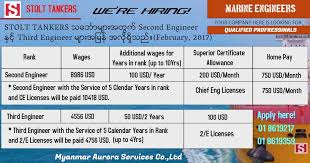
The director of manufacturing oversees the company's production process. They are responsible for overseeing all aspects of manufacturing, from design through to production. The ideal candidate should have extensive manufacturing experience and be proficient in new technologies in order to succeed in this position. Examples of such technologies are robotics and 3-D printing. These technologies are an asset for any director. As the manufacturing industry continues to evolve, the director's role will become increasingly complex, as he or she must work with the engineering and operations departments, as well as putting a greater emphasis on quality control within the manufacturing plant.
Salary for a Director of Manufacturing
The region in which a Director or Manufacturing is located can have a significant impact on their salary. Many directors get a salary in the low six figures, but some earn more than others. The years of experience and education can have an impact on the salary of a director of manufacturing. Here are some factors that could impact your salary.
The salary for a director of manufacturing varies but it's generally higher if you have more work experience. Salary can be affected depending on where you live and how much it costs to live. You will earn a higher salary if you live in a large city. However, your salary may not be sufficient to cover the cost of living. When the opportunity presents itself, it is important to be open to negotiations to obtain a higher wage.
The salary for a Director of Manufacturing Operations ranges from $181,500 to $66,000 per annum. The salary of a Director in Manufacturing Operations can vary greatly and may differ by as much as 8% depending on where you live. A director of manufacturing operations in Fremont, CA can earn between $128,493 and $164,500, which is considerably more than the national average. The salary of a Director in Manufacturing Operations can vary depending on where you live, how experienced you are, and what company you work for.
Education required
The director of manufacturing oversees the management and production of a facility. This position includes the hiring of new employees, quality assurance oversight, collaboration with designers, and ensuring that operations standards are met. A director of manufacturing usually reports to the top management team. He or she executes sales and policy initiatives. Candidates must have some manufacturing experience and be able communicate well. Different companies have different requirements for directors of manufacturing.
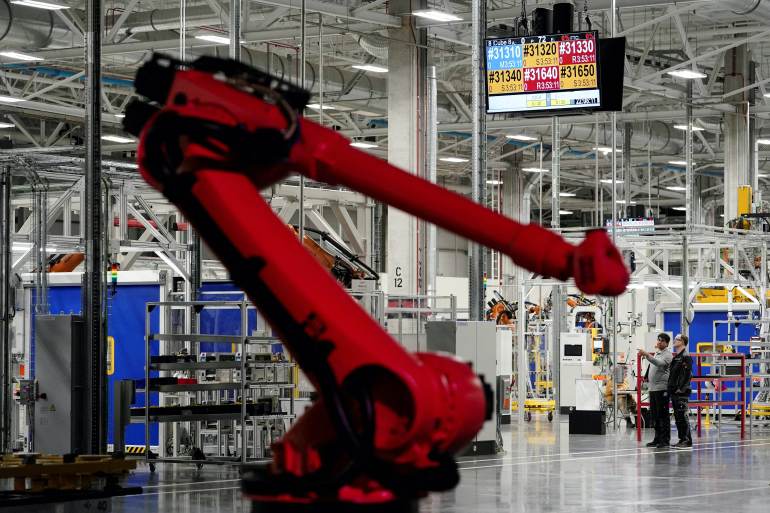
Although a master's degree in engineering does not necessarily make you a director in manufacturing, having a post-secondary education is a great way to increase your knowledge and skill set. A MBA in industrial management or business administration would be a great option for this job. It teaches candidates about economics, management, and organizational behavior. In the end, you will manage a diverse team of people.
As a director of manufacturing, you will work closely with designers and engineers during the product development phase. You will play a key role in this stage by evaluating new processes and making sure quality standards are met before you commit resources to larger productions. Successful directors are also responsible for overseeing the production process and acting as coaches for their employees. They will coach them in best practices and risk mitigation. Manufacturing directors are responsible for overseeing all aspects of production and must also have problem-solving skills.
Experience required
This position often requires a bachelor's degree in a relevant area and five to ten years of progressive work experience. In general, manufacturing companies prefer to hire employees for this job. The ideal candidate will have a thorough understanding of the manufacturing process and business objectives. Employers may require a graduate degree. Candidates may also need additional training in the chosen industry or field.

The manufacturing process is managed by the director of production, who oversees engineers, supervisors and workers. They may be responsible in solving problems and creating solutions. They could also be responsible, in addition to supervising production, for creating and implementing quality-control programmes. The manufacturing director reports directly to the chief executive of the organization. Manufacturing experience is a must. If you are looking to succeed in the manufacturing management position, it is important that you have some experience.
Manufacturing experience is essential. Directors should have at least 10 years' experience in a manufacturing setting. Some of these people may have started as manufacturing supervisors or technicians. Strong communication skills are also required. Also, a director of manufacturing needs to have a good understanding of business strategy. A director of manufacturing must also be able and willing to collaborate with other departments. The director of manufacturing oversees production and ensures it meets high quality standards.
