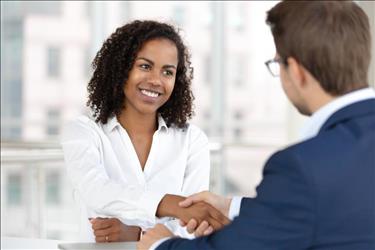
Japanese factories produce high-quality products at low costs. They make up five percent of the country’s GDP and are the economic backbone. However, they have struggled to cope with tighter standards as well growing competition and the rising cost pressures caused by the recent recession.
A white paper published by the government last year found that Japanese companies were not prepared to handle a cut in parts procurement. The recession hit the Japanese automobile industry hard. Traditionally, the car manufacturing industry relies on 30,000 different parts, so a disruption to the supply chain can stop production. Some parts don't have substitutes.
Japanese manufacturers closely work with suppliers to address problems and improve efficiency, in order not to compromise the quality of their products. They also encourage workers, salesmen, and quality inspectors to give feedback.
Japanese manufacturers are concerned about the high number of accidents on the factory floor. There have been a series of safety scandals that have erupted across the country's manufacturing sector. This has increased scrutiny over the quality of work in factories.
Non-regular staff is another problem that has impacted the production of Japanese products. Companies can reduce labor costs by hiring non-regular workers, but they also increase the chance of accidents and lower the skill level on the production floor. For their employees to be more safe and competent, companies are now focusing on training them.
Japan's growing labor shortage is due to the country's declining birthrate. A 25-year high number of Japanese companies are complaining of a lack of labor. Japanese companies will face further challenges if their labor force shrinks.
Although there are fewer skilled workers, many factories have cut costs. A growing number of so-called "factries" employ fewer than ten people. These small workshops often produce some of the most advanced equipment in the world.
China and South Korea are increasing their competition for the Japanese manufacturing sector. Many factories are trying reduce costs and increase productivity. The Japanese government has warned, however, that the industry may lose its competitive edge overseas.
As Japan faces increased competition from Asia and abroad, it is facing questions about whether it can adjust its processes to meet demand and adapt quickly enough. The demand for skilled workers will rise even if Japan can adapt its processes to meet the increased competition from Asia and abroad.
Japanese factories are a major source of components for global markets. They also source advanced materials like silicon chips for smart phones and computers. They rely on Japan for crucial components, whereas Chinese factories focus on low-cost assembly.
While they have tried to improve their quality and productivity, the Japanese have also faced increased competition from other countries. Their products have seen a drop in value on the domestic market due to recession. They have also had to cut their costs. The Japanese are able to produce high-quality products despite all these difficulties.
FAQ
What are the products and services of logistics?
Logistics is the process of moving goods from one point to another.
They cover all aspects of transportation, such as packing, loading, transporting and unloading.
Logisticians ensure the product reaches its destination in the most efficient manner. They help companies manage their supply chain efficiency by providing information on demand forecasts, stock levels, production schedules, and availability of raw materials.
They coordinate with vendors and suppliers, keep track of shipments, monitor quality standards and perform inventory and order replenishment.
What does "warehouse" mean?
A warehouse is an area where goods are stored before being sold. It can be indoors or out. In some cases it could be both indoors and outdoors.
What skills does a production planner need?
To become a successful production planner, you need to be organized, flexible, and able to multitask. It is also important to be able communicate with colleagues and clients.
Statistics
- According to a Statista study, U.S. businesses spent $1.63 trillion on logistics in 2019, moving goods from origin to end user through various supply chain network segments. (netsuite.com)
- [54][55] These are the top 50 countries by the total value of manufacturing output in US dollars for its noted year according to World Bank.[56] (en.wikipedia.org)
- (2:04) MTO is a production technique wherein products are customized according to customer specifications, and production only starts after an order is received. (oracle.com)
- In 2021, an estimated 12.1 million Americans work in the manufacturing sector.6 (investopedia.com)
- It's estimated that 10.8% of the U.S. GDP in 2020 was contributed to manufacturing. (investopedia.com)
External Links
How To
How to Use Six Sigma in Manufacturing
Six Sigma is "the application statistical process control (SPC), techniques for continuous improvement." Motorola's Quality Improvement Department developed it at their Tokyo plant in Japan in 1986. Six Sigma is a method to improve quality through standardization and elimination of defects. Many companies have adopted this method in recent years. They believe there is no such thing a perfect product or service. The main goal of Six Sigma is to reduce variation from the mean value of production. This means that you can take a sample from your product and then compare its performance to the average to find out how often the process differs from the norm. If there is a significant deviation from the norm, you will know that something needs to change.
Understanding how variability works in your company is the first step to Six Sigma. Once you have a good understanding of the basics, you can identify potential sources of variation. Also, you will need to identify the sources of variation. Random variations occur when people do mistakes. Symmetrical variations are caused due to factors beyond the process. For example, if you're making widgets, and some of them fall off the assembly line, those would be considered random variations. However, if you notice that every time you assemble a widget, it always falls apart at exactly the same place, then that would be a systematic problem.
After identifying the problem areas, you will need to devise solutions. It might mean changing the way you do business or redesigning it entirely. You should then test the changes again after they have been implemented. If they don't work you need to rework them and come up a better plan.