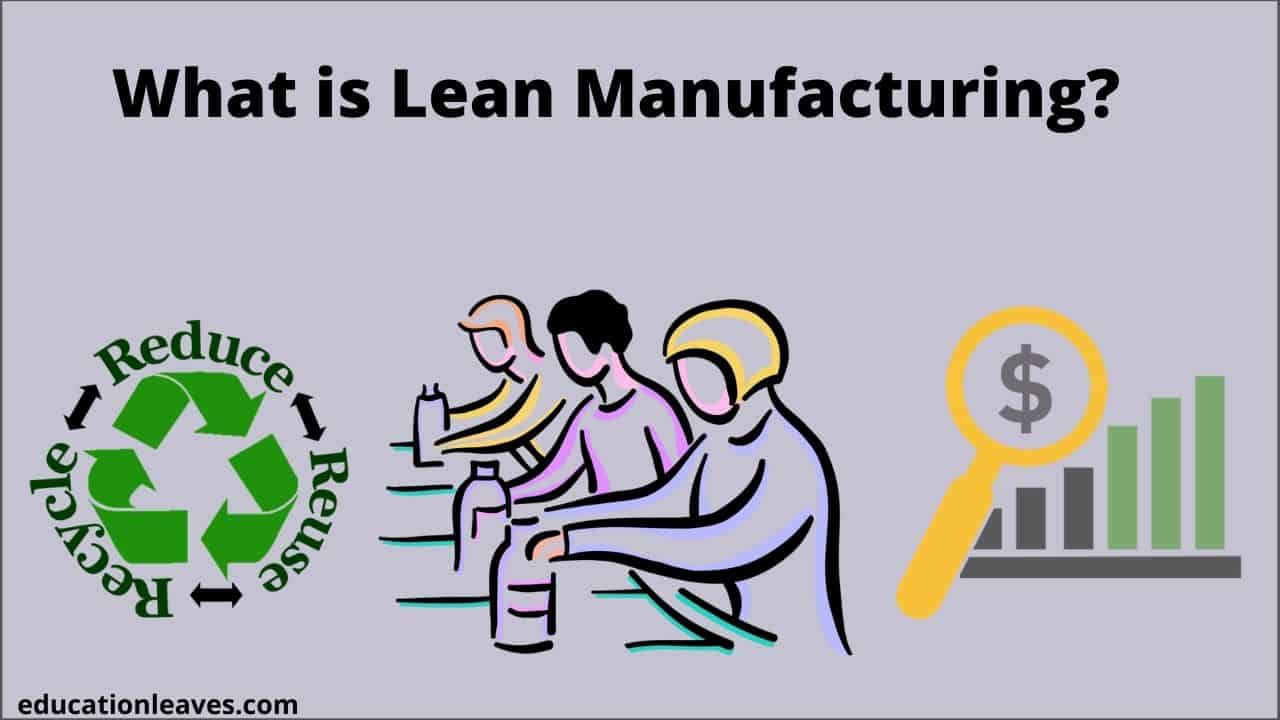
Do you want to work in asset protection at Walmart? Continue reading to learn more about these roles and the safety procedures involved. Apply today if you feel that Walmart is the right fit for you. Find out more information about Walmart's Asset Protection Associate Salary and Compensation. Also, learn about safety procedures. Find out more about this position. You can find out more information by completing the application form online. An account is required to get started.
Walmart asset protection associates: Salary range
Walmart Asset Protection Associate earns an average salary of Rs 1.8 Lakhs to RS 2.2 Lakhs per annum. This figure is based upon statistical methods and the actual salaries of six employees at Walmart Asset Protection Associates. To learn more about this job, please review the following information. Based on six anonymous Glassdoor salaries, the following salary estimates were generated by Asset Protection Associates. This information does not include bonuses, overtime, or other compensation.
