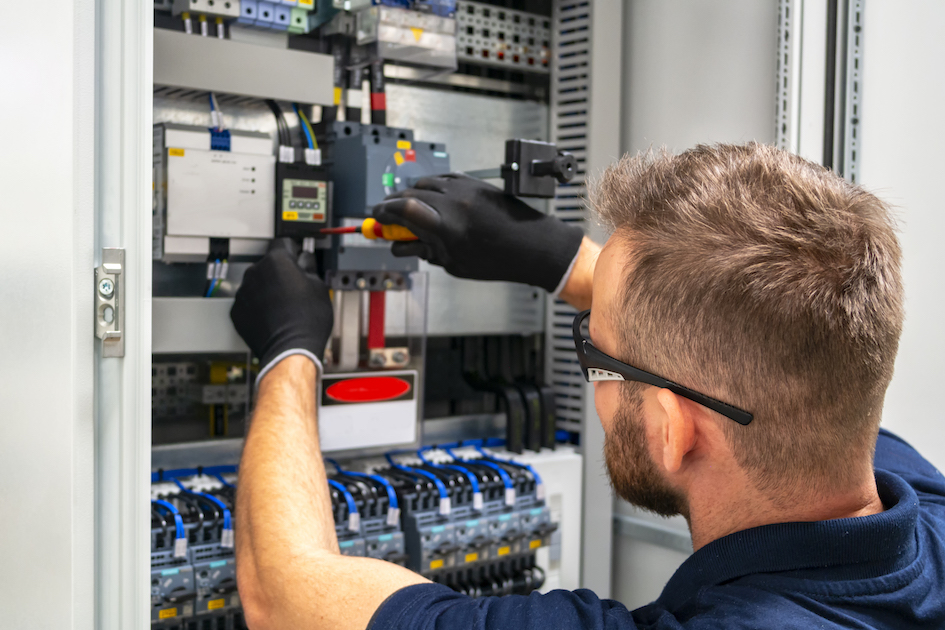
Supply chain management software is a great tool to streamline your business processes and increase efficiency, regardless of whether you run a large company or a small one. These software systems provide a central view of your entire supply chain. This allows you to plan production, shipping plans, and delivery routes. They help you automate and streamline processes, freeing up your employees' time to focus on other areas of the business. Supply chain management software is important to every organization that controls shipping and manufacturing.
You must consider many capabilities and features in order to find the best supply management software. These include ease of use, scalability and integration with other software. You should also consider the provider's reputation and the features they offer. Additionally, it is important to find a solution within your budget. You should also consider whether you want a SaaS package or a full-scale plan. This will allow you to adjust as your business grows.
E2open is a leading provider of supply chain management software. It specializes in cloud-based solutions that provide better demand forecasting, operations management, and other benefits. E2open also provides advanced features and a technology platform. Software is available for businesses in many industries including manufacturing, retail, and transportation.
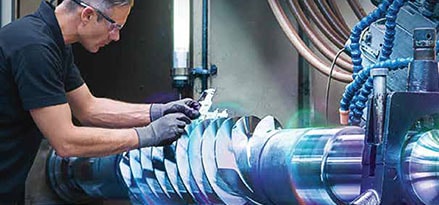
Supply chain management software has a key feature: real-time visibility. This software allows you to track and monitor your inventory as well as your shipments. This helps ensure your customers always have the right product at the right time. It helps you to develop long-term strategies that manage demand-supply balancing.
Kinaxis, a supply chain management software that streamlines and breaks down silos, is a complete solution. It integrates human and machine intelligence to make it easier for you to make better decisions. It can also be used to plan inventory and capacity in order to better respond for opportunities.
Sales forecasting software allows you to better understand historical sales, sales cycles, and seasonality. Machine learning is also used to predict sales. This software allows you to predict sales and also helps prepare your sales team. You also have access to data from multiple sources so you can see the whole picture of your business.
Descartes Systems Group, the biggest competitor to supply-chain management software, is their main competitor. They are the top vendor for many organizations. This company is home to over 13,000 active users. Its products are competitive with SAP SCM (SAP Megaventory), JDA, Logility, and JDA.
