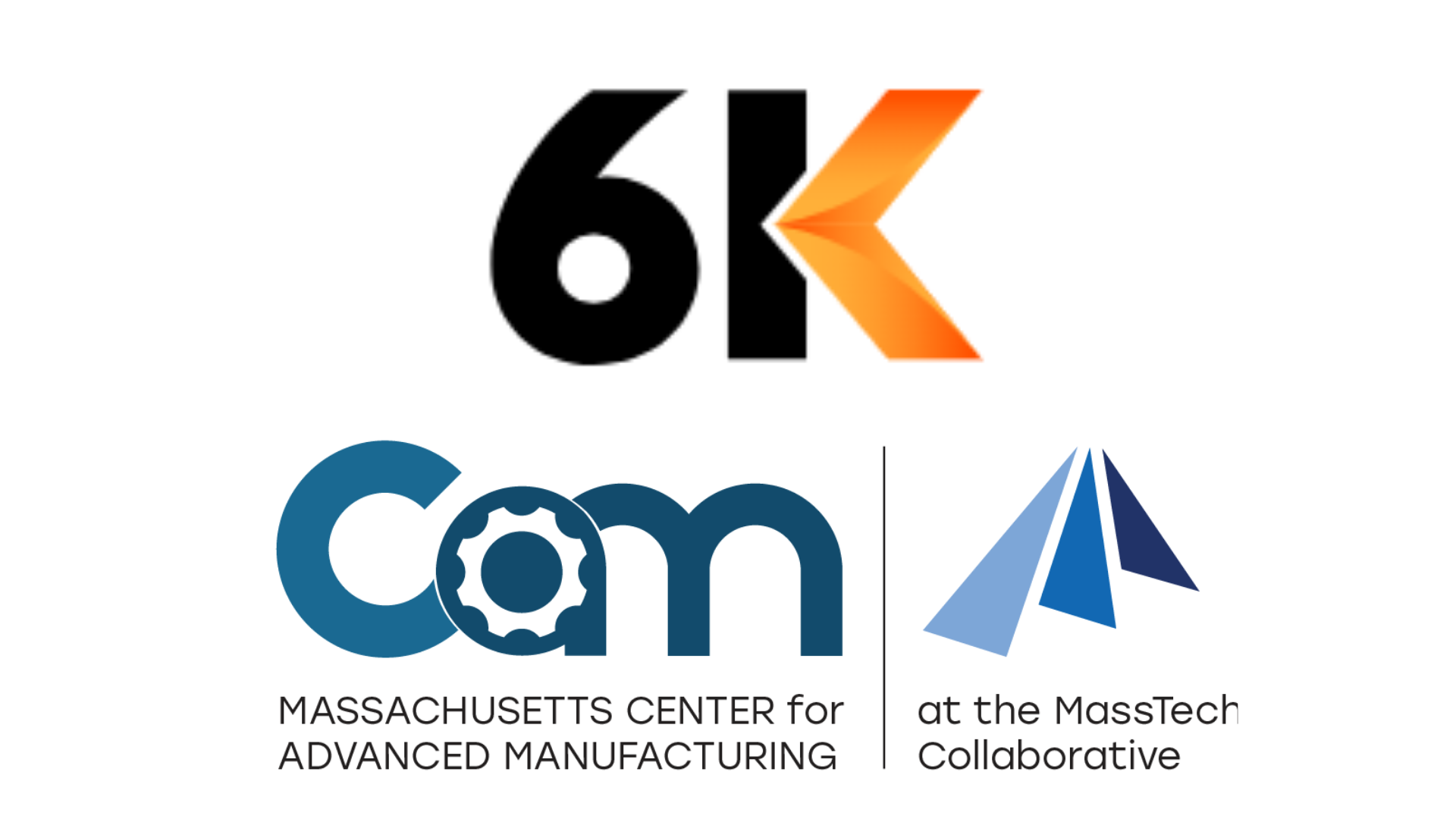
Industrial engineers need to have strong math skills and a background in physical sciences. They also need to be able to solve problems. These people can work in various sectors, such as manufacturing and construction. They may work in offices or on the factory floor.
Industrial engineers design and implement manufacturing processes to increase efficiency. They also help to develop quality control processes. They may also set manufacturing standards and train workers. People who want to become industrial engineers need to be open-minded and willing work with others. They should have a passion for improving efficiency and streamlining processes. They should have strong leadership and communication skills. They should also be adept at problem solving.
