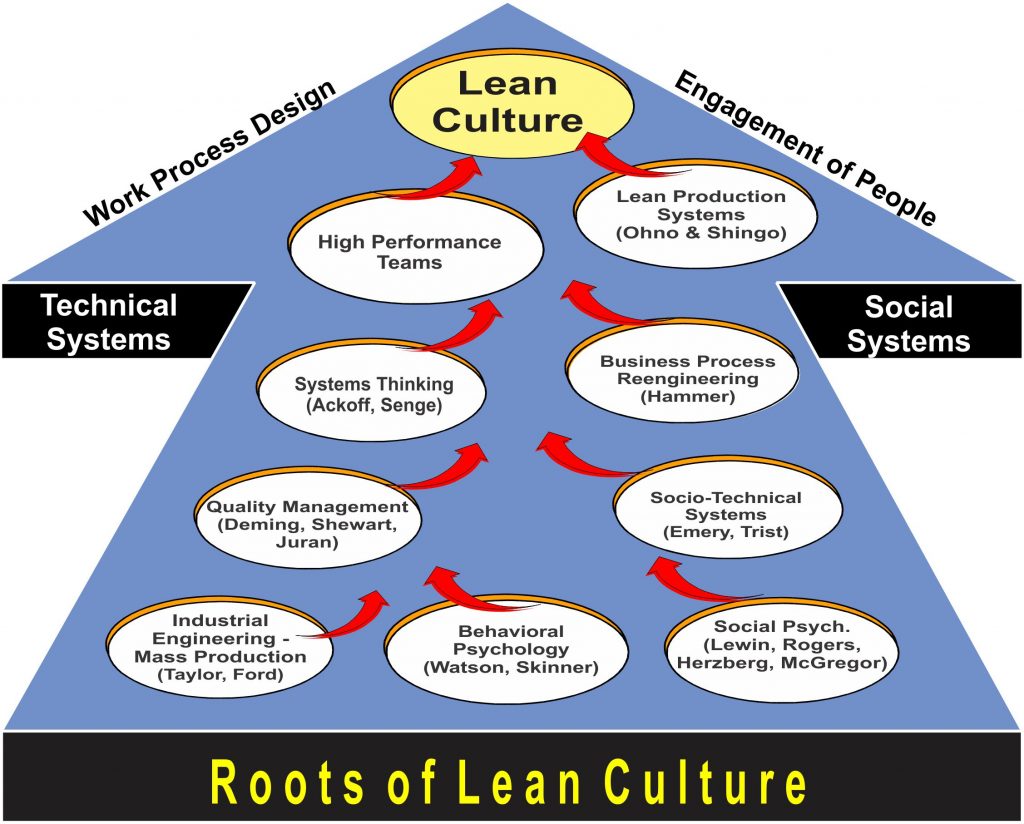
He was open to problem solving and developed a tool maintenance plan that saved the company $2 million during the recession. He also established an early retirement program for unionized employees. These moves helped him transform Wiremold from a haphazard, inefficient company into a Lean-oriented one.
In addition to the aforementioned plan, he introduced a system for monitoring the flow of raw materials throughout the manufacturing process. He also implemented a brand new ERP system. He made sure his employees understood the importance and value of respecting their colleagues. His lean strategies were simple and effective, allowing him to make sure all employees understood the concept of kaizen. His management style promoted respect for people and an active approach.
His best asset was his knowledge of the kaizen process. Danaher Corporation was his previous employer, so he knew that a good Kaizen includes the three P's, people, process, and product. He also managed to reduce the number of salaried staff. His kaizen strategy allowed him to make sure that his team was successful.
He also introduced value stream mapping. This diagram illustrates the impact of manufacturing resources on overall company efficiency. He also introduced the concept of a Kaizen event worksheet, which can be used to track key improvement activities. The chart displays the overall achievements.
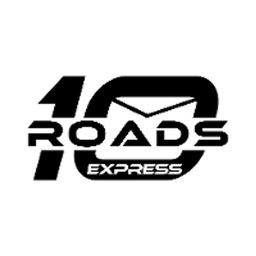
He also implemented a system for reducing lead time, which is important for the manufacturing industry. The fine blanking machine produced 600 to 800-blades per hour. This machine also eliminates the need to do a lot more manual work. Another tool used to reduce lead time was the kanban card.
Wiremold was a leader in conduit casing manufacturing. After the company underwent a major overhaul under Art Byrne, sales skyrocketed from 100 million dollars to 450 million dollars in just ten years. The company was bought out by French competitor Legrand in 2001. Wiremold didn't always succeed in its journey. The biggest problem with the system was its queue processing. This left stations with too little or too much work.
FAQ
What are the essential elements of running a logistics firm?
It takes a lot of skills and knowledge to run a successful logistics business. To communicate effectively with clients and suppliers, you must be able to communicate well. It is important to be able to analyse data and draw conclusions. You must be able manage stress and pressure under pressure. You must be creative and innovative to develop new ideas to improve efficiency. You need to have strong leadership qualities to motivate team members and direct them towards achieving organizational goals.
It is important to be organized and efficient in order to meet tight deadlines.
How can I find out more about manufacturing?
Practical experience is the best way of learning about manufacturing. You can read books, or watch instructional videos if you don't have the opportunity to do so.
