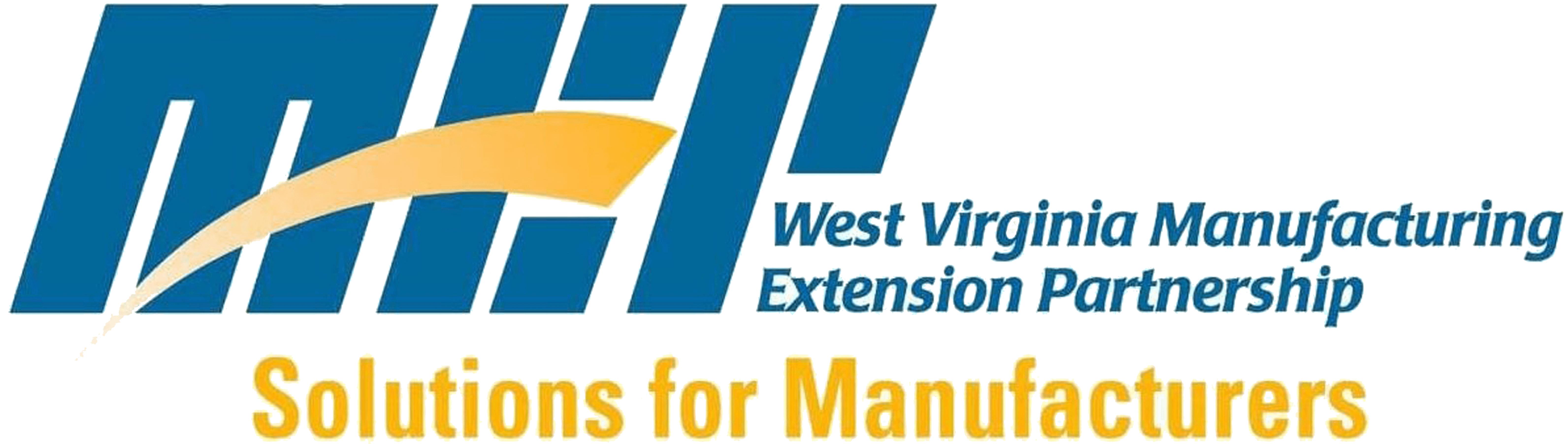
There are many logistics companies in North Carolina that can help you, whether your company requires a warehouse, distribution center or product transport. They offer many services including warehouse distribution, drayage trucks, and broared transportation solutions.
The Charlotte region in North Carolina is the perfect place to find distribution services. The region is located between two major interstate highways and has easy access to the bulk of the U.S. population and ports. It is also home to the sixth busiest airport in the nation.
There are many advantages for companies looking to locate their distribution centers in Charlotte. This includes easy access to major ports, an inland city location, and cost-effective industrial space. The country's leading high-technology research and development park is located here.
North Carolina's rail infrastructure continues to improve. North Carolina has the country's largest consolidated railway system. The rail system connects 22 states. Your company can travel to more than 70% of the U.S. in one day.
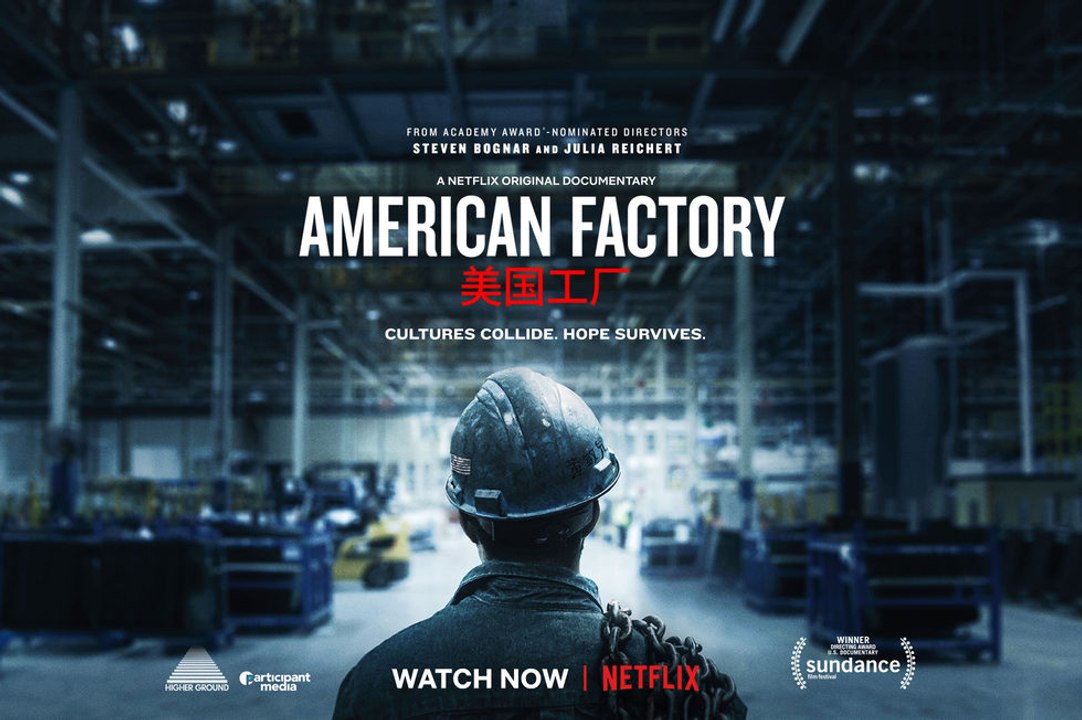
North Carolina also offers two major shipping ports. Both the Port of Wilmington, Morehead City and Morehead City offer full-service transportation to both coastal and inland destinations. The Port of Virginia is also accessible at Norfolk/Hampton Roads.