Industrial engineers design cost analysis systems. They also create systems that make robots more efficient. They also analyze data to determine whether processes are effective or not. They might also create manufacturing standards or design standards. Additionally, they are responsible for ensuring safety standards are met. They will develop procedures for equipment, inventory control, and create documentation. They may also present their plans in oral presentations or written reports.
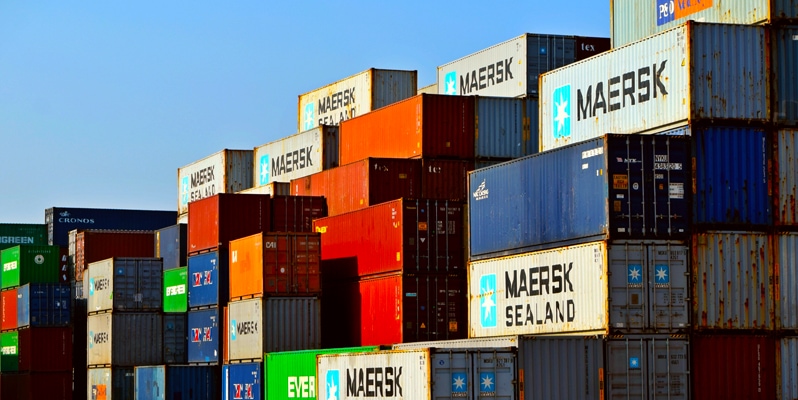
Industrial engineers work in offices and warehouses. They may need to work in noisy or cramped spaces. They may need to wear protective safety clothes. Sometimes they might have to work for longer hours than usual to meet production deadlines.
Industrial engineers are responsible for designing and implementing processes, ensuring that they operate efficiently and that the products are of high quality. They may also be responsible for solving production problems. Some industrial engineers are also entrepreneurs. They might have to train employees and ensure they know how the work. They may also have the responsibility of ensuring that raw materials meet certain quality standards before they can be used in manufacturing.
Industrial engineers work with other departments to create integrated systems for managing industrial production processes. They may specialize in one area of engineering. They might have to work in noisy or cramped environments and may need to work overtime to solve unexpected manufacturing problems. They may need to travel to warehouses or construction sites to gather data, and they may have to work with other professionals to find solutions to manufacturing problems.
Industrial engineers can advance through education or experience, and they may move to management positions. They may also start their own consulting firms or become technical experts in a particular area. They could also be experts in quality control or facility planning. They may also be responsible designing production layouts. They may also be responsible for developing wage and salary administration systems. They might also be responsible to schedule deliveries based upon production forecasts, storage and handling capabilities, and maintenance needs. They might also travel to other places and do administrative tasks. They may also supervise technicians.
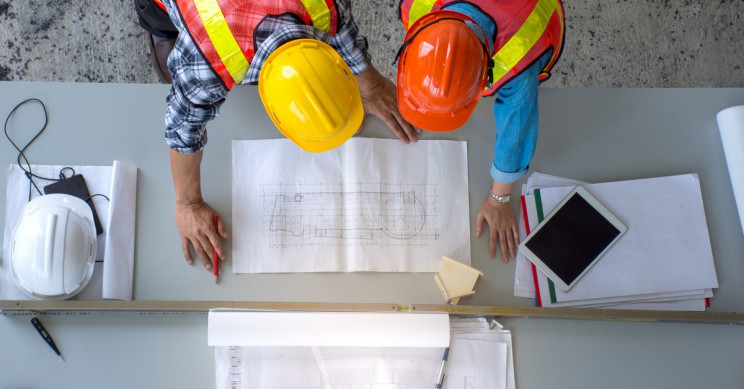
Industrial engineers could work for a company. They can work for a company or for a consulting service, and may work up to 40 hours per week. They may also be required to work for more hours in a consultancy service, if they are providing technical assistance for a business.
FAQ
What do we need to know about Manufacturing Processes in order to learn more about Logistics?
No. No. But, being familiar with manufacturing processes will give you a better understanding about how logistics works.
How can manufacturing prevent production bottlenecks?
To avoid production bottlenecks, ensure that all processes run smoothly from the moment you receive your order to the time the product ships.
