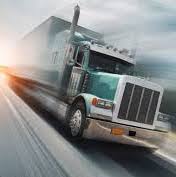
Factory orders are a great way to tell if your economy is moving in the right direction. They measure the growth of the manufacturing sector, and give you a sense of how much of the consumer market is buying goods. The stronger the economy, the more new orders it receives.
The U.S. Census Bureau, a Division of the Department of Commerce, publishes every month the Factory Orders Report. It's measured in dollars and shows total inventories and shipments. This includes durable as well non-durable products. In addition, the report focuses on the amount of unfilled orders.
Each month, the report is published in the first few days. It is an excellent source of economic data for monitoring the economy and providing an economic background for portfolios. There are many reasons to track economic data, and the most important is that it can help you develop a clear picture of the current state of the economy.
The US factory orders report will likely increase over the next few months. However, investors must be cautious. This is due to the fact that inflation is picking up again. And, as the Federal Reserve moves to raise interest rates at a faster rate than has been seen in years, demand for goods and services is slowing down.
A survey of top executives has shown that the economy is slowing. For example, consumer spending is down, and it is possible that the government will cut its budget by more than it has in recent years. This is combined with the most recent rate-hike cycle putting pressure to the manufacturing sector. This is why Federal Reserve is revising its approach to Monetary Policy.
Despite not being the most important indicator of economy, the Factory Orders Report still provides valuable economic data. It measures the volume of new orders placed by factories, the total shipments of goods, and the inventories of these companies. These data are useful in determining the overall health of the economy, and they are also important for predicting future output levels.
The report is divided into the following sections: the "Factory Orders", section, "Factory Orders M3", section, "Factory Shipments", section and the "Inventories". The most complete of these is the "Factory Orders report". This calculation includes all new orders received by factories.
The "Factory Orders(M3)" report provides a greater level of detail than the "Factory Shipments", which only shows the number of shipments of manufactured products. Both "Factory Shipments” as well as "Factory Orders” are measured in dollars. More information can be found on the Commerce Department's website.
An unfilled order indicator is also part of the "Factory Orders” report. This indicator indicates how many shipments of durable and other non-durable goods have not been filled. It indicates that there is an industrial demand to purchase durable goods when the indicator rises.
FAQ
What are the 7 Rs of logistics?
The acronym 7Rs of Logistics refers to the seven core principles of logistics management. It was created by the International Association of Business Logisticians and published in 2004 under its "Seven Principles of Logistics Management".
The acronym consists of the following letters:
-
Responsible - ensure that actions are in compliance with legal requirements and do not cause harm to others.
-
Reliable – have faith in your ability and capability to keep promises.
-
Reasonable - make sure you use your resources well and don't waste them.
-
Realistic – Consider all aspects, including cost-effectiveness as well as environmental impact.
-
Respectful - treat people fairly and equitably.
-
Responsive - Look for ways to save time and increase productivity.
-
Recognizable provides value-added products and services to customers
What skills does a production planner need?
Production planners must be flexible, organized, and able handle multiple tasks. Also, you must be able and willing to communicate with clients and coworkers.
What do you mean by warehouse?
Warehouses and storage facilities are where goods are kept before being sold. It can be indoors or out. It could be one or both.
What does it take to run a logistics business?
To be a successful businessman in logistics, you will need many skills and knowledge. For clients and suppliers to be successful, you need to have excellent communication skills. You will need to know how to interpret data and draw conclusions. You must be able to work well under pressure and handle stressful situations. To improve efficiency, you must be innovative and creative. You must be a strong leader to motivate others and direct them to achieve organizational goals.
It is important to be organized and efficient in order to meet tight deadlines.
What is the role of a logistics manager
Logistics managers are responsible for ensuring that all goods arrive in perfect condition and on time. This is done by using his/her experience and knowledge of the company's products. He/she must also ensure sufficient stock to meet the demand.
Can we automate some parts of manufacturing?
Yes! Automation has been around since ancient times. The Egyptians invent the wheel thousands of year ago. Nowadays, we use robots for assembly lines.
Actually, robotics can be used in manufacturing for many purposes. They include:
-
Line robots
-
Robot welding
-
Robot painting
-
Robotics inspection
-
Robots that make products
Manufacturing can also be automated in many other ways. For example, 3D printing allows us to make custom products without having to wait for weeks or months to get them manufactured.
What is the best way to learn about manufacturing?
Practical experience is the best way of learning about manufacturing. However, if that's not possible, you can always read books or watch educational videos.
Statistics
- Many factories witnessed a 30% increase in output due to the shift to electric motors. (en.wikipedia.org)
- [54][55] These are the top 50 countries by the total value of manufacturing output in US dollars for its noted year according to World Bank.[56] (en.wikipedia.org)
- It's estimated that 10.8% of the U.S. GDP in 2020 was contributed to manufacturing. (investopedia.com)
- Job #1 is delivering the ordered product according to specifications: color, size, brand, and quantity. (netsuite.com)
- In 2021, an estimated 12.1 million Americans work in the manufacturing sector.6 (investopedia.com)
External Links
How To
How to Use Six Sigma in Manufacturing
Six Sigma is defined by "the application SPC (statistical process control) techniques to achieve continuous improvements." Motorola's Quality Improvement Department, Tokyo, Japan, developed it in 1986. Six Sigma's basic concept is to improve quality and eliminate defects through standardization. This method has been adopted by many companies in recent years as they believe there are no perfect products or services. Six Sigma aims to reduce variation in the production's mean value. If you take a sample and compare it with the average, you will be able to determine how much of the production process is different from the norm. If this deviation is too big, you know something needs fixing.
Understanding how variability works in your company is the first step to Six Sigma. Once you have this understanding, you will need to identify sources and causes of variation. Also, you will need to identify the sources of variation. Random variations are caused when people make mistakes. While systematic variations are caused outside of the process, they can occur. These are, for instance, random variations that occur when widgets are made and some fall off the production line. However, if you notice that every time you assemble a widget, it always falls apart at exactly the same place, then that would be a systematic problem.
Once you've identified the problem areas you need to find solutions. You might need to change the way you work or completely redesign the process. To verify that the changes have worked, you need to test them again. If they don't work, you will need to go back to the drawing boards and create a new plan.