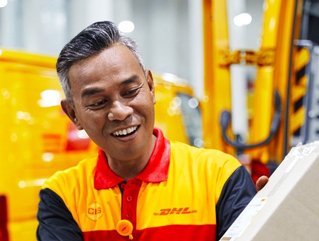
You can use your creativity to improve the world. Whether you're designing bridges, medical equipment or processes for cleaning up toxic spills, your work will make a difference to the lives of many people.
It's important to choose a course that suits your interests and abilities. Kingston University offers undergraduate degrees in chemical, civil and electrical engineering, among other engineering disciplines.
A bachelor’s degree in Engineering is the first step towards becoming a Professional Engineer. It includes math, sciences and humanities coursework that can be applied in a wide range of career options.
Some engineers obtain a master's and doctorate to specialize in one area. These can be helpful for expanding your career options and enhancing your job prospects.
You can also take an industry-specific engineering course, such as mining or oil and gas. These courses teach how to explore and evaluate mineral resources underground, as well as assess the availability or metals, petroleum or other natural materials.
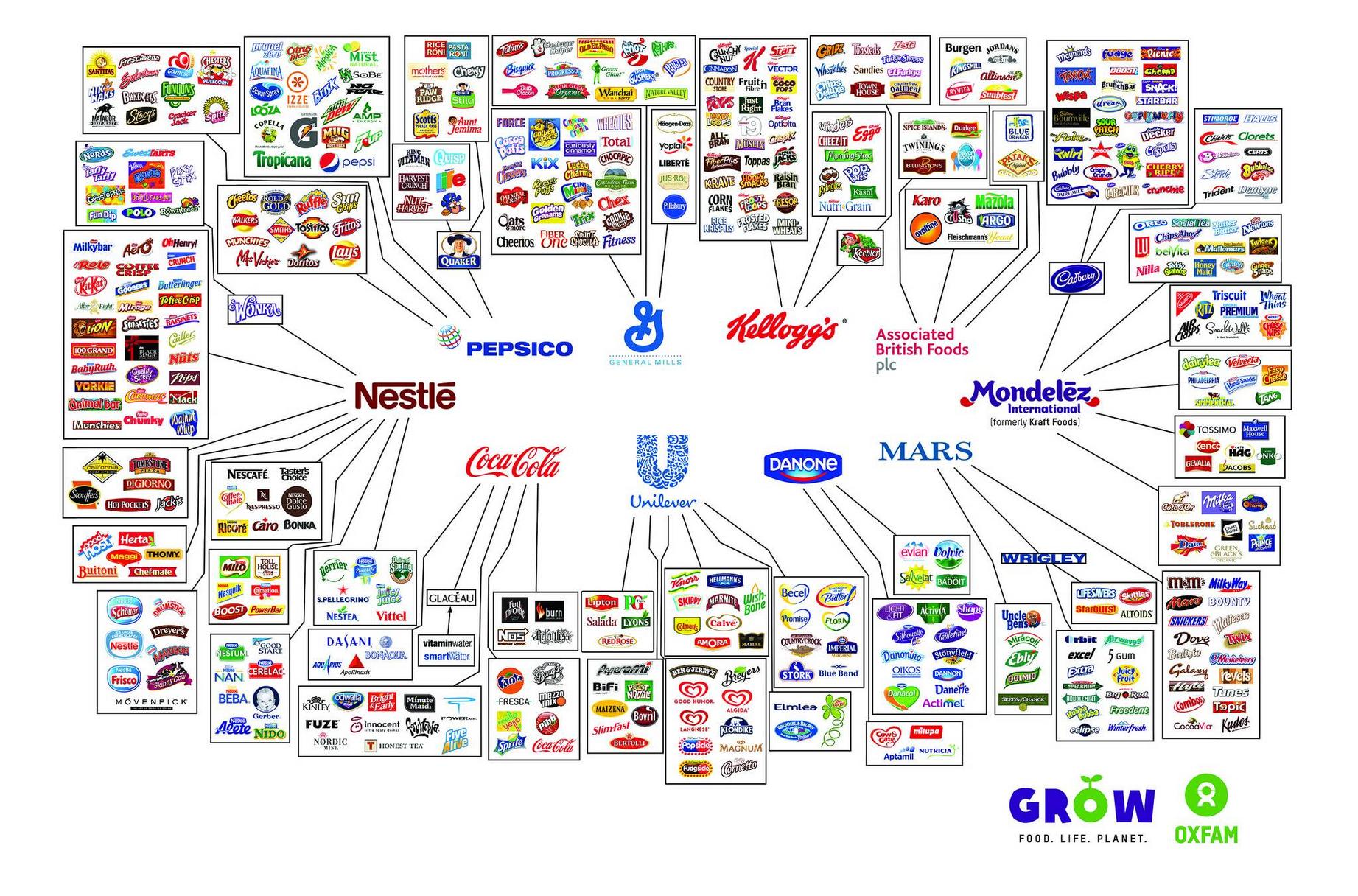
Manufacturing is the conversion of raw materials to finished products which are then sold in stores and markets. You will learn about the basics of production, including how to plan and implement production lines.
