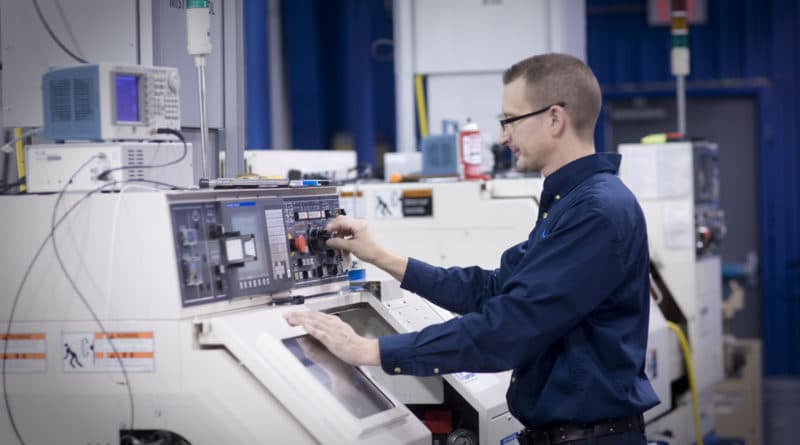
In classical economics, there are three basic sectors. These three main sectors include manufacturing, finance, and services. Business classifications are based on the characteristics and risks of each business. Below, you will learn more about each of the three sectors. Here is a quick overview of the different types of businesses within each sector. If you are interested, you can explore the information further. These categories do not have to be mutually exclusive.
Economic activity
Factors that are used to produce, inputs, or outputs affect the country's economic activity. The demand for particular goods or services is often the determinant of a region’s economic activity. There are two types economic activity: primary or secondary. Primary economic activities provide goods or services to satisfy daily human needs, while secondary economic activities add value to raw materials and combine them to make a more valuable product. Manufacturing and processing industries are examples of secondary economic activity.
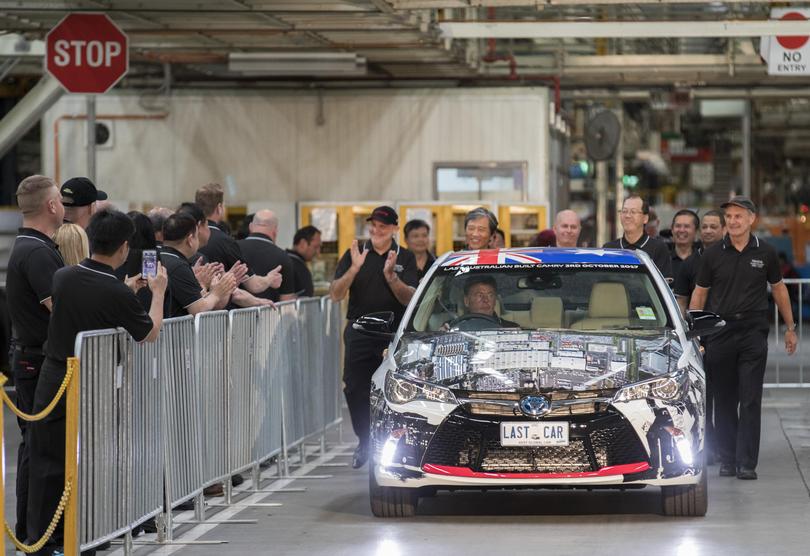
Classification of businesses
Business classification refers the process of dividing businesses in groups based their type of activities. There are two main categories: primary and secondary. Primary businesses are those which extract or exchange natural resources. The second type converts raw materials into ready-to-use products. There are many distinctions between these two types. Here are some major differences between both types. The information in this article will help you to decide which type is right for your business.
Characteristics
This discussion will explain the differences between primary, secondary and tertiary sector and focus on the economic impact of each. First, let's define sectors. Each sector is an economic entity that responds differently to different factors. These conditions could be repeated, such business cycles, or they might be one-off events, such improvements in technology. These characteristics are useful in identifying the most profitable sectors and determining their relative importance within an economy.
