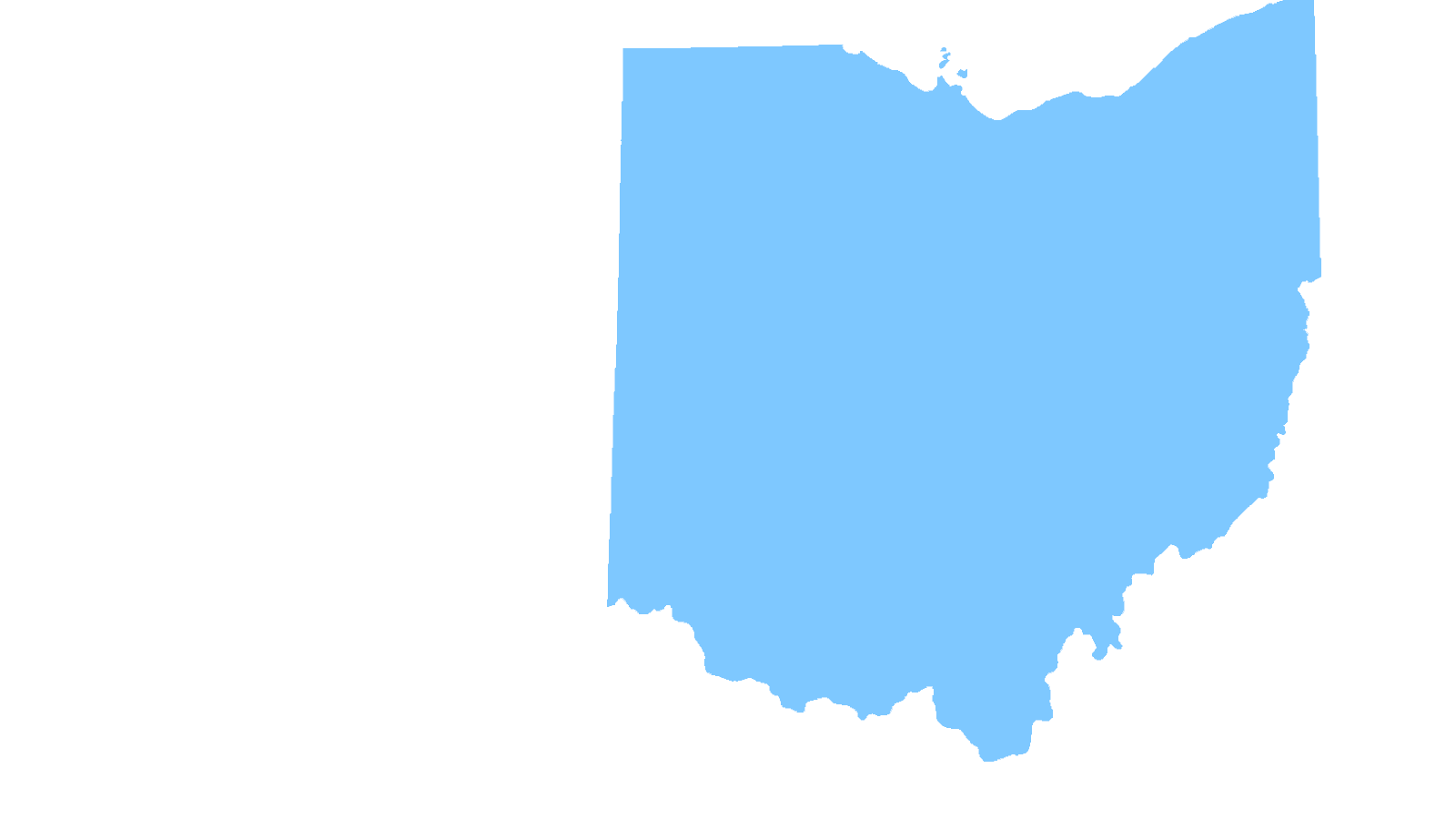
Supply Dynamics, a multi-enterprise supply channel analytics suite, was established in Loveland Ohio in 2003. It provides technology solutions to manufacturers operating in highly distributed manufacturing environments. Supply Dynamics collaborates closely with the Navy's Defense Logistics Agency. It gives visibility and control over an organization's entire supply chain. It assists manufacturers in planning production and reducing the cost of raw material. Supply Dynamics works with a variety of industries including aerospace, defense, manufacturing, and transportation.
