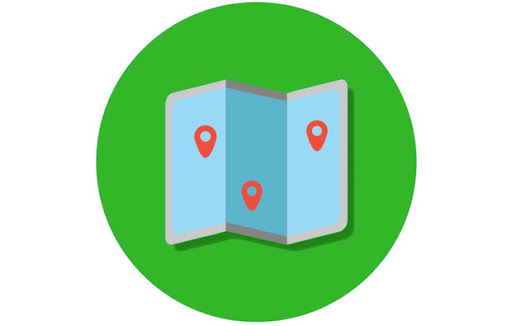
Originally developed by Toyota, Gemba Walk is a tool that takes managers to the shop floor to gain insights into the processes in the company. This is an important part of any facility improvement project. This helps managers to understand their company's processes and makes better decisions. It also helps identify potential problems and solutions.
Gemba is a Japanese term that means "where the work happens." It can be used to denote the factory floor or shopfloor, but it could also refer to any location where a product/service is created. Gemba is also the name of a Japanese business philosophy that sets out a series of objectives. In general, the goal of Gemba is to achieve in-depth knowledge of the processes in an organization, while eliminating waste and improving efficiency.
Companies looking to improve their processes, eliminate waste and increase productivity are able to take Gemba Walks. Gemba walks promote cooperation and a better work environment. They encourage employees' to share their ideas, which can help improve the quality of the service or product being made. Managers and executives can benefit from them by better understanding the company's processes.
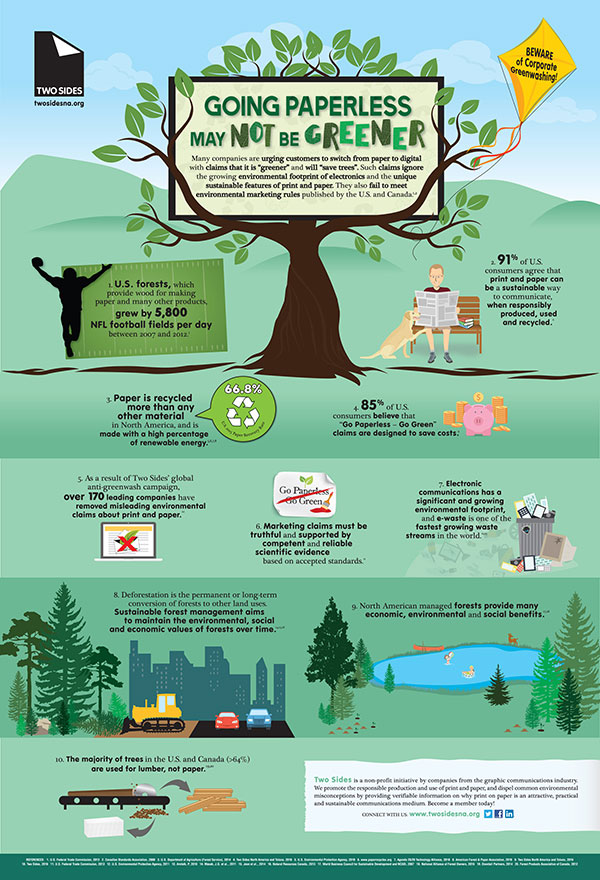
Gemba walks can usually be carried out by supervisors and managers. But, they can also easily be undertaken by executives. Gemba walks should be done on a daily basis by executive managers. They should spend about 45-60 minutes each week on a Gemba walk with a Lean teacher or Sensei. This is because it allows workers to be seen at their best.
Gemba Walks aid executives and managers to understand how processes work and help them identify improvement opportunities. They can also be used to improve safety and security in the workplace. Safety issues make up the majority of waste produced in manufacturing plants. Improved safety can contribute to continual improvement.
Gemba Walks play an important role in Lean. However, they should be applied at all levels within the organization. They can help leaders and executives gain a fresh perspective on the needs of their customers, which can lead to better products, services, and processes. Gemba Walks are an effective way to help your organization reach its full potential.
Gemba Walks are an integral part of Lean process design and are frequently used by key stakeholders at Kaizen events. Kaizen events bring together key stakeholders to assess activities and make recommendations.
