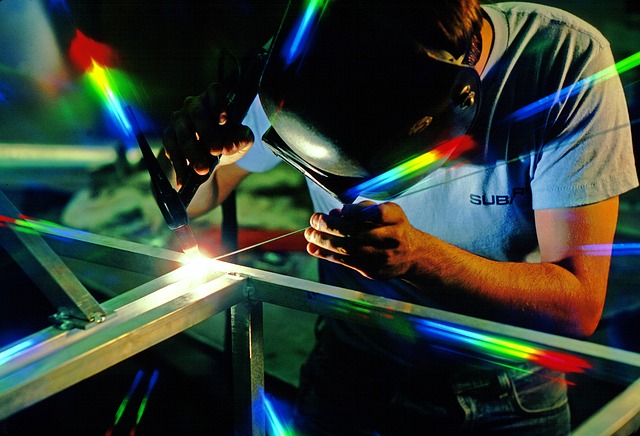
You can choose to be new or have years of work experience in logistics. There are many career opportunities available. These careers offer many opportunities to earn competitive salaries. These jobs also give you the opportunity to work across many industries, including banking, pharmaceutical, manufacturing, shipping, and transport.
There are many skills required to work in logistics. These include communication, problem solving, collaboration, and critical thinking. These skills are critical for success in the logistics industry. You might be looking for the best way to transport a shipment to one destination, or working to ensure that all goods clear customs. No matter what position you are in logistics, you will be responsible to coordinate the movement of goods, supplies and equipment. You will also need to work to coordinate and streamline operations.
A bachelor's program in logistics and supply-chain management can prepare you for any career. You can even earn professional certifications to demonstrate your skills. There are many continuing education opportunities available for logistics professionals. You can learn about the logistics industry through online courses or in-house training.
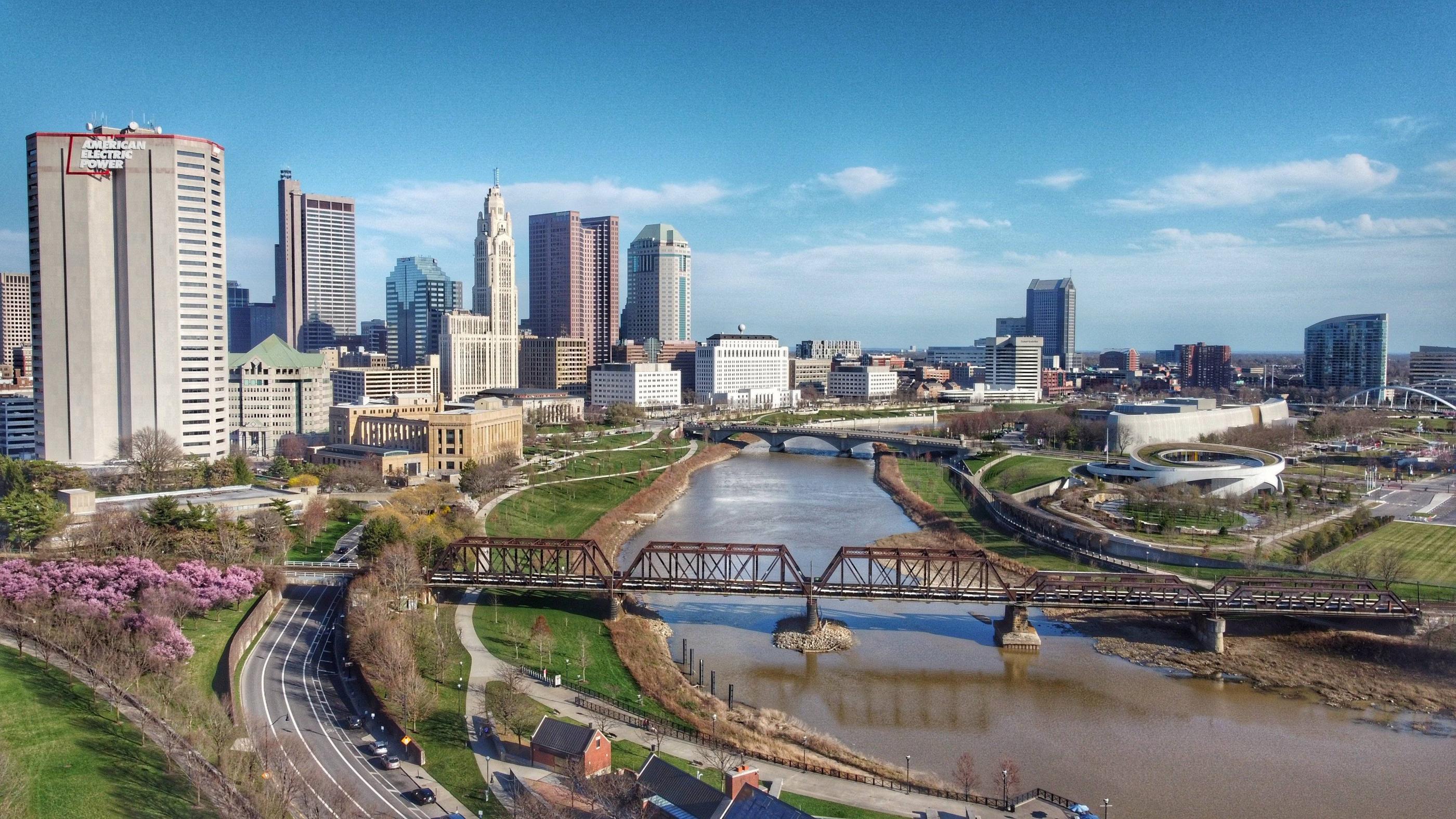
The Logistics & Transportation Association of North America is a professional organization that provides networking opportunities, education events, and a job board. These organizations are committed to improving logistics. Members can also obtain certifications through the association.
