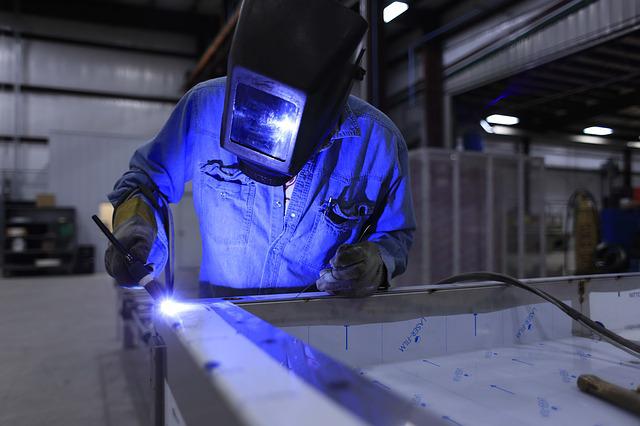
An industrial engineer uses engineering and testing to improve products. Industrial engineers use shaker tables to test whole products in a variety of temperatures, humidity, or vibrations. Failure data can be used to improve engineering and manufacturing processes. Simple changes, like mold-resistant paint, can greatly improve the quality and service life of a product. Even the smallest changes, such as a lock-washed placement, can improve a product's service life.
Job description
Your job description is a key component of a career as an engineer. A job description that is clear and concise will make you stand out from the rest. Monster has many engineering job listings that can help you get ideas for your job description. Begin with a persuasive introduction that highlights the company's benefits. Your employer should be attractive to you, whether you are looking to join a well-respected brand, an innovative start up, or a young, dynamic company with a creative, open atmosphere.
Along with excellent technical skills and communication skills, industrial engineers should also be able to communicate well. Industrial processes involve multiple departments and people, so an industrial engineer needs to know how to interact with them all. A successful industrial engineer must know how to persuade managers and employees that his orher proposed methods will increase efficiency. The best relationship management results in higher productivity. An industrial engineer job description does not require only technical skills.
Education requirements
For a position in industrial engineering, a degree in math and analytical skills is essential. As they communicate their findings to others, industrial engineers must also have excellent communication skills. Additionally, industrial engineers must be able and willing to create processes and designs that are cost-effective and reduce labor. Education in this field will also enable you to succeed in this field. These are some of the key educational requirements required for this position.
Industrial engineers should have a college degree but also excellent interpersonal and communication skills. They are closely connected with other professionals and serve as the link between technical and business sides of organizations. To effectively communicate with business leaders as well as employees, industrial engineers must have strong communication skills and analytical abilities. This profession requires excellent leadership and problem-solving skills. A high level of technical and mechanical competence is required for industrial engineers.
Options for a career
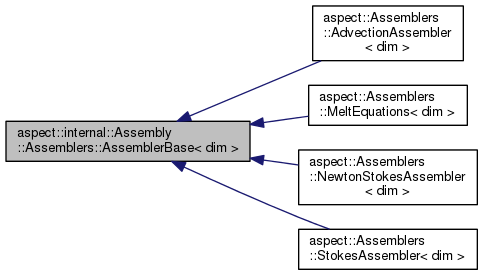
If you're interested in industrial engineering, you have many career options. While most industrial engineers start their career in manufacturing, hospitals and government agencies are other options. Industrial engineers can also work in the retail trade, educational agencies and professional trade associations. There are many jobs available for industrial engineers. Here are some of the best. Read on to find out more about the various career opportunities available to you.
An industrial engineer can be focused on efficiency and effectiveness. They must balance many factors, including time, workers required, technology available, and the actions that workers need to take. They must also be aware of safety and environment concerns. Many industrial engineers work in quality assurance or supply chain management. This is important because many industries are constantly trying to cut costs while increasing their productivity. They can also help with product development and work flow optimization.
Salary
The average industrial engineer salary in 2004 was $87,513 US Dollars. This figure is expected to rise to $114,146 by 2020. The salary depends on which industry you work in. Salary increases in highly regarded industries will be higher. Industrial Engineers receive a variety of bonuses, which can change often and are usually moderate. Most of those who receive bonuses are involved in revenue generation. An industrial engineering degree is necessary to receive the best possible salary.
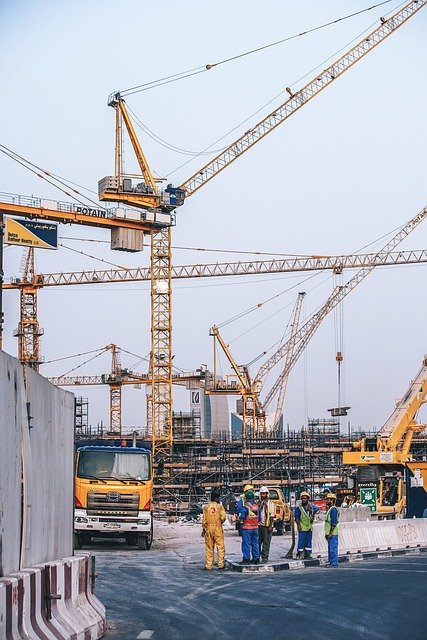
To be a successful industrial engineer, you must hold a bachelor's degree. Some employers, however, prefer PhDs. An industrial engineer can earn between $56,000 and $121,000 in the U.S. but this amount can vary greatly. Industrial engineers can be employed in an office setting, but some jobs require protective clothing and overtime. Therefore, flexibility is essential.
FAQ
Why is logistics so important in manufacturing?
Logistics are an essential component of any business. Logistics can help you achieve amazing results by helping to manage product flow from raw materials to finished products.
Logistics play a key role in reducing expenses and increasing efficiency.
What are the logistics products?
Logistics involves the transportation of goods from point A and point B.
