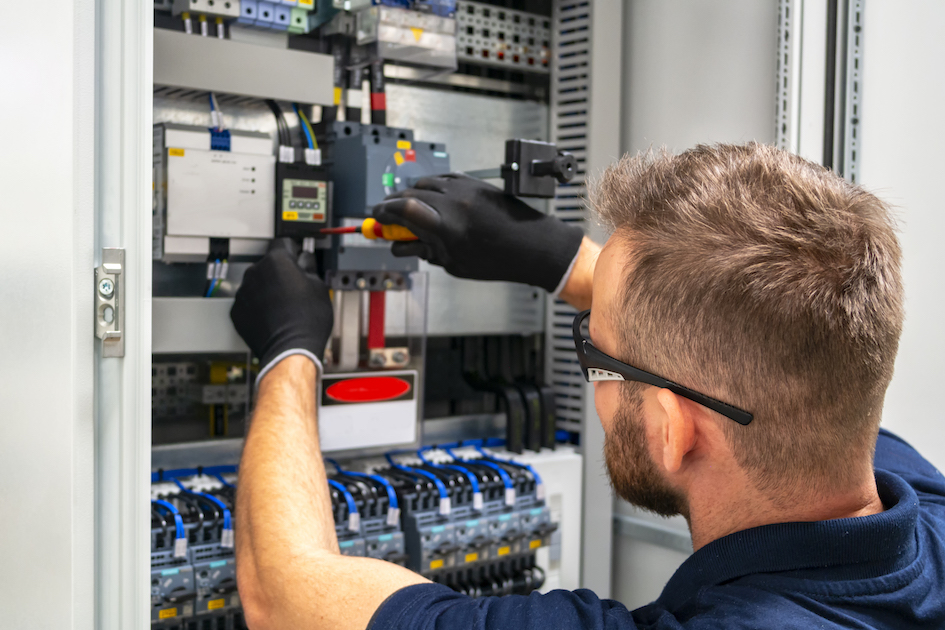
Originally developed by Toyota, Gemba Walk is a tool that takes managers to the shop floor to gain insights into the processes in the company. This practice is essential for any facility improvement program. It allows managers and employees to be more aware of the business processes and make better decision. It helps to identify both potential and existing problems.
Gemba, a Japanese term meaning "where the work happens", is a Japanese term. It is used to identify the factory floor and shop floor but can also refer to any other place where a product, or service, is created. Gemba refers to a Japanese business philosophy. Gemba is a Japanese business philosophy that aims to in depth understand the processes of an organization and reduce waste.
Gemba walks are important for companies that are looking to improve their processes and to eliminate waste. They also help to promote a more cooperative atmosphere in an organization. They encourage employees sharing ideas and can help improve the quality or the design of the product. They are also a great way to help executives and managers understand the business processes.
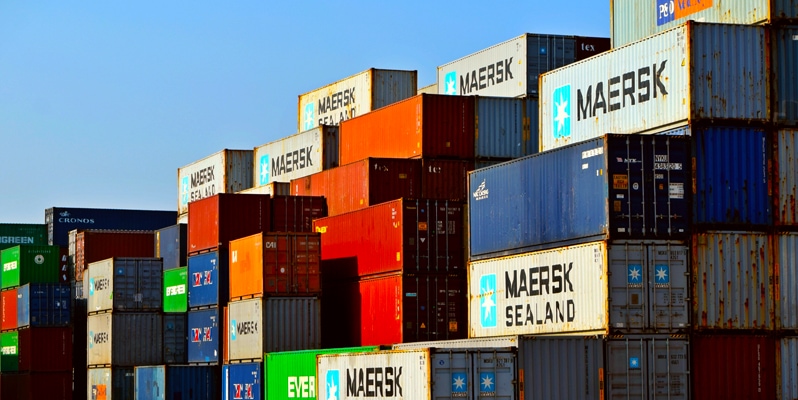
Gemba walks are usually conducted by supervisors or managers, but they can also be performed by executives on their own. Gemba walks should always be conducted by senior executives. Gemba walks should last between 45-60 minutes per week. Because it is easy to observe how workers do their jobs, these walks should not be done during peak hours.
Gemba Walks enable executives and managers to better understand the business processes. They also help to improve the overall safety of an organization. Safety issues account for the majority of waste generated by manufacturing plants. Continuous improvement can be made possible through safety improvements.
Gemba Walks, while an essential part of Lean, should be adopted by every level of the organization. They can help leaders and executives gain a fresh perspective on the needs of their customers, which can lead to better products, services, and processes. Gemba Walks can help an organization achieve its full potential.
