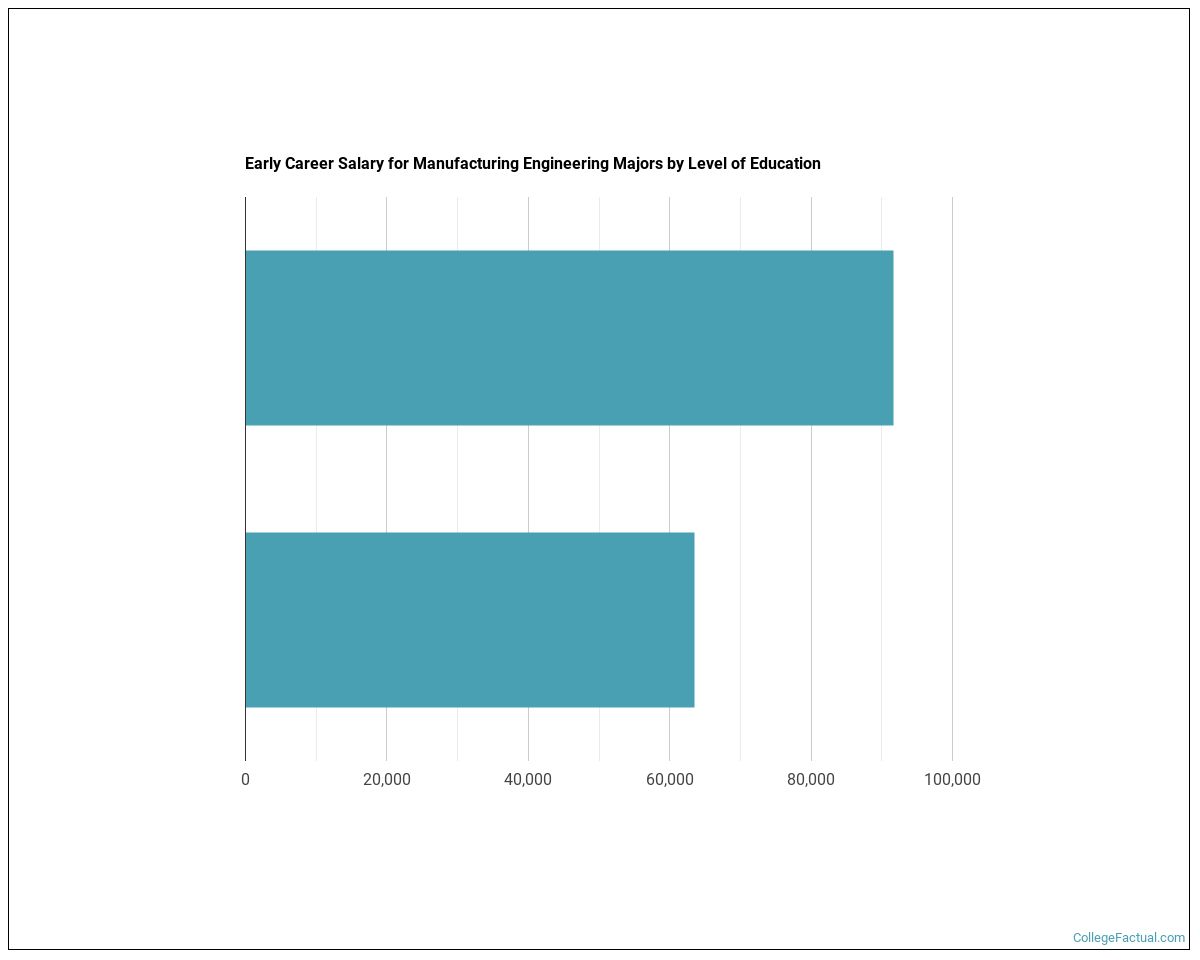
Toyota Production System, originally called Just-in-Time production was an integrated sociotechnical and technological system used to eliminate waste from processes and improve them. It is designed to efficiently organize manufacturing, logistics, and customer interaction. It encourages continuous improvement and employee growth. It is the basis of Lean Manufacturing. Toyota Production System has been applied to many manufacturing facilities in the United States and overseas.
SakichiToyoda, founder of Toyota was the one who developed Toyota Production System. Sakichi Toyoda analyzed each phase of his company's production, and removed all unnecessary parts. This resulted in a 20% decrease in build time. Toyota also had to build a vehicle half the time it took GM. Toyota was however on the verge to go bankrupt in the 1950s.
