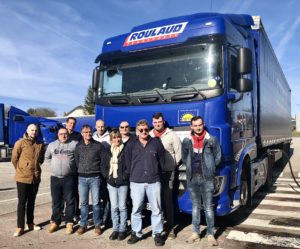
The duties and responsibilities of job directors in job manufacturing are similar to those of manufacturing associates. This article will provide information on the qualifications necessary to be a job administrator in manufacturing. This position requires a skilled workforce to execute various operations. It is crucial to have an unpredictable workflow in order to be able manage projects and track the development. This type of production line requires a highly skilled workforce, as it requires employees who are able to keep up with the pace and deliver quality products on time.
The job of a job director in manufacturing
A job director of manufacturing oversees the daily operations and management of a manufacturing unit. They ensure products are delivered on time and meet high standards. The director of manufacturing must be able to work with engineers and designers in order to develop new products. Before a product is put into mass production, they must evaluate its feasibility, market fit, impact on quality and processes, as well as the potential for disruption. They must have leadership abilities as a director for manufacturing. They should be able supervise workers and implement process and equipment improvements.
Directors of manufacturing typically have a bachelor's degree. Employers will hire more experienced candidates. In addition, directors of manufacturing should have at least five years of experience in management positions. Candidates should be able to adapt to a high learning curve.
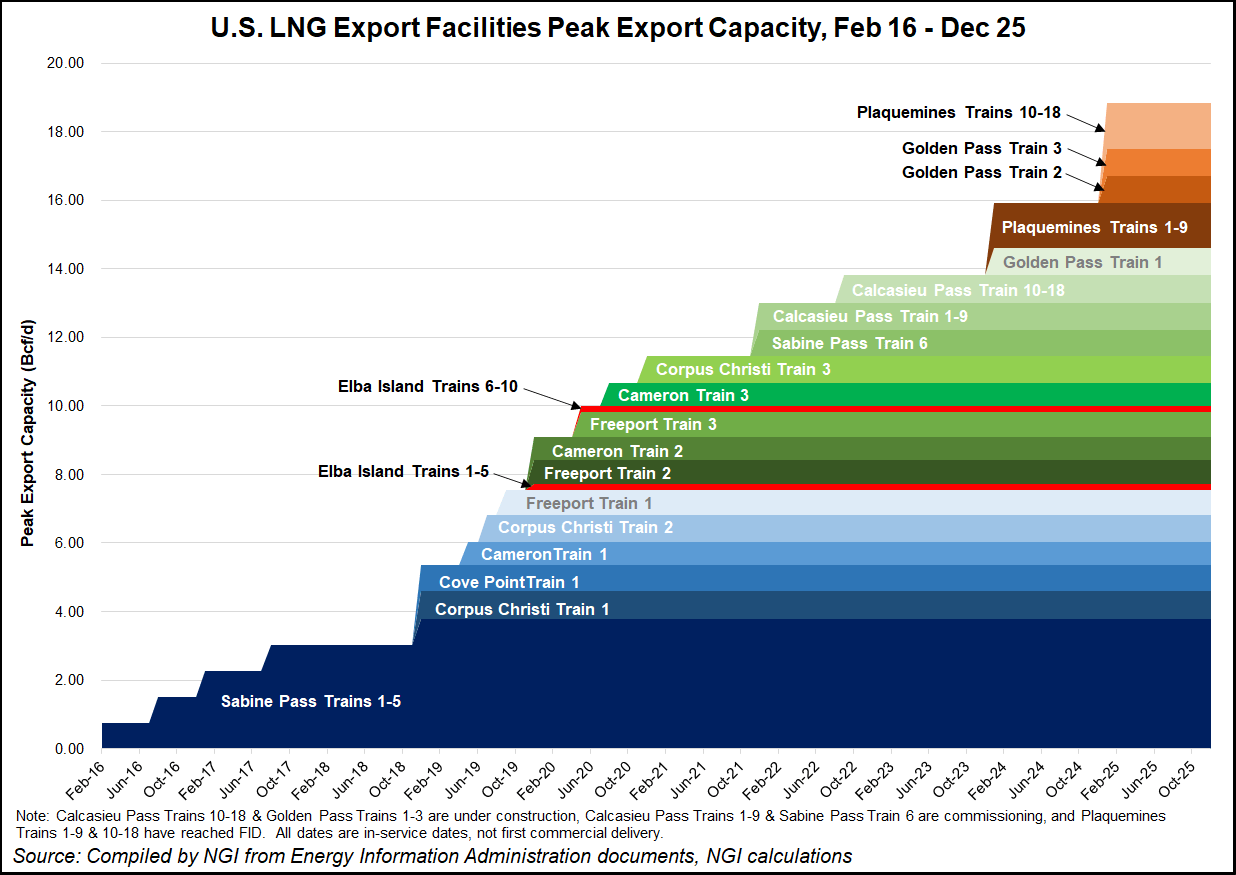
Assistant in manufacturing
Manufacturing associates can have many duties, but they are often required to perform repetitive tasks and assembly line work. To avoid injury, associates need to be strong in their body mechanics. They may have to lift heavy items or stand for long periods.