Risques
Industry risk is the variance in performance between different industries and their companies. It can be measured by assessing the variance in return on equity (ROE) and profitability. Depending on the industry, this may also reflect the performance of stock markets. An example of this is a steel company, which is considered to be at high risk because there are potential earthquakes in the region. An analysis of these risks can help investors identify volatile sectors.
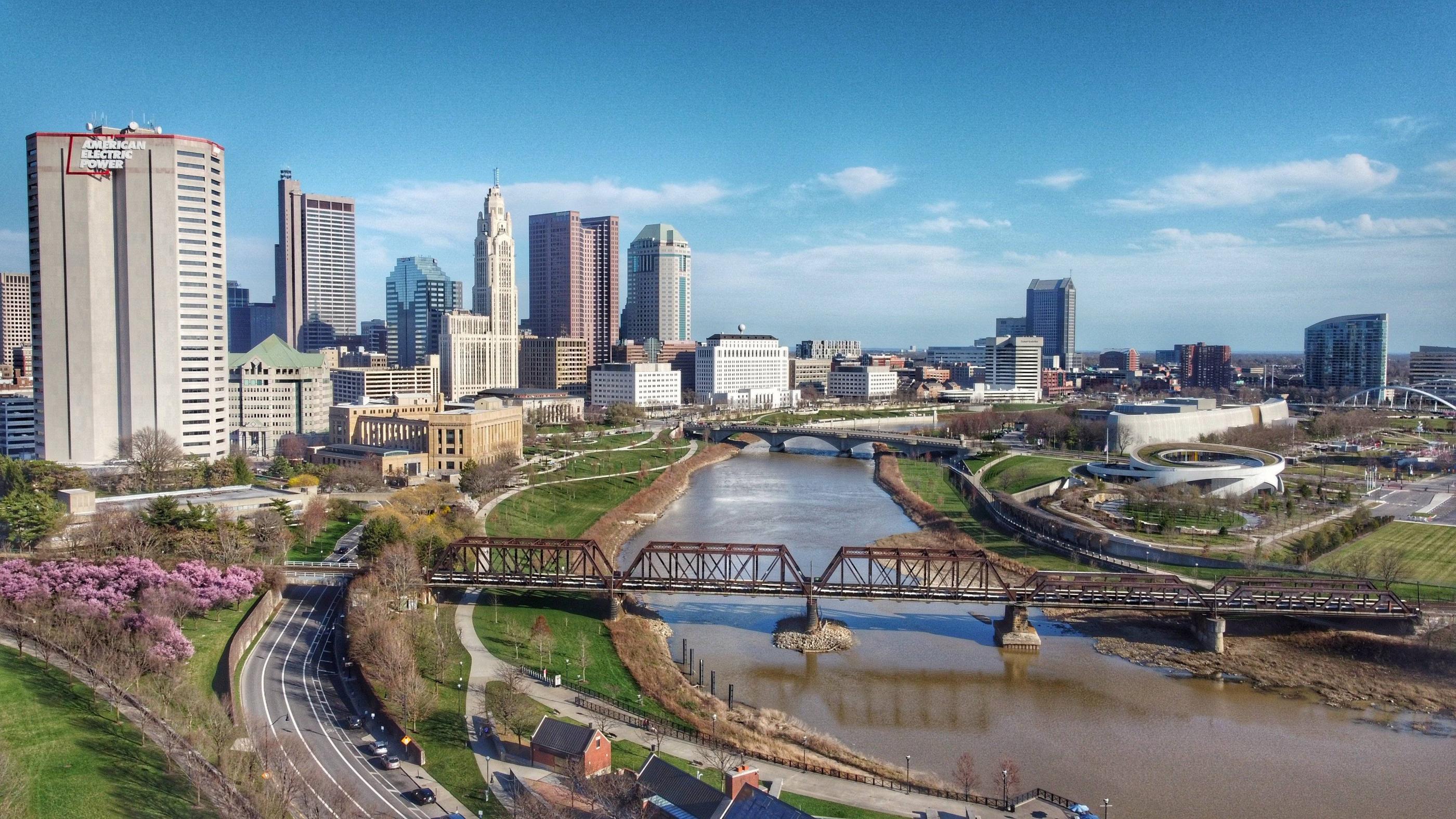
Investments
While many investors invest in specific companies, investing in sectors can be an excellent choice for the cautious investor. Sectors can be found both in mutual funds as well as exchange-traded funds. They are safer and have lower risks. Additionally, sector investing has become a very popular investment strategy. This article will explain how sector investing can help to find the right investments. Continue reading to find out more. Don't forget our free resource section to get more information.
