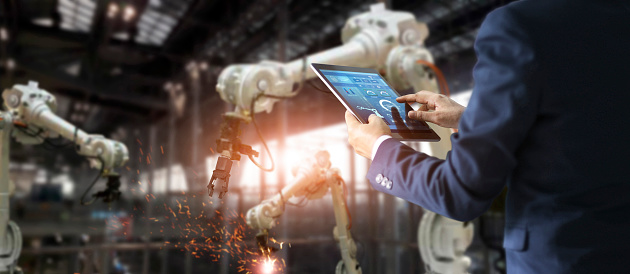
A number of factors have contributed to the recent shortage of chip supplies. These include transportation issues and manufacturing problems. There have also been many disasters that have caused the closure of chip plants. This has affected consumer devices including gaming consoles, healthcare devices, as well as data centers. The Chinese government has made several efforts to support semiconductor manufacturing in China. The Chinese government has created an investment fund to aid chip manufacturers.
As a result of this effort, China's chip production has seen tremendous progress over the past few years. According to IC Insights by 2025, China's chip production is expected to increase by 19.4%. The industry still has a ways to go before reaching its former levels. Despite these improvements, there is still a small number of chip companies in the country. Many of these companies have not yet become independent.
Huawei, Oppo & Midea are some the most popular chip manufacturers in China. Chinese companies have also been gaining significant market share within the mobile processor space. These companies are also developing their own chips to expand their chip manufacturing capabilities. This has helped to make them more competitive in the industry.
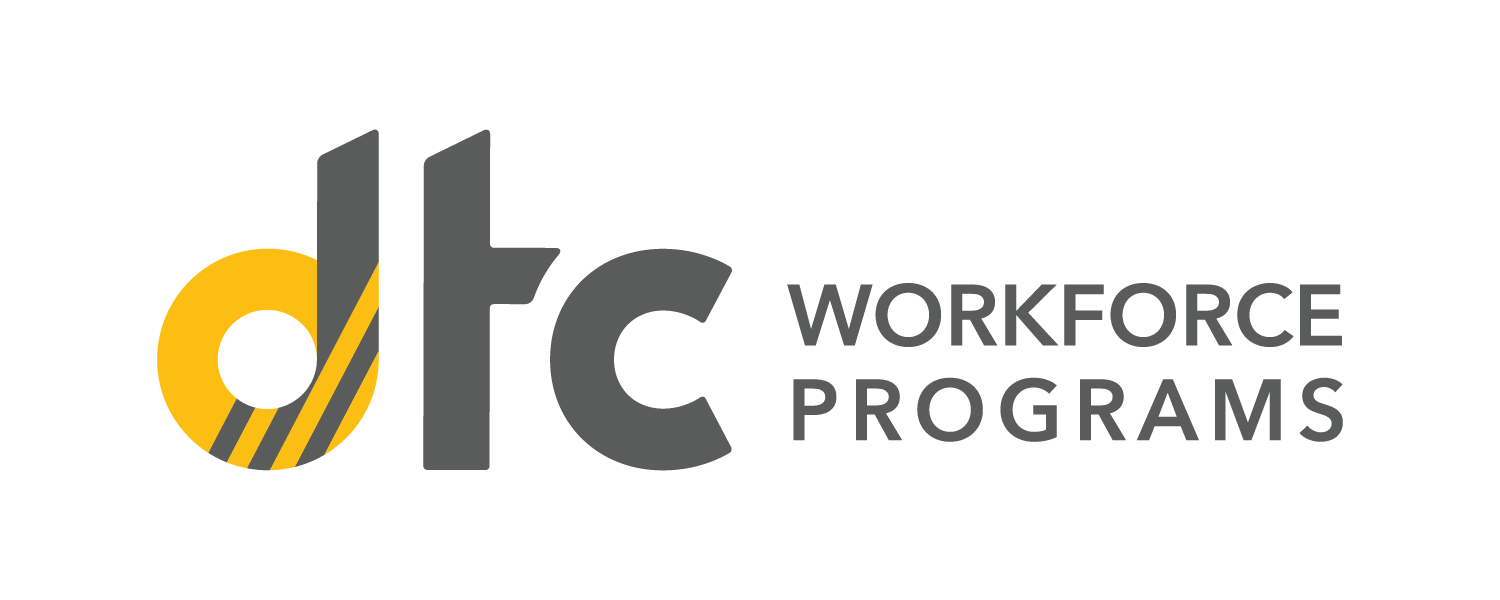
China is developing rapidly as a chip manufacturing hub. However, there are still limitations. Chinese companies have limited resources and are not able to mass-produce high end microchips. These chips are used in smartphones, wearable devices, and servers. In addition, the country is not yet self-sufficient in the raw materials required for chip manufacturing. These include enriched isotopes, tantalum, and neon. These raw materials are processed chemically.
