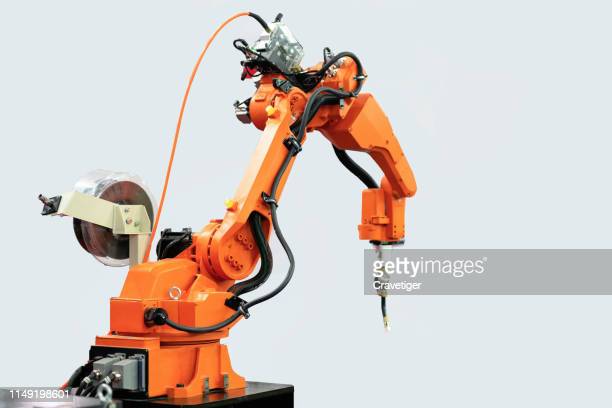
If you want to ensure your product is profitable, it is important to factor in manufacturing costs. If you plan to sell wooden tabletop furniture, then you will need to purchase adhesives, wood, and other materials. For your products to last, you will need to be able find reliable suppliers of high quality raw materials. You can end up with a defective item and lost revenue if your supplier does not provide high quality raw material.
It is best to break down manufacturing costs into three categories. Each of these costs will have an effect on the final cost of the product you are selling. The unit cost is a key component of manufacturing costs. It's the cost it takes to produce an item. While this number can be a good starting point, it is difficult to quantify.
It is a good idea to use the units-perhour (or unit-perunit ratio) as a guideline when choosing the most cost-effective manufacturing process. To illustrate, let's say you want to make 5,000 wooden table tops. You can find the average cost by subtracting the amount of time required to complete the project.
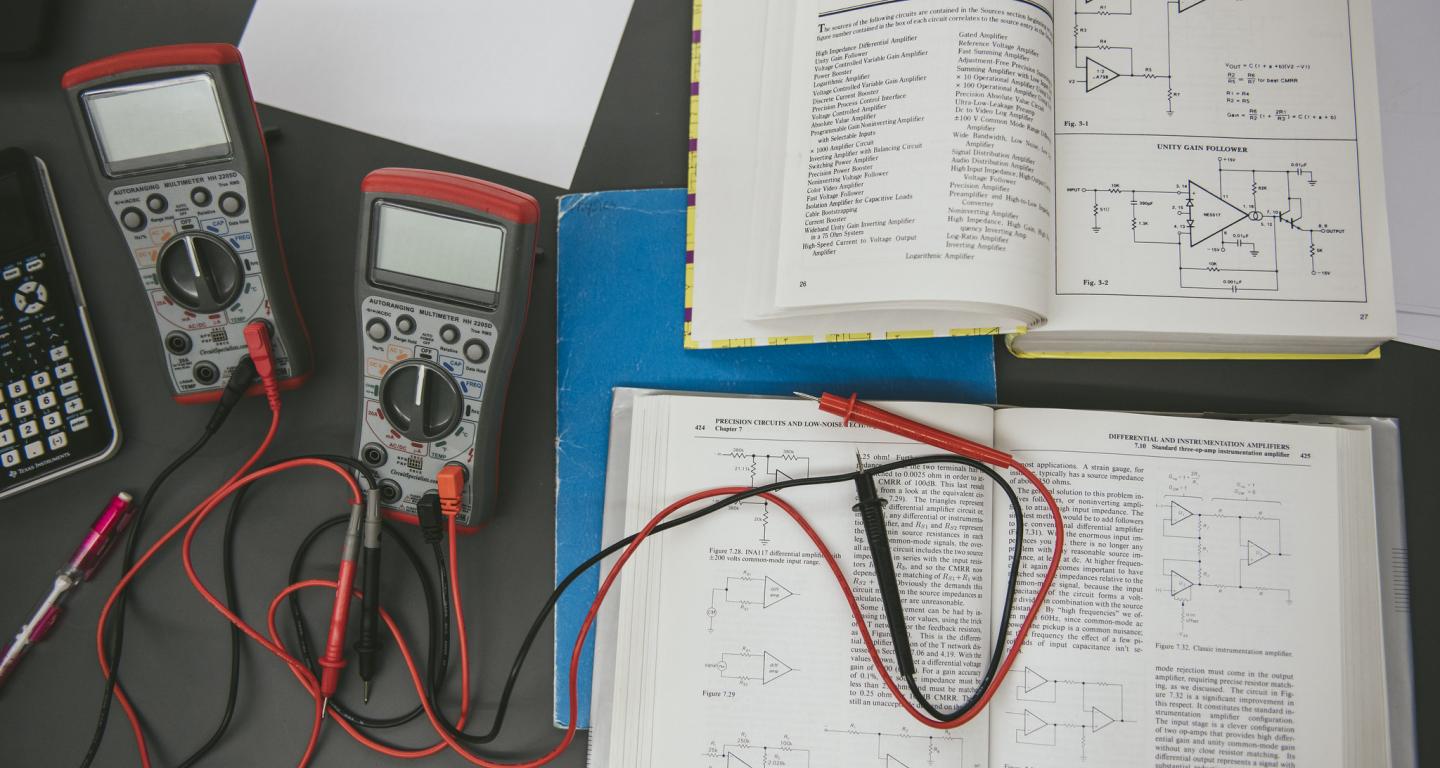
A budget will be needed for administrative and general costs. These expenses can include advertising costs and office supplies, rent, or sales commissions. You will also need to spend large amounts to meet regulatory requirements. However, these expenses can be reduced by using online inventory software to track production or forecast production.
Direct labor costs refer to wages that are paid to workers at a factory. They include employees who prepare the goods for manufacture. They can also include maintenance personnel, sanitation personnel and bookkeepers. In general, the hourly wage for direct labor is around $150.
