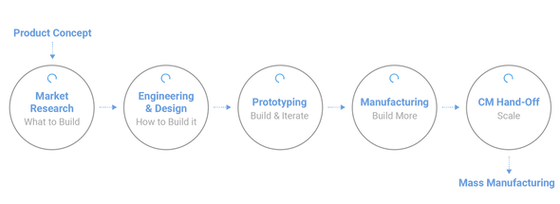
Industrial technology can be described as a broad field. It includes technicians, technologists and other jobs related to productivity. Technologists and technicians can be found working in many different fields. However, their salaries may vary significantly. The salary ranges of industrial technologists can vary depending upon where they work. The type of employer an industrial technologist works for can also impact their income.
Technicians and technologists working in industrial engineering are in high demand. Many companies employ them, including government agencies as well as pharmaceutical companies. They often use computer-aided design software to design solutions for industry problems. These professionals need to have the right education, experience, work ethic, and skills.
Salary for an Industrial Engineering Technologist varies depending on the location, skills level and years of experience. Higher-paying jobs will be more lucrative than those in entry-level positions. An average annual salary of $53,080 for a bachelor's-level job is $53,080. Entry-level jobs can pay between $36,550 and $45,040. You can earn as much as $86,900 annually depending on your level of experience.
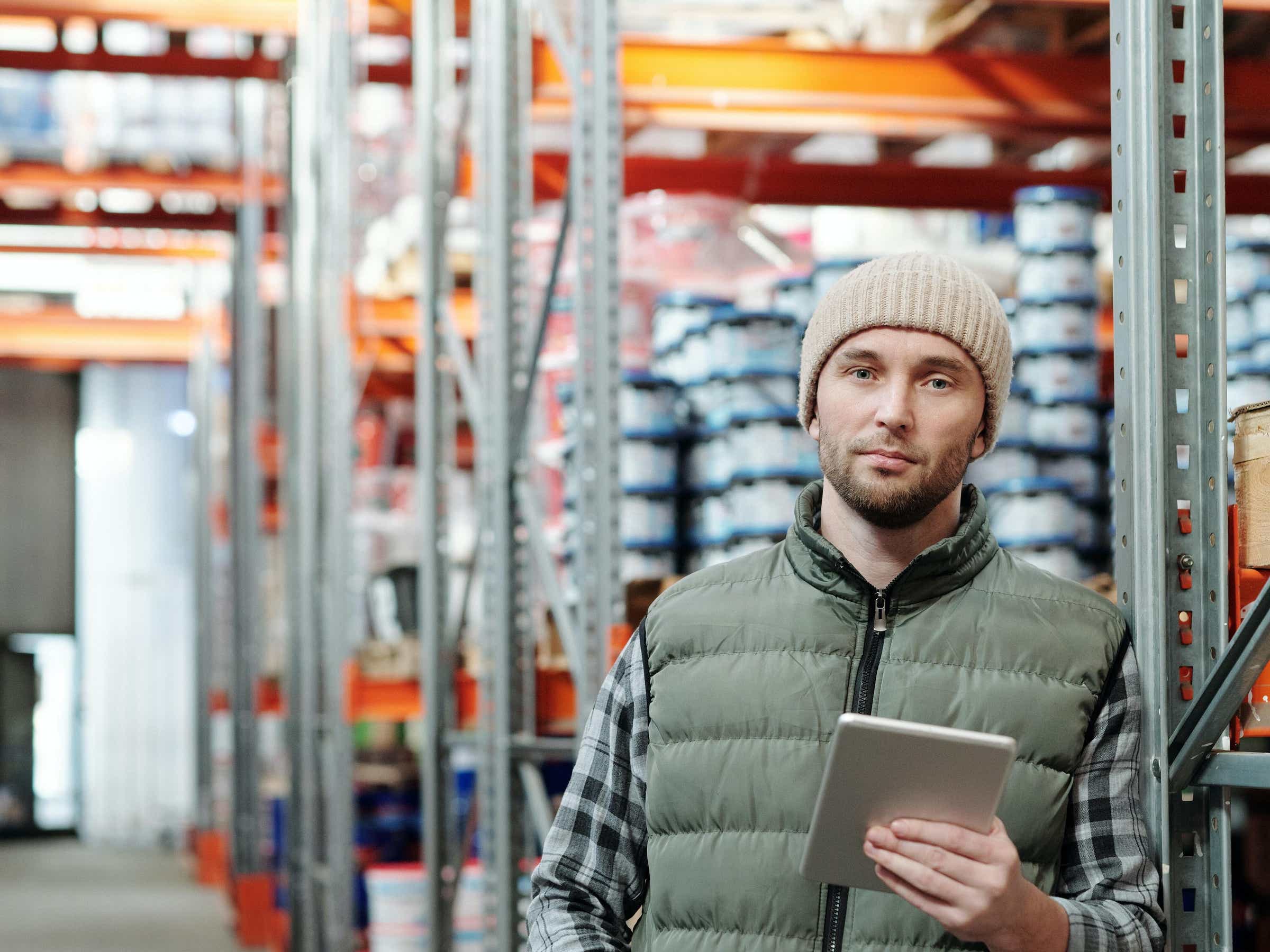
The cost of living is a major factor in determining the salary of an Industrial Engineering Technologist. It is possible to live in very affordable areas. This can be a major advantage. However, some cities have a higher cost of living than others. Regardless, it is still possible to get a good salary in the field, so long as you work hard.
