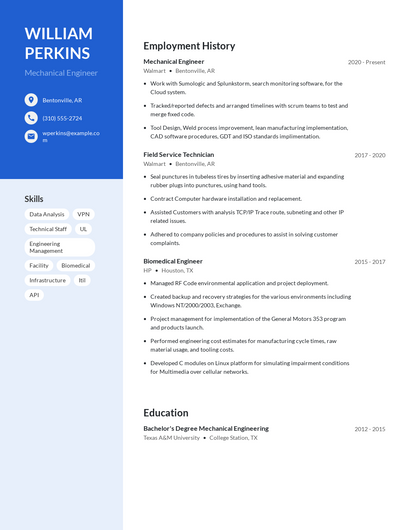
Toyota Production System was originally known as Just in Time production. It is an integrated socio-technical program that eliminates waste and improves processes. It is used to organize manufacturing, logistics, as well as customer interaction. It also drives continuous improvement and employee development. It is also the foundation for Lean Manufacturing. Numerous manufacturing facilities, both in the United States of America and overseas, have adopted the Toyota Production System.
SakichiToyoda was the creator of Toyota's Production System. He studied every production phase of his company and removed unnecessary parts. This resulted in a 20% decrease in build time. Toyota also had to build a vehicle half the time it took GM. Toyota was at the brink of bankruptcy in the early 1950s.
Taiichi Okno, Toyota's executive in the mid-1940s observed the stocking process at a supermarket. He saw the potential for reducing production time by using Just-in Time methods. Eiji Toyoda was his president and he developed the Toyota Production System. It was created between 1948-1975.
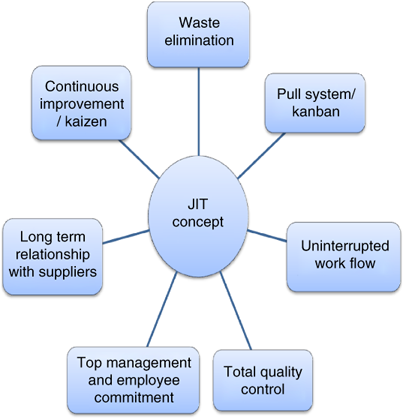
Toyota Production System was built to eliminate waste, inconsistency and inefficiency. Kaizen, Japanese for continuous improvement is the basis of the overall philosophy. Toyota's Production System is continually improved to meet company needs. It drives learning throughout the company and uses simple yet effective low-tech tools combined with advanced production techniques. It also makes use of advanced information technology and uses unique management/social practices.
The Toyota Production System was built around six core principles. It has been used by many companies such as Boeing, Porsche, Honda, and others. These companies reengineered processes in order to copy Toyota's production systems.
The Toyota Production System also involves team building activities. These activities include safety rounds at the local level, where staff are evaluated on their compliance with safety measures. All team members are encouraged and encouraged to share their ideas and seek out ways to improve. This has helped to change the culture in the company.
Jidoka is another concept that automates processes with a human touch. Jidoka encourages workers not to do their best work and to stop producing when they discover problems. Jidoka also stresses the importance in building things right from the beginning, and not overlooking problems.
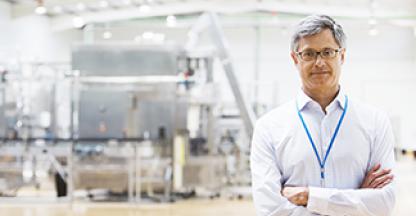
Visual control is another feature of the Toyota Production System. It makes work instructions visible on the factory floor. This ensures that workers follow instructions correctly. The company also uses poka-yoke devices to verify quality standards. These devices can also help to identify a red bunny.
The Toyota Production System is not only applicable to manufacturing plants, but also health care. It can be used by patients to improve their satisfaction. It can also be applied to critical care and the operating room.
Using the Toyota Production System, it is possible to improve patient satisfaction and health care delivery. In 2003, an EPA case study reported that Toyota's efforts in waste reduction had caught the EPA’s attention. This led to several partnerships with companies including the St. Bernard Project, which employs military vets.
FAQ
How can manufacturing avoid production bottlenecks
The key to avoiding bottlenecks in production is to keep all processes running smoothly throughout the entire production cycle, from the time you receive an order until the time when the product ships.
This includes both planning for capacity and quality control.
Continuous improvement techniques such Six Sigma can help you achieve this.
Six Sigma management is a system that improves quality and reduces waste within your organization.
It emphasizes consistency and eliminating variance in your work.
What are the products and services of logistics?
Logistics are the activities involved in moving goods from point A to point B.
They include all aspects of transport, including packaging, loading, transporting, unloading, storing, warehousing, inventory management, customer service, distribution, returns, and recycling.
Logisticians make sure that the right product arrives at the right place at the correct time and in safe conditions. They help companies manage their supply chain efficiency by providing information on demand forecasts, stock levels, production schedules, and availability of raw materials.
They can also track shipments in transit and monitor quality standards.
What is the role of a production manager?
A production planner makes sure all project elements are delivered on schedule, within budget, as well as within the agreed scope. They ensure that the product or service is of high quality and meets client requirements.
Statistics
- Job #1 is delivering the ordered product according to specifications: color, size, brand, and quantity. (netsuite.com)
- You can multiply the result by 100 to get the total percent of monthly overhead. (investopedia.com)
- It's estimated that 10.8% of the U.S. GDP in 2020 was contributed to manufacturing. (investopedia.com)
- Many factories witnessed a 30% increase in output due to the shift to electric motors. (en.wikipedia.org)
- According to a Statista study, U.S. businesses spent $1.63 trillion on logistics in 2019, moving goods from origin to end user through various supply chain network segments. (netsuite.com)
External Links
How To
How to Use 5S for Increasing Productivity in Manufacturing
5S stands as "Sort", Set In Order", Standardize", Separate" and "Store". Toyota Motor Corporation invented the 5S strategy in 1954. This methodology helps companies improve their work environment to increase efficiency.
The idea behind standardizing production processes is to make them repeatable and measurable. This means that tasks such as cleaning, sorting, storing, packing, and labeling are performed daily. This knowledge allows workers to be more efficient in their work because they are aware of what to expect.
Implementing 5S requires five steps. These are Sort, Set In Order, Standardize. Separate. And Store. Each step involves a different action which leads to increased efficiency. You can make it easy for people to find things later by sorting them. When you arrange items, you place them together. Next, organize your inventory into categories and store them in containers that are easily accessible. Finally, label all containers correctly.
Employees must be able to critically examine their work practices. Employees should understand why they do the tasks they do, and then decide if there are better ways to accomplish them. They will need to develop new skills and techniques in order for the 5S system to be implemented.
In addition to increasing efficiency, the 5S method also improves morale and teamwork among employees. They feel more motivated to work towards achieving greater efficiency as they see the results.