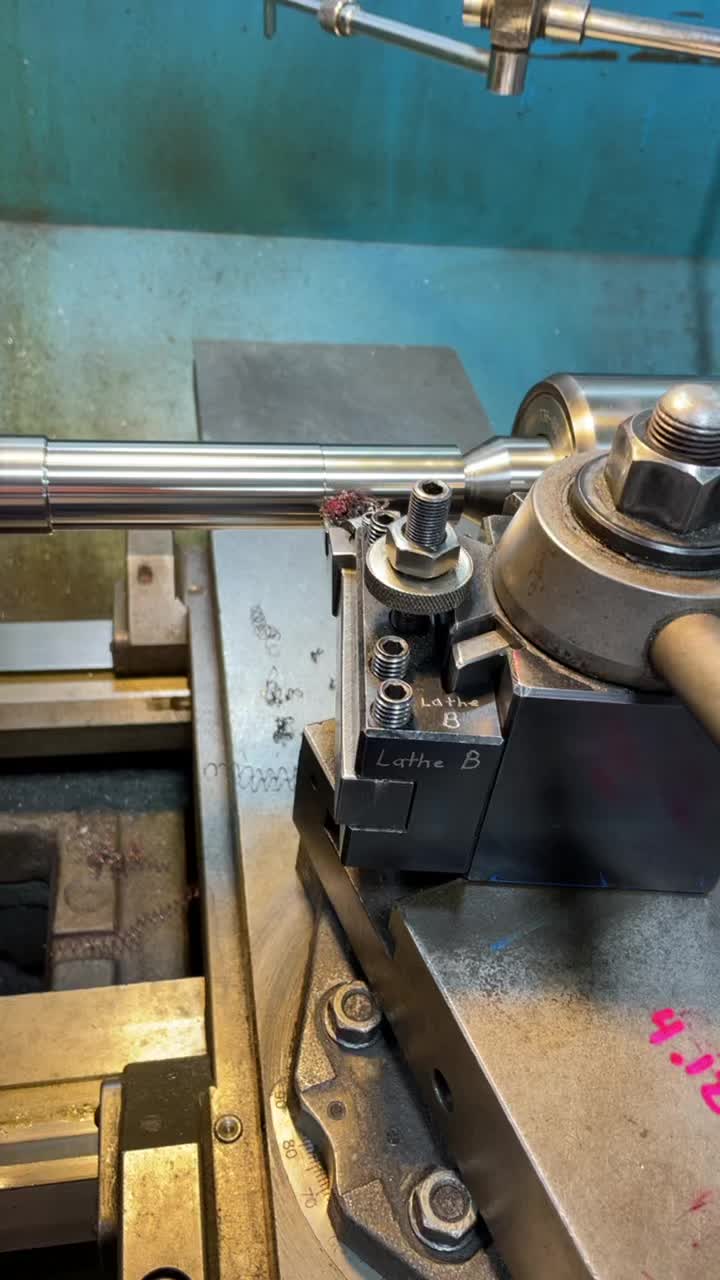
Are you interested in the average salary of environmental engineers? Here's a quick overview on the average annual salary for environmental engineers. You can also read the following to learn more about the job outlook, and what it takes to be a environmental engineer. We will be discussing the salary requirements and the future employment prospects for environmental engineers in this article. Average annual salaries for environmental engineers are $59,870. You need to realize that your potential earnings could be much higher. You'll need a bachelor’s degree in environmental engineering (or an equivalent) to get started.
Average annual salary
The average environmental engineer's annual salary is $96,820. This average is slightly lower than the average of all occupations. The number of openings is expected to grow by four percent over the next decade, and about 4,000 positions are anticipated each year, mostly due to workers transitioning to other occupations or retiring. To see if your degree or experience matches the job duties of an environmental engineer, check the salary ranges of similar occupations.
