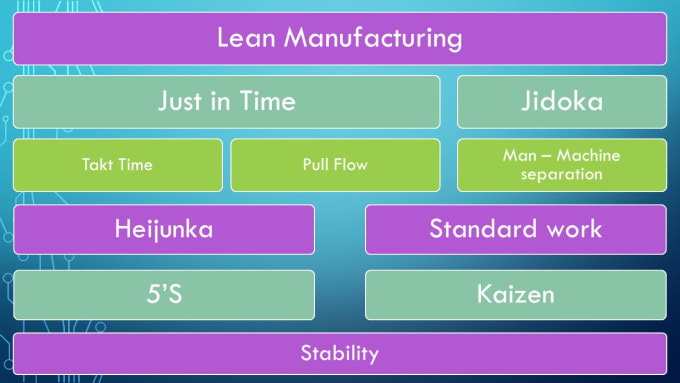
Lean is a term used in manufacturing to describe a series of principles and techniques. It is also a motivating word that encourages improvements in the process.
Definition of lean
If an organization wants to improve its efficiency, it might have to eliminate certain activities. They may not add any value to the products or services it offers. This includes idle time, equipment that is not used, and other resources which are not being utilized fully.
This is lean management's main goal, which is to remove waste in the production process. This is because the process will never stop, it's always changing and improving.
Lean philosophy is based on a belief that businesses should prioritize what their customers need and want rather than what it thinks they do. The companies will save money and time by not creating products which are not desired by their clients.
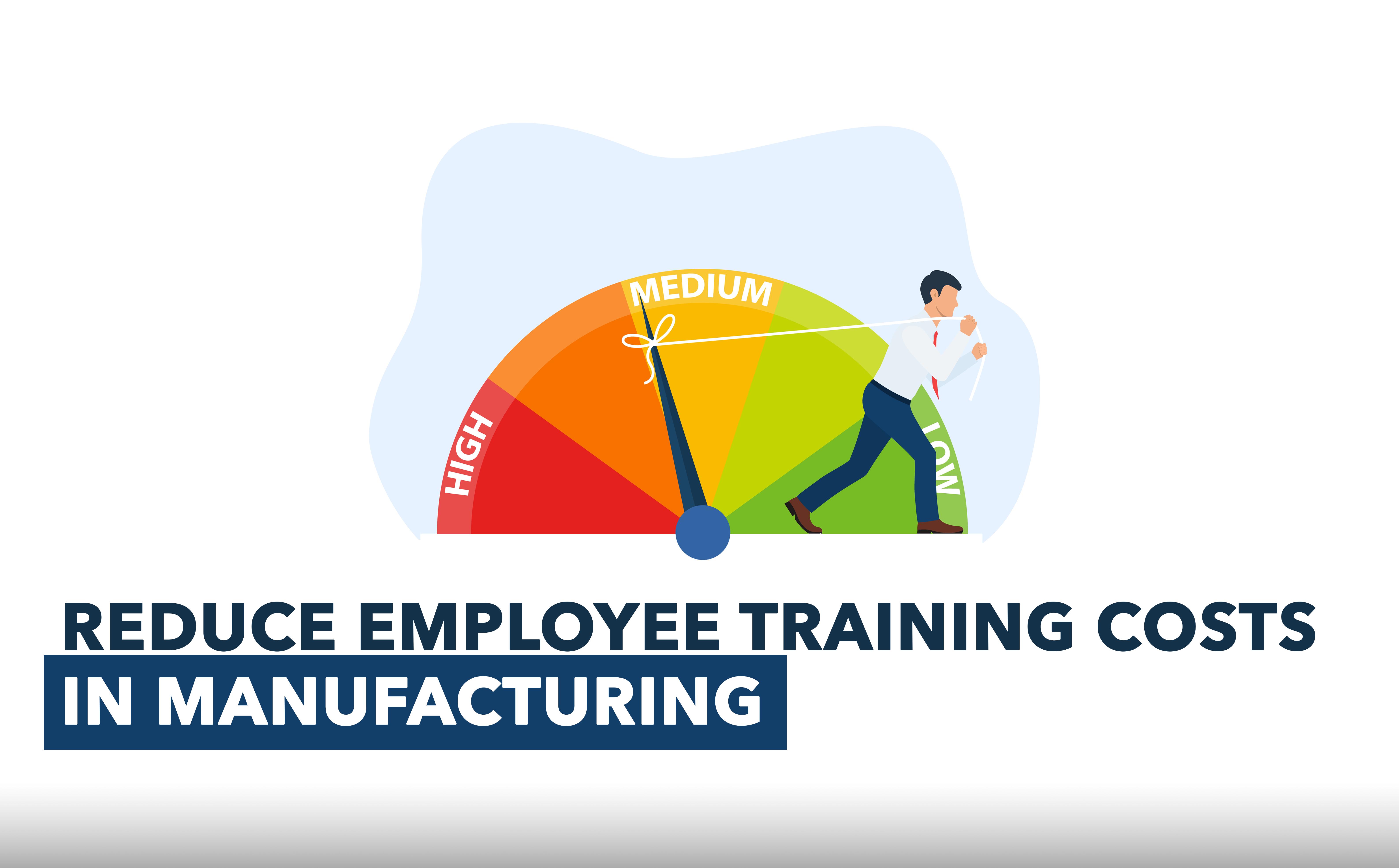
You should be aware that the lean concept can be adapted to any type of industry or production process. It is for this reason that it has been so widely adopted by many industries.