Indirect costs, which are part manufacturing, include utilities bills and equipment maintenance. To calculate the unit-per-hour you need to include the costs of preparation, assembly and delivery. A manufacturing overhead account is a tool that will allow you calculate the total cost for your operation and give you an estimate of your overhead in the coming fiscal year.
When calculating manufacturing costs, you should also consider the indirect and direct materials that were used in the manufacture of the product. Wood, thread, or cotton are just a few examples. Using low quality materials can lead to an inferior final product, and if you are a food manufacturer in certain parts of the world, you'll need to test your products to make sure they are safe to eat.
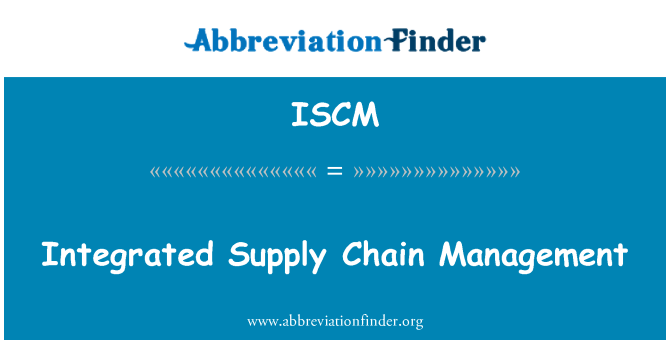
The unit-per -unit ratio of your products and their manufacturing costs will help you decide whether or not to produce a product. You should also know the price you should charge for your products to increase your business' profitability.
FAQ
Why automate your warehouse
Modern warehousing has seen automation take center stage. The rise of e-commerce has led to increased demand for faster delivery times and more efficient processes.
Warehouses must adapt quickly to meet changing customer needs. Technology is essential for warehouses to be able to adapt quickly to changing needs. Automation of warehouses offers many benefits. Here are some reasons why it's worth investing in automation:
-
Increases throughput/productivity
-
Reduces errors
-
Increases accuracy
-
Safety enhancements
-
Eliminates bottlenecks
-
Allows companies to scale more easily
-
Workers are more productive
-
Gives you visibility into all that is happening in your warehouse
-
Enhances customer experience
-
Improves employee satisfaction
-
Minimizes downtime and increases uptime
-
High quality products delivered on-time
-
Removes human error
-
It helps ensure compliance with regulations
What are the 7 Rs of logistics?
The acronym "7R's" of Logistics stands for seven principles that underpin logistics management. It was published in 2004 by the International Association of Business Logisticians as part of their "Seven Principles of Logistics Management" series.
The following letters form the acronym:
-
Responsible – ensure that all actions are legal and don't cause harm to anyone else.
-
Reliable - Have confidence in your ability to fulfill all of your commitments.
-
Be responsible - Use resources efficiently and avoid wasting them.
-
Realistic - Consider all aspects of operations, including environmental impact and cost effectiveness.
-
Respectful - show respect and treat others fairly and fairly
-
You are resourceful and look for ways to save money while increasing productivity.
-
Recognizable provides value-added products and services to customers
What does it take for a logistics enterprise to succeed?
You need to have a lot of knowledge and skills to manage a successful logistic business. Good communication skills are essential to effectively communicate with your suppliers and clients. You need to understand how to analyze data and draw conclusions from it. You need to be able work under pressure and manage stressful situations. In order to innovate and create new ways to improve efficiency, creativity is essential. You will need strong leadership skills to motivate and direct your team members towards achieving their organizational goals.
To meet tight deadlines, you must also be efficient and organized.
How does a production planner differ from a project manager?
The major difference between a Production Planner and a Project Manager is that a Project Manager is often the person responsible for organizing and planning the entire project. While a Production Planner is involved mainly in the planning stage,
Statistics
- According to the United Nations Industrial Development Organization (UNIDO), China is the top manufacturer worldwide by 2019 output, producing 28.7% of the total global manufacturing output, followed by the United States, Japan, Germany, and India.[52][53] (en.wikipedia.org)
- In 2021, an estimated 12.1 million Americans work in the manufacturing sector.6 (investopedia.com)
- You can multiply the result by 100 to get the total percent of monthly overhead. (investopedia.com)
- In the United States, for example, manufacturing makes up 15% of the economic output. (twi-global.com)
- It's estimated that 10.8% of the U.S. GDP in 2020 was contributed to manufacturing. (investopedia.com)
External Links
How To
Six Sigma in Manufacturing
Six Sigma is defined as "the application of statistical process control (SPC) techniques to achieve continuous improvement." Motorola's Quality Improvement Department in Tokyo, Japan developed Six Sigma in 1986. The basic idea behind Six Sigma is to improve quality by improving processes through standardization and eliminating defects. Since there are no perfect products, or services, this approach has been adopted by many companies over the years. Six Sigma aims to reduce variation in the production's mean value. If you take a sample and compare it with the average, you will be able to determine how much of the production process is different from the norm. If it is too large, it means that there are problems.
Understanding the nature of variability in your business is the first step to Six Sigma. Once you've understood that, you'll want to identify sources of variation. It is important to identify whether the variations are random or systemic. Random variations occur when people do mistakes. Symmetrical variations are caused due to factors beyond the process. These are, for instance, random variations that occur when widgets are made and some fall off the production line. But if you notice that every widget you make falls apart at the exact same place each time, this would indicate that there is a problem.
Once you've identified the problem areas you need to find solutions. You might need to change the way you work or completely redesign the process. Test them again once you've implemented the changes. If they fail, you can go back to the drawing board to come up with a different plan.