The duties of a manufacturing associate include inspection, engineering drawings, and execution of manufacturing documents. They also have to coordinate with other members of the team and produce reports. You will need to be organized, detail-oriented and good communicators.
Another major responsibility is to maintain quality control of manufactured items. They must have a good understanding of the manufacturing process and must be able check whether products comply with company standards. They must also inspect finished products to identify defects and ensure that they are in compliance with company standards.
Qualifications for a job in the manufacturing industry director position
Director of manufacturing is a job that requires you to manage all aspects of manufacturing operations, including scheduling and product production. You'll need to be able to maintain high quality standards as well as implement and evaluate cost-saving strategies and new ideas. Your responsibilities include evaluating all staff members' performance. You will need to have leadership skills and problem-solving abilities, as well as knowledge about manufacturing processes, in order to be a director of production.
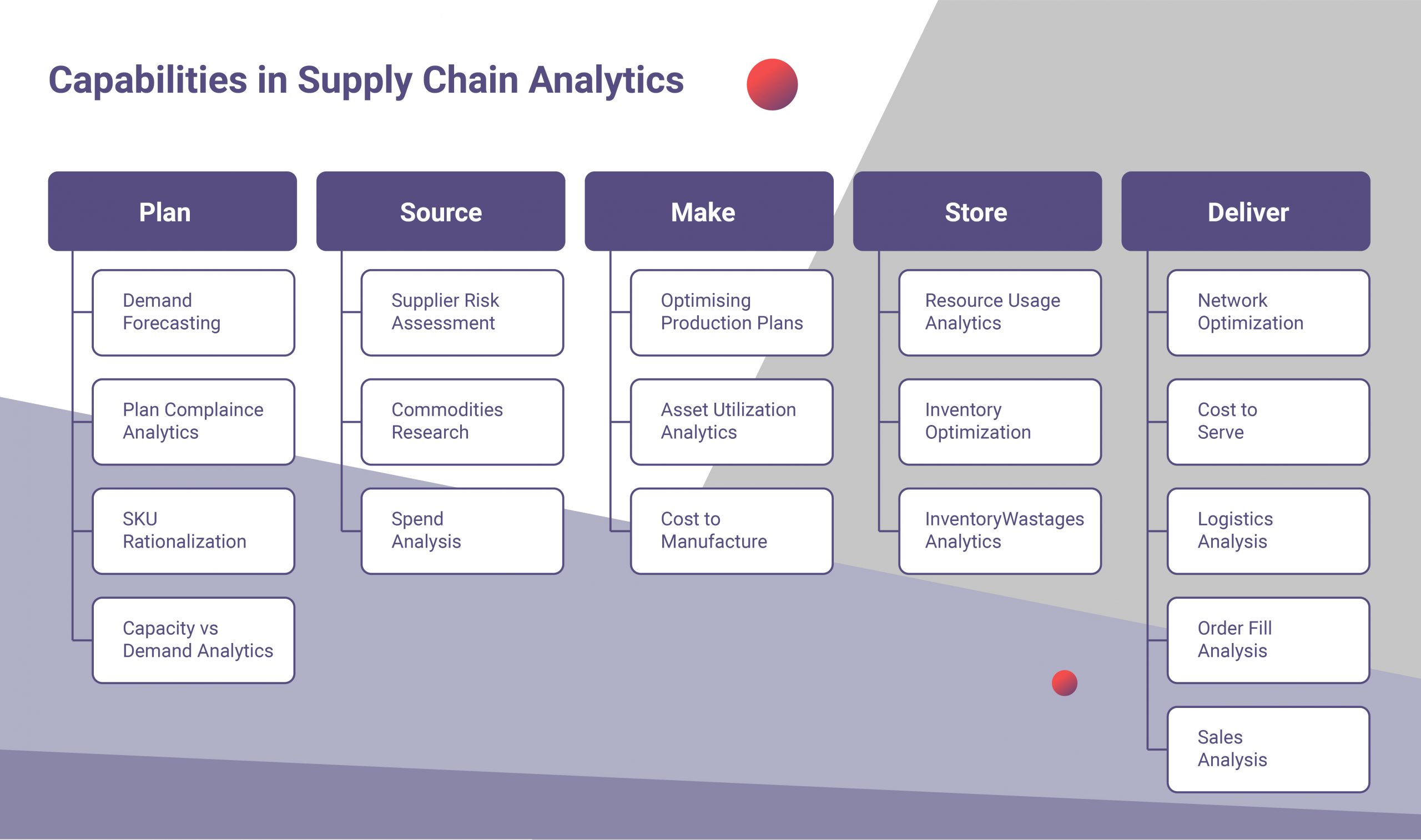
As a manufacturing director, you will work with engineers and designers to develop products and services for a company. To ensure everyone understands their roles and is on the same page, you will need excellent communication skills. Effectively managing the company will only be possible if you are able communicate effectively. As a director for manufacturing, you will need to mentor and coach employees. You will be required to train employees in safety procedures, risk mitigation and the use of new equipment.
FAQ
Is automation important for manufacturing?
Not only are service providers and manufacturers important, but so is automation. It allows them to offer services faster and more efficiently. They can also reduce their costs by reducing human error and improving productivity.
What are the 7 Rs of logistics.
The acronym 7R's for Logistics stands to represent the seven basic principles in logistics management. It was created by the International Association of Business Logisticians and published in 2004 under its "Seven Principles of Logistics Management".
The following letters form the acronym:
-
Responsible - ensure that actions are in compliance with legal requirements and do not cause harm to others.
-
Reliable: Have faith in your ability or the ability to honor any promises made.
-
It is reasonable to use resources efficiently and not waste them.
-
Realistic – Consider all aspects, including cost-effectiveness as well as environmental impact.
-
Respectful - Treat people fairly and equitably
