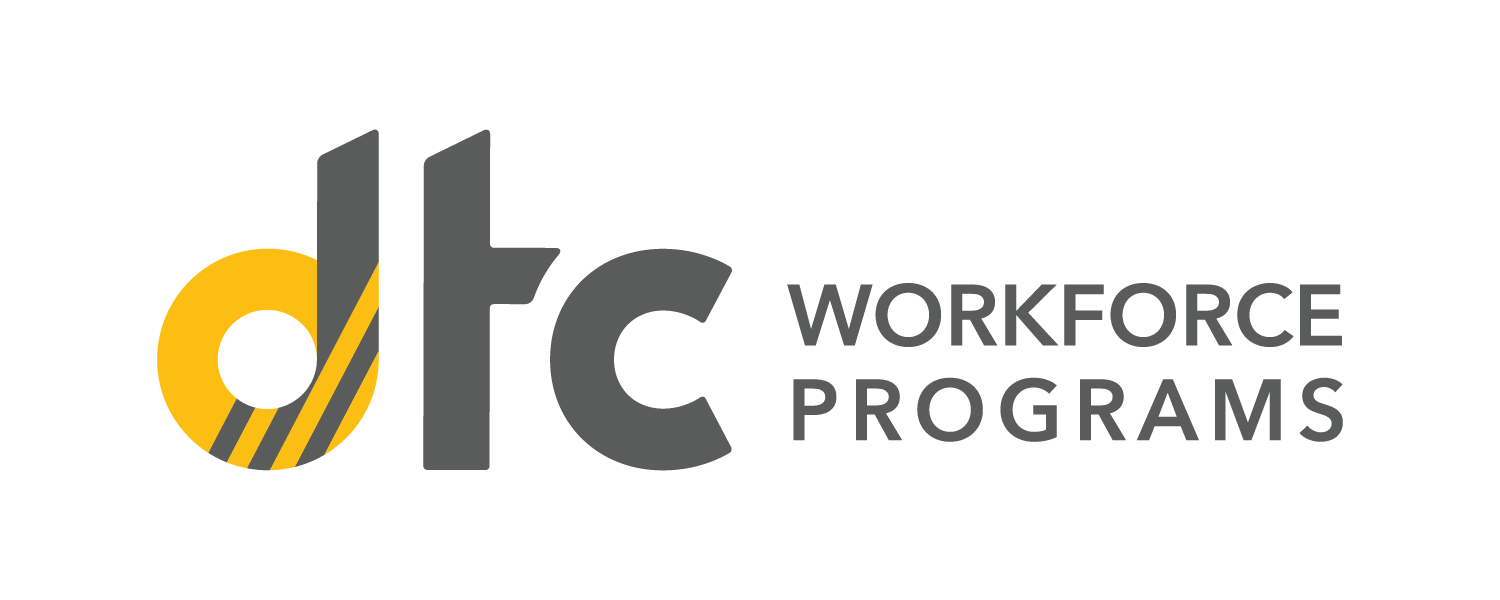
Toyota Motor Manufacturing Indiana Inc. is located in Gibson County Indiana. This plant was the first Toyota plant in America to be completely owned by Toyota. It produces Toyota's full-size pickup trucks including the Avalon, Corolla and Corolla as well as the Sienna minivan. It also produces Toyota's best-selling hybrid, the Toyota RAV4 Hybrid.
The plant was originally intended to make the Toyota Highlander. Instead, it moved to Gibson County, Indiana. The plant has been producing Toyota's RAV4 Hybrid compact SUV and the Lexus ES 350 since 2011. Toyota spent over $1.33 billion on the plant in 2017.
Toyota Safety Sense 2.5+ can also be manufactured here. This feature includes automatic emergency braking. In addition, the plant is preparing all of the new 2018 Camry models. The new model boasts a new transmission with more power and a more stylish look. It will be $25,900.
Toyota's Camry is the most popular car in America. It is America's most-sold midsize sedan and has been since 1995. Toyota has produced 10 million Camry vehicles in Kentucky. The plant is the first in North America to manufacture the hybrid model.
