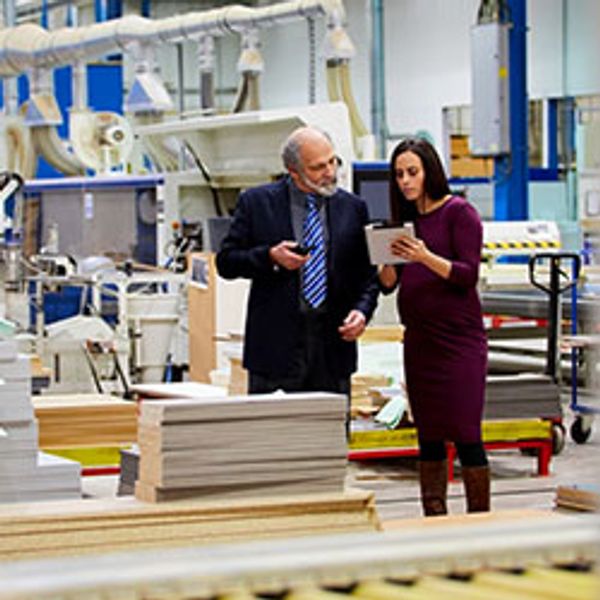
Apparel manufacturers today face a unique challenge in meeting the diverse demands of their customers. These consumers vary in terms of physiographics, socioeconomics, and demographics, and their preferences are not easily predictible. Additionally, consumer awareness of different products is increasing, and they can access information readily. They are also more likely to purchase high-fashion, expensive items.
Production efficiency
A key component of the overall strategy for apparel producers is to increase production efficiency. Clothing industry relies heavily on human labor. With ever-changing fashion trends and production planning, it is crucial to plan for the future. Apparel manufacturers must be flexible enough to meet global demands and maintain a short product cycle. In addition to designing new products, apparel companies should assess the efficiency of existing lines, and consider digital technologies that can speed up the product development process from months down to days. In the planning process, critical path analysis is crucial.
Although the apparel manufacturing industry is very labor-intensive, it is not impossible to increase production efficiency. It takes the right tools, and good management to achieve this goal. An increase of efficiency by 10 to 15% can result in a 35% increase in EBITDA. Additionally, efficiency can help increase workers' wages and increase the country’s competitiveness on global markets.
Fabric layering
Fabric layering is a technique used in apparel manufacture. This involves placing a pattern over a laid fabric. You can make the pattern either manually or using a plotter. The pattern components are laid in markers. They are then cut with a straight knife, or another cutting method.
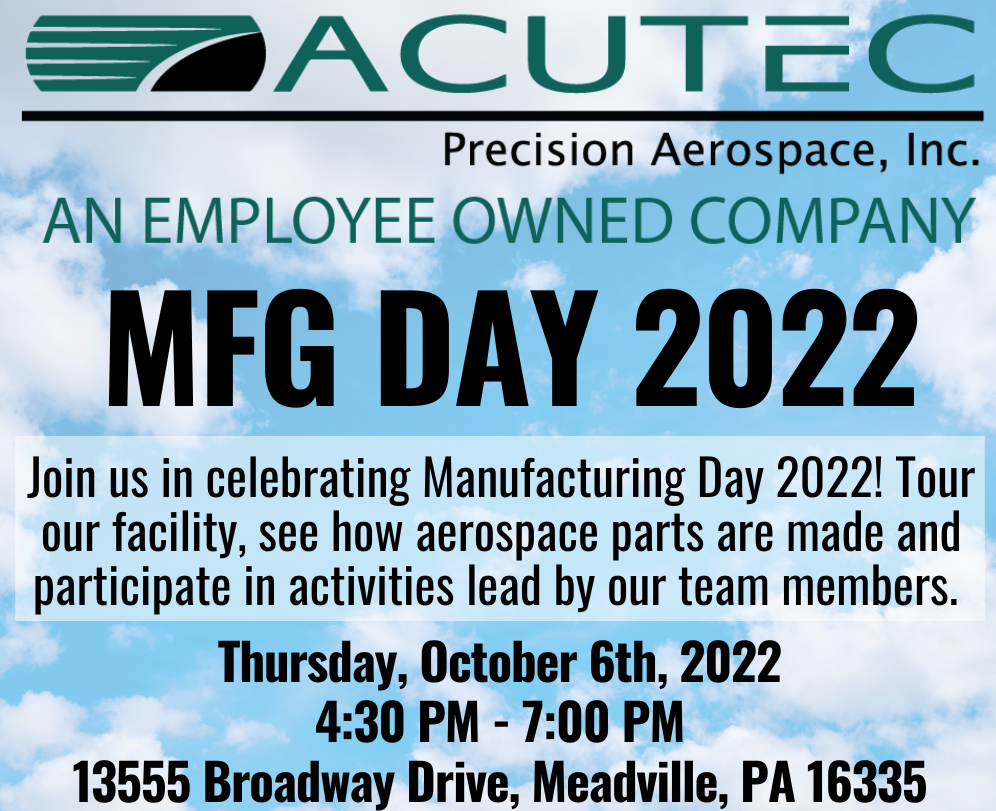
The fabric is evenly distributed during this process. The fabric can be laid in a pile, or in layers with the cutting marker. The maximum cutting width is the fabric width that is usable, minus any selvedges or needle marks. The area of fabric being used is also known by the term fabric utilization. Half-garment layout and whole-garment layout are the two main types. Half-garment lie involves only laying fabric on one side, while whole garment lay involves covering the entire garment piece with fabric. The disadvantage of the whole garment lay is that it consumes more fabric.
