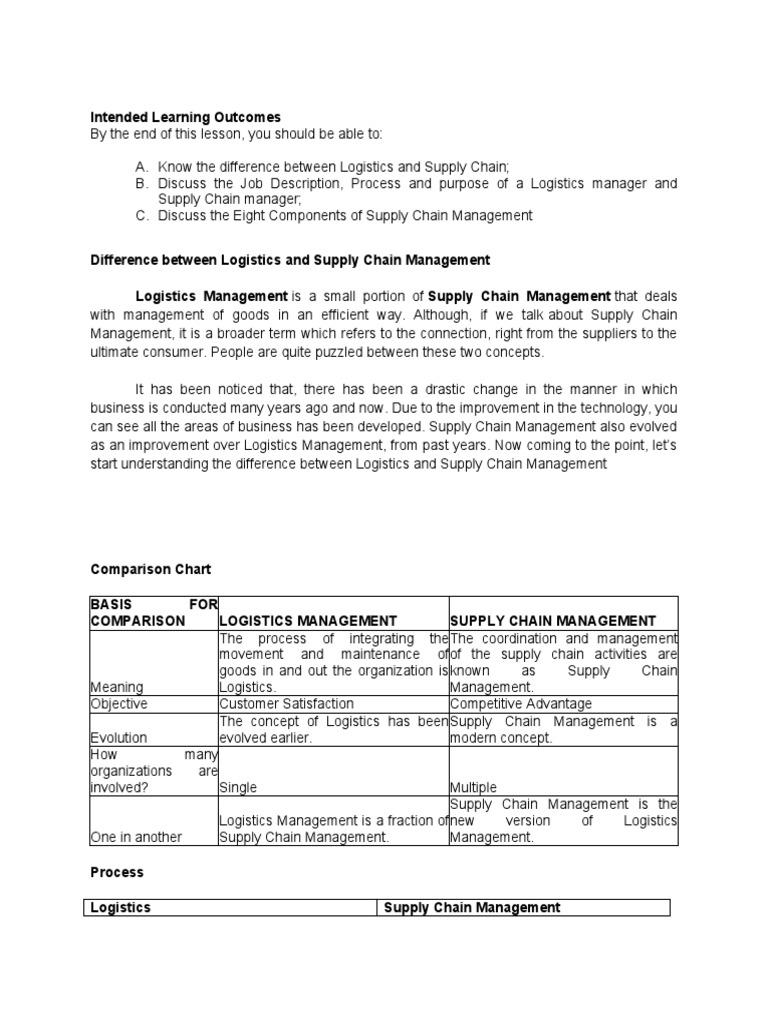
Industrial Engineering managers are essential members of the team. They play a critical role in guiding employees and improving production output. This includes managing the factory floor's layout and design, and overseeing implementation of processes and procedures. Additionally, they offer technical knowledge and expertise that can be used to aid in the development of new products or processes.
Managers in Industrial Engineering are responsible for creating and maintaining efficient manufacturing processes. This requires knowledge about the most recent trends in robotics and automation. They must also monitor and maintain industrial processes and ensure that they comply with safety and health standards. They supervise the usage of raw materials, consumables, and other industrial processes. They also carry out studies to improve workflow efficiency and space use. The manager supervises all work projects including product cost reduction, cycle time and process improvement. They also oversee preventative maintenance.
As a manager, you work with other teams to improve efficiency and streamline operations. He or she oversees equipment renovations and the redesign and installation thereof. The manager is responsible for communicating technical information to nontechnical stakeholders as part the project management process. The manager also secures resources and visits suppliers' facilities. He or she is a champion for members of the team and ensures they adhere to quality standards.
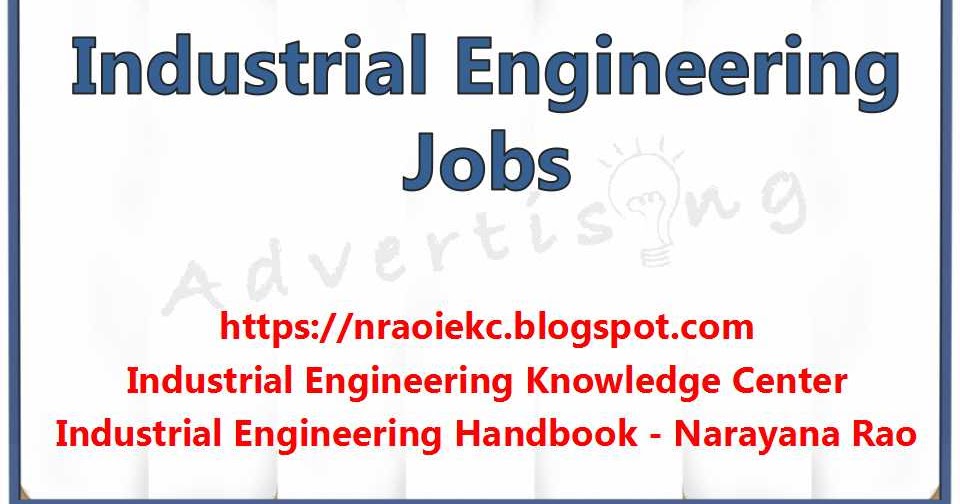
Managers in industrial engineering are expected be to be innovative, motivated, and able resolve problems. They must be able to work in hot and cold environments, be physically fit, and climb and walk for 8 to 12 hours a day. They must also be able communicate with all levels of employees.