Taiichi Ahno, Toyota's executive, saw the supermarket shelf-stocking process in the late 1940s. He discovered that Just in Time methods in vehicle production could make it more efficient. He developed the Toyota Production System from 1948 to 1975 with Eiji Toyoda (the president of Toyota).
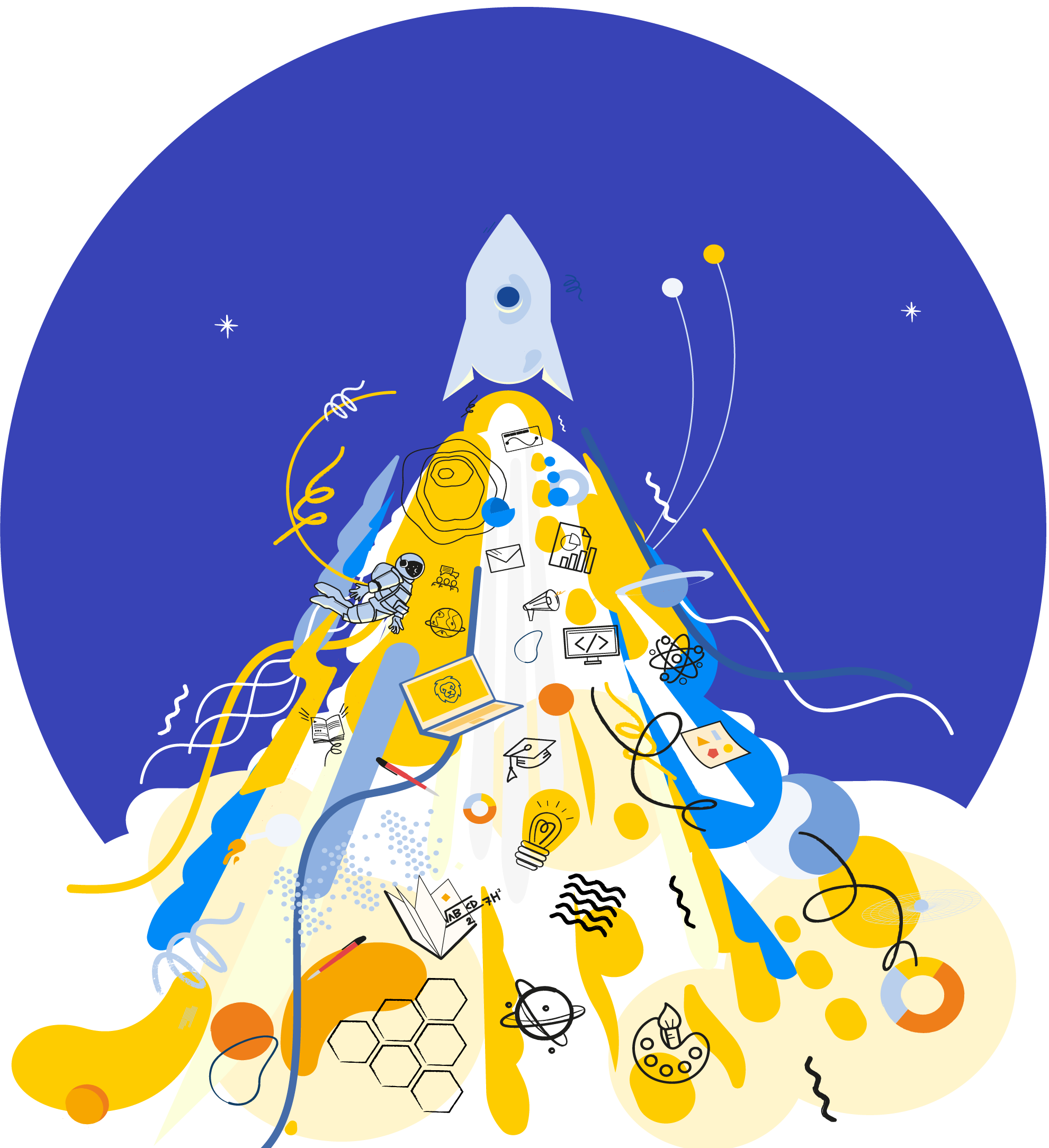
Toyota Production System was developed to eliminate wastefulness and inconsistency. Kaizen, Japanese for continuous improvement is the basis of the overall philosophy. Toyota's Production System is continually improved to meet company needs. It fosters learning in the company. It uses simple but efficient low-tech tools, combined with advanced production methods. It also utilizes innovative information technology as well unique social/management techniques.
