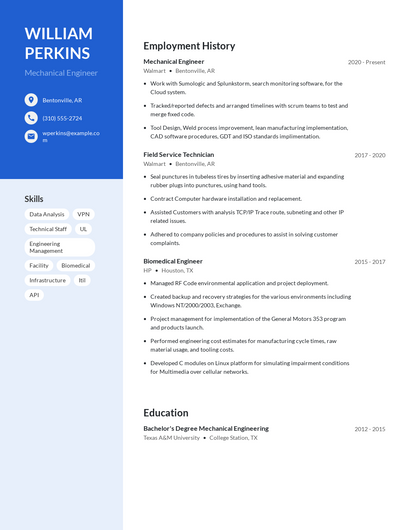
Lean thinking is a method to improve performance in an organization. It's about eliminating wastes and unvalued tasks from your process. It can also be used to establish a lean culture in your company. A lean cultural is a set if values, principles, or practices that are designed to increase employee morale as well as quality and productivity. It promotes a more sustainable workplace.
To implement lean thinking, the first step is to identify customer value. This involves understanding the entire chain of value and the customer needs. This will allow you to identify the steps involved in your current process. By identifying the steps within different processes, you can determine if your current process is inefficient. You can also use the value stream map to see how your company is currently operating. The value stream mapping shows how your business works and the value that each process creates.
Lean thinking is all about flow. It is the ability of switching quickly between activities. This is particularly important for responding to customer demands. This reduces inventory and backlogs. It allows workers to quickly switch tasks.
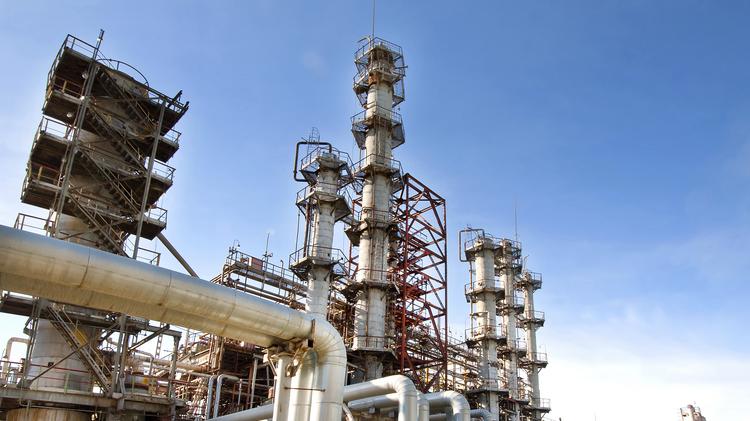
Lean organizations adopt a lean approach to managing output. They encourage collaboration and clear communication. They encourage quality assurance, and celebrate the successes. They also reduce unnecessary over-costs to suppliers or customers.
Lean thinking involves a continual process. It can be applied to any type or work. It can help to reduce environmental damage, reduce the waste, and improve employee motivation. Although lean thinking is often used in manufacturing, it can be used in all areas of business.
A culture that encourages lean thinking and collaboration is key to implementing lean production techniques. It should be clear about the value of lean production practices, as well as the motivation of employees. It must also be willing, on a consistent basis, to take small steps ahead. This is called Kaizen.
Lean thinking requires continuous improvement. For example, if you are looking to improve the quality of your product, you need to be willing to make small improvements on a daily basis. This can be accomplished either by implementing changes to the organization or using standardized works. A standardized job is a description of a seamless flow of work. Everything is clearly located. It helps people see how to overcome obstacles and make work easier.
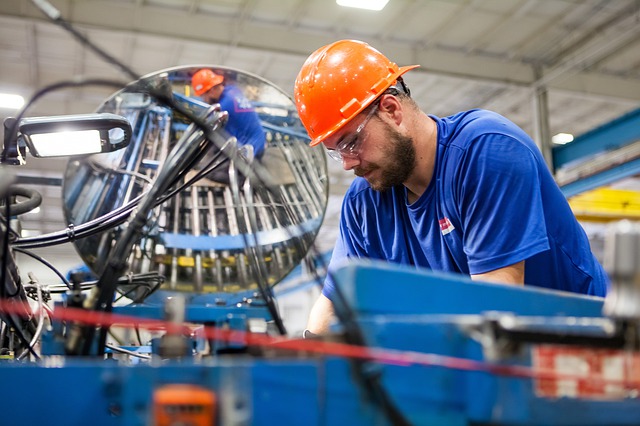
When implementing lean production methods, it is important to also consider other production metrics. For example, the ratio of downtime to running time shows how often an asset is available for production. It also shows how frequent maintenance is needed. It is an indicator of the supplier's ability to deliver quality products.
