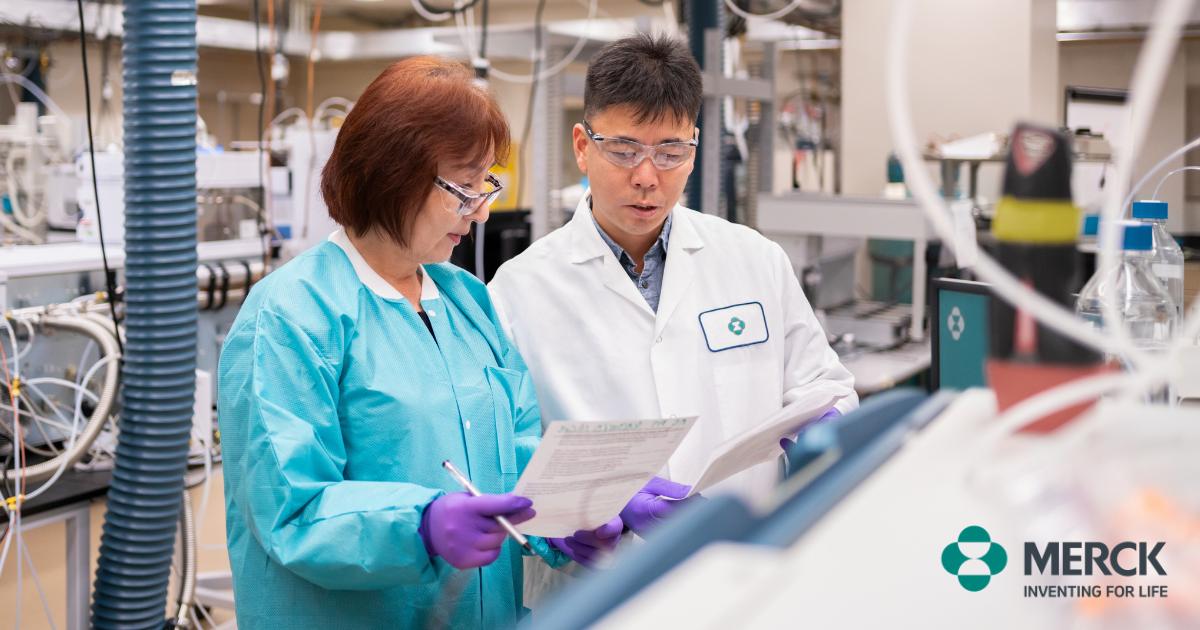
A variety of factors can cause supply chain disruptions. You can think of natural disasters, product recalls, or delays in transport as examples. These disruptions can lead to price increases or margin cuts. Companies may also need to adjust their sourcing strategies in an effort to continue production. In many cases, companies will need to re-evaluate their supply networks, diversify their production, and audit their current inventories to prepare for the next disruption.
Diverse industries like transportation, electronics and pharmaceuticals have had to deal with disruptions in supply chains. In some cases, the disruption was due to an internal issue at a company, while in other cases it was a response to a global event. One example is a pandemic that caused widespread health disruptions across several countries. It also had a negative impact on the retail sector. The pandemic forced governments into adopting policies to stop the spread of the disease.
Pandemics can cause disruption to a company's distribution system, workforce, and manufacturing process. Companies will need to adjust their supply and production chains and reevaluate the impact on production. Depending on how severe the disruption is, the impact could last from weeks to months. Businesses will need to evaluate their inventory and, if necessary, reallocate capital.
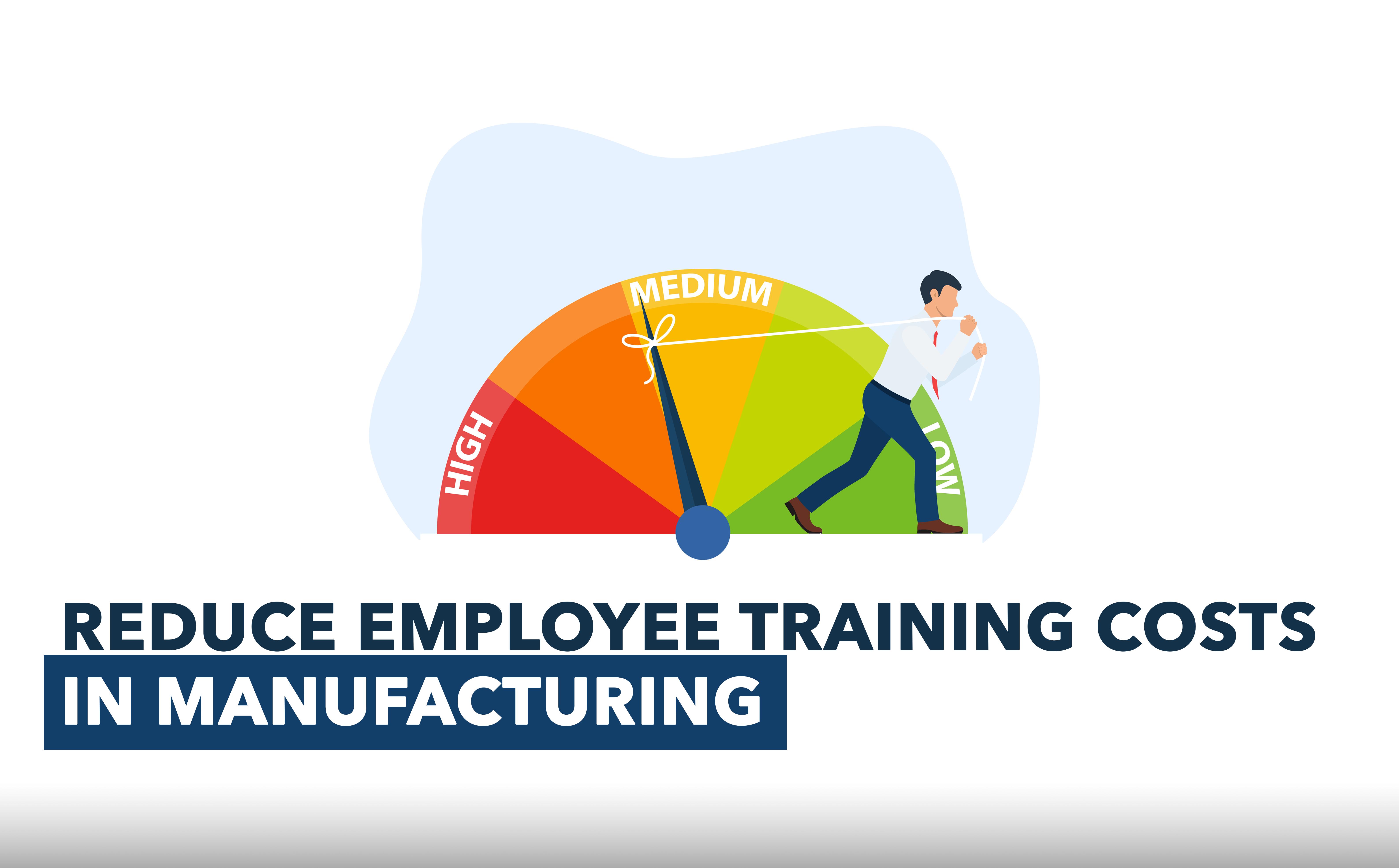
Disruption may occur at any stage in the supply chain and can impact both supply or demand. In most instances, the demand side will be more affected than the supply side. However, a pandemic that disrupts the supply will cause ripple effects throughout the economy.
Supply chain disruptions can cause major impacts to a business, and they are often difficult to predict. While it is easy to identify seasonal fluctuations, it is more challenging to predict a rapid shift in consumer behavior. These risks can be mitigated by using predictive analytics to spot potential problems.
Labor shortages are another common cause of disruption in supply chains. Unreliable suppliers can cause companies to lose productivity. A machine failure can also disrupt an entire operation.