These include all aspects related to transport such as packaging, loading and transporting, storing, transporting, unloading and warehousing inventory management, customer service. Distribution, returns, recycling are some of the options.
Logisticians make sure that the right product arrives at the right place at the correct time and in safe conditions. They help companies manage their supply chain efficiency by providing information on demand forecasts, stock levels, production schedules, and availability of raw materials.
They can also track shipments in transit and monitor quality standards.
What is production plan?
Production Planning refers to the development of a plan for every aspect of production. This document aims to ensure that everything is planned and ready when you are ready to shoot. It should also contain information on achieving the best results on set. This includes shooting schedules, locations, cast lists, crew details, and equipment requirements.
The first step in filming is to define what you want. You may have already decided where you would like to shoot, or maybe there are specific locations or sets that you want to use. Once you have identified your locations and scenes, you can start working out which elements you require for each scene. For example, you might decide that you need a car but don't know exactly what model you want. To narrow your options, you can search online for available models.
Once you have found the right vehicle, you can think about adding accessories. Are you looking for people to sit in the front seats? You might also need someone to help you get around the back. Perhaps you would like to change the interior colour from black to white. These questions will help you determine the exact look and feel of your car. The type of shots that you are looking for is another thing to consider. Will you be filming close-ups or wide angles? Maybe you want to show your engine or the steering wheel. These things will help you to identify the car that you are looking for.
Once you have determined all of the above, you can move on to creating a schedule. A schedule will tell you when you need to start shooting and when you need to finish. You will need to know when you have to be there, what time you have to leave and when your return home. So everyone is clear about what they need to do. Hire extra staff by booking them ahead of time. There is no point in hiring someone who won't turn up because you didn't let him know.
When creating your schedule, you will also need to consider the number of days you need to film. Some projects can be completed in a matter of days or weeks. Others may take several days. While creating your schedule, it is important to remember whether you will require more than one shot per day. Multiple takes at the same place will result in higher costs and longer completion times. You can't be certain if you will need multiple takes so it is better not to shoot too many.
Budgeting is another crucial aspect of production plan. As it will allow you and your team to work within your financial means, setting a realistic budget is crucial. If you have to reduce your budget due to unexpected circumstances, you can always lower it later. However, it is important not to overestimate the amount that you will spend. Underestimating the cost will result in less money after you have paid for other items.
Production planning can be a complex process. However, once you know how everything works together it will become easier to plan future projects.
How can overproduction in manufacturing be reduced?
In order to reduce excess production, you need to develop better inventory management methods. This would reduce time spent on activities such as purchasing, stocking, and maintaining excess stock. We could use these resources to do other productive tasks.
You can do this by adopting a Kanban method. A Kanbanboard is a visual tool that allows you to keep track of the work being done. In a Kanban system, work items move through a sequence of states until they reach their final destination. Each state represents an individual priority level.
To illustrate, work can move from one stage or another when it is complete enough for it to be moved to a new stage. If a task is still in its beginning stages, it will continue to be so until it reaches the end.
This allows you to keep work moving along while making sure that no work gets neglected. Managers can view the Kanban board to see how much work they have done. This allows them the ability to adjust their workflow using real-time data.
Lean manufacturing, another method to control inventory levels, is also an option. Lean manufacturing works to eliminate waste throughout every stage of the production chain. Any product that isn't adding value can be considered waste. Some common types of waste include:
-
Overproduction
-
Inventory
-
Packaging that is not necessary
-
Exceed materials
These ideas can help manufacturers improve efficiency and reduce costs.
How does manufacturing avoid bottlenecks in production?
The key to avoiding bottlenecks in production is to keep all processes running smoothly throughout the entire production cycle, from the time you receive an order until the time when the product ships.
This includes planning for capacity requirements as well as quality control measures.
The best way to do this is to use continuous improvement techniques such as Six Sigma.
Six Sigma can be used to improve the quality and decrease waste in all areas of your company.
It's all about eliminating variation and creating consistency in work.
What are my options for learning more about manufacturing
Hands-on experience is the best way to learn more about manufacturing. However, if that's not possible, you can always read books or watch educational videos.
Statistics
- It's estimated that 10.8% of the U.S. GDP in 2020 was contributed to manufacturing. (investopedia.com)
- (2:04) MTO is a production technique wherein products are customized according to customer specifications, and production only starts after an order is received. (oracle.com)
- Many factories witnessed a 30% increase in output due to the shift to electric motors. (en.wikipedia.org)
- You can multiply the result by 100 to get the total percent of monthly overhead. (investopedia.com)
- In 2021, an estimated 12.1 million Americans work in the manufacturing sector.6 (investopedia.com)
External Links
How To
How to Use 5S to Increase Productivity in Manufacturing
5S stands to stand for "Sort", “Set In Order", “Standardize", and "Store". Toyota Motor Corporation created the 5S methodology in 1954. This methodology helps companies improve their work environment to increase efficiency.
This approach aims to standardize production procedures, making them predictable, repeatable, and easily measurable. Cleaning, sorting and packing are all done daily. These actions allow workers to perform their job more efficiently, knowing what to expect.
Five steps are required to implement 5S: Sort, Set In Order, Standardize. Separate. Each step involves a different action which leads to increased efficiency. If you sort items, it makes them easier to find later. You arrange items by placing them in an order. You then organize your inventory in groups. Finally, label all containers correctly.
Employees need to reflect on how they do their jobs. Employees must be able to see why they do what they do and find a way to achieve them without having to rely on their old methods. They must learn new skills and techniques in order to implement the 5S system.
The 5S Method not only improves efficiency, but it also helps employees to be more productive and happier. As they begin to see improvements, they feel motivated to continue working towards the goal of achieving higher levels of efficiency.