-
Reliable - Find ways to save money and increase your productivity.
-
Recognizable is a company that provides customers with value-added solutions.
Is there anything we should know about Manufacturing Processes prior to learning about Logistics.
No. No. But, being familiar with manufacturing processes will give you a better understanding about how logistics works.
Statistics
- In the United States, for example, manufacturing makes up 15% of the economic output. (twi-global.com)
- According to a Statista study, U.S. businesses spent $1.63 trillion on logistics in 2019, moving goods from origin to end user through various supply chain network segments. (netsuite.com)
- It's estimated that 10.8% of the U.S. GDP in 2020 was contributed to manufacturing. (investopedia.com)
- You can multiply the result by 100 to get the total percent of monthly overhead. (investopedia.com)
- According to the United Nations Industrial Development Organization (UNIDO), China is the top manufacturer worldwide by 2019 output, producing 28.7% of the total global manufacturing output, followed by the United States, Japan, Germany, and India.[52][53] (en.wikipedia.org)
External Links
How To
How to use 5S to increase Productivity in Manufacturing
5S stands for "Sort", "Set In Order", "Standardize", "Separate" and "Store". The 5S methodology was developed at Toyota Motor Corporation in 1954. It helps companies achieve higher levels of efficiency by improving their work environment.
The basic idea behind this method is to standardize production processes, so they become repeatable, measurable, and predictable. This means that every day tasks such cleaning, sorting/storing, packing, and labeling can be performed. Through these actions, workers can perform their jobs more efficiently because they know what to expect from them.
Implementing 5S requires five steps. These are Sort, Set In Order, Standardize. Separate. And Store. Each step requires a different action, which increases efficiency. Sorting things makes it easier to find them later. You arrange items by placing them in an order. After you have divided your inventory into groups you can store them in easy-to-reach containers. Labeling your containers will ensure that everything is correctly labeled.
Employees need to reflect on how they do their jobs. Employees must be able to see why they do what they do and find a way to achieve them without having to rely on their old methods. To be successful in the 5S system, employees will need to acquire new skills and techniques.
In addition to improving efficiency, the 5S system also increases morale and teamwork among employees. They feel more motivated to work towards achieving greater efficiency as they see the results.