Natural disasters and market fluctuations are the main causes of supply chain disruptions. Natural disasters, which are expensive, can cause disruptions in the global supply chain. Another cause of disruption in supply chains is a power outage or telecommunications blackout. Companies may have to store large quantities of stock in order to protect their businesses.
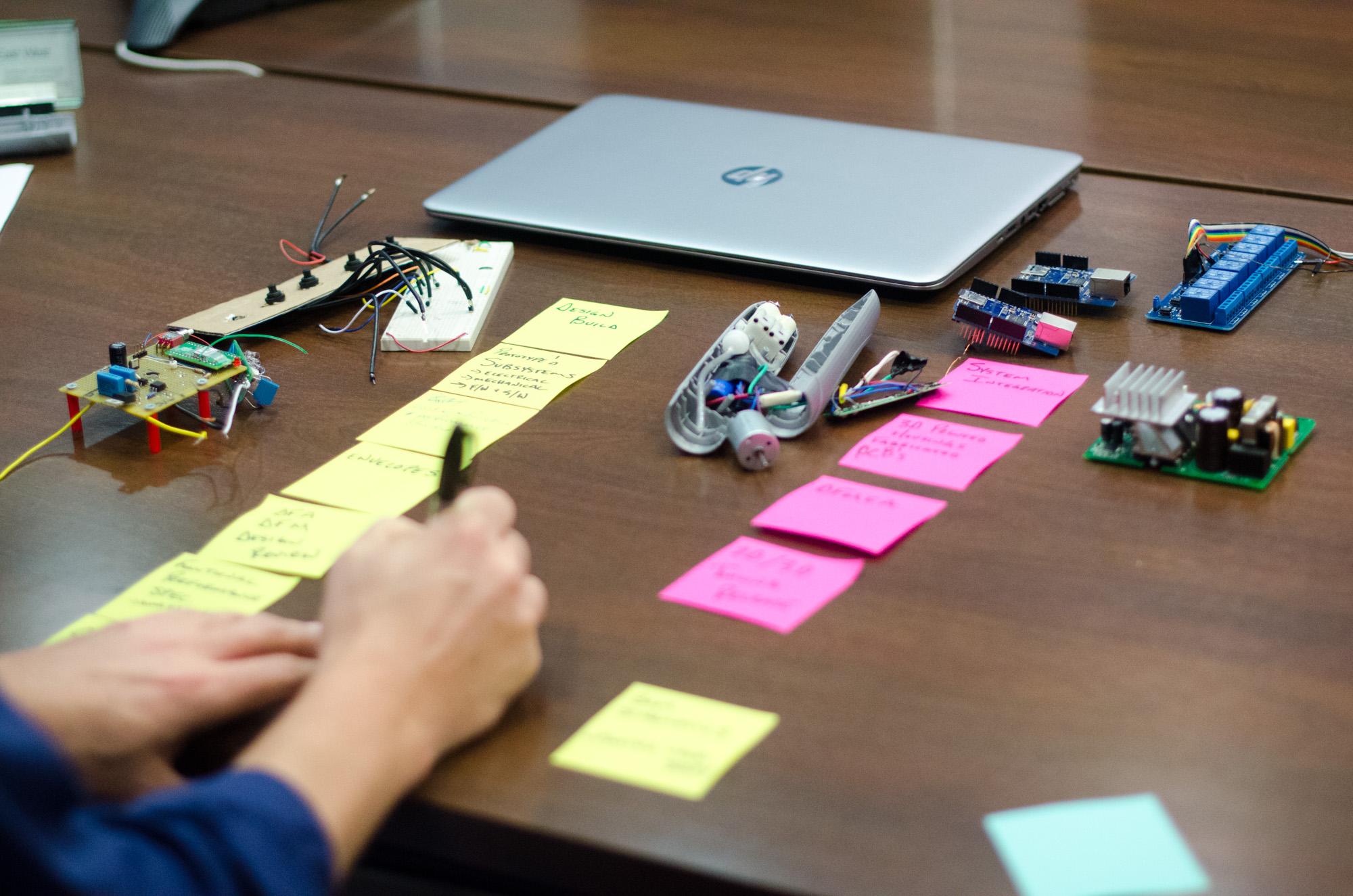
As a general rule, disruptions to supply chains have very little impact. Companies will need action to detect disruptions and most companies will need it at some point. It's important to recognize problems early in order to avoid conflict.
In a recent survey, Ernest & Young LLP found that 72 percent of companies have experienced a disruption at some point, and 57 percent have reported adverse effects. While many of these issues can be fixed quickly, others require a more strategic approach.
FAQ
What is the role of a production manager?
Production planners ensure that all project aspects are completed on time, within budget and within the scope. A production planner ensures that the service and product meet the client's expectations.
Why is logistics so important in manufacturing?
Logistics is an integral part of every business. They help you achieve great results by helping you manage all aspects of product flow, from raw materials to finished goods.
Logistics also play a major role in reducing costs and increasing efficiency.
How can manufacturing efficiency be improved?
The first step is to determine the key factors that impact production time. The next step is to identify the most important factors that affect production time. If you aren't sure where to begin, think about the factors that have the greatest impact on production time. Once you've identified them, try to find solutions for each of those factors.
Statistics
- It's estimated that 10.8% of the U.S. GDP in 2020 was contributed to manufacturing. (investopedia.com)
- According to the United Nations Industrial Development Organization (UNIDO), China is the top manufacturer worldwide by 2019 output, producing 28.7% of the total global manufacturing output, followed by the United States, Japan, Germany, and India.[52][53] (en.wikipedia.org)