Industrial Engineering Managers must have a degree in engineering or a related field. They also must have at least five years of experience in the field. Postgraduate degrees are preferred by some employers. You may also need specific skills like project management or logistics.
Industrial Engineering Managers are responsible for the development and creation of new products. They have strong skills in problem-solving, quality improvement, and other related areas. They thrive in a team environment. The manager is most successful when he or she is able to facilitate employees' growth.
Industrial Engineers have the ability to streamline operations and reduce costs. They have a good understanding of manufacturing processes and are able to meet deadlines. They also have experience with recruiting, human resources, logistics, and vendor / supplier relations. They are skilled at managing budgets, setting goals and administering procedures. They are also able to prepare strategies to increase the efficiency of engineering projects.
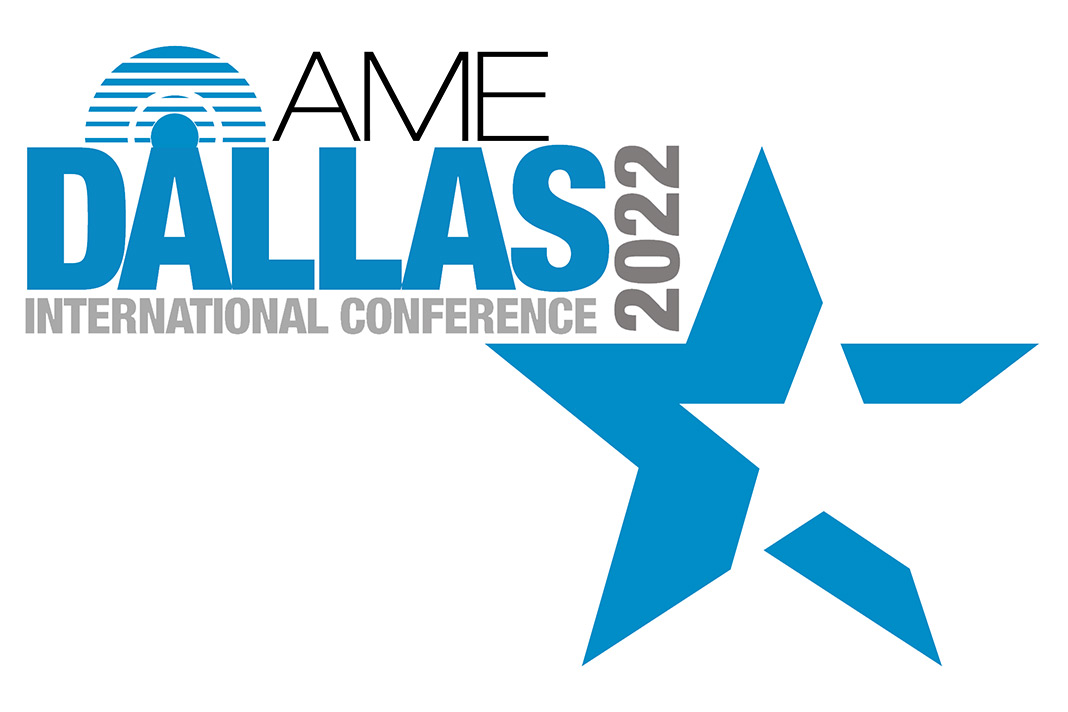
Industrial Engineering Managers are responsible for overseeing new manufacturing lines and operating equipment. They have to create plans for new equipment, and operate according to existing guidelines and standards. They are responsible for overseeing the implementation of waste elimination plans. They also have to analyze the factory's labor productivity.
Industrial Engineering Managers can also contribute their expertise in developing strategies for improving productivity, developing new products, and managing human resources. They can also improve efficiency and develop new processes.
FAQ
How can manufacturing reduce production bottlenecks?
The key to avoiding bottlenecks in production is to keep all processes running smoothly throughout the entire production cycle, from the time you receive an order until the time when the product ships.