FAQ
What is the difference between a production planner and a project manager?
The main difference between a production planner and a project manager is that a project manager is usually the person who plans and organizes the entire project, whereas a production planner is mainly involved in the planning stage of the project.
What is it like to manage a logistics company?
You need to have a lot of knowledge and skills to manage a successful logistic business. Good communication skills are essential to effectively communicate with your suppliers and clients. You will need to know how to interpret data and draw conclusions. You will need to be able handle pressure well and work in stressful situations. You need to be innovative and creative to come up with new ways to increase efficiency. Strong leadership qualities are essential to motivate your team and help them achieve their organizational goals.
It is also important to be efficient and well organized in order meet deadlines.
How can manufacturing efficiency be improved?
First, identify the factors that affect production time. We then need to figure out how to improve these variables. If you aren't sure where to begin, think about the factors that have the greatest impact on production time. Once you've identified them, try to find solutions for each of those factors.
What are the 7 Rs of logistics?
The acronym "7R's" of Logistics stands for seven principles that underpin logistics management. It was created by the International Association of Business Logisticians and published in 2004 under its "Seven Principles of Logistics Management".
The acronym is composed of the following letters.
-
Responsible - ensure that all actions taken are within legal requirements and are not harmful to others.
-
Reliable - have confidence in the ability to deliver on commitments made.
-
Be responsible - Use resources efficiently and avoid wasting them.
-
Realistic - Consider all aspects of operations, including environmental impact and cost effectiveness.
-
Respectful - treat people fairly and equitably.
-
Responsive - Look for ways to save time and increase productivity.
-
Recognizable provides value-added products and services to customers
How can I find out more about manufacturing?
Practical experience is the best way of learning about manufacturing. You can read books, or watch instructional videos if you don't have the opportunity to do so.
How can manufacturing excess production be decreased?
It is essential to find better ways to manage inventory to reduce overproduction. This would decrease the time that is spent on inefficient activities like purchasing, storing, or maintaining excess stock. This would allow us to use our resources for more productive tasks.
A Kanban system is one way to achieve this. A Kanban board is a visual display used to track work in progress. In a Kanban system, work items move through a sequence of states until they reach their final destination. Each state represents an individual priority level.
If work is moving from one stage to the other, then the current task can be completed and moved on to the next. However, if a task is still at the beginning stages, it will remain so until it reaches the end of the process.
This allows for work to continue moving forward, while also ensuring that there is no work left behind. With a Kanban board, managers can see exactly how much work is being done at any given moment. This data allows them adjust their workflow based upon real-time data.
Lean manufacturing is another way to manage inventory levels. Lean manufacturing emphasizes eliminating waste in all phases of production. Waste includes anything that does not add value to the product. The following are examples of common waste types:
-
Overproduction
-
Inventory
-
Unnecessary packaging
-
Material surplus
By implementing these ideas, manufacturers can improve efficiency and cut costs.
Statistics
- According to a Statista study, U.S. businesses spent $1.63 trillion on logistics in 2019, moving goods from origin to end user through various supply chain network segments. (netsuite.com)
- [54][55] These are the top 50 countries by the total value of manufacturing output in US dollars for its noted year according to World Bank.[56] (en.wikipedia.org)
- According to the United Nations Industrial Development Organization (UNIDO), China is the top manufacturer worldwide by 2019 output, producing 28.7% of the total global manufacturing output, followed by the United States, Japan, Germany, and India.[52][53] (en.wikipedia.org)
- In 2021, an estimated 12.1 million Americans work in the manufacturing sector.6 (investopedia.com)
- (2:04) MTO is a production technique wherein products are customized according to customer specifications, and production only starts after an order is received. (oracle.com)
External Links
How To
Six Sigma and Manufacturing
Six Sigma refers to "the application and control of statistical processes (SPC) techniques in order to achieve continuous improvement." It was developed by Motorola's Quality Improvement Department at their plant in Tokyo, Japan, in 1986. Six Sigma's main goal is to improve process quality by standardizing processes and eliminating defects. Since there are no perfect products, or services, this approach has been adopted by many companies over the years. The main goal of Six Sigma is to reduce variation from the mean value of production. You can calculate the percentage of deviation from the norm by taking a sample of your product and comparing it to the average. If this deviation is too big, you know something needs fixing.
The first step toward implementing Six Sigma is understanding how variability works in your business. Once you have this understanding, you will need to identify sources and causes of variation. This will allow you to decide if these variations are random and systematic. Random variations are caused when people make mistakes. While systematic variations are caused outside of the process, they can occur. If you make widgets and some of them end up on the assembly line, then those are considered random variations. It would be considered a systematic problem if every widget that you build falls apart at the same location each time.
Once you identify the problem areas, it is time to create solutions. You might need to change the way you work or completely redesign the process. After implementing the new changes, you should test them again to see if they worked. If they don't work you need to rework them and come up a better plan.