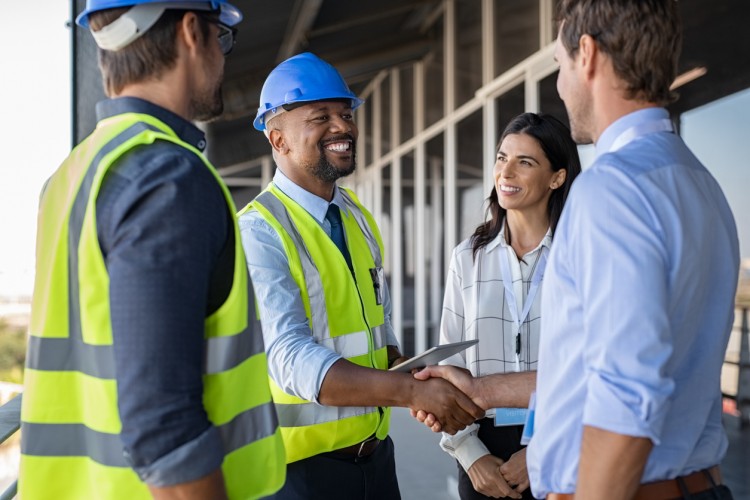
While there is no one set average annual salary for an environmental engineer, this field offers both financial and meaning work. The BLS reported that the average annual wage for environmental engineers working in the federal government was $101,640. However, the highest-paid 10 per cent earned more than $128,000. However, there are differences within the occupation. Some individuals earn more than $150,000 while others make less than $67,000.
Employment outlook for environmental engineers
According to the Bureau of Labor Statistics, the employment outlook for environmental engineers is positive. There will be an increase of 3.23% in the number of environmental engineer jobs from 2004 to 2024. It is slightly lower than what the national average is. The number of job openings is expected to increase by 1.63 percent annually in the next year. The growth in job opportunities is expected to be modest.
As the world becomes more conscious about the effects of human beings on the environment, the demand for environmental engineers will increase. This is due to increasing awareness about environmental damage and the need find ways to mitigate it. This makes the job market for environmental engineering very attractive. According to the U.S. Bureau of Labor Statistics there is a 12 percent growth in demand for environmental engineers between 2014 and 2024. Therefore, it is a good time to pursue a degree in environmental engineering.
How to become an Environmental Engineer
After completing a bachelor’s degree in engineering, engineers who are environmental engineers are eligible for the Foundational Examination. The test is designed to assess their basic knowledge of the environment. These engineers are also called "engineer interns" or "engineer in training" until they can take the Principles and Practice of Engineering (PPE) exam. While many states require the continued education of environmental engineers, most will recognize prior licensure. AACE offers board certification to environmental engineers, which is a mark of competence that shows the extent of their knowledge in a particular field of environmental engineering.
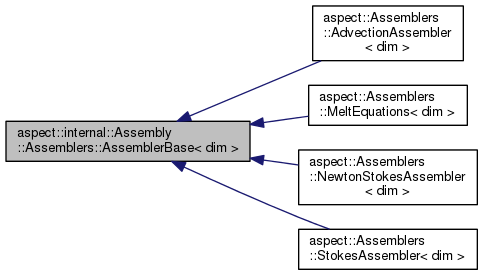
Additional skills are needed, besides a bachelor’s degree. Environment engineers need to be imaginative and able think about how their designs or solutions will impact larger systems. They need to be able speak clearly with people and work alone. They must be able interact with a variety of professionals, including scientists or engineers with other specialties. They must also have the ability to write clearly.
FAQ
What is the job of a manufacturer manager?
The manufacturing manager should ensure that every manufacturing process is efficient and effective. They must also be alert to any potential problems and take appropriate action.
They should also be able communicate with other departments, such as sales or marketing.
They must also keep up-to-date with the latest trends in their field and be able use this information to improve productivity and efficiency.
How can I learn about manufacturing?
Experience is the best way for you to learn about manufacturing. But if that is not possible you can always read books and watch educational videos.
Are there ways to automate parts of manufacturing?
Yes! Yes. Automation has been around since ancient time. The wheel was invented by the Egyptians thousands of years ago. Robots are now used to assist us in assembly lines.
There are many applications for robotics in manufacturing today. These include:
-
Line robots
-
Robot welding
-
Robot painting
-
Robotics inspection
-
Robots that create products
Automation could also be used to improve manufacturing. 3D printing, for example, allows us to create custom products without waiting for them to be made.
What are the logistics products?
Logistics refers to the movement of goods from one place to another.