Dynamics 365 Supply Chain Management (powered by Microsoft Cloud) is a Microsoft Cloud-powered software that enables organizations improve operational efficiency, streamline manufacturing, and build strong supply chain networks. It provides unparalleled visibility into the supply chain from beginning to end, with unrivalled flexibility and predictive analytics. Its modules ensure that products reach their customers on-time and provide functionality for the entire product lifecycle.
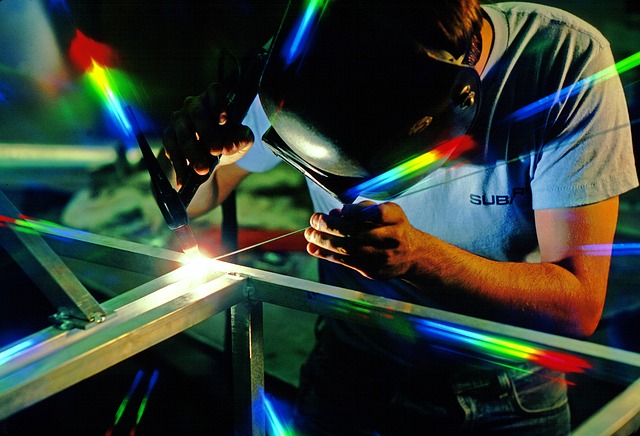
The Dynamics Supply Chain module features include the ability to submit RFQs, configure discrete items, submit purchase orders, submit RFQs, and test product quality. Gantt charts are also available to give transparency to all operations. Visual Supply Schedule lets users see the forecast of inventory levels and anticipated demand. You can also modify the schedules if there are supply chain problems. It also provides managers with the ability to track progress of job functions in various areas of a production floor.
Microsoft Dynamics 365 Supply Chain Management gives organizations a unified, predictive way to manage customer demands and ensure the right materials are available at the right moment. It is also useful for businesses in anticipating customer needs and changing capacity. It can be used on multiple sites and warehouses, and integrates logistics purchasing and production. It also supports vendor-specific pricing, multiple inventory costing methods, and transportation management. The solution also supports the use of inventory optimization and predictive analytics, as well as AI features.
Dynamics 365 also offers self-service for suppliers. Suppliers can accept and reject purchase orders, raise invoices on POs, and enter shipment information for existing POs. You can also use it to calculate inventory costs, including vendor-specific pricing, item-level and item-group pricing. It also includes several inventory optimization features, including the ability to create an inventory allocation plan for an order.
Supply Dynamics offers unique solutions for benchmarking metals prices. This technology allows manufacturers faster response to fluctuations in market conditions. They can also predict and anticipate fluctuations in production costs. This technology can reduce manufacturing costs and reduce waste. It also gives manufacturers a blueprint for data conversion to bill-ofmaterial.
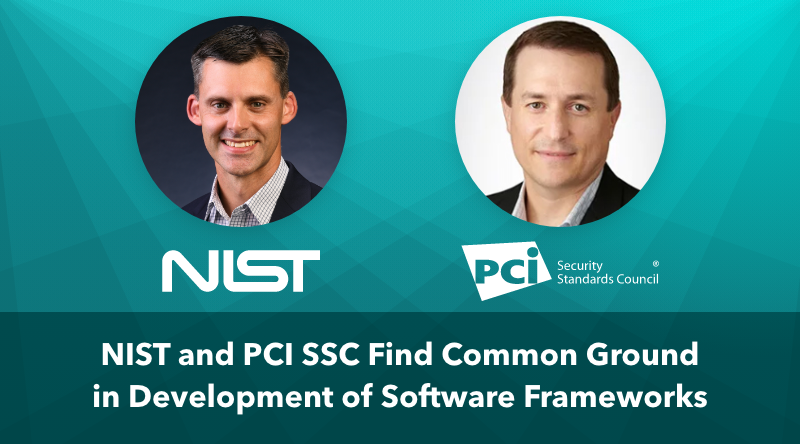
Its master-planning feature automates creating Production Orders from open Purchase Orders. It also comes with an optimization addon that allows users anticipate changes in customer demands. The AI capabilities of the program can help improve the flow in goods distribution. Microsoft has certified Dynamics Supply Chain Management as a solution for companies looking for a strong supply chain.
