
A cost estimate is required for almost everything a company does. This task is performed by cost estimators. They help companies determine the costs of manufacturing and developing new products and services. They are also required to evaluate the cost of building a new structure. This includes cost analysis of labor and materials.
Most cost estimators are employed by construction companies. They should have a solid understanding of construction methods and processes. They also need to be familiar with computer-aided design (CAD) software. This software can improve design and manufacturing efficiency. Also, cost estimators must be able to access data from databases. They can also use other types of software, such as Microsoft Excel.
In order to provide accurate cost estimates, cost estimators often collaborate with other professionals. They evaluate the project blueprints, site conditions, and other materials to determine the costs of each component. They may also work closely with engineers to determine gauges or machining requirements.
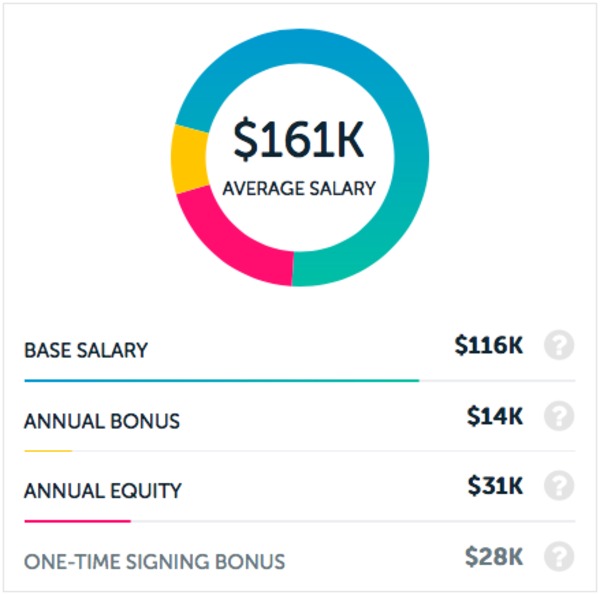
Cost estimators have to be detail-oriented and assertive. They must be capable of interpreting difficult information. They must also have the ability to clearly and convincingly present findings. In addition, they must be able to work with professionals and clients.
Cost estimators are usually assigned to the cost or engineering department of a company. They should have strong math and science backgrounds. They should also be comfortable with commercial and CAD software. They might also need to complete a certification course. Certified Cost Estimator/Analysts (CCEA), Professional Estimator/Analysts, and Certified Professional Estimators are just a few of the certifications available.
Cost estimators may be skilled in certain services or industries. Some people specialize in building or construction costs. Others focus on software costs. Cost estimators could also be employed in other areas like automotive repair and management, building construction, or specialty trade contractors.
These people communicate with engineers, clients, or suppliers. They are also well-versed in industry terminology. They have extensive knowledge before they can prepare cost estimates. In addition to preparing cost estimates, many individuals in this occupation conduct studies, study the effects of different processes on costs, and find ways to reduce costs.
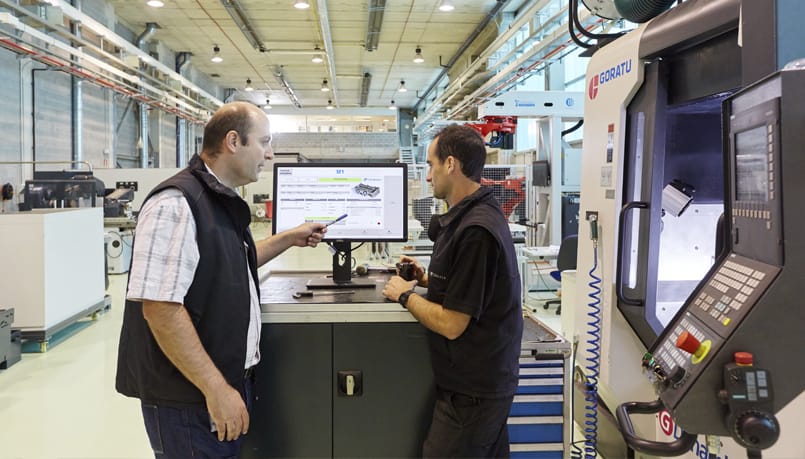
A bachelor's degree may be required depending on the industry. They may also need to complete an internship. They may also be eligible for cooperative education programs. A degree in building construction, or construction management is also an advantage for construction companies.
Cost estimators work in construction firms and other manufacturing companies. They provide accurate estimates to companies that enable them to make profitable bids. They can also analyze data regarding the supply chain, and other factors that influence costs. They can also be cost estimators for government programs. They may also be required to redesign existing products.