The Toyota Production System is built on a set of six core principles. It has been used by many companies such as Boeing, Porsche, Honda, and others. These companies reengineered production processes to mimic Toyota's.
Toyota Production System also offers team building activities. These activities include weekly safety rounds with local leaders, which assess the performance of staff members in key safety initiatives. Everyone is encouraged to contribute ideas and identify opportunities for improvement. This has helped to change the culture in the company.
Another concept is Jidoka, which refers to automating processes with a human touch. Jidoka encourages workers to check their work and stop production when they find problems. Jidoka also stresses the importance in building things right from the beginning, and not overlooking problems.
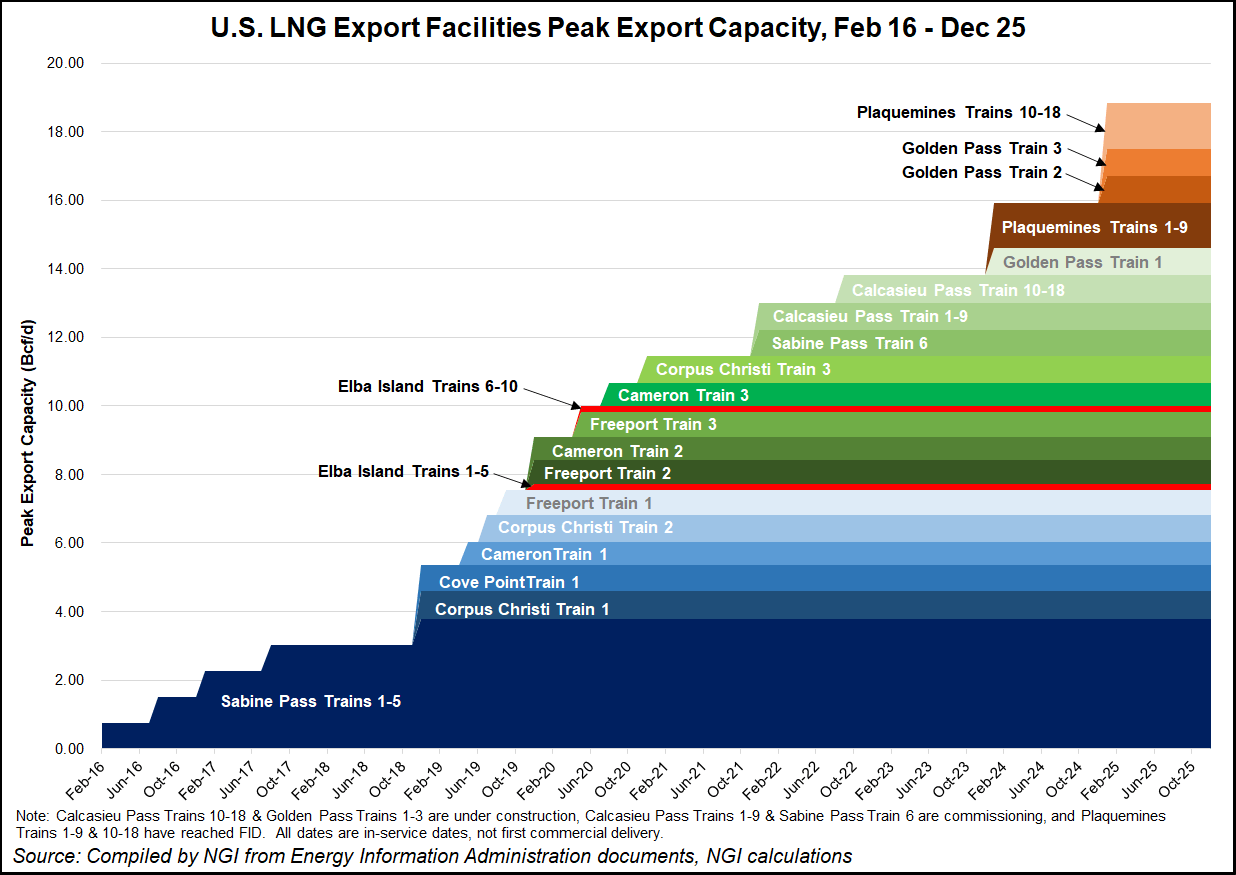
Visual control is an integral part of the Toyota Production System. It allows for work instructions to be clearly visible on the factory floors. This helps workers follow instructions precisely. The company also uses poka-yoke devices to verify quality standards. These devices can also be used to verify the identification of a red rabbit.