Cutting
The cutting process uses cutting blades to reduce a piece of fabric to a smaller size. Fabric typically accounts for 60% to 70% of the cost of a garment. Therefore, it is important that every inch is used. The strictest control system in apparel manufacturing will ensure that every ounce of fabric is used.
Spreading fabric onto a large surface is the first step to cutting fabric. In mass production, fabric is usually spread out in layers. Based on the number and thickness of the fabric, the cutting master decides how many layers are needed to cover a particular garment. Once the fabric has been spread out, it is measured so that a maximum cutting width can be determined.
Pressing
Pressing is an important process in the manufacture of apparel. It is responsible for maintaining the comfort of garments as well as their appearance. This is done in a factory. The press can be either manually or automatically operated. Software can be used to control the automation level. Software can be used to program a press to follow certain instructions. A factory that produces apparel can automate pressing to reduce human error. The increasing number of fibers and fabric varieties will require more precise control of temperature and pressure during the process.
The process of pressing involves heating the fibers of the garment. The garment's shape is stabilized by the softened fibers. It is important to choose the correct temperature in order not to damage the yarns and fibres.
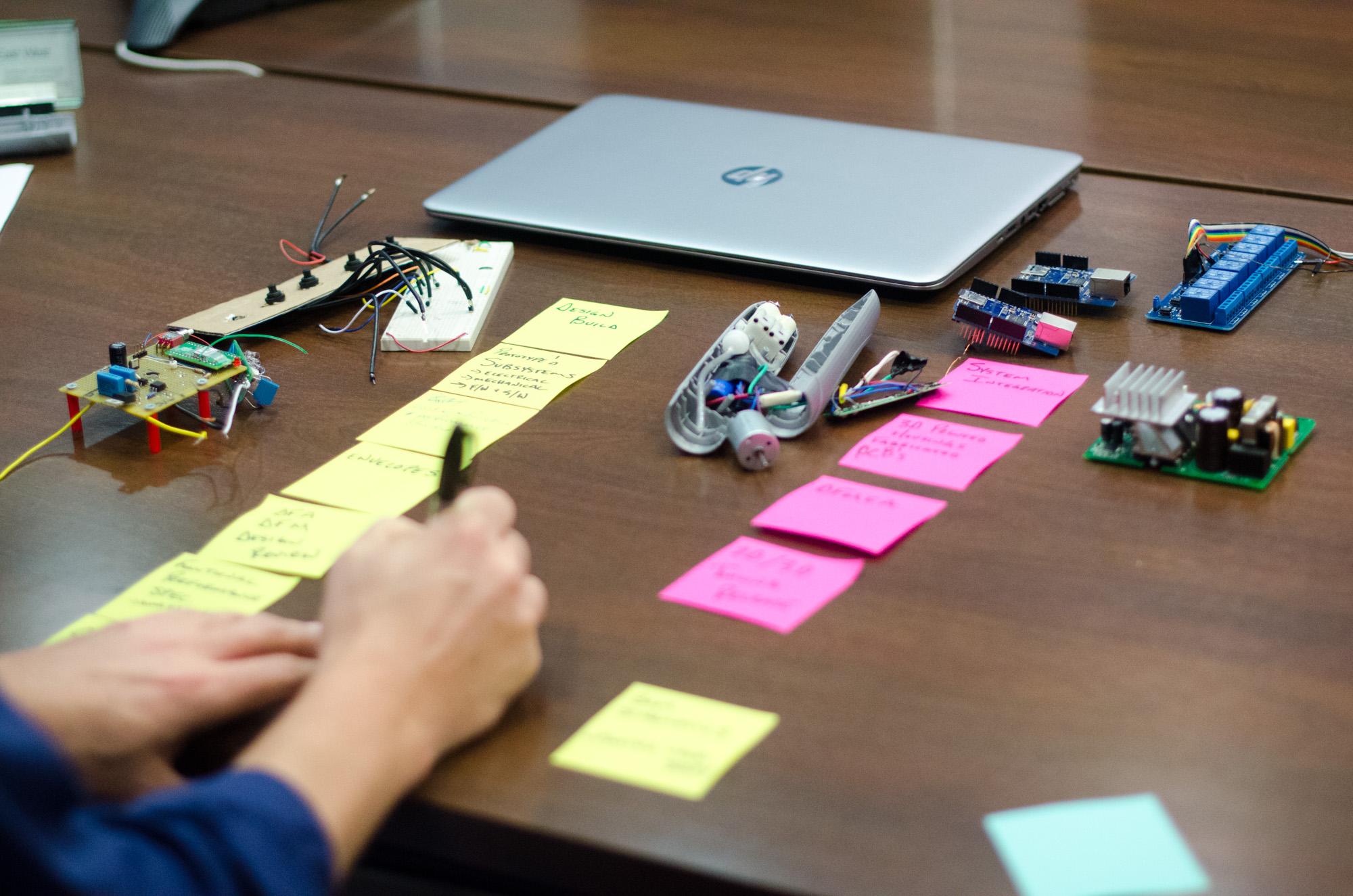
Minimum order quantity
It is essential to know the Minimum Order Quantity (or MOQ), of each clothing manufacturer when searching for one. Many garment factories will not produce your garments without a minimum order amount. The MOQ is dependent on the technical characteristics of your designs and varies from one factory to another. Some factories are able to accept orders up to 100 items. Others require orders over a thousand.