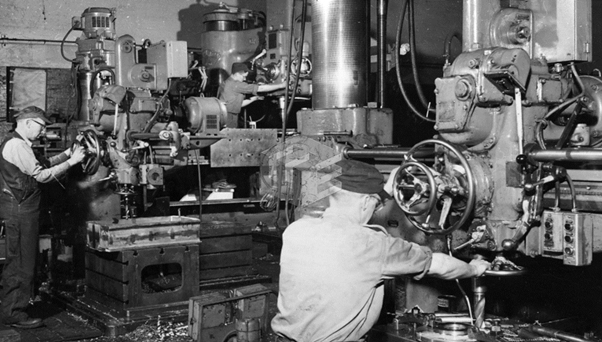
For this job, people with criminal justice backgrounds and experience in retail loss prevention will be a good fit. Walmart offers many career opportunities and salary ranges to asset protection associates. Walmart Careers allows interested applicants to access job descriptions and learn about the job responsibilities. Sign the disclosures and then create a profile to apply. If you are applying to an AP manager position, you can fill out an application.
Safety procedures
Walmart is one of the most diverse and largest retailers in the world and has many safety and security concerns. Here are the top priorities and safety protocols for Walmart’s Asset Protection program. Mike Lamb, vice president of Walmart US's asset protection and safety department, explains how these policies help protect Walmart's assets, while addressing the most common problems and opportunities. This program protects the company's assets and keeps customers and associates safe.
Associate: Walmart Asset Protection Program Associates are the frontline of crime prevention. They help store managers and employees keep their stores safe from theft and fraud. Entry-level positions do not require formal qualifications, but managers must hold a bachelor's degree in criminal law or a Loss Prevention Qualified Certificate. For entry-level roles, however, a Loss Prevention Qualified Certificate or a degree relating to criminal justice are required.
Compensation
Based on 974 workers with this job title, the average Walmart Asset Protection compensation amount is $33,000 per annum. The figure includes tips, taxable wages and bonuses and can range from $18,500 to $53,000 depending upon the person's education and experience. These figures are not representative of actual Walmart Asset Protection salaries. It does provide a starting point for you to figure the salary you're entitled to.
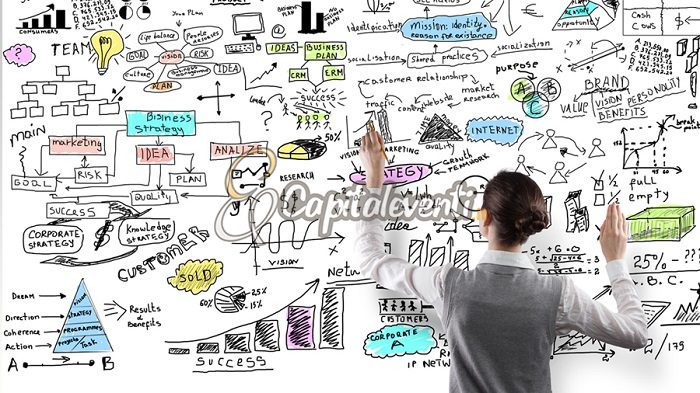
Wal-Mart will continue to give bonuses to store managers that can be tied to store performance. Walmart also knows that long-term employees are more likely receive raises than newer employees. As such, associates who have many years of work experience can request raises at least once a year. The hourly rate is between $12 and $16. Below is a table that shows the average Walmart Ap Customer Host's salary. Visit the official Walmart website for more information.
FAQ
How can efficiency in manufacturing be improved?
The first step is to determine the key factors that impact production time. We then need to figure out how to improve these variables. If you don't know where to start, then think about which factor(s) have the biggest impact on production time. Once you identify them, look for solutions.
How can manufacturing overproduction be reduced?
In order to reduce excess production, you need to develop better inventory management methods. This would reduce the time spent on unproductive activities like purchasing, storing and maintaining excess stock. We could use these resources to do other productive tasks.
This can be done by using a Kanban system. A Kanban board, a visual display to show the progress of work, is called a Kanban board. Kanban systems allow work items to move through different states until they reach their final destination. Each state represents an individual priority level.
When work is completed, it can be transferred to the next stage. A task that is still in the initial stages of a process will be considered complete until it moves on to the next stage.
This keeps work moving and ensures no work is lost. Managers can view the Kanban board to see how much work they have done. This information allows managers to adjust their workflow based off real-time data.