The Chinese government is also keen to decrease its dependence upon imported chips. China will produce 70% of its chips in China by 2025, according to the country. This will be difficult to achieve, however. China currently has 32 registered chip companies, many of which are still waiting for IPOs. The government actively markets its industrial policies. The government hopes to encourage more chip production in the country. This is a major challenge considering the resources available.
The US semiconductor sector is currently facing an unprecedented shortage for tech talent. Washington also recently adopted new rules to limit the US's ability to support chip production.
TSMC is one of the most important chipmakers in the world. However, it has not made any announcements yet about a new plant in Europe. But, it has not ruled building an older-generation European chip plant. The company has also partnered with European automakers to purchase less-advanced chips. The idea was largely rejected by European automakers. Adding a plant to Europe to the supply chains would mean chips would have back-end processing in Asia. This could prolong the life of the chip by several more years.
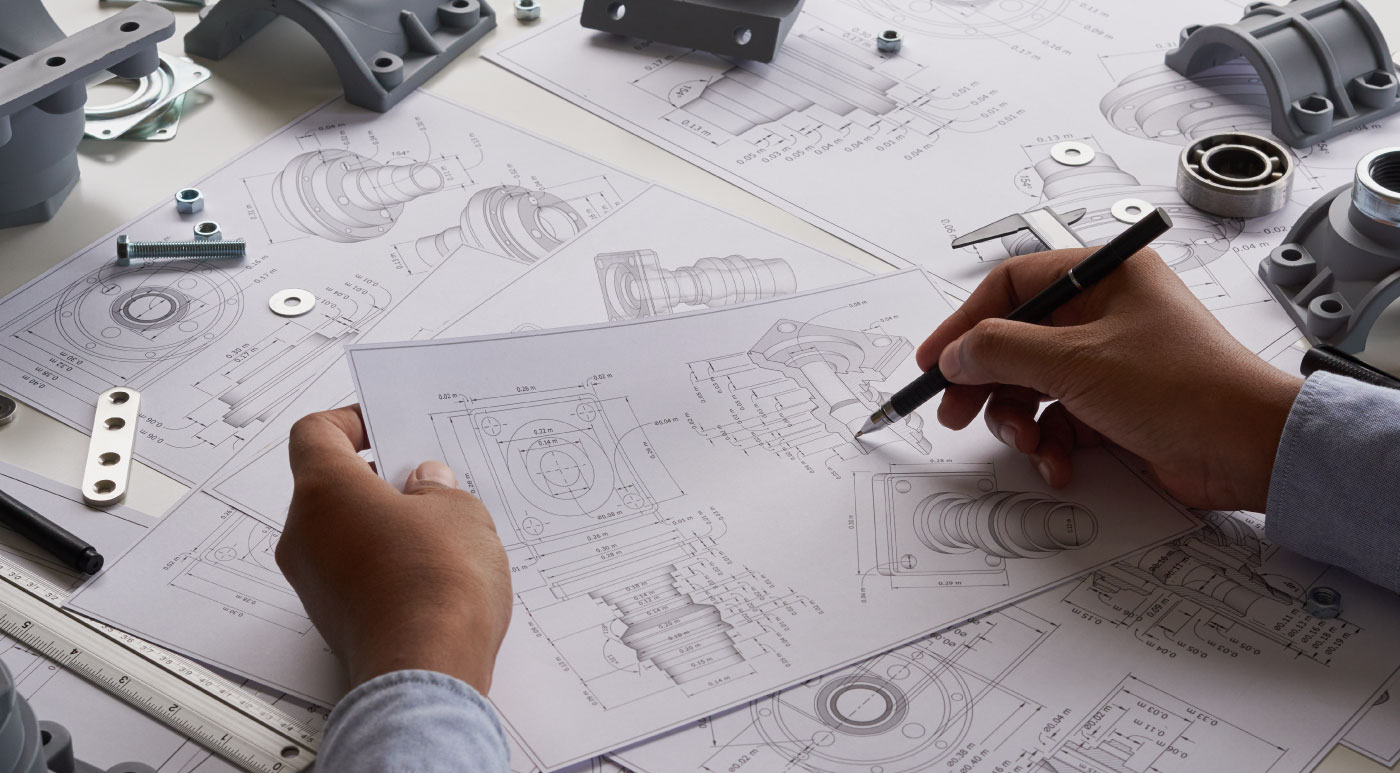
According to the US Commerce Department, there will be a severe shortage of chips in 2021. This has caused long delays for consumers. The shortage also has impacted transportation, healthcare, gaming consoles, and other areas. The US government will invest in reshoring chips production to create thousands of jobs and ensure a more resilient chip supply.
