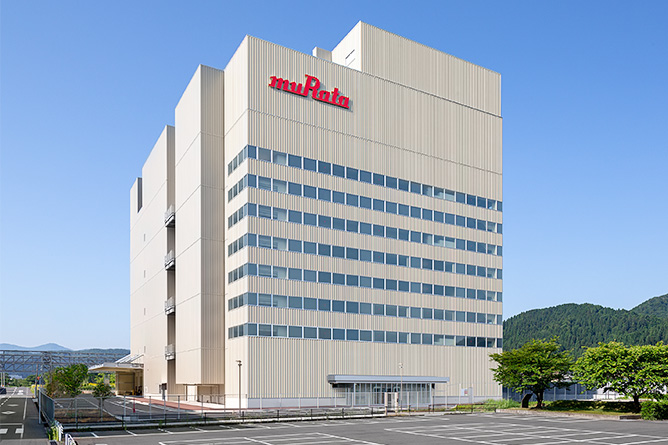
Global supply chains have changed over the years. They have become a major economic problem, rather than being an industrial problem. It is worth keeping an eye on new developments. Global supply chains are a complex system that interact in many ways.
Global value chain are made up of capital, flows, and intangibles. They are a reflection of economies of scale and long-standing relationships, as well as specialization. Some value chains have high capital requirements, but others are more regionalized.
Global supply chains are dynamic, multi-dimensional, and increasingly complex. They are an essential component of global trade and the functioning of economies. They are also susceptible for disruptions. These disruptions may be temporary or long-lasting. A flexible, resilient, diverse supply chain is the best way for these disruptions to be avoided. This requires a holistic approach that includes structural reform and strategic initiatives as well as prudent risk management. Identifying the biggest challenges and assessing the solutions is the first step towards building a supply chain that can withstand the next storm.
Companies should assess the risks of supply-chain disruptions and also consider the risks associated manufacturing, energy, and materials. They should also simulate extreme supply/demand disruptions in an effort to gauge their impact. They should also assess their inventories for critical materials and ensure that there is enough supply to meet demand. A strategic strategy is required to develop a resilient supply network. This may involve reprioritizing production and shifting manufacturing to more flexible places, improving supply chain technology, and implementing guaranteed sources.
The COVID-19 epidemic caused severe disruptions in global supply chain operations. Many countries imposed tariffs against one another, while other countries imposed sanctions on the other. These tariffs and sanctions have increased trade frictions and made it more difficult for the United States to sell certain products to China and other countries. These disruptions have led to an increase in price inflation. But they have also made companies more aware of the fragility of their supply chains and have made them re-think the design and implementation of their supply chains.
While the COVID-19 pandemic caused widespread disruption in global supply chains, the effects are still being felt. The blockage of the Suez Canal, for instance, has caused supply chain disruptions for up to six months. This has caused a sharp rise in freight cost. Annual inflation in the UK has reached 9%.
It's hard to ignore the fact that the United States and China are facing a trade war. Supply chain leaders must question the logic of heavily relying on outsourced networks. They should also take into account the risks of labor shortages caused by economic shocks. Leaders in supply chains should also be aware of the potential benefits of cross-border finance as well as regulation that can help expand global integration.
Despite all the chaos, the world continues to be a deeply interconnected place. If firms are open to a more holistic approach in their supply chains, global integration will bring benefits.
FAQ
What is the responsibility of a production planner?
A production planner makes sure all project elements are delivered on schedule, within budget, as well as within the agreed scope. They make sure that the product and services meet client expectations.
How does a production planner differ from a project manager?
The major difference between a Production Planner and a Project Manager is that a Project Manager is often the person responsible for organizing and planning the entire project. While a Production Planner is involved mainly in the planning stage,
What are the responsibilities for a manufacturing manager
Manufacturing managers must ensure that manufacturing processes are efficient, effective, and cost-effective. They should be aware of any issues within the company and respond accordingly.
They should also know how to communicate with other departments such as sales and marketing.
They should be informed about industry trends and be able make use of this information to improve their productivity and efficiency.
Statistics
- In 2021, an estimated 12.1 million Americans work in the manufacturing sector.6 (investopedia.com)
- According to a Statista study, U.S. businesses spent $1.63 trillion on logistics in 2019, moving goods from origin to end user through various supply chain network segments. (netsuite.com)
- Job #1 is delivering the ordered product according to specifications: color, size, brand, and quantity. (netsuite.com)
- It's estimated that 10.8% of the U.S. GDP in 2020 was contributed to manufacturing. (investopedia.com)
- [54][55] These are the top 50 countries by the total value of manufacturing output in US dollars for its noted year according to World Bank.[56] (en.wikipedia.org)
External Links
How To
Six Sigma: How to Use it in Manufacturing
Six Sigma can be described as "the use of statistical process control (SPC), techniques to achieve continuous improvement." Motorola's Quality Improvement Department created Six Sigma at their Tokyo plant, Japan in 1986. Six Sigma's main goal is to improve process quality by standardizing processes and eliminating defects. This method has been adopted by many companies in recent years as they believe there are no perfect products or services. Six Sigma's main objective is to reduce variations from the production average. This means that if you take a sample of your product, then measure its performance against the average, you can find out what percentage of the time the process deviates from the norm. If it is too large, it means that there are problems.
Understanding the nature of variability in your business is the first step to Six Sigma. Once you understand this, you can then identify the causes of variation. This will allow you to decide if these variations are random and systematic. Random variations are caused by human errors. Systematic variations can be caused by outside factors. Random variations would include, for example, the failure of some widgets to fall from the assembly line. However, if you notice that every time you assemble a widget, it always falls apart at exactly the same place, then that would be a systematic problem.
Once you've identified the problem areas you need to find solutions. That solution might involve changing the way you do things or redesigning the process altogether. After implementing the new changes, you should test them again to see if they worked. If they don't work you need to rework them and come up a better plan.