You'll also need to have the ability to handle multiple responsibilities and work under pressure. You will also have to manage time and prioritize so that you can finish your tasks within a set time frame.
You'll want to select a college with an accredited engineering program if you plan on pursuing a degree in the field. This means that the institution has met the requirements set by ABET. ABET is the organization responsible for accrediting engineering education in the United States.
You'll have to go to college full-time and for four semesters, earning a total of at least 60 credits. Then, you must pass a test and gain work experience in your chosen engineering area.
The average pay for a study engineer is $94,463 per year, with an entry-level salary of about $30,000 and a senior research engineer's salary of about $123,325 annually.
You'll be tasked with identifying technologies that will help businesses produce products more efficiently or at a lower cost, as well as developing designs and testing prototyping for ease-of-use, longevity, and functionality. The work may involve collaborating with marketing and product design to refine or develop existing products.
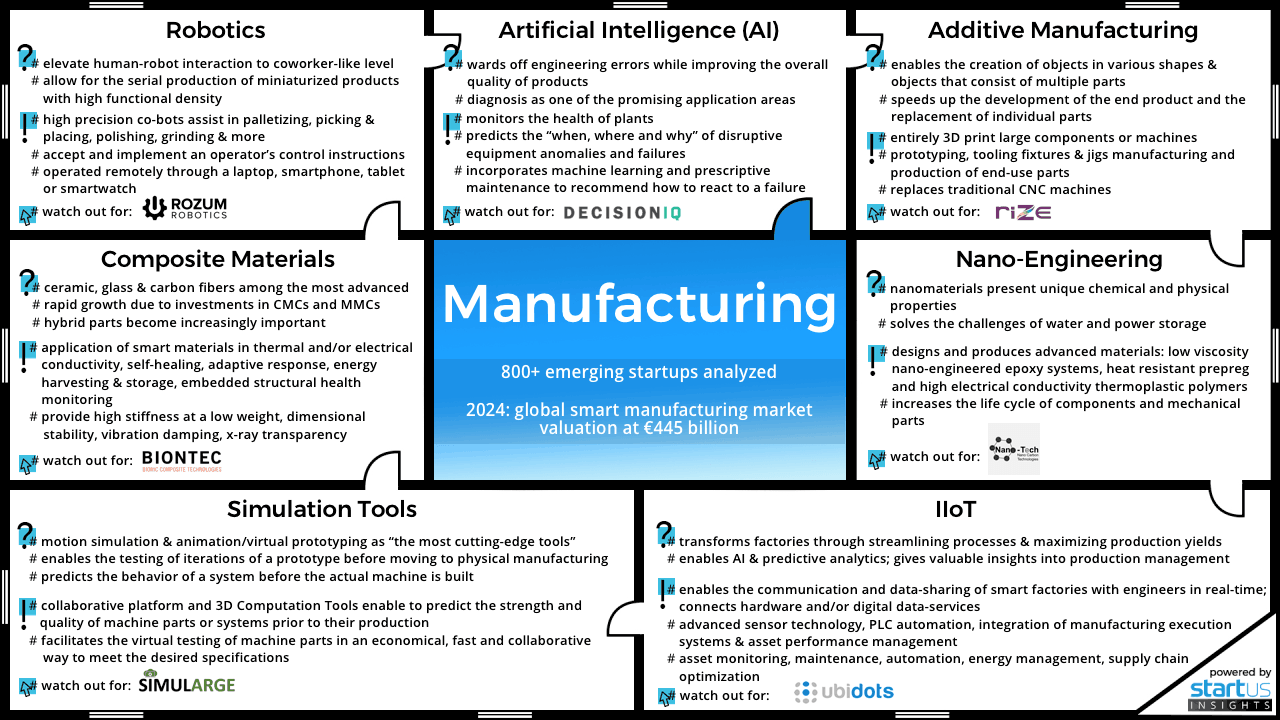
You'll spend a lot of time on the job and in the laboratory as a study engineering student. You will need to be able perform complex data analyses and have a solid grasp of the science behind engineering projects.