Manufacturers who deal with bulk goods, such as manufacturers, must meet the MOQ requirement. They can keep their profits high and eliminate businesses who are only looking to order small quantities, but not necessarily large orders. This is especially important with custom orders.
FAQ
What is the difference between Production Planning and Scheduling?
Production Planning (PP), or production planning, is the process by which you determine what products are needed at any given time. This is accomplished by forecasting the demand and identifying production resources.
Scheduling refers to the process of allocating specific dates to tasks in order that they can be completed within a specified timeframe.
What is meant by manufacturing industries?
Manufacturing Industries is a group of businesses that produce goods for sale. Consumers are the people who purchase these products. These companies use a variety processes such as distribution, retailing and management to accomplish their purpose. They create goods from raw materials, using machines and various other equipment. This includes all types of manufactured goods, including food items, clothing, building supplies, furniture, toys, electronics, tools, machinery, vehicles, pharmaceuticals, medical devices, chemicals, and many others.
What is the role of a logistics manager
A logistics manager ensures that all goods are delivered on time and without damage. This is accomplished by using the experience and knowledge gained from working with company products. He/she should ensure that sufficient stock is available in order to meet customer demand.
How can efficiency in manufacturing be improved?
First, determine which factors have the greatest impact on production time. We then need to figure out how to improve these variables. If you don’t know where to begin, consider which factors have the largest impact on production times. Once you've identified them, try to find solutions for each of those factors.
What are the 7 Rs of logistics?
The 7R's of Logistics is an acronym for the seven basic principles of logistics management. It was created by the International Association of Business Logisticians and published in 2004 under its "Seven Principles of Logistics Management".
