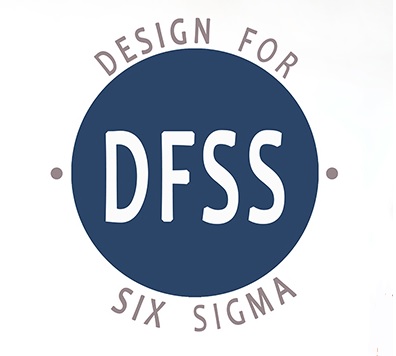
Production workers play a crucial role in manufacturing. They help get the products to market. From operating machinery to working in warehouses, these employees help make sure all of the components that go into creating a product are properly made and packaged for shipping.
The average manufacturing wages are higher than those of other industries. The wage premiums generally range between 10 and 15 percent (Langdon, Lehrman, 2012). The compensation premium for the past few years has been significantly lower. This suggests that those advocating for the expansion of manufacturing cannot take the benefit for granted.
Pay by Experience Level for Production Workers
You are more likely to earn higher salaries as a production employee if you have good skills and experience. Your earning potential can be increased by changing jobs, gaining new experience, and moving into a job with more managerial responsibilities.
Create Effective Workplace Strategy
As a manufacturing worker you should look at ways to improve your workplace's efficiency without sacrificing its quality. This means identifying the areas that slow down production and finding a solution to speed up the entire line. It is important to work with supervisors as well as other members of the team in order to implement and measure these efficiency improvements.
Safety at Work. It is important to keep all equipment clean and prevent accidents.
Maintaining Production Standards. As a production worker you have the responsibility of producing high quality products that meet strict standards in manufacturing and quality. In order to achieve this, you must be able to operate machines consistently and accurately and check the equipment for any defects.
Cleaning the Workplace. As a worker in production, it is your responsibility to clean the workspace and all equipment at the end each production session. To prevent contamination, and to ensure a more productive workplace, you should clean your workspace at the end of each production session.
Monitoring Product Qualitative: As a producer, you must conduct daily inspections in order to make sure that your output meets company specifications. This includes checking for faulty items and recording them on your production report.
Use of New Technologies for Productivity Improvement: As a manufacturing worker you are able apply new and innovative methods to the factory environment. You may decide to adopt a different way of assembling products or develop an alternative system for packaging.
These improvements could increase the productivity and earnings of your business as well as the production workers. These improvements may include things such as implementing robots, automating processes, or improving the human-machine interaction.
Manufacturing Workers' Wages
As a manufacturer, you must be aware of how much other workers in your industry earn. This will help you to set a competitive wage. This could include looking for new positions with other companies, getting advanced degrees or certificates, and managing yourself to qualify as a candidate for promotions.
FAQ
What is the responsibility of a manufacturing manager?
A manufacturing manager must make sure that all manufacturing processes run smoothly and effectively. They should also be aware and responsive to any company problems.
They should also know how to communicate with other departments such as sales and marketing.
They should also be aware of the latest trends in their industry and be able to use this information to help improve productivity and efficiency.
What types of jobs can you find in logistics
There are many kinds of jobs available within logistics. Some of them are:
-
Warehouse workers: They load and unload trucks, pallets, and other cargo.
-
Transportation drivers: They drive trucks and trailers and deliver goods and make pick-ups.
-
Freight handlers - They sort and pack freight in warehouses.
-
Inventory managers – These people oversee inventory at warehouses.
-
Sales representatives - They sell products.
-
Logistics coordinators are responsible for organizing and planning logistics operations.
-
Purchasing agents - They purchase goods and services needed for company operations.
-
Customer service representatives - Answer calls and email from customers.
-
Ship clerks - They issue bills and process shipping orders.
-
Order fillers are people who fill orders based only on what was ordered.
-
Quality control inspectors - They check incoming and outgoing products for defects.
-
Others - There is a variety of other jobs in logistics. These include transportation supervisors and cargo specialists.
What skills is required for a production planner?
You must be flexible and organized to become a productive production planner. Effective communication with clients and colleagues is essential.
Is it necessary to be familiar with Manufacturing Processes before we learn about Logistics.
No. No. However, knowing about manufacturing processes will definitely give you a better understanding of how logistics works.
What are the 7 R's of logistics?
The acronym 7Rs of Logistics refers to the seven core principles of logistics management. It was developed by the International Association of Business Logisticians (IABL) and published in 2004 as part of its "Seven Principles of Logistics Management" series.