FAQ
What are the responsibilities of a production planner
A production planner makes sure all project elements are delivered on schedule, within budget, as well as within the agreed scope. They also ensure the quality of the product and service meets the client's requirements.
What are the responsibilities of a manufacturing manager
Manufacturing managers must ensure that manufacturing processes are efficient, effective, and cost-effective. They should also be aware and responsive to any company problems.
They should also be able communicate with other departments, such as sales or marketing.
They should also be knowledgeable about the latest trends in the industry so they can use this information for productivity and efficiency improvements.
What are the 7 Rs of logistics management?
The acronym 7R's of Logistic is an acronym that stands for seven fundamental principles of logistics management. It was developed and published by the International Association of Business Logisticians in 2004 as part of the "Seven Principles of Logistics Management".
The acronym is made up of the following letters:
-
Responsible - to ensure that all actions are within the legal requirements and are not detrimental to others.
-
Reliable - You can have confidence that you will fulfill your promises.
-
Use resources effectively and sparingly.
-
Realistic - Take into consideration all aspects of operations including cost-effectiveness, environmental impact, and other factors.
-
Respectful – Treat others fairly and equitably.
-
You are resourceful and look for ways to save money while increasing productivity.
-
Recognizable - Provide value-added services to customers
Can we automate some parts of manufacturing?
Yes! Yes. Automation has been around since ancient time. The wheel was invented by the Egyptians thousands of years ago. To help us build assembly lines, we now have robots.
There are many uses of robotics today in manufacturing. These include:
-
Automated assembly line robots
-
Robot welding
-
Robot painting
-
Robotics inspection
-
Robots that make products
Automation can be applied to manufacturing in many other ways. For instance, 3D printing allows us make custom products and not have to wait for months or even weeks to get them made.
Is it necessary to be familiar with Manufacturing Processes before we learn about Logistics.
No. No. But, being familiar with manufacturing processes will give you a better understanding about how logistics works.
Statistics
- It's estimated that 10.8% of the U.S. GDP in 2020 was contributed to manufacturing. (investopedia.com)
- Many factories witnessed a 30% increase in output due to the shift to electric motors. (en.wikipedia.org)
- [54][55] These are the top 50 countries by the total value of manufacturing output in US dollars for its noted year according to World Bank.[56] (en.wikipedia.org)
- According to a Statista study, U.S. businesses spent $1.63 trillion on logistics in 2019, moving goods from origin to end user through various supply chain network segments. (netsuite.com)
- In the United States, for example, manufacturing makes up 15% of the economic output. (twi-global.com)
External Links
How To
Six Sigma: How to Use it in Manufacturing
Six Sigma refers to "the application and control of statistical processes (SPC) techniques in order to achieve continuous improvement." Motorola's Quality Improvement Department created Six Sigma at their Tokyo plant, Japan in 1986. Six Sigma is a method to improve quality through standardization and elimination of defects. Since there are no perfect products, or services, this approach has been adopted by many companies over the years. The main goal of Six Sigma is to reduce variation from the mean value of production. This means that if you take a sample of your product, then measure its performance against the average, you can find out what percentage of the time the process deviates from the norm. If the deviation is excessive, it's likely that something needs to be fixed.
Understanding the nature of variability in your business is the first step to Six Sigma. Once you've understood that, you'll want to identify sources of variation. You'll also want to determine whether these variations are random or systematic. Random variations are caused by human errors. Systematic variations can be caused by outside factors. These are, for instance, random variations that occur when widgets are made and some fall off the production line. But if you notice that every widget you make falls apart at the exact same place each time, this would indicate that there is a problem.
Once you have identified the problem, you can design solutions. You might need to change the way you work or completely redesign the process. You should then test the changes again after they have been implemented. If they fail, you can go back to the drawing board to come up with a different plan.