Other organizations include the International Society of Logistics, which promotes education and technology to help improve the industry. Logistics professionals can also apply for fellowships at the American College of Healthcare Executives.
The International Warehouse Logistics Association (IWLLA) supports warehouse logistics companies. The association offers various career development opportunities such as education events and a job board. You can also find industry news updates and conventions at the association.
Many companies prefer to hire current employees for their positions. However, a degree that focuses on logistics can lead to managerial positions. A bachelor's degree in logistics will equip you with the knowledge and skills to manage the complicated supply chain, as well the laws and rules that govern transportation. You can also study a master's in logistics to increase your professional skills and advancement.
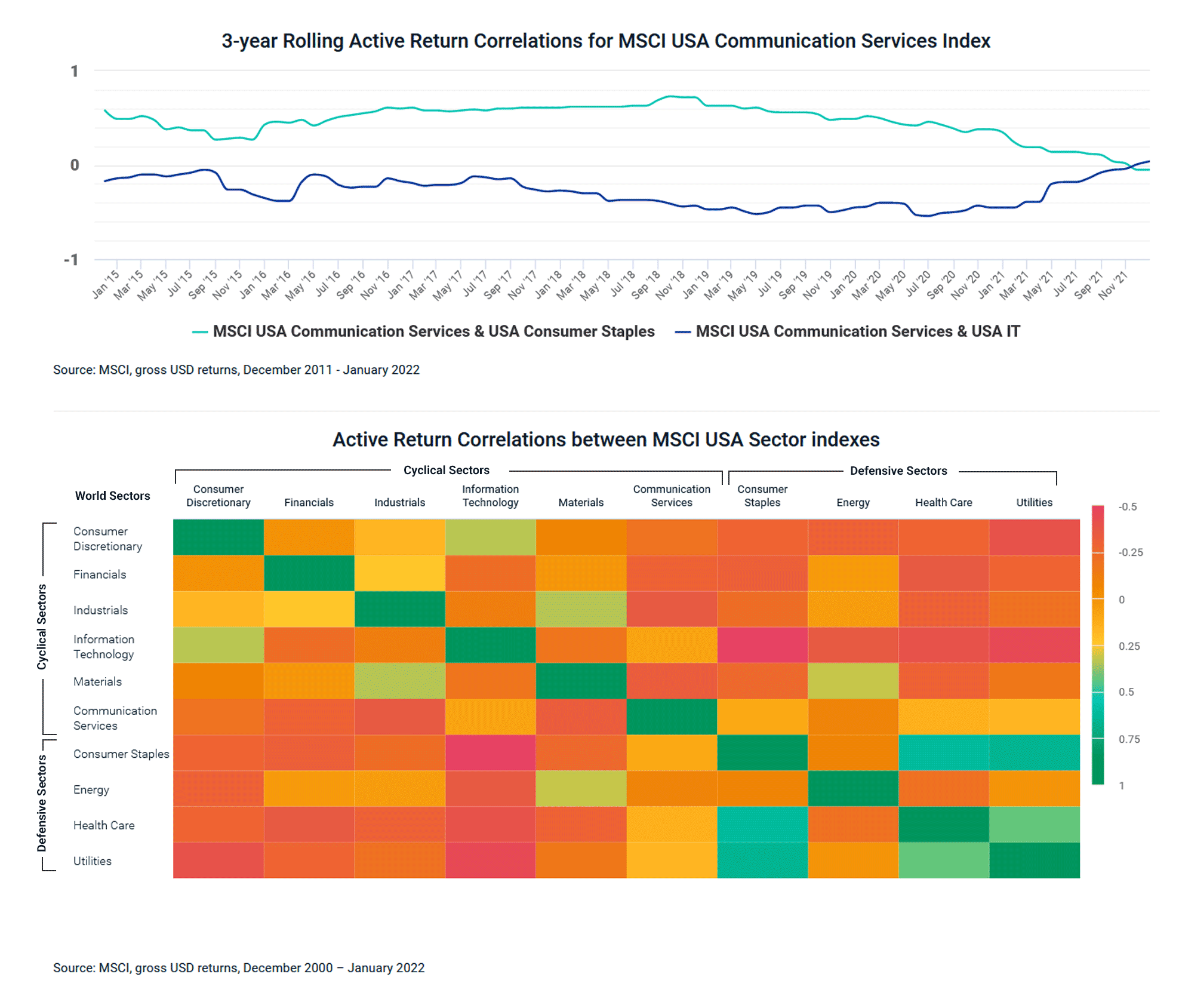
The Federal Government is one the most well-paid employers in logistics. Logistics workers in the federal government earn a median salary of $85,000. California, Michigan, and District of Columbia all have the highest average salaries.