Gemba Walks are an integral part of Lean process design and are frequently used by key stakeholders at Kaizen events. Kaizen events allow key stakeholders to meet up and discuss activities.
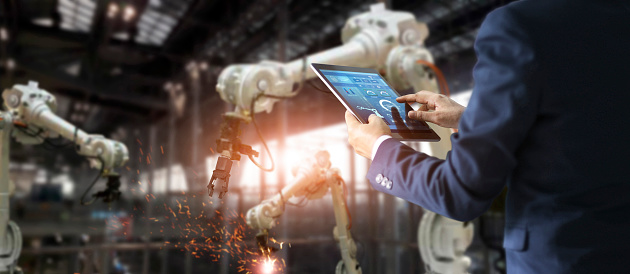
Gemba Walks must be done regularly. When done correctly, they can help reduce waste and increase productivity. Because these are the busiest hours of the day, it is best to do them during shift changes. This will help executives and project mangers gain a better understanding of their business. It is important to note any potential improvements, such as new products and services, or any ideas from employees.
FAQ
What are the jobs in logistics?
Logistics can offer many different jobs. Here are some examples:
-
Warehouse workers – They load, unload and transport pallets and trucks.
-
Transportation drivers – These drivers drive trucks and wagons to transport goods and pick up the goods.
-
Freight handlers, - They sort out and pack freight in warehouses.
-
Inventory managers – They manage the inventory in warehouses.
-
Sales reps are people who sell products to customers.
-
Logistics coordinators are responsible for organizing and planning logistics operations.
-
Purchasing agents - They buy goods and services that are necessary for company operations.
-
Customer service representatives – They answer emails and phone calls from customers.
-
Shipping clerks: They process shipping requests and issue bills.
-
Order fillers – They fill orders based upon what was ordered and shipped.
-
Quality control inspectors are responsible for inspecting incoming and outgoing products looking for defects.
-
Others - There is a variety of other jobs in logistics. These include transportation supervisors and cargo specialists.
How can manufacturing efficiency be improved?
First, identify the factors that affect production time. We must then find ways that we can improve these factors. You can start by identifying the most important factors that impact production time. Once you've identified them, try to find solutions for each of those factors.
What is the responsibility of a production planner?
Production planners ensure that all project aspects are completed on time, within budget and within the scope. They also ensure the quality of the product and service meets the client's requirements.
What skills does a production planner need?
You must be flexible and organized to become a productive production planner. It is also important to be able communicate with colleagues and clients.
Do we need to know about Manufacturing Processes before learning about Logistics?
No. You don't have to know about manufacturing processes before learning about logistics. Knowing about manufacturing processes will help you understand how logistics works.
Statistics
- Job #1 is delivering the ordered product according to specifications: color, size, brand, and quantity. (netsuite.com)
- You can multiply the result by 100 to get the total percent of monthly overhead. (investopedia.com)
- According to a Statista study, U.S. businesses spent $1.63 trillion on logistics in 2019, moving goods from origin to end user through various supply chain network segments. (netsuite.com)
- (2:04) MTO is a production technique wherein products are customized according to customer specifications, and production only starts after an order is received. (oracle.com)
- It's estimated that 10.8% of the U.S. GDP in 2020 was contributed to manufacturing. (investopedia.com)
External Links
How To
How to Use Six Sigma in Manufacturing
Six Sigma can be described as "the use of statistical process control (SPC), techniques to achieve continuous improvement." It was developed by Motorola's Quality Improvement Department at their plant in Tokyo, Japan, in 1986. Six Sigma's core idea is to improve the quality of processes by standardizing and eliminating defects. This method has been adopted by many companies in recent years as they believe there are no perfect products or services. The main goal of Six Sigma is to reduce variation from the mean value of production. This means that if you take a sample of your product, then measure its performance against the average, you can find out what percentage of the time the process deviates from the norm. If there is a significant deviation from the norm, you will know that something needs to change.
Understanding the dynamics of variability within your business is the first step in Six Sigma. Once you have a good understanding of the basics, you can identify potential sources of variation. These variations can also be classified as random or systematic. Random variations are caused when people make mistakes. While systematic variations are caused outside of the process, they can occur. These are, for instance, random variations that occur when widgets are made and some fall off the production line. If however, you notice that each time you assemble a widget it falls apart in exactly the same spot, that is a problem.
Once you identify the problem areas, it is time to create solutions. This could mean changing your approach or redesigning the entire process. Once you have implemented the changes, it is important to test them again to ensure they work. If they don't work, you will need to go back to the drawing boards and create a new plan.