FAQ
Can certain manufacturing steps be automated?
Yes! Yes. The Egyptians invent the wheel thousands of year ago. Nowadays, we use robots for assembly lines.
There are many uses of robotics today in manufacturing. These include:
-
Assembly line robots
-
Robot welding
-
Robot painting
-
Robotics inspection
-
Robots create products
Manufacturing could also benefit from automation in other ways. 3D printing makes it possible to produce custom products in a matter of days or weeks.
What are the responsibilities of a production planner
Production planners ensure that all project aspects are completed on time, within budget and within the scope. They also ensure that the product/service meets the client’s needs.
What makes a production planner different from a project manger?
The primary difference between a producer planner and a manager of a project is that the manager usually plans and organizes the whole project, while a production planner is only involved in the planning stage.
How can we reduce manufacturing overproduction?
Improved inventory management is the key to reducing overproduction. This would reduce the time spent on unproductive activities like purchasing, storing and maintaining excess stock. This could help us free up our time for other productive tasks.
This can be done by using a Kanban system. A Kanban board can be used to monitor work progress. In a Kanban system, work items move through a sequence of states until they reach their final destination. Each state has a different priority level.
When work is completed, it can be transferred to the next stage. It is possible to keep a task in the beginning stages until it gets to the end.
This allows you to keep work moving along while making sure that no work gets neglected. Managers can see how much work has been done and the status of each task at any time with a Kanban Board. This information allows them to adjust their workflow based on real-time data.
Lean manufacturing is another way to manage inventory levels. Lean manufacturing emphasizes eliminating waste in all phases of production. Anything that doesn't add value to the product is considered waste. The following are examples of common waste types:
-
Overproduction
-
Inventory
-
Packaging that is not necessary
-
Overstock materials
These ideas can help manufacturers improve efficiency and reduce costs.
What is the role of a manager in manufacturing?
A manufacturing manager has to ensure that all manufacturing processes work efficiently and effectively. They should be alert for any potential problems in the company and react accordingly.
They should also be able and comfortable communicating with other departments like sales and marketing.
They should also be aware of the latest trends in their industry and be able to use this information to help improve productivity and efficiency.
How can manufacturing reduce production bottlenecks?
Production bottlenecks can be avoided by ensuring that processes are running smoothly during the entire production process, starting with the receipt of an order and ending when the product ships.
This includes planning to meet capacity requirements and quality control.
Continuous improvement techniques such Six Sigma are the best method to accomplish this.
Six Sigma Management System is a method to increase quality and reduce waste throughout your organization.
It focuses on eliminating variation and creating consistency in your work.
What does "warehouse" mean?
A warehouse or storage facility is where goods are stored before they are sold. It can be an indoor space or an outdoor area. In some cases, it may be a combination of both.
Statistics
- Job #1 is delivering the ordered product according to specifications: color, size, brand, and quantity. (netsuite.com)
- According to a Statista study, U.S. businesses spent $1.63 trillion on logistics in 2019, moving goods from origin to end user through various supply chain network segments. (netsuite.com)
- You can multiply the result by 100 to get the total percent of monthly overhead. (investopedia.com)
- In 2021, an estimated 12.1 million Americans work in the manufacturing sector.6 (investopedia.com)
- According to the United Nations Industrial Development Organization (UNIDO), China is the top manufacturer worldwide by 2019 output, producing 28.7% of the total global manufacturing output, followed by the United States, Japan, Germany, and India.[52][53] (en.wikipedia.org)
External Links
How To
How to Use 5S to Increase Productivity in Manufacturing
5S stands for "Sort", 'Set In Order", 'Standardize', & Separate>. Toyota Motor Corporation created the 5S methodology in 1954. It assists companies in improving their work environments and achieving higher efficiency.
The idea behind standardizing production processes is to make them repeatable and measurable. This means that tasks such as cleaning, sorting, storing, packing, and labeling are performed daily. These actions allow workers to perform their job more efficiently, knowing what to expect.
Implementing 5S involves five steps: Sort, Set in Order, Standardize Separate, Store, and Each step has a different action and leads to higher efficiency. By sorting, for example, you make it easy to find the items later. When you arrange items, you place them together. After you have divided your inventory into groups you can store them in easy-to-reach containers. Make sure everything is correctly labeled when you label your containers.
This requires employees to critically evaluate how they work. Employees must be able to see why they do what they do and find a way to achieve them without having to rely on their old methods. They must learn new skills and techniques in order to implement the 5S system.
The 5S method not only increases efficiency but also boosts morale and teamwork. As they begin to see improvements, they feel motivated to continue working towards the goal of achieving higher levels of efficiency.