The following letters make up the acronym:
-
Responsible – ensure that all actions are legal and don't cause harm to anyone else.
-
Reliable – have faith in your ability and capability to keep promises.
-
Be responsible - Use resources efficiently and avoid wasting them.
-
Realistic - consider all aspects of operations, including cost-effectiveness and environmental impact.
-
Respectful - Treat people fairly and equitably
-
Resourceful - look for opportunities to save money and increase productivity.
-
Recognizable - provide customers with value-added services.
How can manufacturing avoid production bottlenecks
Avoiding production bottlenecks is as simple as keeping all processes running smoothly, from the time an order is received until the product ships.
This includes both planning for capacity and quality control.
The best way to do this is to use continuous improvement techniques such as Six Sigma.
Six Sigma is a management system used to improve quality and reduce waste in every aspect of your organization.
It is focused on creating consistency and eliminating variation in your work.
What are the four types in manufacturing?
Manufacturing refers to the transformation of raw materials into useful products by using machines and processes. It involves many different activities such as designing, building, testing, packaging, shipping, selling, servicing, etc.
Statistics
- According to the United Nations Industrial Development Organization (UNIDO), China is the top manufacturer worldwide by 2019 output, producing 28.7% of the total global manufacturing output, followed by the United States, Japan, Germany, and India.[52][53] (en.wikipedia.org)
- In the United States, for example, manufacturing makes up 15% of the economic output. (twi-global.com)
- Job #1 is delivering the ordered product according to specifications: color, size, brand, and quantity. (netsuite.com)
- It's estimated that 10.8% of the U.S. GDP in 2020 was contributed to manufacturing. (investopedia.com)
- (2:04) MTO is a production technique wherein products are customized according to customer specifications, and production only starts after an order is received. (oracle.com)
External Links
How To
How to Use the Just-In-Time Method in Production
Just-in-time (JIT) is a method that is used to reduce costs and maximize efficiency in business processes. It is a process where you get the right amount of resources at the right moment when they are needed. This means that you only pay the amount you actually use. Frederick Taylor was the first to coin this term. He developed it while working as a foreman during the early 1900s. He observed how workers were paid overtime if there were delays in their work. He decided that workers would be more productive if they had enough time to complete their work before they started to work.
JIT is about planning ahead. You should have all the necessary resources ready to go so that you don’t waste money. You should also look at the entire project from start to finish and make sure that you have sufficient resources available to deal with any problems that arise during the course of your project. You can anticipate problems and have enough equipment and people available to fix them. This way you won't be spending more on things that aren’t really needed.
There are many JIT methods.
-
Demand-driven: This type of JIT allows you to order the parts/materials required for your project on a regular basis. This will allow for you to track the material that you have left after using it. This will allow to you estimate the time it will take for more to be produced.
-
Inventory-based: This allows you to store the materials necessary for your projects in advance. This allows for you to anticipate how much you can sell.
-
Project-driven: This approach involves setting aside sufficient funds to cover your project's costs. You will be able to purchase the right amount of materials if you know what you need.
-
Resource-based JIT: This is the most popular form of JIT. You assign certain resources based off demand. If you have many orders, you will assign more people to manage them. If you don’t have many orders you will assign less people to the work.
-
Cost-based : This is similar in concept to resource-based. But here, you aren't concerned about how many people your company has but how much each individual costs.
-
Price-based pricing: This is similar in concept to cost-based but instead you look at how much each worker costs, it looks at the overall company's price.
-
Material-based: This approach is similar to cost-based. However, instead of looking at the total cost for the company, you look at how much you spend on average on raw materials.
-
Time-based: This is another variation of resource-based JIT. Instead of focusing on how much each employee costs, you focus on how long it takes to complete the project.
-
Quality-based JIT: This is another variation of resource based JIT. Instead of focusing on the cost of each worker or how long it takes, think about how high quality your product is.
-
Value-based JIT: This is the latest form of JIT. In this instance, you are not concerned about the product's performance or meeting customer expectations. Instead, you're focused on how much value you add to the market.
-
Stock-based: This stock-based method focuses on the actual quantity of products being made at any given time. It's used when you want to maximize production while minimizing inventory.
-
Just-in-time (JIT) planning: This is a combination of JIT and supply chain management. It's the process of scheduling delivery of components immediately after they are ordered. It's important as it reduces leadtimes and increases throughput.