Lean manufacturing can also be used to reduce inventory levels. Lean manufacturing emphasizes eliminating waste in all phases of production. Anything that does nothing to add value to a product is waste. Here are some examples of common types.
-
Overproduction
-
Inventory
-
Unnecessary packaging
-
Overstock materials
These ideas can help manufacturers improve efficiency and reduce costs.
What is the responsibility for a logistics manager
Logistics managers are responsible for ensuring that all goods arrive in perfect condition and on time. This is done through his/her expertise and knowledge about the company's product range. He/she also needs to ensure adequate stock to meet demand.
What does it take for a logistics enterprise to succeed?
A successful logistics business requires a lot more than just knowledge. Good communication skills are essential to effectively communicate with your suppliers and clients. You will need to know how to interpret data and draw conclusions. You need to be able work under pressure and manage stressful situations. To improve efficiency, you must be innovative and creative. You need to have strong leadership qualities to motivate team members and direct them towards achieving organizational goals.
You must be organized to meet tight deadlines.
How can manufacturing reduce production bottlenecks?
Avoiding production bottlenecks is as simple as keeping all processes running smoothly, from the time an order is received until the product ships.
This includes planning to meet capacity requirements and quality control.
Continuous improvement techniques such Six Sigma are the best method to accomplish this.
Six Sigma Management System is a method to increase quality and reduce waste throughout your organization.
It seeks to eliminate variation and create consistency in your work.
What are the logistics products?
Logistics are the activities involved in moving goods from point A to point B.
They include all aspects of transport, including packaging, loading, transporting, unloading, storing, warehousing, inventory management, customer service, distribution, returns, and recycling.
Logisticians ensure that the product is delivered to the correct place, at the right time, and under safe conditions. They help companies manage their supply chain efficiency by providing information on demand forecasts, stock levels, production schedules, and availability of raw materials.
They monitor shipments in transit, ensure quality standards, manage inventories, replenish orders, coordinate with suppliers and other vendors, and offer support services for sales, marketing, and customer service.
Why is logistics important in manufacturing
Logistics is an integral part of every business. They are essential to any business's success.
Logistics plays a significant role in reducing cost and increasing efficiency.
Statistics
- Many factories witnessed a 30% increase in output due to the shift to electric motors. (en.wikipedia.org)
- In the United States, for example, manufacturing makes up 15% of the economic output. (twi-global.com)
- According to the United Nations Industrial Development Organization (UNIDO), China is the top manufacturer worldwide by 2019 output, producing 28.7% of the total global manufacturing output, followed by the United States, Japan, Germany, and India.[52][53] (en.wikipedia.org)
- It's estimated that 10.8% of the U.S. GDP in 2020 was contributed to manufacturing. (investopedia.com)
- According to a Statista study, U.S. businesses spent $1.63 trillion on logistics in 2019, moving goods from origin to end user through various supply chain network segments. (netsuite.com)
External Links
How To
How to Use Six Sigma in Manufacturing
Six Sigma is "the application statistical process control (SPC), techniques for continuous improvement." It was developed by Motorola's Quality Improvement Department at their plant in Tokyo, Japan, in 1986. Six Sigma's main goal is to improve process quality by standardizing processes and eliminating defects. In recent years, many companies have adopted this method because they believe there is no such thing as perfect products or services. Six Sigma's primary goal is to reduce variation from the average value of production. This means that you can take a sample from your product and then compare its performance to the average to find out how often the process differs from the norm. If this deviation is too big, you know something needs fixing.
Understanding the dynamics of variability within your business is the first step in Six Sigma. Once you have a good understanding of the basics, you can identify potential sources of variation. Also, you will need to identify the sources of variation. Random variations are caused when people make mistakes. While systematic variations are caused outside of the process, they can occur. If you make widgets and some of them end up on the assembly line, then those are considered random variations. However, if you notice that every time you assemble a widget, it always falls apart at exactly the same place, then that would be a systematic problem.
After identifying the problem areas, you will need to devise solutions. It might mean changing the way you do business or redesigning it entirely. Test them again once you've implemented the changes. If they don't work, you will need to go back to the drawing boards and create a new plan.