How can manufacturing efficiency be improved?
The first step is to identify the most important factors affecting production time. We must then find ways that we can improve these factors. If you don’t know where to begin, consider which factors have the largest impact on production times. Once you've identified them all, find solutions to each one.
Is there anything we should know about Manufacturing Processes prior to learning about Logistics.
No. It doesn't matter if you don't know anything about manufacturing before you learn about logistics. Understanding the manufacturing process will allow you to better understand logistics.
What types of jobs can you find in logistics
There are different kinds of jobs available in logistics. Some of them are:
-
Warehouse workers – They load, unload and transport pallets and trucks.
-
Transportation drivers – These drivers drive trucks and wagons to transport goods and pick up the goods.
-
Freight handlers - They sort and pack freight in warehouses.
-
Inventory managers: They are responsible for the inventory and management of warehouses.
-
Sales representatives - They sell products to customers.
-
Logistics coordinators: They plan and manage logistics operations.
-
Purchasing agents are those who purchase goods and services for the company.
-
Customer service representatives - Answer calls and email from customers.
-
Shipping clerks – They process shipping orders, and issue bills.
-
Order fillers: They fill orders based off what has been ordered and shipped.
-
Quality control inspectors: They inspect outgoing and incoming products for any defects.
-
Others - There are many other types of jobs available in logistics, such as transportation supervisors, cargo specialists, etc.
What is production planning?
Production Planning is the creation of a plan to cover all aspects, such as scheduling, budgeting. Location, crew, equipment, props and other details. This document will ensure everything is in order and ready to go when you need it. It should also contain information on achieving the best results on set. This includes location information, crew details, equipment specifications, and casting lists.
First, you need to plan what you want to film. You might have an idea of where you want to film, or you may have specific locations or sets in mind. Once you have identified your locations and scenes it's time to begin figuring out what elements you will need for each one. Perhaps you have decided that you need to buy a car but aren't sure which model. You could look online for cars to see what options are available, and then narrow down your choices by selecting between different makes or models.
After you have selected the car you want, you can begin to think about additional features. Are you looking for people to sit in the front seats? Maybe you need someone to move around in the back. You might want to change your interior color from black and white. These questions will help you determine the exact look and feel of your car. It is also worth considering the types of shots that you wish to take. Will you be filming close-ups or wide angles? Maybe you want the engine or the steering wheels to be shown. These details will help identify the exact car you wish to film.
Once you have established all the details, you can create a schedule. You can create a schedule that will outline when you must start and finish your shoots. You will need to know when you have to be there, what time you have to leave and when your return home. So everyone is clear about what they need to do. It is possible to make arrangements in advance for additional staff if you are looking to hire. There is no point in hiring someone who won't turn up because you didn't let him know.
Also, consider how many days you will be filming your schedule. Some projects are quick and easy, while others take weeks. When you are creating your schedule, you should always keep in mind whether you need more than one shot per day or not. Multiple takes at the same place will result in higher costs and longer completion times. If you are unsure if you need multiple takes, it is better to err on the side of caution and shoot fewer takes rather than risk wasting money.
Budget setting is an important part of production planning. A realistic budget will help you work within your means. You can always lower the budget if you encounter unexpected problems. However, it is important not to overestimate the amount that you will spend. You will end up spending less money if you underestimate the cost of something.
Production planning is a detailed process. But, once you understand the workings of everything, it becomes easier for future projects to be planned.
Statistics
- According to the United Nations Industrial Development Organization (UNIDO), China is the top manufacturer worldwide by 2019 output, producing 28.7% of the total global manufacturing output, followed by the United States, Japan, Germany, and India.[52][53] (en.wikipedia.org)
- In 2021, an estimated 12.1 million Americans work in the manufacturing sector.6 (investopedia.com)
- In the United States, for example, manufacturing makes up 15% of the economic output. (twi-global.com)
- [54][55] These are the top 50 countries by the total value of manufacturing output in US dollars for its noted year according to World Bank.[56] (en.wikipedia.org)
- (2:04) MTO is a production technique wherein products are customized according to customer specifications, and production only starts after an order is received. (oracle.com)
External Links
How To
Six Sigma in Manufacturing:
Six Sigma is "the application statistical process control (SPC), techniques for continuous improvement." Motorola's Quality Improvement Department in Tokyo, Japan developed Six Sigma in 1986. Six Sigma is a method to improve quality through standardization and elimination of defects. Many companies have adopted Six Sigma in recent years because they believe that there are no perfect products and services. Six Sigma's main objective is to reduce variations from the production average. If you take a sample and compare it with the average, you will be able to determine how much of the production process is different from the norm. If it is too large, it means that there are problems.
Understanding the nature of variability in your business is the first step to Six Sigma. Once you have this understanding, you will need to identify sources and causes of variation. Also, you will need to identify the sources of variation. Random variations occur when people do mistakes. Symmetrical variations are caused due to factors beyond the process. If you make widgets and some of them end up on the assembly line, then those are considered random variations. You might notice that your widgets always fall apart at the same place every time you put them together.
Once you identify the problem areas, it is time to create solutions. This could mean changing your approach or redesigning the entire process. Once you have implemented the changes, it is important to test them again to ensure they work. If they don’t work, you’ll need to go back and rework the plan.