There are several large aerospace companies as well as many other manufacturing firms in the state. North Carolina is also home to several Foreign Trade Zones, making it a convenient location to import or export products. Strong product demand is a result of a robust economy. This will continue to impact the global supply chain.
ACI Transport believes in integrity and adaptability. It also places emphasis on customer service and communication. ACI offers a variety of transportation services for the building, chemical, and healthcare industries.
C&O Warehousing & Logistics has a 400,000 square-foot modern warehouse facility in Raleigh-Durham, NC. This company offers complete distribution services and is built around modern warehouse spaces.
The company is currently expanding its offerings to the East Coast's life science industry. The company has also partnered up with a prominent Food & Beverage manufacturer. Over the next few year, 300 new employees will be added to the company.
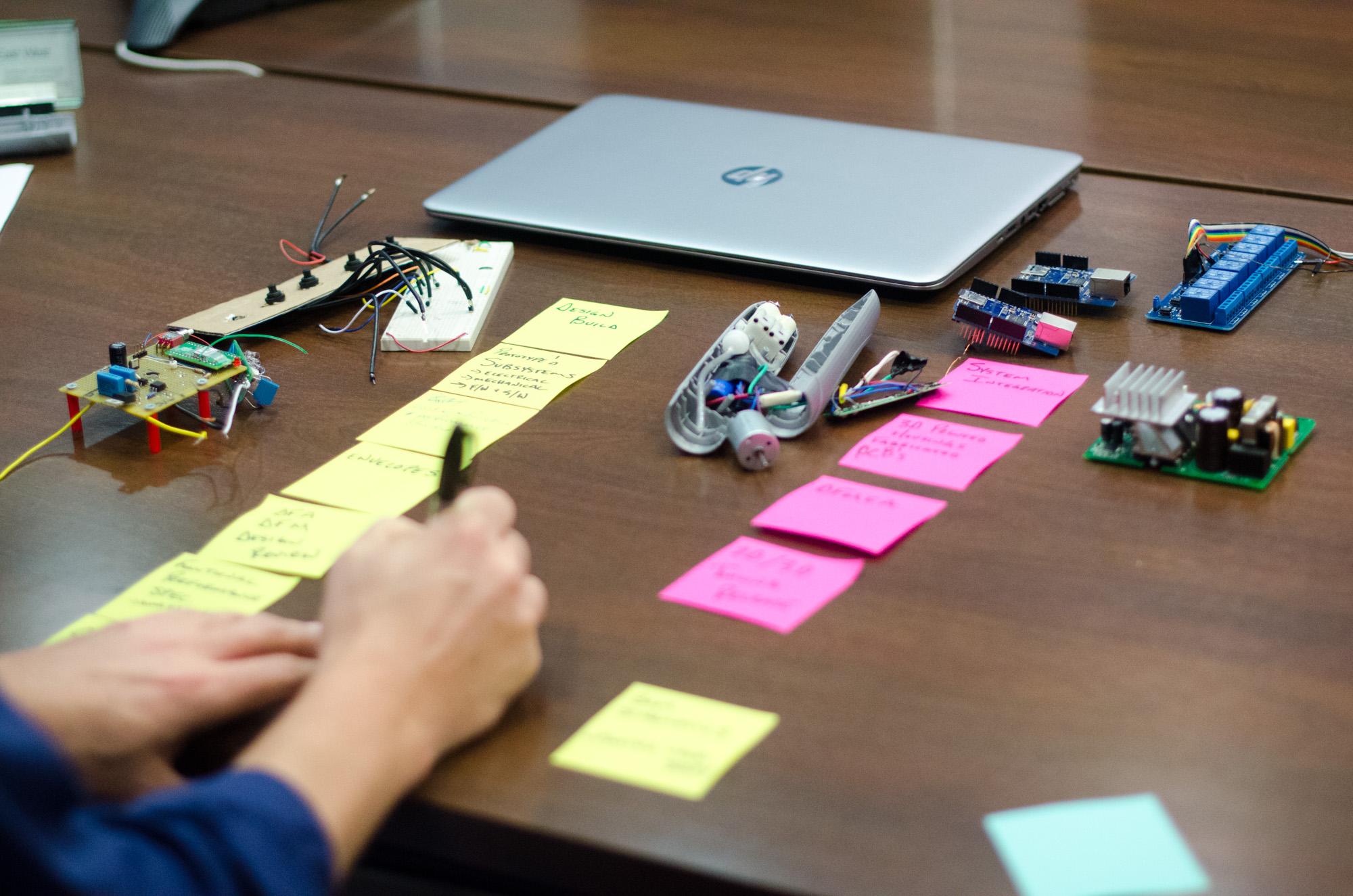
CSX has opened the CSX Carolina Connector intermodal terminal in Rocky Mount (NC) recently. This project won the Hay Award for Excellence. CSX has also opened direct rail service from the Port of Wilmington. This is a major boon to manufacturers in Rocky Mount, NC.
North Carolina has two full service shipping ports in addition to warehousing. Port City Logistics offers several transportation services, such as drayage and warehouse distribution. Port City has over 3.5 million square foot of warehouse space. Port City also offers brokered transportation solutions. Port City intends to invest $16 millions in a 150,000 sq. ft. building in New Hanover County. New Hanover County will benefit from 75 new jobs created by this building.
FAQ
What does warehouse mean?
A warehouse, or storage facility, is where goods are stored prior to being sold. It can be indoors or out. In some cases, it may be a combination of both.
What kind of jobs are there in logistics?
There are many types of jobs in logistics. Here are some:
-
Warehouse workers - They load trucks and pallets.
-
Transportation drivers - They drive trucks and trailers to deliver goods and carry out pick-ups.
-
Freight handlers are people who sort and pack freight into warehouses.
-
Inventory managers - They oversee the inventory of goods in warehouses.
-
Sales representatives: They sell products to customers.
-
Logistics coordinators are responsible for organizing and planning logistics operations.
-
Purchasing agents - They buy goods and services that are necessary for company operations.
-
Customer service representatives - Answer calls and email from customers.
-
Shipping clerks - They process shipping orders and issue bills.
-
Order fillers – They fill orders based upon what was ordered and shipped.
-