Toyota Production System is a collection if practices and techniques that improve quality, efficiency, and productivity. This system will include 600 Toyota engineers. This center will also be one of the first to manufacture hydrogen fuel cells modules for heavy-duty commercial trucks. This facility can manufacture up to 100,000 vehicles each year.
Toyota has made $1.5 billion investments in the plant during the last five-years. It also hired 700 more employees. By 2020, this investment will provide 470,100 additional jobs in the United States. Toyota has made over $147 Million in Kentucky non-profit partners since 1986.
The Toyota Camry, a reliable and elegant vehicle, is very popular. It uses the GA-K platform and a new transmission. It is also fun to drive. Consumer Reports highlighted Toyota Camry's popularity as one of America’s top-selling cars in July.
Toyota's production systems include a variety of elements, such as continuous improvement, justin time parts delivery, and a sophisticated robot welding system. The Toyota Production Engineering and Manufacturing Center is a good example of how Toyota has made the most of its investment in Kentucky.
Toyota has a new production facility design that allows them to reduce construction and cooling costs. The building also features a Visitor Center, which includes interactive video displays and exhibits on hybrid technology. Toyota will be producing up to 2,000,000 vehicles in North America over the next 10 year. This is the largest Toyota facility outside Japan.
Toyota's New Global Architecture (or New Global Architecture) is a huge step forward in improving Toyota's production process. This strategy includes a revamped engine and organization of production. It also includes a module that unifies all vehicle components. While the new design is a reflection of Toyota's traditional values, it retains its innovative spirit.
FAQ
What is the role of a manager in manufacturing?
A manufacturing manager must make sure that all manufacturing processes run smoothly and effectively. They should be aware of any issues within the company and respond accordingly.
They should also know how to communicate with other departments such as sales and marketing.
They should be up to date on the latest trends and be able apply this knowledge to increase productivity and efficiency.
What are the 4 types of manufacturing?
Manufacturing is the process of transforming raw materials into useful products using machines and processes. Manufacturing can include many activities such as designing and building, testing, packaging shipping, selling, servicing, and other related activities.
What is production planning?
Production planning is the process of creating a plan that covers all aspects of production. This includes scheduling, budgeting and crew, location, equipment, props, and more. This document will ensure everything is in order and ready to go when you need it. It should also contain information on achieving the best results on set. This includes information on shooting times, locations, cast lists and crew details.
The first step is to outline what you want to film. You might have an idea of where you want to film, or you may have specific locations or sets in mind. Once you have identified your locations and scenes it's time to begin figuring out what elements you will need for each one. One example is if you are unsure of the exact model you want but decide that you require a car. This is where you can look up car models online and narrow down your options by choosing from different makes and models.
After you have selected the car you want, you can begin to think about additional features. You might need to have people in the front seats. Maybe you need someone to move around in the back. Maybe you want to change the interior color from black to white? These questions will help determine the look and feel you want for your car. Another thing you can do is think about what type of shots are desired. Are you going to be shooting close-ups? Or wide angles? Maybe you want the engine or the steering wheels to be shown. This will allow you to determine the type of car you want.
Once you have determined all of the above, you can move on to creating a schedule. You can create a schedule that will outline when you must start and finish your shoots. Each day will include the time when you need to arrive at the location, when you need to leave and when you need to return home. Everyone will know what they need and when. It is possible to make arrangements in advance for additional staff if you are looking to hire. You don't want to hire someone who won't show up because he didn't know.
You will need to factor in the days that you have to film when creating your schedule. Some projects are quick and easy, while others take weeks. When you are creating your schedule, you should always keep in mind whether you need more than one shot per day or not. Multiple takes at the same place will result in higher costs and longer completion times. You can't be certain if you will need multiple takes so it is better not to shoot too many.
Budgeting is another important aspect of production planning. As it will allow you and your team to work within your financial means, setting a realistic budget is crucial. Remember that you can always reduce the budget later on if you run into unforeseen problems. But, don't underestimate how much money you'll spend. You will end up spending less money if you underestimate the cost of something.