You must be passionate about science and enjoy solving problems. You should have a good background in physics as well as math and chemistry.
It is best to enroll in an accredited engineering program, and then to take the FE test after graduating. Then, you'll need to get some engineering work experience before taking the PE exam and getting licensed.
FAQ
How can excess manufacturing production be reduced?
It is essential to find better ways to manage inventory to reduce overproduction. This would decrease the time that is spent on inefficient activities like purchasing, storing, or maintaining excess stock. This will allow us to free up resources for more productive tasks.
You can do this by adopting a Kanban method. A Kanban board can be used to monitor work progress. A Kanban system allows work items to move through several states before reaching their final destination. Each state has a different priority level.
When work is completed, it can be transferred to the next stage. A task that is still in the initial stages of a process will be considered complete until it moves on to the next stage.
This allows work to move forward and ensures that no work is missed. A Kanban board allows managers to monitor how much work is being completed at any given moment. This allows them the ability to adjust their workflow using real-time data.
Lean manufacturing is another way to manage inventory levels. Lean manufacturing seeks to eliminate waste from every step of the production cycle. Any product that isn't adding value can be considered waste. There are several types of waste that you might encounter:
-
Overproduction
-
Inventory
-
Unnecessary packaging
-
Exceed materials
These ideas can help manufacturers improve efficiency and reduce costs.
What does the term manufacturing industries mean?
Manufacturing Industries are those businesses that make products for sale. Consumers are people who purchase these goods. These companies use a variety processes such as distribution, retailing and management to accomplish their purpose. These companies produce goods using raw materials and other equipment. This includes all types and varieties of manufactured goods, such as food items, clothings, building supplies, furnitures, toys, electronics tools, machinery vehicles, pharmaceuticals medical devices, chemicals, among others.
What is the role of a logistics manager
A logistics manager makes sure that all goods are delivered on-time and in good condition. This is achieved by using their knowledge and experience with the products of the company. He/she also needs to ensure adequate stock to meet demand.
What type of jobs is there in logistics
There are different kinds of jobs available in logistics. Here are some examples:
-
Warehouse workers - They load and unload trucks and pallets.
-
Transportation drivers – They drive trucks or trailers to transport goods and perform pick-ups.
-
Freight handlers - They sort and pack freight in warehouses.
-
Inventory managers - These are responsible for overseeing the stock of goods in warehouses.
-
Sales representatives: They sell products to customers.
-
Logistics coordinators - They plan and organize logistics operations.
-
Purchasing agents - They buy goods and services that are necessary for company operations.
-
Customer service representatives – They answer emails and phone calls from customers.
-
Shipping clerks – They process shipping orders, and issue bills.
-
Order fillers – They fill orders based upon what was ordered and shipped.
-
Quality control inspectors - They check incoming and outgoing products for defects.
-
Others - There are many types of jobs in logistics such as transport supervisors and cargo specialists.
What does it take for a logistics enterprise to succeed?
To be a successful businessman in logistics, you will need many skills and knowledge. To communicate effectively with clients and suppliers, you must be able to communicate well. It is important to be able to analyse data and draw conclusions. You must be able manage stress and pressure under pressure. You need to be innovative and creative to come up with new ways to increase efficiency. You must be a strong leader to motivate others and direct them to achieve organizational goals.
You should also be organized and efficient to meet tight deadlines.
What is manufacturing and logistics?