Industrial engineers are often eligible for bonuses. Although a bonus doesn't increase your salary, it can add significant funds to your income. A typical bonus for an Industrial Engineer is $825. This is approximately 2% of your total salary. SalaryExpert allows you to find out the potential bonuses that are available.
The right skills and knowledge are required to work as an industrial technologist or technician in a variety industries. Most popular positions as an industrial technician or technologist are in the manufacturing, health care, and utilities sectors. These industries have a high degree of job satisfaction, which is why there is such a high demand.
The demand for this career is expected to rise over the next decade. Job openings are estimated to increase by up to 2,100 jobs per year. These openings will be mainly due to people leaving work. According to projections, the number of Industrial Engineering Technologists (Technicians) will grow by 3 percentage between 2021-2031.
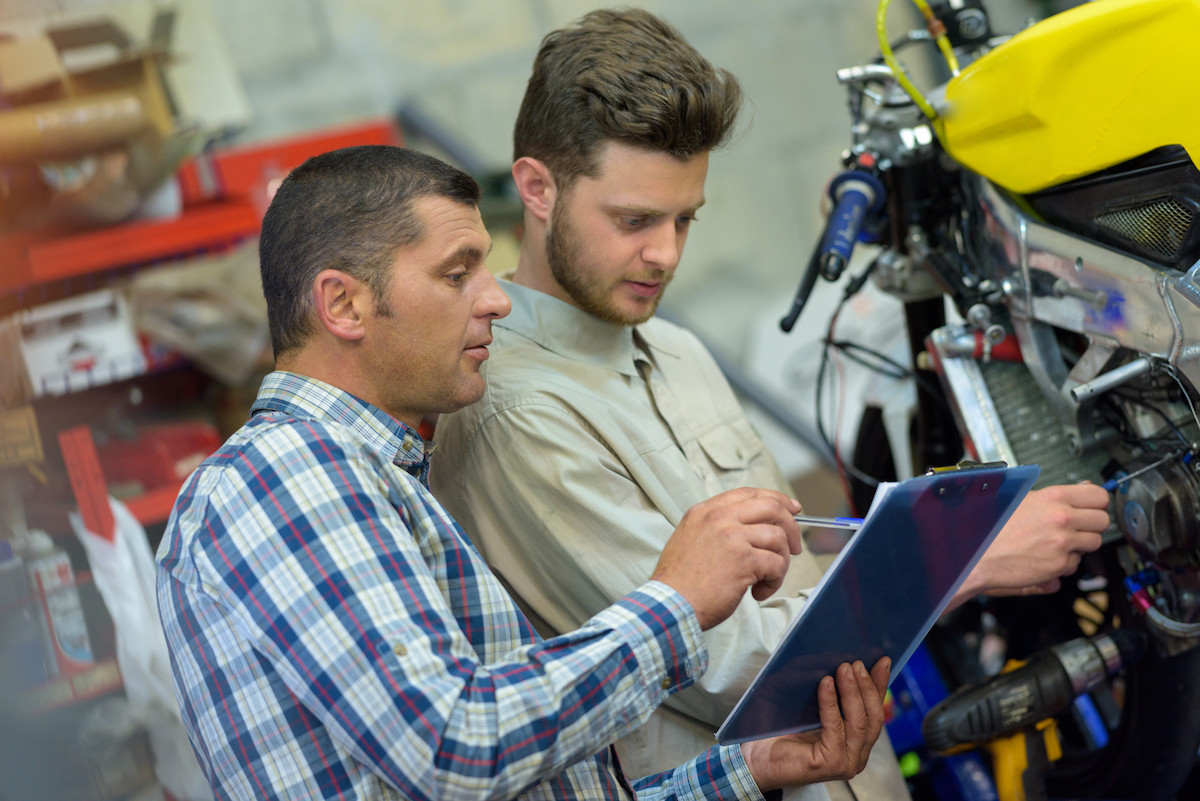
The average Industrial Engineering Technician salary is $75648. This is $2.234 more than that of the national average. Those working in the Chicago area can expect to make $77,882 a year.
