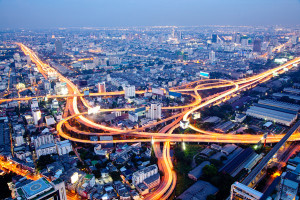
There are many lucrative jobs available in mathematics. In many cities, mathematicians are highly sought after. Mathematicians use math to solve real world problems, and they can find jobs in the private and public sectors. The Human Genome Project, for example, was made possible by mathematicians. Mathematicians use mathematical theory, algorithms, and computational techniques to solve problems. Their work is also supported by the latest computer technology. Mathematicians can send secure emails and buy items online securely. They also solve complex data points.
A mathematician's salary is usually higher than the average salary. These salaries are typically very generous and allow for a comfortable lifestyle. To increase their earning potential, mathematicians have the option to get a graduate degree. The average mathematician's salary is $103,000 per annum. This can change depending on where you reside and what industry it is.
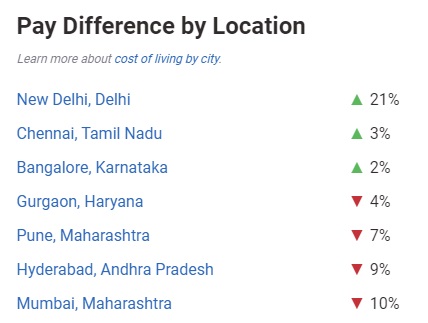
The specialty of applied mathematics is math that emphasizes using math in science, engineering and business. Applied mathematicians blend mathematical theory with specialized knowledge to find solutions to specific problems. Mathematicians may work in many different fields such as finance, ecology, engineering, and finance. Applied mathematicians also have the ability to work in healthcare, long-term care, and other areas.
Payrolls for mathematicians are high, especially in the federal sector. This field is a vital part of the allocation of resources for the largest military in the world. Mathematicians are required to work with data. There are many databases that give insight into different sectors. This information is used in the allocation of resources for the military, federal bugets, and other large programmes. Mathematicians with bachelor's degrees can seek entry-level positions in the public or private sectors. Specialized training is necessary for government careers.
Applied mathematicians will also be needed in the banking, finance, and insurance industries. These mathematicians can specialize in digital imaging, ecology and economics. Mathematicians can analyze the aerodynamic characteristics, as well as the effectiveness of drugs. They also provide information about liability insurance and insurance for property.
Applied mathematicians might also be employed in hospitals and insurance companies. The government also needs mathematicians to provide information on large programs. A master's degree in mathematics can lead to employment in many industries, such as finance, actuarial and computer science. As mathematicians use data and algorithms to solve complex issues, they may also be able to find work in research.
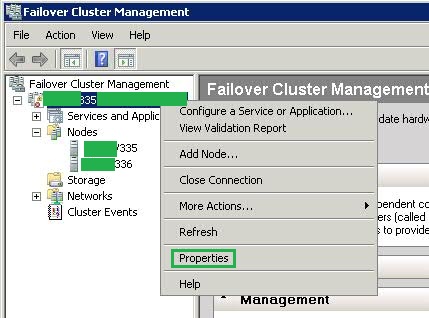
Because math majors can take a wide range of finance classes, many choose to go into business or finance. This could lead you to a career of actuary, budget analyst, or financial advisor. These individuals can also look for work in cybersecurity and cryptography. Computer development can also be possible with a master's in mathematics. The salary of those with a master's in math can increase by 38% over those without a bachelor's.
FAQ
What is the difference between manufacturing and logistics
Manufacturing is the process of creating goods from raw materials by using machines and processes. Logistics encompasses the management of all aspects associated with supply chain activities such as procurement, production planning, distribution and inventory control. It also includes customer service. Manufacturing and logistics are often considered together as a broader term that encompasses both the process of creating products and delivering them to customers.
What are the differences between these four types?
Manufacturing is the process by which raw materials are transformed into useful products through machines and processes. Manufacturing can include many activities such as designing and building, testing, packaging shipping, selling, servicing, and other related activities.
How can overproduction in manufacturing be reduced?
Better inventory management is key to reducing excess production. This would reduce the amount of time spent on unnecessary activities such as purchasing, storing, and maintaining excess stock. This could help us free up our time for other productive tasks.
You can do this by adopting a Kanban method. A Kanbanboard is a visual tool that allows you to keep track of the work being done. In a Kanban system, work items move through a sequence of states until they reach their final destination. Each state represents a different priority level.
As an example, if work is progressing from one stage of the process to another, then the current task is complete and can be transferred to the next. But if a task remains in the beginning stages it will stay that way until it reaches its end.
This allows work to move forward and ensures that no work is missed. Managers can see how much work has been done and the status of each task at any time with a Kanban Board. This information allows managers to adjust their workflow based off real-time data.
Lean manufacturing can also be used to reduce inventory levels. Lean manufacturing emphasizes eliminating waste in all phases of production. Any product that isn't adding value can be considered waste. Here are some examples of common types.
-
Overproduction
-
Inventory
-
Packaging not required
-
Overstock materials
Manufacturers can reduce their costs and improve their efficiency by using these ideas.
Why automate your warehouse?