Quality control inspectors – They inspect incoming and outgoing products to ensure that there are no defects.
-
Others - There are many other types of jobs available in logistics, such as transportation supervisors, cargo specialists, etc.
What are the responsibilities for a manufacturing manager
A manufacturing manager has to ensure that all manufacturing processes work efficiently and effectively. They should also be aware and responsive to any company problems.
They should also be able and comfortable communicating with other departments like sales and marketing.
They should also be knowledgeable about the latest trends in the industry so they can use this information for productivity and efficiency improvements.
What is the difference between Production Planning, Scheduling and Production Planning?
Production Planning (PP) is the process of determining what needs to be produced at any given point in time. This is done through forecasting demand and identifying production capacities.
Scheduling refers the process by which tasks are assigned dates so that they can all be completed within the given timeframe.
What are the four types in manufacturing?
Manufacturing refers the process of turning raw materials into useful products with machines and processes. It involves many different activities such as designing, building, testing, packaging, shipping, selling, servicing, etc.
What is production planning?
Production Planning refers to the development of a plan for every aspect of production. It is important to have everything ready and planned before you start shooting. This document should also include information on how to get the best result on set. It should include information about shooting locations, casting lists, crew details, equipment requirements, and shooting schedules.
The first step is to decide what you want. You may have already decided where you would like to shoot, or maybe there are specific locations or sets that you want to use. Once you have identified your locations and scenes it's time to begin figuring out what elements you will need for each one. You might decide you need a car, but not sure what make or model. You could look online for cars to see what options are available, and then narrow down your choices by selecting between different makes or models.
After you have selected the car you want, you can begin to think about additional features. Do you need people sitting in the front seats? Perhaps you have someone who needs to be able to walk around the back of your car. You may want to change the interior's color from black or white. These questions will help to determine the style and feel of your car. Also, think about what kind of shots you would like to capture. Do you want to film close-ups, or wider angles? Maybe the engine or steering wheel is what you are looking to film. This will allow you to determine the type of car you want.