Lean manufacturing has been around for many years. It is a system which focuses delivering the best products in the most efficient way. It is also a great tool for creating efficiencies in the manufacturing process.
Toyoda defined lean as a concept that aims to eliminate waste from the production process. It includes defects and other waste that would be unacceptable to the customer.
Toyoda solved this issue with a flow system, in which workers stopped the production line for inspection and removed a component if needed. The flow process allowed Toyoda to fine-tune every step of production, eliminating defects as they occurred and increasing productivity.
Jidoka stops production automatically when there's an abnormality. This is known as kaizen, and is a key part of the lean manufacturing process.
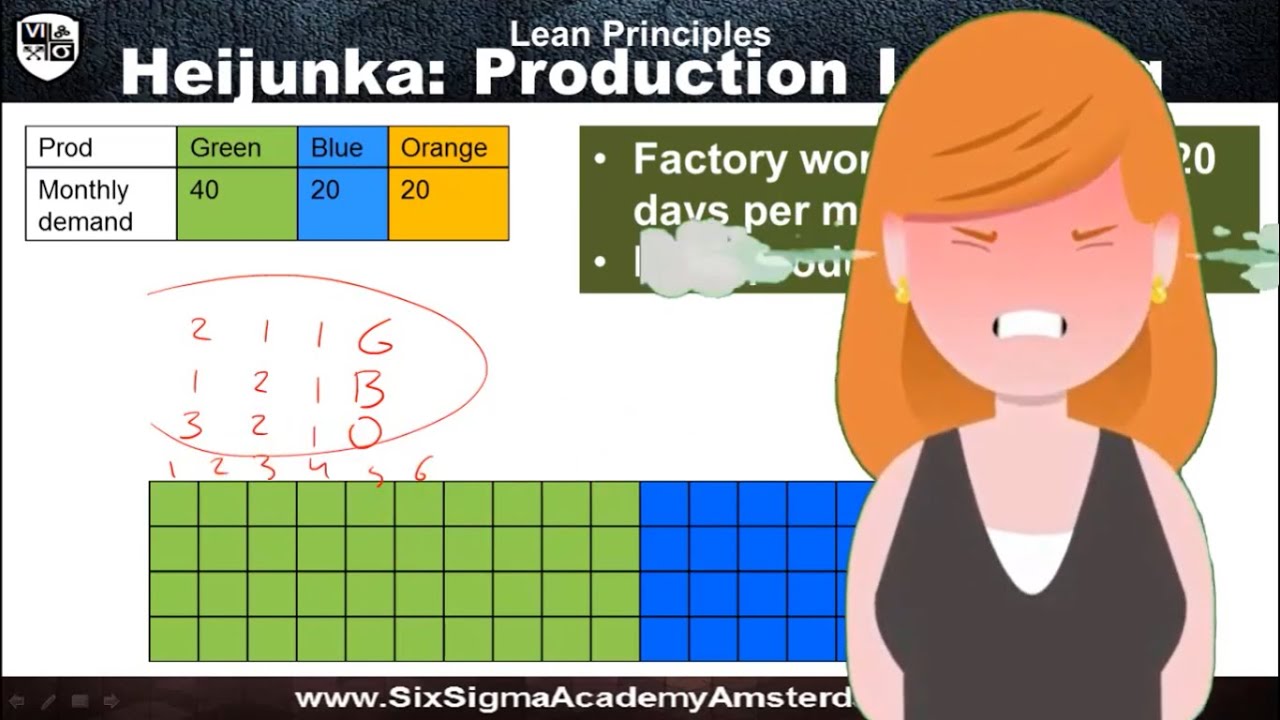
Kaizen is the process of continuous improvement in any process. This can be applied to the production of products or any other area in the business that needs an update.
