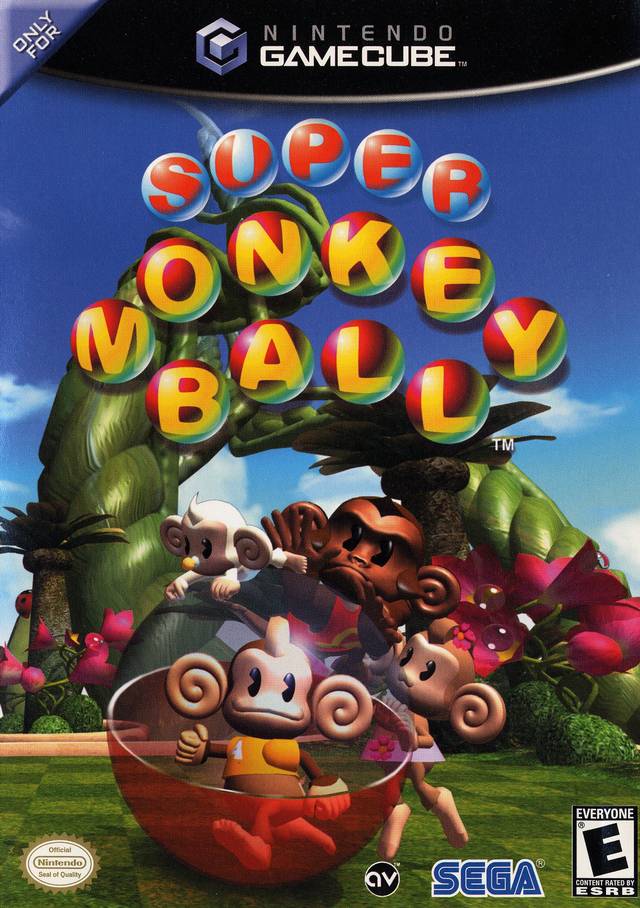
Six sigma principles are important for improving efficiency and productivity within an organization. They also reduce costs and improve product quality. This process can be accomplished using a variety of strategies and methodologies including process mappings, statistical analysis charts, and control chart.
What are the six sigma principles?
The 6 sigma methods are used for identifying defects and eliminating them in manufacturing processes. These principles can be used in many different ways and can have a huge impact. They are also a great way to ensure that all processes run smoothly and efficiently.
Lean six sigma:
Lean six sigma's first principle is to understand how the workflow actually works. This means that it is important to watch the process and make notes to identify where there could be improvements. This step is very important because it helps you identify the problem and develop a solution.
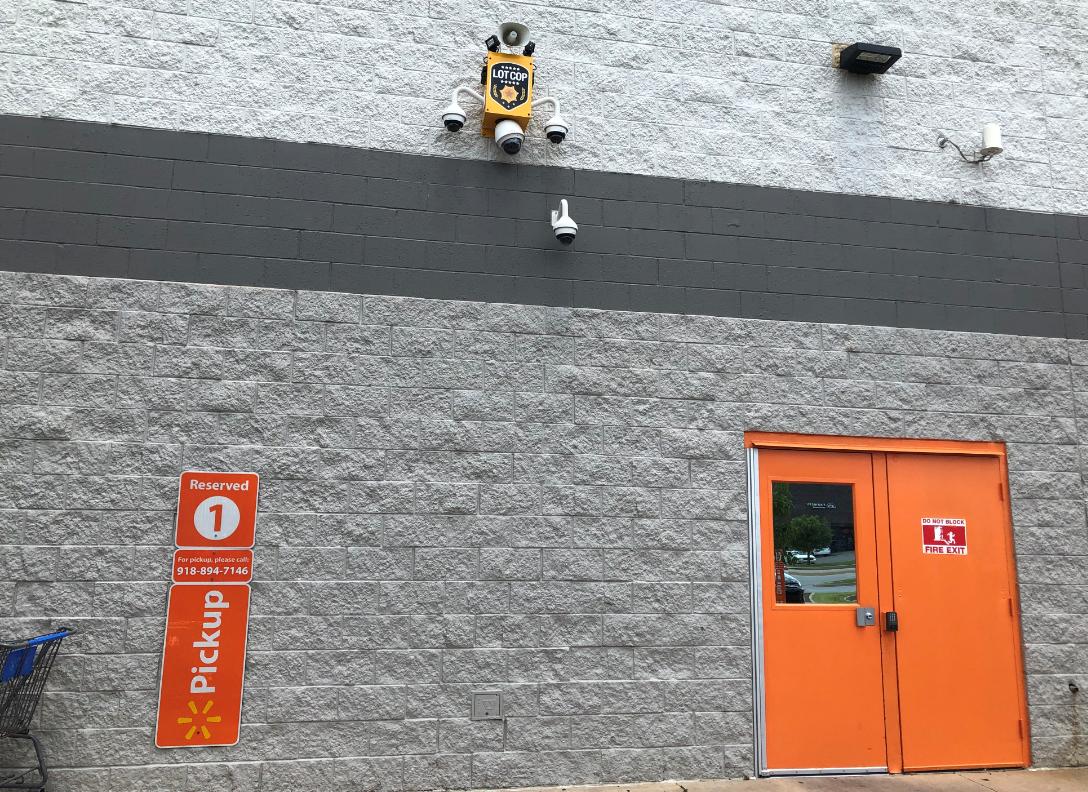
This principle is crucial for any project and is even more important when it comes to process improvement. This is because it's hard to make a change if you have a clear idea of what needs improvement but no clue how to fix it.
To improve a business process, it may be necessary to alter the work practices of employees or to adjust their approach. The task can seem daunting, but it is possible to make the necessary changes if you are willing to adapt.
Six sigma's key principle is to empower employees to take part in projects. The main reason for this is that it can be extremely difficult to implement any changes with only upper management on board.
It is essential that employees be trained on the principles of the new process, so they can recognize and eliminate any errors or defects. They should also be given the resources and tools needed to participate in the project.