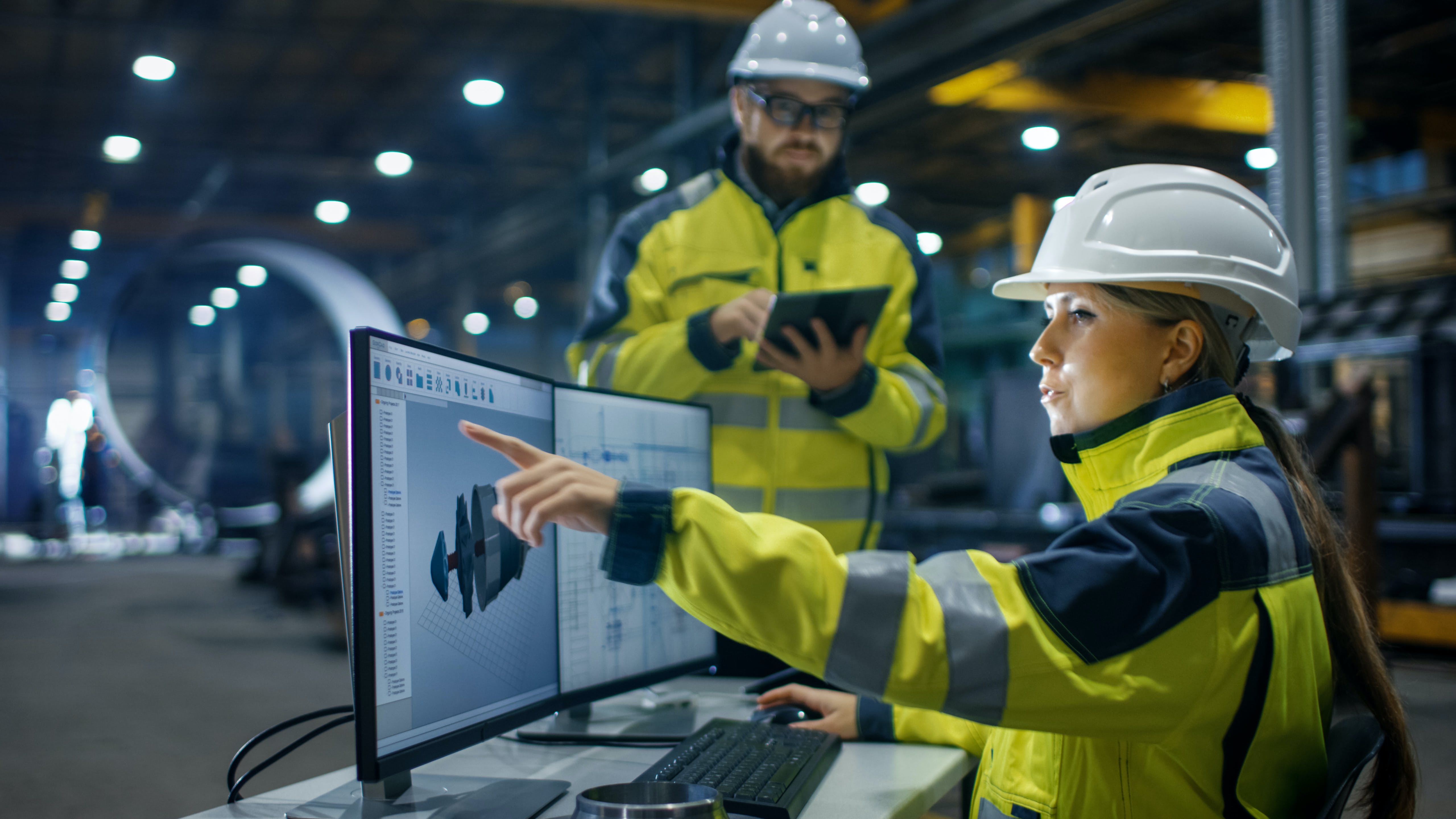
Gemba Walks should always be performed on a daily basis. They can reduce waste and increase productivity if done properly. These should be completed during shift changes as these are the busiest times of the day. This will allow executives and project managers to gain a fresh perspective on the business. These executives and project managers must also note any possible improvements they uncover, such new products or service ideas, as well any suggestions from employees.
FAQ
What kind of jobs are there in logistics?