A lot of people don't really understand what lean means, but it is a great concept that helps improve the way businesses run. Lean can save companies money and time, while also helping them to build a stronger reputation with their customers.
It is important to remember that lean is not an isolated practice; it's a process that will need to be improved by all levels of a company in order to be successful. This is why it is crucial to involve all employees in the process, so that everyone can contribute their ideas and ensure that everything goes smoothly.
FAQ
What is the difference between a production planner and a project manager?
The major difference between a Production Planner and a Project Manager is that a Project Manager is often the person responsible for organizing and planning the entire project. While a Production Planner is involved mainly in the planning stage,
What are the 7 Rs of logistics.
The acronym "7R's" of Logistics stands for seven principles that underpin logistics management. It was created by the International Association of Business Logisticians and published in 2004 under its "Seven Principles of Logistics Management".
The acronym is made up of the following letters:
-
Responsible - ensure that actions are in compliance with legal requirements and do not cause harm to others.
-
Reliable: Have faith in your ability or the ability to honor any promises made.
-
It is reasonable to use resources efficiently and not waste them.
-
Realistic – consider all aspects of operations, from cost-effectiveness to environmental impact.
-
Respectful - treat people fairly and equitably.
-
You are resourceful and look for ways to save money while increasing productivity.
-
Recognizable is a company that provides customers with value-added solutions.
Is it necessary to be familiar with Manufacturing Processes before we learn about Logistics.
No. You don't have to know about manufacturing processes before learning about logistics. Knowing about manufacturing processes will help you understand how logistics works.
What can I do to learn more about manufacturing?
Practical experience is the best way of learning about manufacturing. You can also read educational videos or take classes if this isn't possible.
What skills does a production planner need?
Production planners must be flexible, organized, and able handle multiple tasks. Also, you must be able and willing to communicate with clients and coworkers.
What are the responsibilities of a production planner
Production planners ensure all aspects of the project are delivered within time and budget. A production planner ensures that the service and product meet the client's expectations.
What's the difference between Production Planning & Scheduling?
Production Planning (PP), or production planning, is the process by which you determine what products are needed at any given time. Forecasting and identifying production capacity are two key elements to this process.
Scheduling is the process that assigns dates to tasks so they can get completed within a given timeframe.
Statistics
- In the United States, for example, manufacturing makes up 15% of the economic output. (twi-global.com)
- In 2021, an estimated 12.1 million Americans work in the manufacturing sector.6 (investopedia.com)
- It's estimated that 10.8% of the U.S. GDP in 2020 was contributed to manufacturing. (investopedia.com)
- According to the United Nations Industrial Development Organization (UNIDO), China is the top manufacturer worldwide by 2019 output, producing 28.7% of the total global manufacturing output, followed by the United States, Japan, Germany, and India.[52][53] (en.wikipedia.org)
- Many factories witnessed a 30% increase in output due to the shift to electric motors. (en.wikipedia.org)
External Links
How To
How to Use 5S for Increasing Productivity in Manufacturing
5S stands to stand for "Sort", “Set In Order", “Standardize", and "Store". Toyota Motor Corporation was the first to develop the 5S approach in 1954. It allows companies to improve their work environment, thereby achieving greater efficiency.
This approach aims to standardize production procedures, making them predictable, repeatable, and easily measurable. This means that every day tasks such cleaning, sorting/storing, packing, and labeling can be performed. Because workers know what they can expect, this helps them perform their jobs more efficiently.
There are five steps that you need to follow in order to implement 5S. Each step involves a different action which leads to increased efficiency. If you sort items, it makes them easier to find later. When items are ordered, they are put together. Then, after you separate your inventory into groups, you store those groups in containers that are easy to access. Finally, when you label your containers, you ensure everything is labeled correctly.
This requires employees to critically evaluate how they work. Employees need to be able understand their motivations and discover alternative ways to do them. They must learn new skills and techniques in order to implement the 5S system.
The 5S method increases efficiency and morale among employees. They feel more motivated to work towards achieving greater efficiency as they see the results.