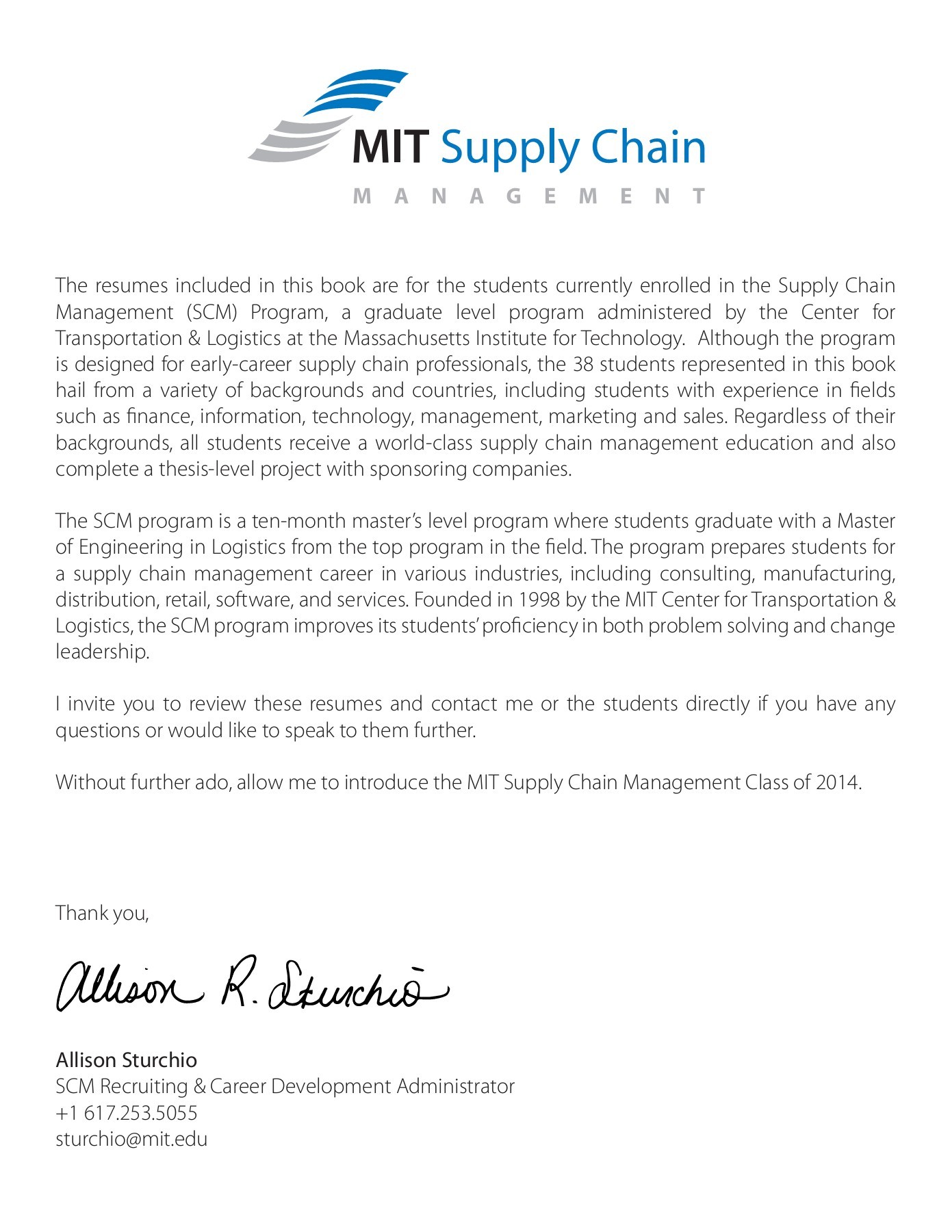
What are the six sigma Values?
Six Sigma values emphasize the importance of customer satisfaction, the belief that all processes should be designed with a minimum amount of waste and the emphasis on data collection and analysis. These factors contribute to higher levels of customer satisfaction.
Lastly, the six sigma values involve consistency and reliability. These factors are crucial in industries where quality products or services are highly demanded. They should apply to all aspects within the company and be continually evaluated and revised, if required.
The six sigma value system helps organizations become more efficient and improve their performance. The six sigma values are important in creating a system that is sustainable and will help the company grow. This is a great method to make sure that your company remains competitive and profitable.
FAQ
What type of jobs is there in logistics
There are different kinds of jobs available in logistics. Here are some examples:
-
Warehouse workers: They load and unload trucks, pallets, and other cargo.
-
Transportation drivers - They drive trucks and trailers to deliver goods and carry out pick-ups.
-
Freight handlers – They sort and package freight at warehouses.
-
Inventory managers - These are responsible for overseeing the stock of goods in warehouses.
-
Sales reps are people who sell products to customers.
-
Logistics coordinators – They plan and coordinate logistics operations.
-
Purchasing agents: They are responsible for purchasing goods and services to support company operations.
-
Customer service representatives - Answer calls and email from customers.
-
Ship clerks - They issue bills and process shipping orders.
-
Order fillers: They fill orders based off what has been ordered and shipped.
-
Quality control inspectors - They check incoming and outgoing products for defects.
-
Others - There are many types of jobs in logistics such as transport supervisors and cargo specialists.
What does manufacturing mean?
Manufacturing Industries is a group of businesses that produce goods for sale. The people who buy these products are called consumers. To accomplish this goal, these companies employ a range of processes including distribution, sales, management, and production. They manufacture goods from raw materials using machines and other equipment. This includes all types if manufactured goods.
What skills should a production planner have?
A production planner must be organized, flexible, and able multitask to succeed. You must also be able to communicate effectively with clients and colleagues.
What is production plan?
Production planning is the process of creating a plan that covers all aspects of production. This includes scheduling, budgeting and crew, location, equipment, props, and more. This document is designed to make sure everything is ready for when you're ready to shoot. This document should include information about how to achieve the best results on-set. This includes shooting schedules, locations, cast lists, crew details, and equipment requirements.
The first step is to decide what you want. You may have decided where to shoot or even specific locations you want to use. Once you have determined your scenes and locations, it is time to start figuring out the elements that you will need for each scene. You might decide you need a car, but not sure what make or model. This is where you can look up car models online and narrow down your options by choosing from different makes and models.