Logistics careers require critical thinking, collaboration skills, and excellent communication. They can be challenging, but also very rewarding. A career in logistics is also a great way to network with industry leaders and experts. There are many positions available, but you will find the best ones in California and New Jersey. The BLS predicts that there will a 5% rise in logistics jobs by 2028.
FAQ
How can manufacturing reduce production bottlenecks?
Avoiding production bottlenecks is as simple as keeping all processes running smoothly, from the time an order is received until the product ships.
This includes planning to meet capacity requirements and quality control.
Continuous improvement techniques like Six Sigma are the best way to achieve this.
Six Sigma is a management system used to improve quality and reduce waste in every aspect of your organization.
It seeks to eliminate variation and create consistency in your work.
What's the difference between Production Planning & Scheduling?
Production Planning (PP) refers to the process of determining how much production is needed at any given moment. This can be done by forecasting demand and identifying production capabilities.
Scheduling refers the process by which tasks are assigned dates so that they can all be completed within the given timeframe.
Is automation necessary in manufacturing?
Not only is automation important for manufacturers, but it's also vital for service providers. Automation allows them to deliver services quicker and more efficiently. It reduces human errors and improves productivity, which in turn helps them lower their costs.
Statistics
- (2:04) MTO is a production technique wherein products are customized according to customer specifications, and production only starts after an order is received. (oracle.com)
- In 2021, an estimated 12.1 million Americans work in the manufacturing sector.6 (investopedia.com)
- It's estimated that 10.8% of the U.S. GDP in 2020 was contributed to manufacturing. (investopedia.com)
- According to a Statista study, U.S. businesses spent $1.63 trillion on logistics in 2019, moving goods from origin to end user through various supply chain network segments. (netsuite.com)
- You can multiply the result by 100 to get the total percent of monthly overhead. (investopedia.com)
External Links
How To
How to use lean manufacturing in the production of goods
Lean manufacturing is an approach to management that aims for efficiency and waste reduction. It was developed by Taiichi Okono in Japan, during the 1970s & 1980s. TPS founder Kanji Takoda awarded him the Toyota Production System Award (TPS). Michael L. Watkins published the original book on lean manufacturing, "The Machine That Changed the World," in 1990.
Lean manufacturing refers to a set of principles that improve the quality, speed and costs of products and services. It emphasizes eliminating waste and defects throughout the value stream. Lean manufacturing can be described as just-in–time (JIT), total productive maintenance, zero defect (TPM), or even 5S. Lean manufacturing seeks to eliminate non-value added activities, such as inspection, work, waiting, and rework.
In addition to improving product quality and reducing costs, lean manufacturing helps companies achieve their goals faster and reduces employee turnover. Lean manufacturing is a great way to manage the entire value chain including customers, suppliers, distributors and retailers as well as employees. Lean manufacturing can be found in many industries. For example, Toyota's philosophy underpins its success in automobiles, electronics, appliances, healthcare, chemical engineering, aerospace, paper, food, etc.
Lean manufacturing is based on five principles:
-
Define value - Find out what your business contributes to society, and what makes it different from other competitors.
-
Reduce waste - Get rid of any activity that does not add value to the supply chain.
-
Create Flow: Ensure that the work process flows without interruptions.
-
Standardize and Simplify – Make processes as consistent, repeatable, and as simple as possible.
-
Build Relationships- Develop personal relationships with both internal as well as external stakeholders.
Lean manufacturing, although not new, has seen renewed interest in the economic sector since 2008. Many businesses are now using lean manufacturing to improve their competitiveness. Economists think that lean manufacturing is a crucial factor in economic recovery.
Lean manufacturing is becoming a popular practice in automotive. It has many advantages. These include better customer satisfaction and lower inventory levels. They also result in lower operating costs.
The principles of lean manufacturing can be applied in almost any area of an organization. This is because it ensures efficiency and effectiveness in all stages of the value chain.
There are three types principally of lean manufacturing:
-
Just-in-Time Manufacturing: Also known as "pull systems", this type of lean manufacturing uses just-in-time manufacturing (JIT). JIT means that components are assembled at the time of use and not manufactured in advance. This strategy aims to decrease lead times, increase availability of parts and reduce inventory.
-
Zero Defects Manufacturing, (ZDM): ZDM is focused on ensuring that no defective products leave the manufacturing facility. Repairing a part that is damaged during assembly should be done, not scrapping. This also applies to finished products that need minor repairs before being shipped.
-
Continuous Improvement: Continuous Improvement aims to improve efficiency by continually identifying problems and making adjustments to eliminate or minimize waste. Continuous improvement involves continuous improvement of processes and people as well as tools.