Cost estimators must have a strong understanding of computer-aided design (CAD) software. They can also be trained in the use of automatic cost estimation software.
FAQ
Is it possible to automate certain parts of manufacturing
Yes! Since ancient times, automation has been in existence. The Egyptians created the wheel thousands years ago. We now use robots to help us with assembly lines.
Actually, robotics can be used in manufacturing for many purposes. These include:
-
Automated assembly line robots
-
Robot welding
-
Robot painting
-
Robotics inspection
-
Robots that produce products
Manufacturing could also benefit from automation in other ways. For instance, 3D printing allows us make custom products and not have to wait for months or even weeks to get them made.
What does "warehouse" mean?
Warehouses and storage facilities are where goods are kept before being sold. It can be indoors or out. It may also be an indoor space or an outdoor area.
What is the role and responsibility of a Production Planner?
Production planners make sure that every aspect of the project is delivered on-time, within budget, and within schedule. They also ensure the quality of the product and service meets the client's requirements.
What kind of jobs are there in logistics?
Logistics can offer many different jobs. Here are some:
-
Warehouse workers – They load and unload pallets and trucks.
-
Transportation drivers – They drive trucks or trailers to transport goods and perform pick-ups.
-
Freight handlers are people who sort and pack freight into warehouses.
-
Inventory managers – They manage the inventory in warehouses.
-
Sales representatives - They sell products.
-
Logistics coordinators - They plan and organize logistics operations.
-
Purchasing agents – They buy goods or services necessary to run a company.
-
Customer service representatives are available to answer customer calls and emails.
-
Shippers clerks - They process shipping order and issue bills.
-
Order fillers are people who fill orders based only on what was ordered.
-
Quality control inspectors – They inspect incoming and outgoing products to ensure that there are no defects.
-
Others - There are many types of jobs in logistics such as transport supervisors and cargo specialists.
What does the term manufacturing industries mean?
Manufacturing Industries are companies that manufacture products. Consumers are those who purchase these products. To accomplish this goal, these companies employ a range of processes including distribution, sales, management, and production. They manufacture goods from raw materials using machines and other equipment. This includes all types of manufactured goods, including food items, clothing, building supplies, furniture, toys, electronics, tools, machinery, vehicles, pharmaceuticals, medical devices, chemicals, and many others.
What is the responsibility of a logistics manager?
Logistics managers ensure that goods arrive on time and are unharmed. This is done through his/her expertise and knowledge about the company's product range. He/she should also ensure enough stock is available to meet demand.
What are my options for learning more about manufacturing
The best way to learn about manufacturing is through hands-on experience. You can also read educational videos or take classes if this isn't possible.
Statistics
- Many factories witnessed a 30% increase in output due to the shift to electric motors. (en.wikipedia.org)
- According to the United Nations Industrial Development Organization (UNIDO), China is the top manufacturer worldwide by 2019 output, producing 28.7% of the total global manufacturing output, followed by the United States, Japan, Germany, and India.[52][53] (en.wikipedia.org)
- Job #1 is delivering the ordered product according to specifications: color, size, brand, and quantity. (netsuite.com)
- According to a Statista study, U.S. businesses spent $1.63 trillion on logistics in 2019, moving goods from origin to end user through various supply chain network segments. (netsuite.com)
- You can multiply the result by 100 to get the total percent of monthly overhead. (investopedia.com)
External Links
How To
How to Use 5S for Increasing Productivity in Manufacturing
5S stands for "Sort", 'Set In Order", 'Standardize', & Separate>. Toyota Motor Corporation invented the 5S strategy in 1954. It assists companies in improving their work environments and achieving higher efficiency.
The basic idea behind this method is to standardize production processes, so they become repeatable, measurable, and predictable. This means that every day tasks such cleaning, sorting/storing, packing, and labeling can be performed. These actions allow workers to perform their job more efficiently, knowing what to expect.
There are five steps that you need to follow in order to implement 5S. Each step has a different action and leads to higher efficiency. Sorting things makes it easier to find them later. When items are ordered, they are put together. Once you have separated your inventory into groups and organized them, you will store these groups in easily accessible containers. Finally, when you label your containers, you ensure everything is labeled correctly.
Employees need to reflect on how they do their jobs. Employees need to be able understand their motivations and discover alternative ways to do them. To be successful in the 5S system, employees will need to acquire new skills and techniques.
In addition to improving efficiency, the 5S system also increases morale and teamwork among employees. They feel more motivated to work towards achieving greater efficiency as they see the results.