Logistics can offer many different jobs. These are some of the jobs available in logistics:
-
Warehouse workers – They load, unload and transport pallets and trucks.
-
Transportation drivers - They drive trucks and trailers to deliver goods and carry out pick-ups.
-
Freight handlers, - They sort out and pack freight in warehouses.
-
Inventory managers - These are responsible for overseeing the stock of goods in warehouses.
-
Sales representatives - They sell products.
-
Logistics coordinators – They plan and coordinate logistics operations.
-
Purchasing agents are those who purchase goods and services for the company.
-
Customer service agents - They answer phone calls and respond to emails.
-
Ship clerks - They issue bills and process shipping orders.
-
Order fillers: They fill orders based off what has been ordered and shipped.
-
Quality control inspectors - They check incoming and outgoing products for defects.
-
Others - There is a variety of other jobs in logistics. These include transportation supervisors and cargo specialists.
What are the essential elements of running a logistics firm?
To be a successful businessman in logistics, you will need many skills and knowledge. For clients and suppliers to be successful, you need to have excellent communication skills. It is important to be able to analyse data and draw conclusions. You will need to be able handle pressure well and work in stressful situations. In order to innovate and create new ways to improve efficiency, creativity is essential. You will need strong leadership skills to motivate and direct your team members towards achieving their organizational goals.
You should also be organized and efficient to meet tight deadlines.
What is the best way to learn about manufacturing?
Experience is the best way for you to learn about manufacturing. However, if that's not possible, you can always read books or watch educational videos.
What does it mean to be a manufacturer?
Manufacturing Industries are businesses that produce products for sale. These products are sold to consumers. To accomplish this goal, these companies employ a range of processes including distribution, sales, management, and production. They manufacture goods from raw materials using machines and other equipment. This includes all types manufactured goods such as clothing, building materials, furniture, electronics, tools and machinery.
Is there anything we should know about Manufacturing Processes prior to learning about Logistics.
No. No. Knowing about manufacturing processes will help you understand how logistics works.
What are the logistics products?
Logistics refers to the movement of goods from one place to another.
They encompass all aspects transport, including packaging and loading, transporting, storage, unloading.
Logisticians ensure that the product is delivered to the correct place, at the right time, and under safe conditions. They help companies manage their supply chain efficiency by providing information on demand forecasts, stock levels, production schedules, and availability of raw materials.
They can also track shipments in transit and monitor quality standards.
What are the responsibilities of a production planner
Production planners ensure all aspects of the project are delivered within time and budget. They make sure that the product and services meet client expectations.
Statistics
- According to a Statista study, U.S. businesses spent $1.63 trillion on logistics in 2019, moving goods from origin to end user through various supply chain network segments. (netsuite.com)
- Job #1 is delivering the ordered product according to specifications: color, size, brand, and quantity. (netsuite.com)
- In 2021, an estimated 12.1 million Americans work in the manufacturing sector.6 (investopedia.com)
- It's estimated that 10.8% of the U.S. GDP in 2020 was contributed to manufacturing. (investopedia.com)
- In the United States, for example, manufacturing makes up 15% of the economic output. (twi-global.com)
External Links
How To
How to Use 5S to Increase Productivity in Manufacturing
5S stands for "Sort", "Set In Order", "Standardize", "Separate" and "Store". Toyota Motor Corporation invented the 5S strategy in 1954. It assists companies in improving their work environments and achieving higher efficiency.
This method has the basic goal of standardizing production processes to make them repeatable. Cleaning, sorting and packing are all done daily. Workers can be more productive by knowing what to expect.
Implementing 5S involves five steps: Sort, Set in Order, Standardize Separate, Store, and Each step is a different action that leads to greater efficiency. For example, when you sort things, you make them easy to find later. You arrange items by placing them in an order. After you have divided your inventory into groups you can store them in easy-to-reach containers. Finally, label all containers correctly.
Employees will need to be more critical about their work. Employees must understand why they do certain tasks and decide if there's another way to accomplish them without relying on the old ways of doing things. They must learn new skills and techniques in order to implement the 5S system.
The 5S Method not only improves efficiency, but it also helps employees to be more productive and happier. They feel more motivated to work towards achieving greater efficiency as they see the results.