FAQ
Why is logistics important in manufacturing?
Logistics is an integral part of every business. Logistics can help you achieve amazing results by helping to manage product flow from raw materials to finished products.
Logistics also play a major role in reducing costs and increasing efficiency.
What is production planning?
Production Planning involves developing a plan for all aspects of the production, including scheduling, budgeting, casting, crew, location, equipment, props, etc. This document ensures that everything is prepared and available when you are ready for shooting. It should also contain information on achieving the best results on set. This includes location information, crew details, equipment specifications, and casting lists.
The first step in filming is to define what you want. You may have decided where to shoot or even specific locations you want to use. Once you have identified your locations and scenes it's time to begin figuring out what elements you will need for each one. Perhaps you have decided that you need to buy a car but aren't sure which model. If this is the case, you might start searching online for car models and then narrow your options by selecting from different makes.
Once you have found the right car, you can start thinking about extras. Do you need people sitting in the front seats? Or maybe you just need someone to push the car around. Maybe you want to change the interior color from black to white? These questions will help you determine the exact look and feel of your car. It is also worth considering the types of shots that you wish to take. Do you want to film close-ups, or wider angles? Maybe you want the engine or the steering wheels to be shown. These details will help identify the exact car you wish to film.
Once you have all the information, you are ready to create a plan. The schedule will show you when to begin shooting and when to stop. The schedule will show you when to get there, what time to leave, and when to return home. It will help everyone know exactly what they have to do and when. Hire extra staff by booking them ahead of time. It is not worth hiring someone who won’t show up because you didn’t tell him.
You will need to factor in the days that you have to film when creating your schedule. Some projects may only take a couple of days, while others could last for weeks. When you are creating your schedule, you should always keep in mind whether you need more than one shot per day or not. Multiple shots at the same location can increase costs and make it more difficult to complete. If you aren't sure whether you need multiple shots, it is best to take fewer photos than you would like.
Budgeting is another crucial aspect of production plan. It is important to set a realistic budget so you can work within your budget. You can always lower the budget if you encounter unexpected problems. You shouldn't underestimate the amount you'll spend. If you underestimate the cost of something, you will have less money left after paying for other items.
Planning production is a tedious process. Once you have a good understanding of how everything works together, planning future projects becomes easy.
What does it mean to warehouse?
A warehouse or storage facility is where goods are stored before they are sold. It can be an indoor space or an outdoor area. Sometimes, it can be both an indoor and outdoor space.
What are the responsibilities of a manufacturing manager
The manufacturing manager should ensure that every manufacturing process is efficient and effective. They should be aware of any issues within the company and respond accordingly.
They should also know how to communicate with other departments such as sales and marketing.
They should be informed about industry trends and be able make use of this information to improve their productivity and efficiency.
What does it take to run a logistics business?
To run a successful logistics company, you need a lot knowledge and skills. To communicate effectively with clients and suppliers, you must be able to communicate well. You will need to know how to interpret data and draw conclusions. You must be able manage stress and pressure under pressure. To improve efficiency, you must be innovative and creative. Strong leadership qualities are essential to motivate your team and help them achieve their organizational goals.