This includes planning to meet capacity requirements and quality control.
Continuous improvement techniques such Six Sigma are the best method to accomplish this.
Six Sigma management is a system that improves quality and reduces waste within your organization.
It focuses on eliminating variation and creating consistency in your work.
What skills does a production planner need?
A production planner must be organized, flexible, and able multitask to succeed. Communication skills are essential to ensure that you can communicate effectively with clients, colleagues, and customers.
How can manufacturing efficiency improved?
First, we need to identify which factors are most critical in affecting production times. Next, we must find ways to improve those factors. If you don’t know how to start, look at which factors have the greatest impact upon production time. Once you've identified them all, find solutions to each one.
What is production planning?
Production Planning includes planning for all aspects related to production. It is important to have everything ready and planned before you start shooting. This document should also include information on how to get the best result on set. This information includes locations, crew details and equipment requirements.
First, you need to plan what you want to film. You may have already chosen the location you want, or there are locations or sets you prefer. Once you've identified the locations and scenes you want to use, you can begin to plan what elements you need for each scene. Perhaps you have decided that you need to buy a car but aren't sure which model. This is where you can look up car models online and narrow down your options by choosing from different makes and models.
Once you have found the right car, you can start thinking about extras. Are you looking for people to sit in the front seats? Maybe you need someone to move around in the back. You may want to change the interior's color from black or white. These questions will help to determine the style and feel of your car. Also, think about what kind of shots you would like to capture. Do you want to film close-ups, or wider angles? Maybe you want to show your engine or the steering wheel. These things will help you to identify the car that you are looking for.
Once you have all the information, you are ready to create a plan. You can use a schedule to determine when and where you need it to be shot. A schedule for each day will detail when you should arrive at the location and when you need leave. Everyone knows exactly what they should do and when. If you need to hire extra staff, you can make sure you book them in advance. There is no point in hiring someone who won't turn up because you didn't let him know.
You will need to factor in the days that you have to film when creating your schedule. Some projects may only take a couple of days, while others could last for weeks. When creating your schedule, be aware of whether you need more shots per day. Multiple takes at the same place will result in higher costs and longer completion times. If you aren't sure whether you need multiple shots, it is best to take fewer photos than you would like.
Budget setting is another important aspect in production planning. It is important to set a realistic budget so you can work within your budget. Remember that you can always reduce the budget later on if you run into unforeseen problems. It is important to not overestimate how much you will spend. If you underestimate how much something costs, you'll have less money to pay for other items.
Planning production is a tedious process. Once you have a good understanding of how everything works together, planning future projects becomes easy.
What is manufacturing and logistics?
Manufacturing is the act of producing goods from raw materials using machines and processes. Logistics manages all aspects of the supply chain, including procurement, production planning and distribution, inventory control, transportation, customer service, and transport. Manufacturing and logistics can often be grouped together to describe a larger term that covers both the creation of products, and the delivery of them to customers.
Statistics
- (2:04) MTO is a production technique wherein products are customized according to customer specifications, and production only starts after an order is received. (oracle.com)
- Job #1 is delivering the ordered product according to specifications: color, size, brand, and quantity. (netsuite.com)
- It's estimated that 10.8% of the U.S. GDP in 2020 was contributed to manufacturing. (investopedia.com)
- You can multiply the result by 100 to get the total percent of monthly overhead. (investopedia.com)
- [54][55] These are the top 50 countries by the total value of manufacturing output in US dollars for its noted year according to World Bank.[56] (en.wikipedia.org)
External Links
How To
Six Sigma in Manufacturing:
Six Sigma is "the application statistical process control (SPC), techniques for continuous improvement." Motorola's Quality Improvement Department created Six Sigma at their Tokyo plant, Japan in 1986. Six Sigma's basic concept is to improve quality and eliminate defects through standardization. Many companies have adopted Six Sigma in recent years because they believe that there are no perfect products and services. The main goal of Six Sigma is to reduce variation from the mean value of production. If you take a sample and compare it with the average, you will be able to determine how much of the production process is different from the norm. If you notice a large deviation, then it is time to fix it.
Understanding how variability works in your company is the first step to Six Sigma. Once you've understood that, you'll want to identify sources of variation. You'll also want to determine whether these variations are random or systematic. Random variations are caused when people make mistakes. While systematic variations are caused outside of the process, they can occur. Random variations would include, for example, the failure of some widgets to fall from the assembly line. You might notice that your widgets always fall apart at the same place every time you put them together.
Once you've identified where the problems lie, you'll want to design solutions to eliminate those problems. This could mean changing your approach or redesigning the entire process. You should then test the changes again after they have been implemented. If they don’t work, you’ll need to go back and rework the plan.