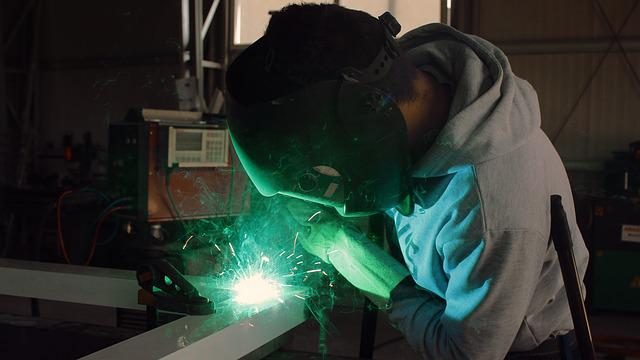
Demand management is a method that ensures that customers are satisfied. It is essentially bridging the gap between supply and marketing by allowing organizations to predict demand. The process can help companies improve the speed and quality of delivery, reduce the amount of invoice disputes, and lower the cost of running the business.
Companies with a well-developed demand management system tend to be more responsive when the market changes occur. They have a process in place to identify the ideal client, which can help with marketing.
Demand management can also help businesses plan for upcoming demand and increase customer satisfaction. Correctly done, demand management can help businesses reduce invoice disputes as well as improve asset utilization. A good demand management strategy will also increase operational flexibility and operational resilience.
Project management software programs can enhance demand management. Software such as project management software can be used to help teams coordinate and avoid silos. A change management plan is a tool that can be used to help companies quickly fix supply chain problems.
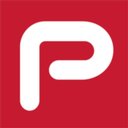
ILOG's PowerOps Suite, for example, integrates manufacturing scheduling functions. Dynasys and QAD offer similar applications that enable organizations to create a supply and demand plan. These applications can help organizations visualize the impact of changes on their supply chains. Optiant provides ERP solutions that allow organizations to establish efficient, consistent, and effective order- and supply management processes.
Tools such as CDC Software, Terra Technology, and Real-Time Inventory provide real-time forecasting solutions which can help reduce supply chain disruptions. Companies can also benefit from the collaborative management strategy which allows them to share information. It involves planning and executing joint actions, knowledge sharing, performance indicators, and planning.
Before you implement a demand management strategy, however, it is important that you consider these factors. These factors will help professionals understand the process better and keep their focus on the most important elements.
Leadership buy in is an essential part of a demand management process. Demand management is a collaborative process that requires input from all levels of management. Managers and top executives are the most important players at the highest levels. They are responsible for ensuring all members are on the exact same page. To ensure the success of the initiative, it is also crucial to include those at the lower levels.
While there are many applications that can help organizations implement a demand and supply plan, some of the key aspects to remember include:
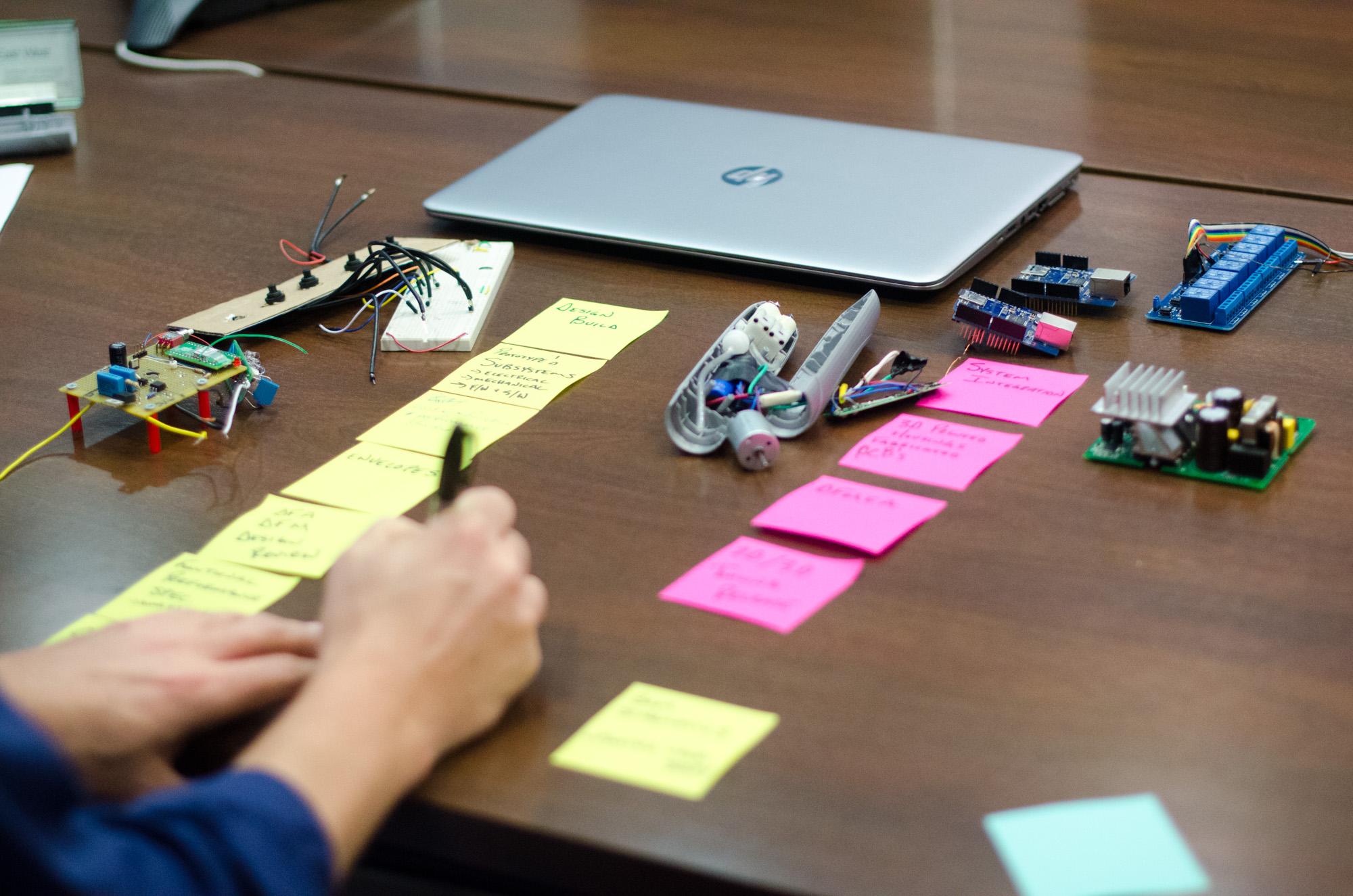
The demand management process is only possible if you know your market well enough to identify the perfect customer. An organization must be able to accurately measure and analyze the outcomes of its efforts, in addition to knowing which customers to target.