The Toyota Production System is not only applicable to manufacturing plants, but also health care. It can be used in improving patient satisfaction. It can be used in critical care and the operating rooms.
The Toyota Production System can be used to increase patient satisfaction and improve health care delivery. In 2003, an EPA case study reported that Toyota's efforts in waste reduction had caught the EPA’s attention. This led to several partnerships with companies including the St. Bernard Project, which employs military vets.
FAQ
Is it necessary to be familiar with Manufacturing Processes before we learn about Logistics.
No. No. However, knowing about manufacturing processes will definitely give you a better understanding of how logistics works.
What does it take to run a logistics business?
It takes a lot of skills and knowledge to run a successful logistics business. To communicate effectively with clients and suppliers, you must be able to communicate well. It is important to be able to analyse data and draw conclusions. You must be able manage stress and pressure under pressure. You must be creative and innovative to develop new ideas to improve efficiency. You will need strong leadership skills to motivate and direct your team members towards achieving their organizational goals.
To meet tight deadlines, you must also be efficient and organized.
Can we automate some parts of manufacturing?
Yes! Since ancient times, automation has been in existence. The Egyptians created the wheel thousands years ago. We now use robots to help us with assembly lines.
Actually, robotics can be used in manufacturing for many purposes. These include:
-
Robots for assembly line
-
Robot welding
-
Robot painting
-
Robotics inspection
-
Robots that create products
Manufacturing could also benefit from automation in other ways. For instance, 3D printing allows us make custom products and not have to wait for months or even weeks to get them made.
What are my options for learning more about manufacturing
Hands-on experience is the best way to learn more about manufacturing. You can also read educational videos or take classes if this isn't possible.
What are manufacturing and logistic?
Manufacturing is the production of goods using raw materials. Logistics covers all aspects involved in managing supply chains, including procurement and production planning. As a broad term, manufacturing and logistics often refer to both the creation and delivery of products.
Is automation important in manufacturing?
Automation is important not only for manufacturers but also for service providers. It allows them provide faster and more efficient services. It helps them to lower costs by reducing human errors, and improving productivity.
Statistics
- You can multiply the result by 100 to get the total percent of monthly overhead. (investopedia.com)
- In 2021, an estimated 12.1 million Americans work in the manufacturing sector.6 (investopedia.com)
- It's estimated that 10.8% of the U.S. GDP in 2020 was contributed to manufacturing. (investopedia.com)
- Many factories witnessed a 30% increase in output due to the shift to electric motors. (en.wikipedia.org)
- [54][55] These are the top 50 countries by the total value of manufacturing output in US dollars for its noted year according to World Bank.[56] (en.wikipedia.org)
External Links
How To
Six Sigma in Manufacturing:
Six Sigma is "the application statistical process control (SPC), techniques for continuous improvement." Motorola's Quality Improvement Department created Six Sigma at their Tokyo plant, Japan in 1986. Six Sigma's main goal is to improve process quality by standardizing processes and eliminating defects. Many companies have adopted this method in recent years. They believe there is no such thing a perfect product or service. Six Sigma seeks to reduce variation between the mean production value. This means that if you take a sample of your product, then measure its performance against the average, you can find out what percentage of the time the process deviates from the norm. If this deviation is too big, you know something needs fixing.
Understanding how variability works in your company is the first step to Six Sigma. Once you understand this, you can then identify the causes of variation. These variations can also be classified as random or systematic. Random variations are caused when people make mistakes. While systematic variations are caused outside of the process, they can occur. These are, for instance, random variations that occur when widgets are made and some fall off the production line. If however, you notice that each time you assemble a widget it falls apart in exactly the same spot, that is a problem.
After identifying the problem areas, you will need to devise solutions. It might mean changing the way you do business or redesigning it entirely. You should then test the changes again after they have been implemented. If they didn't work, then you'll need to go back to the drawing board and come up with another plan.