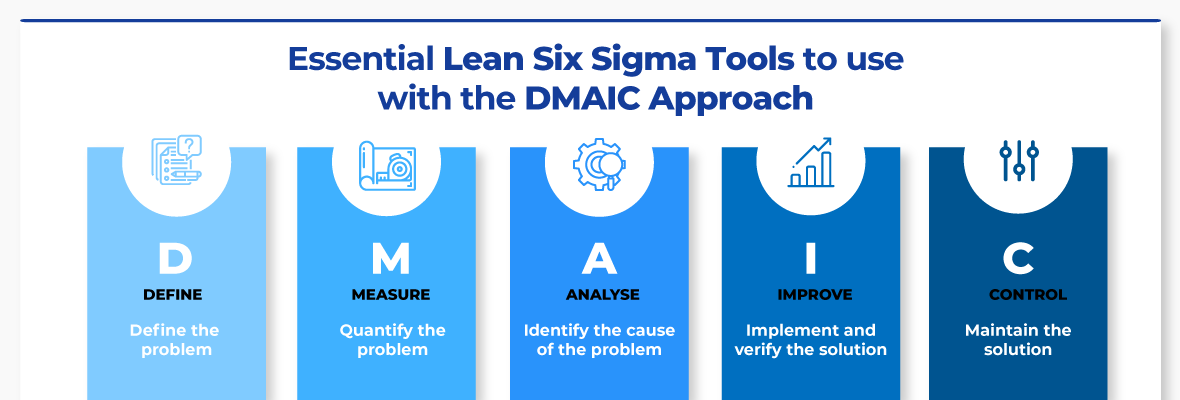
Manhattan Associates is another competitor to supply-chain management software. Manhattan Associates has approximately $617.5 million in revenue and thousands of customers. Eddie Capel currently runs it. This company competes in the market against Logility, JDA, and Infor SCM.
Infor SCM software is the best for supply chain management. It's a great solution for small and large businesses. It's a cloud-based application that unifies all enterprise processes. It also offers analytics at its core, which can be used to optimize your end-to–end supply chain.
FAQ
What does "warehouse" mean?
A warehouse is a place where goods are stored until they are sold. It can be an indoor space or an outdoor area. In some cases it could be both indoors and outdoors.
What does it take for a logistics enterprise to succeed?
A successful logistics business requires a lot more than just knowledge. You must have good communication skills to interact effectively with your clients and suppliers. It is important to be able to analyse data and draw conclusions. You need to be able work under pressure and manage stressful situations. You need to be innovative and creative to come up with new ways to increase efficiency. To motivate and guide your team towards reaching organizational goals, you must have strong leadership skills.
You must be organized to meet tight deadlines.
What is the difference between Production Planning and Scheduling?
Production Planning (PP) is the process of determining what needs to be produced at any given point in time. Forecasting and identifying production capacity are two key elements to this process.
Scheduling refers to the process of allocating specific dates to tasks in order that they can be completed within a specified timeframe.
Statistics
- Many factories witnessed a 30% increase in output due to the shift to electric motors. (en.wikipedia.org)
- In 2021, an estimated 12.1 million Americans work in the manufacturing sector.6 (investopedia.com)
- According to a Statista study, U.S. businesses spent $1.63 trillion on logistics in 2019, moving goods from origin to end user through various supply chain network segments. (netsuite.com)
- According to the United Nations Industrial Development Organization (UNIDO), China is the top manufacturer worldwide by 2019 output, producing 28.7% of the total global manufacturing output, followed by the United States, Japan, Germany, and India.[52][53] (en.wikipedia.org)
- It's estimated that 10.8% of the U.S. GDP in 2020 was contributed to manufacturing. (investopedia.com)
External Links
How To
How to use 5S to increase Productivity in Manufacturing
5S stands to stand for "Sort", “Set In Order", “Standardize", and "Store". Toyota Motor Corporation developed the 5S method in 1954. It allows companies to improve their work environment, thereby achieving greater efficiency.
The idea behind standardizing production processes is to make them repeatable and measurable. This means that daily tasks such as cleaning and sorting, storage, packing, labeling, and packaging are possible. These actions allow workers to perform their job more efficiently, knowing what to expect.
There are five steps to implementing 5S, including Sort, Set In Order, Standardize, Separate and Store. Each step has a different action and leads to higher efficiency. By sorting, for example, you make it easy to find the items later. When you arrange items, you place them together. Next, organize your inventory into categories and store them in containers that are easily accessible. Finally, when you label your containers, you ensure everything is labeled correctly.
Employees must be able to critically examine their work practices. Employees should understand why they do the tasks they do, and then decide if there are better ways to accomplish them. They will need to develop new skills and techniques in order for the 5S system to be implemented.
The 5S method not only increases efficiency but also boosts morale and teamwork. Once they start to notice improvements, they are motivated to keep working towards their goal of increasing efficiency.