The "Just-In Time" principle has risks. This principle ensures that supplies are delivered at the last minute. It helps you focus your mind on the task at the hand and allows you to concentrate. However, it can create problems for the industry.
FAQ
What is meant by manufacturing industries?
Manufacturing Industries refers to businesses that manufacture products. Consumers are the people who purchase these products. These companies employ many processes to achieve this purpose, such as production and distribution, retailing, management and so on. They create goods from raw materials, using machines and various other equipment. This includes all types if manufactured goods.
What are the four types in manufacturing?
Manufacturing is the process of transforming raw materials into useful products using machines and processes. Manufacturing involves many activities, including designing, building, testing and packaging, shipping, selling, service, and so on.
What is the responsibility of a manufacturing manager?
Manufacturing managers must ensure that manufacturing processes are efficient, effective, and cost-effective. They must also be alert to any potential problems and take appropriate action.
They must also be able to communicate with sales and marketing departments.
They should be up to date on the latest trends and be able apply this knowledge to increase productivity and efficiency.
Can we automate some parts of manufacturing?
Yes! Since ancient times, automation has been in existence. The Egyptians created the wheel thousands years ago. Today, robots assist in the assembly of lines.
Robotics is used in many manufacturing processes today. These include:
-
Automation line robots
-
Robot welding
-
Robot painting
-
Robotics inspection
-
Robots that produce products
Automation can be applied to manufacturing in many other ways. 3D printing, for example, allows us to create custom products without waiting for them to be made.
What is the difference in Production Planning and Scheduling, you ask?
Production Planning (PP), is the process of deciding what production needs to take place at any given time. Forecasting demand is one way to do this.
Scheduling is the process of assigning specific dates to tasks so they can be completed within the specified timeframe.
What is manufacturing and logistics?
Manufacturing is the act of producing goods from raw materials using machines and processes. Logistics manages all aspects of the supply chain, including procurement, production planning and distribution, inventory control, transportation, customer service, and transport. Manufacturing and logistics can often be grouped together to describe a larger term that covers both the creation of products, and the delivery of them to customers.
Statistics
- Job #1 is delivering the ordered product according to specifications: color, size, brand, and quantity. (netsuite.com)
- You can multiply the result by 100 to get the total percent of monthly overhead. (investopedia.com)
- According to the United Nations Industrial Development Organization (UNIDO), China is the top manufacturer worldwide by 2019 output, producing 28.7% of the total global manufacturing output, followed by the United States, Japan, Germany, and India.[52][53] (en.wikipedia.org)
- In the United States, for example, manufacturing makes up 15% of the economic output. (twi-global.com)
- Many factories witnessed a 30% increase in output due to the shift to electric motors. (en.wikipedia.org)
External Links
How To
How to use 5S in Manufacturing to Increase Productivity
5S stands for "Sort", 'Set In Order", 'Standardize', & Separate>. Toyota Motor Corporation developed the 5S method in 1954. It allows companies to improve their work environment, thereby achieving greater efficiency.
The idea behind standardizing production processes is to make them repeatable and measurable. This means that daily tasks such as cleaning and sorting, storage, packing, labeling, and packaging are possible. This knowledge allows workers to be more efficient in their work because they are aware of what to expect.
There are five steps that you need to follow in order to implement 5S. Each step involves a different action which leads to increased efficiency. For example, when you sort things, you make them easy to find later. Once you have placed items in an ordered fashion, you will put them together. You then organize your inventory in groups. Finally, when you label your containers, you ensure everything is labeled correctly.
Employees must be able to critically examine their work practices. Employees must be able to see why they do what they do and find a way to achieve them without having to rely on their old methods. To be successful in the 5S system, employees will need to acquire new skills and techniques.
The 5S method not only increases efficiency but also boosts morale and teamwork. As they begin to see improvements, they feel motivated to continue working towards the goal of achieving higher levels of efficiency.