You must be organized to meet tight deadlines.
Statistics
- You can multiply the result by 100 to get the total percent of monthly overhead. (investopedia.com)
- Many factories witnessed a 30% increase in output due to the shift to electric motors. (en.wikipedia.org)
- According to the United Nations Industrial Development Organization (UNIDO), China is the top manufacturer worldwide by 2019 output, producing 28.7% of the total global manufacturing output, followed by the United States, Japan, Germany, and India.[52][53] (en.wikipedia.org)
- [54][55] These are the top 50 countries by the total value of manufacturing output in US dollars for its noted year according to World Bank.[56] (en.wikipedia.org)
- Job #1 is delivering the ordered product according to specifications: color, size, brand, and quantity. (netsuite.com)
External Links
How To
How to Use lean manufacturing in the Production of Goods
Lean manufacturing (or lean manufacturing) is a style of management that aims to increase efficiency, reduce waste and improve performance through continuous improvement. It was first developed in Japan in the 1970s/80s by Taiichi Ahno, who was awarded the Toyota Production System (TPS), award from KanjiToyoda, the founder of TPS. The first book published on lean manufacturing was titled "The Machine That Changed the World" written by Michael L. Watkins and published in 1990.
Lean manufacturing refers to a set of principles that improve the quality, speed and costs of products and services. It emphasizes the elimination of defects and waste throughout the value stream. Just-in-time (JIT), zero defect (TPM), and 5S are all examples of lean manufacturing. Lean manufacturing focuses on eliminating non-value-added activities such as rework, inspection, and waiting.
Lean manufacturing is a way for companies to achieve their goals faster, improve product quality, and lower costs. Lean manufacturing can be used to manage all aspects of the value chain. Customers, suppliers, distributors, retailers and employees are all included. Lean manufacturing can be found in many industries. For example, Toyota's philosophy underpins its success in automobiles, electronics, appliances, healthcare, chemical engineering, aerospace, paper, food, etc.
Five principles are the basis of lean manufacturing:
-
Define Value - Determine the value that your business brings to society. Also, identify what sets you apart from your competitors.
-
Reduce waste - Stop any activity that isn't adding value to the supply chains.
-
Create Flow: Ensure that the work process flows without interruptions.
-
Standardize & Simplify - Make processes as consistent and repeatable as possible.
-
Develop Relationships: Establish personal relationships both with internal and external stakeholders.
Although lean manufacturing has always been around, it is gaining popularity in recent years because of a renewed interest for the economy after 2008's global financial crisis. Many businesses have adopted lean production techniques to make them more competitive. According to some economists, lean manufacturing could be a significant factor in the economic recovery.
Lean manufacturing is now becoming a common practice in the automotive industry, with many benefits. These benefits include increased customer satisfaction, reduced inventory levels and lower operating costs.
Lean manufacturing can be applied to almost every aspect of an organization. It is especially useful for the production aspect of an organization, as it ensures that every step in the value chain is efficient and effective.
There are three main types:
-
Just-in Time Manufacturing, (JIT): This kind of lean manufacturing is also commonly known as "pull-systems." JIT is a method in which components are assembled right at the moment of use, rather than being manufactured ahead of time. This approach aims to reduce lead times, increase the availability of parts, and reduce inventory.
-
Zero Defects Manufacturing - ZDM: ZDM focuses its efforts on making sure that no defective units leave a manufacturing facility. If a part needs to be fixed during the assembly line, it should be repaired rather than scrapped. This is also true for finished products that require minor repairs before shipping.
-
Continuous Improvement (CI): CI aims to improve the efficiency of operations by continuously identifying problems and making changes in order to eliminate or minimize waste. Continuous Improvement (CI) involves continuous improvement in processes, people, tools, and infrastructure.