Once you have found the right vehicle, you can think about adding accessories. You might need to have people in the front seats. Perhaps you have someone who needs to be able to walk around the back of your car. You may want to change the interior's color from black or white. These questions will help guide you in determining the ideal look and feel for your car. It is also worth considering the types of shots that you wish to take. What type of shots will you choose? Maybe you want to show the engine and the steering wheel. This will allow you to determine the type of car you want.
Once you have made all the necessary decisions, you can start to create a schedule. You can use a schedule to determine when and where you need it to be shot. The schedule will show you when to get there, what time to leave, and when to return home. Everyone knows exactly what they should do and when. Book extra staff ahead of time if you need them. There is no point in hiring someone who won't turn up because you didn't let him know.
It is important to calculate the amount of filming days when you are creating your schedule. Some projects are quick and easy, while others take weeks. You should consider whether you will need more than one shot per week when creating your schedule. Multiple takes at the same place will result in higher costs and longer completion times. If you are unsure if you need multiple takes, it is better to err on the side of caution and shoot fewer takes rather than risk wasting money.
Budget setting is another important aspect in production planning. As it will allow you and your team to work within your financial means, setting a realistic budget is crucial. Keep in mind that you can always reduce your budget if you face unexpected difficulties. But, don't underestimate how much money you'll spend. You will end up spending less money if you underestimate the cost of something.
Production planning is a detailed process. But, once you understand the workings of everything, it becomes easier for future projects to be planned.
What are the logistics products?
Logistics involves the transportation of goods from point A and point B.
They include all aspects associated with transport including packaging, loading transporting, unloading storage, warehousing inventory management customer service, distribution returns and recycling.
Logisticians ensure the product reaches its destination in the most efficient manner. They assist companies with their supply chain efficiency through information on demand forecasts. Stock levels, production times, and availability.
They monitor shipments in transit, ensure quality standards, manage inventories, replenish orders, coordinate with suppliers and other vendors, and offer support services for sales, marketing, and customer service.
What does it take for a logistics enterprise to succeed?
It takes a lot of skills and knowledge to run a successful logistics business. To communicate effectively with clients and suppliers, you must be able to communicate well. You will need to know how to interpret data and draw conclusions. You must be able and able to handle stress situations and work under pressure. To improve efficiency, you must be innovative and creative. To motivate and guide your team towards reaching organizational goals, you must have strong leadership skills.
You should also be organized and efficient to meet tight deadlines.
How can we improve manufacturing efficiency?
The first step is to determine the key factors that impact production time. Next, we must find ways to improve those factors. If you don’t know how to start, look at which factors have the greatest impact upon production time. Once you've identified them, try to find solutions for each of those factors.
Statistics
- In the United States, for example, manufacturing makes up 15% of the economic output. (twi-global.com)
- In 2021, an estimated 12.1 million Americans work in the manufacturing sector.6 (investopedia.com)
- Job #1 is delivering the ordered product according to specifications: color, size, brand, and quantity. (netsuite.com)
- You can multiply the result by 100 to get the total percent of monthly overhead. (investopedia.com)
- (2:04) MTO is a production technique wherein products are customized according to customer specifications, and production only starts after an order is received. (oracle.com)
External Links
How To
How to Use the 5S to Increase Productivity In Manufacturing
5S stands in for "Sort", the "Set In Order", "Standardize", or "Separate". Toyota Motor Corporation created the 5S methodology in 1954. It assists companies in improving their work environments and achieving higher efficiency.
This method aims to standardize production processes so that they are repeatable, measurable and predictable. It means tasks like cleaning, sorting or packing, labeling, and storing are done every day. Workers can be more productive by knowing what to expect.
Implementing 5S requires five steps. These are Sort, Set In Order, Standardize. Separate. And Store. Each step has a different action and leads to higher efficiency. Sorting things makes it easier to find them later. When you set items in an order, you put items together. Then, after you separate your inventory into groups, you store those groups in containers that are easy to access. Finally, label all containers correctly.
Employees will need to be more critical about their work. Employees must understand why they do certain tasks and decide if there's another way to accomplish them without relying on the old ways of doing things. In order to use the 5S system effectively, they must be able to learn new skills.
In addition to increasing efficiency, the 5S method also improves morale and teamwork among employees. Once they start to notice improvements, they are motivated to keep working towards their goal of increasing efficiency.