As businesses look to become more nimble, they must develop a demand management strategy that can be easily altered to accommodate change. A well-designed plan will reduce supply chain disruptions and tactical forecast errors. Demand management is also a useful tool in the development and implementation of portfolio and strategic planning.
FAQ
What does it mean to warehouse?
Warehouses and storage facilities are where goods are kept before being sold. It can be either an indoor or outdoor space. In some cases it could be both indoors and outdoors.
How can we reduce manufacturing overproduction?
Better inventory management is key to reducing excess production. This would reduce the time needed to manage inventory. By doing this, we could free up resources for other productive tasks.
You can do this by adopting a Kanban method. A Kanban Board is a visual display that tracks work progress. In a Kanban system, work items move through a sequence of states until they reach their final destination. Each state has a different priority level.
As an example, if work is progressing from one stage of the process to another, then the current task is complete and can be transferred to the next. But if a task remains in the beginning stages it will stay that way until it reaches its end.
This allows for work to continue moving forward, while also ensuring that there is no work left behind. Managers can monitor the work being done by Kanban boards to see what is happening at any given time. This allows them the ability to adjust their workflow using real-time data.
Lean manufacturing can also be used to reduce inventory levels. Lean manufacturing is about eliminating waste from all stages of the production process. Waste includes anything that does not add value to the product. There are several types of waste that you might encounter:
-
Overproduction
-
Inventory
-
Packaging not required
-
Material surplus
By implementing these ideas, manufacturers can improve efficiency and cut costs.
What are the 4 types of manufacturing?
Manufacturing is the process that transforms raw materials into useful products. It involves many different activities such as designing, building, testing, packaging, shipping, selling, servicing, etc.
What are the responsibilities of a manufacturing manager
A manufacturing manager must ensure that all manufacturing processes are efficient and effective. They should be alert for any potential problems in the company and react accordingly.
They should also be able and comfortable communicating with other departments like sales and marketing.
They should also be knowledgeable about the latest trends in the industry so they can use this information for productivity and efficiency improvements.
What is the role of a production manager?
A production planner ensures all aspects of the project are delivered on time, within budget, and within scope. They make sure that the product and services meet client expectations.
What are the requirements to start a logistics business?
It takes a lot of skills and knowledge to run a successful logistics business. Good communication skills are essential to effectively communicate with your suppliers and clients. You must be able analyze data and draw out conclusions. You will need to be able handle pressure well and work in stressful situations. To increase efficiency and creativity, you need to be creative. You must be a strong leader to motivate others and direct them to achieve organizational goals.
You must be organized to meet tight deadlines.
What are the responsibilities of a logistic manager?
Logistics managers are responsible for ensuring that all goods arrive in perfect condition and on time. This is accomplished by using the experience and knowledge gained from working with company products. He/she must also ensure sufficient stock to meet the demand.
Statistics
- You can multiply the result by 100 to get the total percent of monthly overhead. (investopedia.com)
- In 2021, an estimated 12.1 million Americans work in the manufacturing sector.6 (investopedia.com)
- It's estimated that 10.8% of the U.S. GDP in 2020 was contributed to manufacturing. (investopedia.com)
- Many factories witnessed a 30% increase in output due to the shift to electric motors. (en.wikipedia.org)
- According to the United Nations Industrial Development Organization (UNIDO), China is the top manufacturer worldwide by 2019 output, producing 28.7% of the total global manufacturing output, followed by the United States, Japan, Germany, and India.[52][53] (en.wikipedia.org)
External Links
How To
Six Sigma in Manufacturing:
Six Sigma is defined as "the application of statistical process control (SPC) techniques to achieve continuous improvement." Motorola's Quality Improvement Department created Six Sigma at their Tokyo plant, Japan in 1986. Six Sigma's basic concept is to improve quality and eliminate defects through standardization. Since there are no perfect products, or services, this approach has been adopted by many companies over the years. Six Sigma aims to reduce variation in the production's mean value. It is possible to measure the performance of your product against an average and find the percentage of time that it differs from the norm. If you notice a large deviation, then it is time to fix it.
Understanding how your business' variability is a key step towards Six Sigma implementation is the first. Once you have this understanding, you will need to identify sources and causes of variation. This will allow you to decide if these variations are random and systematic. Random variations are caused when people make mistakes. While systematic variations are caused outside of the process, they can occur. You could consider random variations if some widgets fall off the assembly lines. If however, you notice that each time you assemble a widget it falls apart in exactly the same spot, that is a problem.
Once you identify the problem areas, it is time to create solutions. That solution might involve changing the way you do things or redesigning the process altogether. Once you have implemented the changes, it is important to test them again to ensure they work. If they don't work you need to rework them and come up a better plan.