Production planning is a very detailed process, but once you understand how everything works together, it becomes easier to plan future projects.
Is automation important for manufacturing?
Automating is not just important for manufacturers, but also for service providers. Automation allows them to deliver services quicker and more efficiently. In addition, it helps them reduce costs by reducing human errors and improving productivity.
Statistics
- [54][55] These are the top 50 countries by the total value of manufacturing output in US dollars for its noted year according to World Bank.[56] (en.wikipedia.org)
- (2:04) MTO is a production technique wherein products are customized according to customer specifications, and production only starts after an order is received. (oracle.com)
- You can multiply the result by 100 to get the total percent of monthly overhead. (investopedia.com)
- Many factories witnessed a 30% increase in output due to the shift to electric motors. (en.wikipedia.org)
- It's estimated that 10.8% of the U.S. GDP in 2020 was contributed to manufacturing. (investopedia.com)
External Links
How To
How to Use Lean Manufacturing in the Production of Goods
Lean manufacturing is an approach to management that aims for efficiency and waste reduction. It was developed in Japan during the 1970s and 1980s by Taiichi Ohno, who received the Toyota Production System (TPS) award from TPS founder Kanji Toyoda. Michael L. Watkins published the book "The Machine That Changed the World", which was the first to be published about lean manufacturing.
Lean manufacturing can be described as a set or principles that are used to improve quality, speed and cost of products or services. It is about eliminating defects and waste from all stages of the value stream. Lean manufacturing can be described as just-in–time (JIT), total productive maintenance, zero defect (TPM), or even 5S. Lean manufacturing eliminates non-value-added tasks like inspection, rework, waiting.
Lean manufacturing can help companies improve their product quality and reduce costs. Additionally, it helps them achieve their goals more quickly and reduces employee turnover. Lean manufacturing can be used to manage all aspects of the value chain. Customers, suppliers, distributors, retailers and employees are all included. Lean manufacturing practices are widespread in many industries. For example, Toyota's philosophy underpins its success in automobiles, electronics, appliances, healthcare, chemical engineering, aerospace, paper, food, etc.
Five fundamental principles underlie lean manufacturing.
-
Define Value - Identify the value your business adds to society and what makes you different from competitors.
-
Reduce waste - Get rid of any activity that does not add value to the supply chain.
-
Create Flow: Ensure that the work process flows without interruptions.
-
Standardize and simplify - Make your processes as consistent as possible.
-
Building Relationships – Establish personal relationships with both external and internal stakeholders.
Although lean manufacturing isn't a new concept in business, it has gained popularity due to renewed interest in the economy after the 2008 global financial crisis. Many businesses are now using lean manufacturing to improve their competitiveness. In fact, some economists believe that lean manufacturing will be an important factor in economic recovery.
Lean manufacturing is now becoming a common practice in the automotive industry, with many benefits. These include higher customer satisfaction, lower inventory levels, lower operating expenses, greater productivity, and improved overall safety.
It can be applied to any aspect of an organisation. However, it is particularly useful when applied to the production side of an organization because it ensures that all steps in the value chain are efficient and effective.
There are three main types in lean manufacturing
-
Just-in-Time Manufacturing: Also known as "pull systems", this type of lean manufacturing uses just-in-time manufacturing (JIT). JIT refers to a system in which components are assembled at the point of use instead of being produced ahead of time. This strategy aims to decrease lead times, increase availability of parts and reduce inventory.
-
Zero Defects Manufacturing (ZDM): ZDM focuses on ensuring that no defective units leave the manufacturing facility. Repairing a part that is damaged during assembly should be done, not scrapping. This is also true for finished products that require minor repairs before shipping.
-
Continuous Improvement (CI),: Continuous improvement aims improve the efficiency and effectiveness of operations by continuously identifying issues and making changes to reduce waste. Continuous improvement involves continuous improvement of processes and people as well as tools.