- You can multiply the result by 100 to get the total percent of monthly overhead. (investopedia.com)
- [54][55] These are the top 50 countries by the total value of manufacturing output in US dollars for its noted year according to World Bank.[56] (en.wikipedia.org)
- In 2021, an estimated 12.1 million Americans work in the manufacturing sector.6 (investopedia.com)
External Links
How To
Six Sigma in Manufacturing:
Six Sigma is defined by "the application SPC (statistical process control) techniques to achieve continuous improvements." Motorola's Quality Improvement Department created Six Sigma at their Tokyo plant, Japan in 1986. Six Sigma's basic concept is to improve quality and eliminate defects through standardization. Many companies have adopted Six Sigma in recent years because they believe that there are no perfect products and services. Six Sigma's primary goal is to reduce variation from the average value of production. If you take a sample and compare it with the average, you will be able to determine how much of the production process is different from the norm. If you notice a large deviation, then it is time to fix it.
Understanding how your business' variability is a key step towards Six Sigma implementation is the first. Once you have a good understanding of the basics, you can identify potential sources of variation. This will allow you to decide if these variations are random and systematic. Random variations occur when people make mistakes; systematic ones are caused by factors outside the process itself. If you make widgets and some of them end up on the assembly line, then those are considered random variations. But if you notice that every widget you make falls apart at the exact same place each time, this would indicate that there is a problem.
Once you identify the problem areas, it is time to create solutions. You might need to change the way you work or completely redesign the process. Once you have implemented the changes, it is important to test them again to ensure they work. If they don’t work, you’ll need to go back and rework the plan.