This includes planning for capacity requirements as well as quality control measures.
The best way to do this is to use continuous improvement techniques such as Six Sigma.
Six Sigma can be used to improve the quality and decrease waste in all areas of your company.
It is focused on creating consistency and eliminating variation in your work.
Why should you automate your warehouse?
Automation has become increasingly important in modern warehousing. Increased demand for efficient and faster delivery has resulted in a rise in e-commerce.
Warehouses must be able to quickly adapt to changing demands. Technology investment is necessary to enable warehouses to respond quickly to changing demands. Automation of warehouses offers many benefits. These are just a few reasons to invest in automation.
-
Increases throughput/productivity
-
Reduces errors
-
Improves accuracy
-
Safety increases
-
Eliminates bottlenecks
-
Allows companies scale more easily
-
Makes workers more efficient
-
It gives visibility to everything that happens inside the warehouse
-
Enhances customer experience
-
Improves employee satisfaction
-
Minimizes downtime and increases uptime
-
High quality products delivered on-time
-
Eliminates human error
-
This helps to ensure compliance with regulations
Statistics
- [54][55] These are the top 50 countries by the total value of manufacturing output in US dollars for its noted year according to World Bank.[56] (en.wikipedia.org)
- Many factories witnessed a 30% increase in output due to the shift to electric motors. (en.wikipedia.org)
- (2:04) MTO is a production technique wherein products are customized according to customer specifications, and production only starts after an order is received. (oracle.com)
- Job #1 is delivering the ordered product according to specifications: color, size, brand, and quantity. (netsuite.com)
- According to a Statista study, U.S. businesses spent $1.63 trillion on logistics in 2019, moving goods from origin to end user through various supply chain network segments. (netsuite.com)
External Links
How To
How to Use Just-In-Time Production
Just-intime (JIT), which is a method to minimize costs and maximize efficiency in business process, is one way. It's a way to ensure that you get the right resources at just the right time. This means that your only pay for the resources you actually use. Frederick Taylor was the first to coin this term. He developed it while working as a foreman during the early 1900s. Taylor observed that overtime was paid to workers if they were late in working. He realized that workers should have enough time to complete their jobs before they begin work. This would help increase productivity.
JIT teaches you to plan ahead and prepare everything so you don’t waste time. It is important to look at your entire project from beginning to end and ensure that you have enough resources to handle any issues that may arise. You will have the resources and people to solve any problems you anticipate. This will prevent you from spending extra money on unnecessary things.
There are many types of JIT methods.
-
Demand-driven: This JIT is where you place regular orders for the parts/materials that are needed for your project. This will enable you to keep track of how much material is left after you use it. This will allow you to calculate how long it will take to make more.
-
Inventory-based: This is a type where you stock the materials required for your projects in advance. This allows you to predict how much you can expect to sell.
-
Project-driven: This is an approach where you set aside enough funds to cover the cost of your project. Knowing how much money you have available will help you purchase the correct amount of materials.
-
Resource-based JIT : This is probably the most popular type of JIT. You allocate resources based on the demand. You might assign more people to help with orders if there are many. If you don't have many orders, you'll assign fewer people to handle the workload.
-
Cost-based: This approach is very similar to resource-based. However, you don't just care about the number of people you have; you also need to consider how much each person will cost.
-
Price-based: This is a variant of cost-based. However, instead of focusing on the individual workers' costs, this looks at the total price of the company.
-
Material-based: This approach is similar to cost-based. However, instead of looking at the total cost for the company, you look at how much you spend on average on raw materials.
-
Time-based: Another variation of resource-based JIT. Instead of focusing on the cost of each employee, you will focus on the time it takes to complete a project.
-
Quality-based JIT: This is another variation of resource based JIT. Instead of thinking about the cost of each employee or the time it takes to produce something, you focus on how good your product quality.
-
Value-based JIT : This is the newest type of JIT. In this case, you're not concerned with how well the products perform or whether they meet customer expectations. Instead, you focus on the added value that you provide to your market.
-
Stock-based: This is an inventory-based method that focuses on the actual number of items being produced at any given time. It is used when production goals are met while inventory is kept to a minimum.
-
Just-in-time planning (JIT): This is a combination JIT and supply-chain management. This refers to the scheduling of the delivery of components as soon after they are ordered. It is essential because it reduces lead-times and increases throughput.