Once you have made all the necessary decisions, you can start to create a schedule. You can use a schedule to determine when and where you need it to be shot. The schedule will show you when to get there, what time to leave, and when to return home. This way, everyone knows what they need to do and when. Book extra staff ahead of time if you need them. It's not worth paying someone to show up if you haven't told him.
When creating your schedule, you will also need to consider the number of days you need to film. Some projects are quick and easy, while others take weeks. You should consider whether you will need more than one shot per week when creating your schedule. Shooting multiple takes over the same location will increase costs and take longer to complete. You can't be certain if you will need multiple takes so it is better not to shoot too many.
Another important aspect of production planning is setting budgets. You will be able to manage your resources if you have a realistic budget. You can always lower the budget if you encounter unexpected problems. You shouldn't underestimate the amount you'll spend. If you underestimate how much something costs, you'll have less money to pay for other items.
Production planning is a very detailed process, but once you understand how everything works together, it becomes easier to plan future projects.
What is meant by manufacturing industries?
Manufacturing Industries are those businesses that make products for sale. Consumers are people who purchase these goods. This is accomplished by using a variety of processes, including production, distribution and retailing. They manufacture goods from raw materials using machines and other equipment. This includes all types manufactured goods such as clothing, building materials, furniture, electronics, tools and machinery.
Statistics
- (2:04) MTO is a production technique wherein products are customized according to customer specifications, and production only starts after an order is received. (oracle.com)
- In 2021, an estimated 12.1 million Americans work in the manufacturing sector.6 (investopedia.com)
- Job #1 is delivering the ordered product according to specifications: color, size, brand, and quantity. (netsuite.com)
- Many factories witnessed a 30% increase in output due to the shift to electric motors. (en.wikipedia.org)
- In the United States, for example, manufacturing makes up 15% of the economic output. (twi-global.com)
External Links
How To
How to Use Lean Manufacturing for the Production of Goods
Lean manufacturing is a management style that aims to increase efficiency and reduce waste through continuous improvement. It was created in Japan by Taiichi Ohno during the 1970s and 80s. He received the Toyota Production System award (TPS), from Kanji Toyoda, founder of TPS. Michael L. Watkins published the book "The Machine That Changed the World", which was the first to be published about lean manufacturing.
Lean manufacturing refers to a set of principles that improve the quality, speed and costs of products and services. It emphasizes the elimination and minimization of waste in the value stream. Lean manufacturing is called just-in-time (JIT), zero defect, total productive maintenance (TPM), or 5S. Lean manufacturing focuses on eliminating non-value-added activities such as rework, inspection, and waiting.
In addition to improving product quality and reducing costs, lean manufacturing helps companies achieve their goals faster and reduces employee turnover. Lean Manufacturing is one of the most efficient ways to manage the entire value chains, including suppliers and customers as well distributors and retailers. Lean manufacturing is widely used in many industries. Toyota's philosophy has been a key driver of success in many industries, including automobiles and electronics.
Lean manufacturing is based on five principles:
-
Define Value - Determine the value that your business brings to society. Also, identify what sets you apart from your competitors.
-
Reduce Waste – Eliminate all activities that don't add value throughout the supply chain.
-
Create Flow - Make sure work runs smoothly without interruptions.
-
Standardize & simplify - Make processes consistent and repeatable.
-
Build Relationships- Develop personal relationships with both internal as well as external stakeholders.
Lean manufacturing is not a new concept, but it has been gaining popularity over the last few years due to a renewed interest in the economy following the global financial crisis of 2008. Many businesses are now using lean manufacturing to improve their competitiveness. Many economists believe lean manufacturing will play a major role in economic recovery.
Lean manufacturing is becoming a popular practice in automotive. It has many advantages. These include higher customer satisfaction, lower inventory levels, lower operating expenses, greater productivity, and improved overall safety.
The principles of lean manufacturing can be applied in almost any area of an organization. However, it is particularly useful when applied to the production side of an organization because it ensures that all steps in the value chain are efficient and effective.
There are three main types:
-
Just-in Time Manufacturing: This lean manufacturing method is commonly called "pull systems." JIT is a method in which components are assembled right at the moment of use, rather than being manufactured ahead of time. This method reduces lead times, increases availability, and decreases inventory.
-
Zero Defects Manufacturing: ZDM ensures that no defective units leave the manufacturing plant. You should repair any part that needs to be repaired during an assembly line. This is also true for finished products that require minor repairs before shipping.
-
Continuous Improvement (CI: Continuous improvement aims to increase the efficiency of operations by constantly identifying and making improvements to reduce or eliminate waste. Continuous improvement involves continuous improvement of processes and people as well as tools.