Manufacturing is the process of creating goods from raw materials by using machines and processes. Logistics encompasses the management of all aspects associated with supply chain activities such as procurement, production planning, distribution and inventory control. It also includes customer service. Logistics and manufacturing are often referred to as one thing. It encompasses both the creation of products and their delivery to customers.
What are the 7 Rs of logistics?
The acronym 7R's of Logistic is an acronym that stands for seven fundamental principles of logistics management. It was developed by International Association of Business Logisticians (IABL), and published as part of their "Seven Principles of Logistics Management Series" in 2004.
The acronym is composed of the following letters.
-
Responsible – ensure that all actions are legal and don't cause harm to anyone else.
-
Reliable - have confidence in the ability to deliver on commitments made.
-
Reasonable - use resources efficiently and don't waste them.
-
Realistic - Consider all aspects of operations, including environmental impact and cost effectiveness.
-
Respectful – Treat others fairly and equitably.
-
Resourceful - look for opportunities to save money and increase productivity.
-
Recognizable - Provide value-added services to customers
Statistics
- In the United States, for example, manufacturing makes up 15% of the economic output. (twi-global.com)
- It's estimated that 10.8% of the U.S. GDP in 2020 was contributed to manufacturing. (investopedia.com)
- Many factories witnessed a 30% increase in output due to the shift to electric motors. (en.wikipedia.org)
- According to the United Nations Industrial Development Organization (UNIDO), China is the top manufacturer worldwide by 2019 output, producing 28.7% of the total global manufacturing output, followed by the United States, Japan, Germany, and India.[52][53] (en.wikipedia.org)
- According to a Statista study, U.S. businesses spent $1.63 trillion on logistics in 2019, moving goods from origin to end user through various supply chain network segments. (netsuite.com)
External Links
How To
How to Use the Just-In-Time Method in Production
Just-intime (JIT), which is a method to minimize costs and maximize efficiency in business process, is one way. It allows you to get the right amount resources at the right time. This means you only pay what you use. Frederick Taylor developed the concept while working as foreman in early 1900s. He saw how overtime was paid to workers for work that was delayed. He decided that workers would be more productive if they had enough time to complete their work before they started to work.
JIT is a way to plan ahead and make sure you don't waste any money. Look at your entire project, from start to end. Make sure you have enough resources in place to deal with any unexpected problems. If you anticipate that there might be problems, you'll have enough people and equipment to fix them. This way, you won't end up paying extra money for things that weren't really necessary.
There are many types of JIT methods.
-
Demand-driven: This is a type of JIT where you order the parts/materials needed for your project regularly. This will enable you to keep track of how much material is left after you use it. This will let you know how long it will be to produce more.
-
Inventory-based: This is a type where you stock the materials required for your projects in advance. This allows you to forecast how much you will sell.
-
Project-driven: This method allows you to set aside enough funds for your project. Knowing how much money you have available will help you purchase the correct amount of materials.
-
Resource-based: This is the most common form of JIT. This is where you assign resources based upon demand. You might assign more people to help with orders if there are many. If you don’t have many orders you will assign less people to the work.
-
Cost-based : This is similar in concept to resource-based. But here, you aren't concerned about how many people your company has but how much each individual costs.
-
Price-based: This is a variant of cost-based. However, instead of focusing on the individual workers' costs, this looks at the total price of the company.
-
Material-based: This is quite similar to cost-based, but instead of looking at the total cost of the company, you're concerned with how much raw materials you spend on average.
-
Time-based JIT: A variation on resource-based JIT. Instead of worrying about how much each worker costs, you can focus on how long the project takes.
-
Quality-based JIT - This is another form of resource-based JIT. Instead of looking at the labor costs and time it takes to make a product, think about its quality.
-
Value-based: This is one of the newest forms of JIT. In this case, you're not concerned with how well the products perform or whether they meet customer expectations. Instead, you are focused on adding value to the marketplace.
-
Stock-based: This inventory-based approach focuses on how many items are being produced at any one time. It is used when production goals are met while inventory is kept to a minimum.
-
Just-in-time planning (JIT): This is a combination JIT and supply-chain management. It is the process that schedules the delivery of components within a short time of their order. It is essential because it reduces lead-times and increases throughput.