A large proportion of industrial technologist and technician jobs have been filled by government agencies, manufacturing businesses, and pharmaceutical corporations. The average hourly wage for an industrial engineer technologist or technician in the United States is around $26.
FAQ
What is the responsibility of a logistics manager?
A logistics manager makes sure that all goods are delivered on-time and in good condition. This is achieved by using their knowledge and experience with the products of the company. He/she should also ensure enough stock is available to meet demand.
What do we need to know about Manufacturing Processes in order to learn more about Logistics?
No. It doesn't matter if you don't know anything about manufacturing before you learn about logistics. It is important to know about the manufacturing processes in order to understand how logistics works.
Is automation important for manufacturing?
Not only is automation important for manufacturers, but it's also vital for service providers. It allows them to offer services faster and more efficiently. In addition, it helps them reduce costs by reducing human errors and improving productivity.
What are the 4 types manufacturing?
Manufacturing refers to the transformation of raw materials into useful products by using machines and processes. Manufacturing can include many activities such as designing and building, testing, packaging shipping, selling, servicing, and other related activities.
What are the goods of logistics?
Logistics are the activities involved in moving goods from point A to point B.
They cover all aspects of transportation, such as packing, loading, transporting and unloading.
Logisticians make sure that the right product arrives at the right place at the correct time and in safe conditions. They provide information on demand forecasts as well stock levels, production schedules and availability of raw material.
They can also track shipments in transit and monitor quality standards.
What is the role of a production manager?
Production planners ensure all aspects of the project are delivered within time and budget. A production planner ensures that the service and product meet the client's expectations.
Why automate your factory?
Automation has become increasingly important in modern warehousing. E-commerce has brought increased demand for more efficient and quicker delivery times.
Warehouses should be able adapt quickly to new needs. Technology is essential for warehouses to be able to adapt quickly to changing needs. Automation warehouses can bring many benefits. Here are some benefits of investing in automation
-
Increases throughput/productivity
-
Reduces errors
-
Improves accuracy
-
Safety increases
-
Eliminates bottlenecks
-
Allows companies scale more easily
-
Increases efficiency of workers
-
It gives visibility to everything that happens inside the warehouse
-
Enhances customer experience
-
Improves employee satisfaction
-
Reducing downtime and increasing uptime
-
Quality products delivered on time
-
Human error can be eliminated
-
This helps to ensure compliance with regulations
Statistics
- Many factories witnessed a 30% increase in output due to the shift to electric motors. (en.wikipedia.org)
- According to the United Nations Industrial Development Organization (UNIDO), China is the top manufacturer worldwide by 2019 output, producing 28.7% of the total global manufacturing output, followed by the United States, Japan, Germany, and India.[52][53] (en.wikipedia.org)
- In the United States, for example, manufacturing makes up 15% of the economic output. (twi-global.com)
- (2:04) MTO is a production technique wherein products are customized according to customer specifications, and production only starts after an order is received. (oracle.com)
- Job #1 is delivering the ordered product according to specifications: color, size, brand, and quantity. (netsuite.com)
External Links
How To
Six Sigma in Manufacturing:
Six Sigma refers to "the application and control of statistical processes (SPC) techniques in order to achieve continuous improvement." Motorola's Quality Improvement Department in Tokyo, Japan developed Six Sigma in 1986. Six Sigma's basic concept is to improve quality and eliminate defects through standardization. Since there are no perfect products, or services, this approach has been adopted by many companies over the years. The main goal of Six Sigma is to reduce variation from the mean value of production. If you take a sample and compare it with the average, you will be able to determine how much of the production process is different from the norm. If the deviation is excessive, it's likely that something needs to be fixed.
Understanding the dynamics of variability within your business is the first step in Six Sigma. Once you have this understanding, you will need to identify sources and causes of variation. You'll also want to determine whether these variations are random or systematic. Random variations are caused when people make mistakes. While systematic variations are caused outside of the process, they can occur. If you make widgets and some of them end up on the assembly line, then those are considered random variations. But if you notice that every widget you make falls apart at the exact same place each time, this would indicate that there is a problem.
Once you've identified where the problems lie, you'll want to design solutions to eliminate those problems. You might need to change the way you work or completely redesign the process. To verify that the changes have worked, you need to test them again. If they fail, you can go back to the drawing board to come up with a different plan.