The acronym is composed of the following letters.
-
Responsible - ensure that all actions taken are within legal requirements and are not harmful to others.
-
Reliable - You can have confidence that you will fulfill your promises.
-
Reasonable - make sure you use your resources well and don't waste them.
-
Realistic – consider all aspects of operations, from cost-effectiveness to environmental impact.
-
Respectful - Treat people fairly and equitably
-
Resourceful - look for opportunities to save money and increase productivity.
-
Recognizable: Provide customers with value-added service
What skills do production planners need?
To become a successful production planner, you need to be organized, flexible, and able to multitask. You must also be able to communicate effectively with clients and colleagues.
What are the products of logistics?
Logistics refers to all activities that involve moving goods from A to B.
These include all aspects related to transport such as packaging, loading and transporting, storing, transporting, unloading and warehousing inventory management, customer service. Distribution, returns, recycling are some of the options.
Logisticians ensure that products reach the right destination at the right moment and under safe conditions. They provide information on demand forecasts as well stock levels, production schedules and availability of raw material.
They coordinate with vendors and suppliers, keep track of shipments, monitor quality standards and perform inventory and order replenishment.
Statistics
- (2:04) MTO is a production technique wherein products are customized according to customer specifications, and production only starts after an order is received. (oracle.com)
- Many factories witnessed a 30% increase in output due to the shift to electric motors. (en.wikipedia.org)
- [54][55] These are the top 50 countries by the total value of manufacturing output in US dollars for its noted year according to World Bank.[56] (en.wikipedia.org)
- You can multiply the result by 100 to get the total percent of monthly overhead. (investopedia.com)
- According to a Statista study, U.S. businesses spent $1.63 trillion on logistics in 2019, moving goods from origin to end user through various supply chain network segments. (netsuite.com)
External Links
How To
How to use the Just-In Time Method in Production
Just-in-time is a way to cut costs and increase efficiency in business processes. It's the process of obtaining the right amount and timing of resources when you need them. This means you only pay what you use. Frederick Taylor was the first to coin this term. He developed it while working as a foreman during the early 1900s. He noticed that workers were often paid overtime when they had to work late. He decided that workers would be more productive if they had enough time to complete their work before they started to work.
JIT is about planning ahead. You should have all the necessary resources ready to go so that you don’t waste money. Look at your entire project, from start to end. Make sure you have enough resources in place to deal with any unexpected problems. You'll be prepared to handle any potential problems if you know in advance. This way you won't be spending more on things that aren’t really needed.
There are many types of JIT methods.
-
Demand-driven JIT: You order the parts and materials you need for your project every other day. This will enable you to keep track of how much material is left after you use it. This will let you know how long it will be to produce more.
-
Inventory-based: This allows you to store the materials necessary for your projects in advance. This allows for you to anticipate how much you can sell.
-
Project-driven: This means that you have enough money to pay for your project. You will be able to purchase the right amount of materials if you know what you need.
-
Resource-based: This is the most common form of JIT. Here, you allocate certain resources based on demand. For example, if there is a lot of work coming in, you will have more people assigned to them. You'll have fewer orders if you have fewer.
-
Cost-based: This is the same as resource-based except that you don't care how many people there are but how much each one of them costs.
-
Price-based: This is a variant of cost-based. However, instead of focusing on the individual workers' costs, this looks at the total price of the company.
-
Material-based: This is quite similar to cost-based, but instead of looking at the total cost of the company, you're concerned with how much raw materials you spend on average.
-
Time-based: Another variation of resource-based JIT. Instead of worrying about how much each worker costs, you can focus on how long the project takes.
-
Quality-based JIT: Another variation on resource-based JIT. Instead of thinking about how much each employee costs or how long it takes to manufacture something, you think about how good the quality of your product is.
-
Value-based JIT is the newest form of JIT. In this case, you're not concerned with how well the products perform or whether they meet customer expectations. Instead, your focus is on the value you bring to the market.
-
Stock-based. This method is inventory-based and focuses only on the actual production at any given point. It's useful when you want maximum production and minimal inventory.
-
Just-intime planning (JIT), is a combination JIT/sales chain management. It refers to the process of scheduling the delivery of components as soon as they are ordered. It's important as it reduces leadtimes and increases throughput.