Modern warehouses have become more dependent on automation. E-commerce has increased the demand for quicker delivery times and more efficient processes.
Warehouses should be able adapt quickly to new needs. Technology investment is necessary to enable warehouses to respond quickly to changing demands. The benefits of automating warehouses are numerous. These are some of the benefits that automation can bring to warehouses:
-
Increases throughput/productivity
-
Reduces errors
-
Improves accuracy
-
Safety is boosted
-
Eliminates bottlenecks
-
Allows companies scale more easily
-
Workers are more productive
-
The warehouse can be viewed from all angles.
-
Enhances customer experience
-
Improves employee satisfaction
-
This reduces downtime while increasing uptime
-
Ensures quality products are delivered on time
-
Eliminates human error
-
Assure compliance with regulations
What is production plan?
Production Planning includes planning for all aspects related to production. This document will ensure everything is in order and ready to go when you need it. This document should also include information on how to get the best result on set. This includes location information, crew details, equipment specifications, and casting lists.
The first step in filming is to define what you want. You may already know where you want the film to be shot, or perhaps you have specific locations and sets you wish to use. Once you have identified the scenes and locations, you can start to determine which elements are required for each scene. If you decide you need a car and don't know what model to choose, this could be an example. To narrow your options, you can search online for available models.
Once you have found the right car, you can start thinking about extras. Are you looking for people to sit in the front seats? You might also need someone to help you get around the back. Maybe you want to change the interior color from black to white? These questions can help you decide the right look for your car. It is also worth considering the types of shots that you wish to take. What type of shots will you choose? Maybe you want the engine or the steering wheels to be shown. These things will help you to identify the car that you are looking for.
Once you have all the information, you are ready to create a plan. A schedule will tell you when you need to start shooting and when you need to finish. Every day will have a time for you to arrive at the location, leave when you are leaving and return home when you are done. It will help everyone know exactly what they have to do and when. You can also make sure to book extra staff in advance if you have to hire them. You don't want to hire someone who won't show up because he didn't know.
Also, consider how many days you will be filming your schedule. Some projects take only a few days while others can last several weeks. You should consider whether you will need more than one shot per week when creating your schedule. Multiple shots at the same location can increase costs and make it more difficult to complete. If you are unsure if you need multiple takes, it is better to err on the side of caution and shoot fewer takes rather than risk wasting money.
Budget setting is another important aspect in production planning. A realistic budget will help you work within your means. Remember that you can always reduce the budget later on if you run into unforeseen problems. But, don't underestimate how much money you'll spend. If you underestimate the cost of something, you will have less money left after paying for other items.
Planning production is a tedious process. Once you have a good understanding of how everything works together, planning future projects becomes easy.
How can manufacturing prevent production bottlenecks?
To avoid production bottlenecks, ensure that all processes run smoothly from the moment you receive your order to the time the product ships.
This includes both planning for capacity and quality control.
Continuous improvement techniques like Six Sigma are the best way to achieve this.
Six Sigma is a management method that helps to improve quality and reduce waste.
It is focused on creating consistency and eliminating variation in your work.
What are the responsibilities of a manufacturing manager
Manufacturing managers must ensure that manufacturing processes are efficient, effective, and cost-effective. They should also be aware and responsive to any company problems.
They should also be able communicate with other departments, such as sales or marketing.
They must also keep up-to-date with the latest trends in their field and be able use this information to improve productivity and efficiency.
Statistics
- [54][55] These are the top 50 countries by the total value of manufacturing output in US dollars for its noted year according to World Bank.[56] (en.wikipedia.org)
- In the United States, for example, manufacturing makes up 15% of the economic output. (twi-global.com)
- Job #1 is delivering the ordered product according to specifications: color, size, brand, and quantity. (netsuite.com)
- You can multiply the result by 100 to get the total percent of monthly overhead. (investopedia.com)
- According to the United Nations Industrial Development Organization (UNIDO), China is the top manufacturer worldwide by 2019 output, producing 28.7% of the total global manufacturing output, followed by the United States, Japan, Germany, and India.[52][53] (en.wikipedia.org)
External Links
How To
How to use 5S in Manufacturing to Increase Productivity
5S stands for "Sort", "Set In Order", "Standardize", "Separate" and "Store". Toyota Motor Corporation invented the 5S strategy in 1954. It assists companies in improving their work environments and achieving higher efficiency.
This method aims to standardize production processes so that they are repeatable, measurable and predictable. This means that every day tasks such cleaning, sorting/storing, packing, and labeling can be performed. Through these actions, workers can perform their jobs more efficiently because they know what to expect from them.
Implementing 5S involves five steps: Sort, Set in Order, Standardize Separate, Store, and Each step involves a different action which leads to increased efficiency. For example, when you sort things, you make them easy to find later. You arrange items by placing them in an order. After you have divided your inventory into groups you can store them in easy-to-reach containers. Make sure everything is correctly labeled when you label your containers.
Employees will need to be more critical about their work. Employees need to be able understand their motivations and discover alternative ways to do them. To be successful in the 5S system, employees will need to acquire new skills and techniques.
In addition to increasing efficiency, the 5S method also improves morale and teamwork among employees. As they begin to see improvements, they feel motivated to continue working towards the goal of achieving higher levels of efficiency.