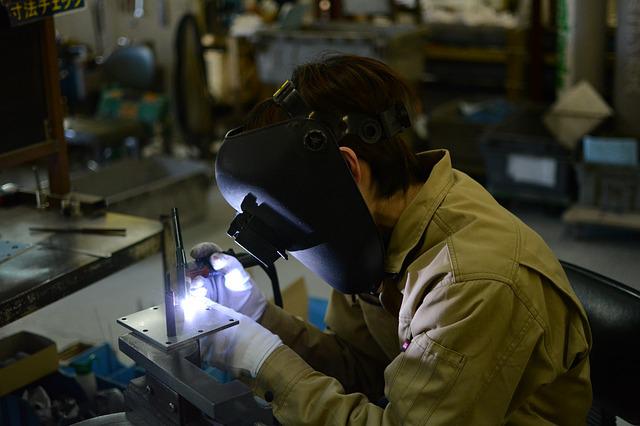
A paper company is an industrial firm that produces papers like newsprint, tissue and paperboard. They may also produce packaging such as bags and shipping boxes. They are typically based in the United States.
The paper sector is a significant part of American economic activity. It produces billions of dollars of goods each year and employs tens of thousands of people. Their products are used for all aspects of modern life, such as consumer goods, commercial applications, and industrial uses.
There are many paper companies in the United States. Some of them are more regionally oriented, while others specialize in particular types of products.
No matter where they are located, all of these companies share a common objective: creating and providing products that consumers can use in everyday life. Some of the companies are also concerned with environmental sustainability.
International Paper, and WestRock are two of the largest paper companies in USA. Both companies are ranked on the Fortune 500 list and are among the world's largest paper companies.
International Paper dominates the paper industry because it has the largest portfolio of forest lands in the United States. It owns over 42 million acre of forest in the U.S. and is home to a large number of pulp paper and containerboard production plants throughout North America.
International Paper's strong focus on diversification is one of the reasons why it dominates in the industry. With a diverse staff, it is easier for employees and managers to work together.
A diverse staff is also important for businesses that wish to succeed, as it helps them better understand the requirements of their clients and prospective customers.
It can also assist them in providing the best products and services to their customers. It can also help them improve their financial performance by reducing costs and lowering expenses.
Lastly, having a diverse workforce can also help them attract and retain the best workers. Having more women and minorities in a company can improve employee morale, which is especially critical for paper companies that are dealing with the ongoing issues of globalization and economic growth.
In order to achieve a sustainable development, companies like these implement policies that reduce the environmental impact of their operations and improve energy efficiency. Also, these companies work together with their supplier to find ways of reducing waste and increasing recycling.
FAQ
What are the responsibilities of a logistic manager?
Logistics managers are responsible for ensuring that all goods arrive in perfect condition and on time. This is done through his/her expertise and knowledge about the company's product range. He/she also needs to ensure adequate stock to meet demand.
What are the responsibilities for a manufacturing manager
A manufacturing manager must make sure that all manufacturing processes run smoothly and effectively. They should be alert for any potential problems in the company and react accordingly.
They should also know how to communicate with other departments such as sales and marketing.
They must also keep up-to-date with the latest trends in their field and be able use this information to improve productivity and efficiency.
What is the role of a production manager?
Production planners make sure that every aspect of the project is delivered on-time, within budget, and within schedule. They also ensure that the product/service meets the client’s needs.
What is meant by manufacturing industries?
Manufacturing Industries are those businesses that make products for sale. Consumers are those who purchase these products. These companies use various processes such as production, distribution, retailing, management, etc., to fulfill this purpose. These companies produce goods using raw materials and other equipment. This includes all types of manufactured goods, including food items, clothing, building supplies, furniture, toys, electronics, tools, machinery, vehicles, pharmaceuticals, medical devices, chemicals, and many others.
Statistics
- In 2021, an estimated 12.1 million Americans work in the manufacturing sector.6 (investopedia.com)
- According to a Statista study, U.S. businesses spent $1.63 trillion on logistics in 2019, moving goods from origin to end user through various supply chain network segments. (netsuite.com)
- Job #1 is delivering the ordered product according to specifications: color, size, brand, and quantity. (netsuite.com)
- You can multiply the result by 100 to get the total percent of monthly overhead. (investopedia.com)
- [54][55] These are the top 50 countries by the total value of manufacturing output in US dollars for its noted year according to World Bank.[56] (en.wikipedia.org)
External Links
How To
Six Sigma: How to Use it in Manufacturing
Six Sigma can be described as "the use of statistical process control (SPC), techniques to achieve continuous improvement." It was developed by Motorola's Quality Improvement Department at their plant in Tokyo, Japan, in 1986. Six Sigma's main goal is to improve process quality by standardizing processes and eliminating defects. Since there are no perfect products, or services, this approach has been adopted by many companies over the years. Six Sigma's primary goal is to reduce variation from the average value of production. If you take a sample and compare it with the average, you will be able to determine how much of the production process is different from the norm. If it is too large, it means that there are problems.
Understanding the nature of variability in your business is the first step to Six Sigma. Once you have a good understanding of the basics, you can identify potential sources of variation. Also, you will need to identify the sources of variation. Random variations occur when people make mistakes; systematic ones are caused by factors outside the process itself. For example, if you're making widgets, and some of them fall off the assembly line, those would be considered random variations. But if you notice that every widget you make falls apart at the exact same place each time, this would indicate that there is a problem.
Once you identify the problem areas, it is time to create solutions. You might need to change the way you work or completely redesign the process. To verify that the changes have worked, you need to test them again. If they fail, you can go back to the drawing board to come up with a different plan.