They encompass all aspects transport, including packaging and loading, transporting, storage, unloading.
Logisticians ensure that the product is delivered to the correct place, at the right time, and under safe conditions. They provide information on demand forecasts as well stock levels, production schedules and availability of raw material.
They keep track and monitor the transit of shipments, maintain quality standards, order replenishment and inventories, coordinate with suppliers, vendors, and provide support for sales and marketing.
What is the difference between Production Planning, Scheduling and Production Planning?
Production Planning (PP), is the process of deciding what production needs to take place at any given time. Forecasting and identifying production capacity are two key elements to this process.
Scheduling involves the assignment of dates and times to tasks in order to complete them within the timeframe.
How does a production planner differ from a project manager?
The primary difference between a producer planner and a manager of a project is that the manager usually plans and organizes the whole project, while a production planner is only involved in the planning stage.
Statistics
- In the United States, for example, manufacturing makes up 15% of the economic output. (twi-global.com)
- (2:04) MTO is a production technique wherein products are customized according to customer specifications, and production only starts after an order is received. (oracle.com)
- Job #1 is delivering the ordered product according to specifications: color, size, brand, and quantity. (netsuite.com)
- It's estimated that 10.8% of the U.S. GDP in 2020 was contributed to manufacturing. (investopedia.com)
- You can multiply the result by 100 to get the total percent of monthly overhead. (investopedia.com)
External Links
How To
How to Use lean manufacturing in the Production of Goods
Lean manufacturing (or lean manufacturing) is a style of management that aims to increase efficiency, reduce waste and improve performance through continuous improvement. It was developed in Japan between 1970 and 1980 by Taiichi Ohno. TPS founder Kanji Tyoda gave him the Toyota Production System, or TPS award. The first book published on lean manufacturing was titled "The Machine That Changed the World" written by Michael L. Watkins and published in 1990.
Lean manufacturing is often described as a set if principles that help improve the quality and speed of products and services. It emphasizes reducing defects and eliminating waste throughout the value chain. Just-in-time (JIT), zero defect (TPM), and 5S are all examples of lean manufacturing. Lean manufacturing seeks to eliminate non-value added activities, such as inspection, work, waiting, and rework.
Lean manufacturing is a way for companies to achieve their goals faster, improve product quality, and lower costs. Lean manufacturing has been deemed one of the best ways to manage the entire value-chain, including customers, distributors as well retailers and employees. Lean manufacturing is widely practiced in many industries around the world. Toyota's philosophy has been a key driver of success in many industries, including automobiles and electronics.
Five fundamental principles underlie lean manufacturing.
-
Define Value: Identify the social value of your business and what sets you apart.
-
Reduce waste - Get rid of any activity that does not add value to the supply chain.
-
Create Flow. Ensure that your work is uninterrupted and flows seamlessly.
-
Standardize & simplify - Make processes consistent and repeatable.
-
Build Relationships - Establish personal relationships with both internal and external stakeholders.
Lean manufacturing isn’t new, but it has seen a renewed interest since 2008 due to the global financial crisis. To increase their competitiveness, many businesses have turned to lean manufacturing. According to some economists, lean manufacturing could be a significant factor in the economic recovery.
Lean manufacturing, which has many benefits, is now a standard practice in the automotive industry. These include higher customer satisfaction levels, reduced inventory levels as well as lower operating costs.
It can be applied to any aspect of an organisation. It is especially useful for the production aspect of an organization, as it ensures that every step in the value chain is efficient and effective.
There are three types of lean manufacturing.
-
Just-in-Time Manufacturing: Also known as "pull systems", this type of lean manufacturing uses just-in-time manufacturing (JIT). JIT is a process in which components can be assembled at the point they are needed, instead of being made ahead of time. This approach reduces lead time, increases availability and reduces inventory.
-
Zero Defects Manufacturing - ZDM: ZDM focuses its efforts on making sure that no defective units leave a manufacturing facility. If a part is required to be repaired on the assembly line, it should not be scrapped. This applies to finished goods that may require minor repairs before shipment.
-
Continuous Improvement (CI),: Continuous improvement aims improve the efficiency and effectiveness of operations by continuously identifying issues and making changes to reduce waste. It involves continuous improvement of processes, people, and tools.