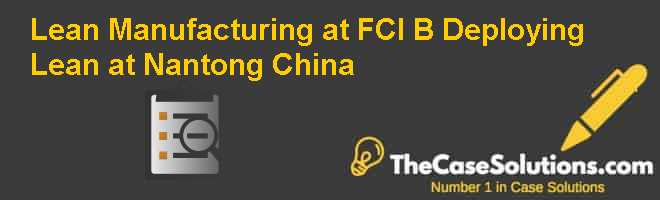
It is much more than simply installing technology. It's about changing the mindset of your factory and adapting to changes. You can help your customers and your business in a new stage of manufacturing with the right technology.
The first step in achieving your goals is to define what you are looking for. You might want to build a smart plant to react to sudden changes in demand. A smart factory can also be built to support global supply chain partners. Perhaps you want to create a factory that can respond to an industry that heavily relies on manual labor. No matter what your goal, the next step in building an ecosystem to support it is to create that ecosystem.
A lack of internet connectivity is one major obstacle to creating a smart factory. It can be hard to overcome this obstacle if you have outdated machinery and equipment. It may be difficult for you to access the information needed on your equipment and machines. The study found that 33% of smart factory leaders said that a lack of IT infrastructure was a significant impediment to a smart factory.
Technology is the next most important factor. There are many advanced manufacturing technologies that are currently available. These technologies can be used to improve your quality and productivity. These technologies can also be used to increase the value of your plant.
You should also consider people. You need to make investments in the right skill sets at the right times. You need to have the right people in place, as well as a sophisticated talent strategy. You should ensure that there is a clear scope to work and that all parties agree on the priorities and timelines. It is important to ensure that the right people work on the right projects.
Process is the third important factor. You must ensure that your applications are able connect to a networking. This will allow you to share information between other factory systems and processes. Lastly, you need to make sure that you have data and analytics in place. This will make it possible to make data-driven choices and to self-heal.
People are the fourth most crucial factor. Your executive team must be committed to the initiative. It is helpful to have someone who can coordinate and align efforts with multiple vendors. It is also a good idea to have a convener who can coordinate and align efforts across multiple vendors.
Security is fifth on the list. There are new technologies that reduce the chance of cyberattacks within manufacturing environments. It is important to have a cybersecurity strategy. You also need to ensure that you have a cybersecurity strategy that is ongoing.
Finally, you need to consider how you will connect your machines and equipment. You can continue to use your existing solutions but you may want to consider newer options. This will enable you to create data sets that can be used to support smart factory initiatives.
FAQ
What is the distinction between Production Planning or Scheduling?
Production Planning (PP), also known as forecasting and identifying production capacities, is the process that determines what product needs to be produced at any particular time. Forecasting and identifying production capacity are two key elements to this process.
Scheduling is the process of assigning specific dates to tasks so they can be completed within the specified timeframe.
Is automation important in manufacturing?
Automation is important not only for manufacturers but also for service providers. It allows them to offer services faster and more efficiently. In addition, it helps them reduce costs by reducing human errors and improving productivity.
How does a production planner differ from a project manager?
The difference between a product planner and project manager is that a planer is typically the one who organizes and plans the entire project. A production planner, however, is mostly involved in the planning stages.
Statistics
- Many factories witnessed a 30% increase in output due to the shift to electric motors. (en.wikipedia.org)
- In 2021, an estimated 12.1 million Americans work in the manufacturing sector.6 (investopedia.com)
- You can multiply the result by 100 to get the total percent of monthly overhead. (investopedia.com)
- According to the United Nations Industrial Development Organization (UNIDO), China is the top manufacturer worldwide by 2019 output, producing 28.7% of the total global manufacturing output, followed by the United States, Japan, Germany, and India.[52][53] (en.wikipedia.org)
- (2:04) MTO is a production technique wherein products are customized according to customer specifications, and production only starts after an order is received. (oracle.com)
External Links
How To
How to Use Lean Manufacturing in the Production of Goods
Lean manufacturing (or lean manufacturing) is a style of management that aims to increase efficiency, reduce waste and improve performance through continuous improvement. It was first developed in Japan in the 1970s/80s by Taiichi Ahno, who was awarded the Toyota Production System (TPS), award from KanjiToyoda, the founder of TPS. Michael L. Watkins published the book "The Machine That Changed the World", which was the first to be published about lean manufacturing.
Lean manufacturing, often described as a set and practice of principles, is aimed at improving the quality, speed, cost, and efficiency of products, services, and other activities. It emphasizes the elimination and minimization of waste in the value stream. Just-in-time (JIT), zero defect (TPM), and 5S are all examples of lean manufacturing. Lean manufacturing focuses on eliminating non-value-added activities such as rework, inspection, and waiting.
Lean manufacturing can help companies improve their product quality and reduce costs. Additionally, it helps them achieve their goals more quickly and reduces employee turnover. Lean manufacturing can be used to manage all aspects of the value chain. Customers, suppliers, distributors, retailers and employees are all included. Lean manufacturing can be found in many industries. Toyota's philosophy is the foundation of its success in automotives, electronics and appliances, healthcare, chemical engineers, aerospace, paper and food, among other industries.
Five principles are the basis of lean manufacturing:
-
Define Value - Identify the value your business adds to society and what makes you different from competitors.
-
Reduce waste - Stop any activity that isn't adding value to the supply chains.
-
Create Flow. Ensure that your work is uninterrupted and flows seamlessly.
-
Standardize and simplify - Make your processes as consistent as possible.
-
Develop Relationships: Establish personal relationships both with internal and external stakeholders.
Lean manufacturing, although not new, has seen renewed interest in the economic sector since 2008. Many businesses have adopted lean manufacturing techniques to help them become more competitive. According to some economists, lean manufacturing could be a significant factor in the economic recovery.
Lean manufacturing is becoming a popular practice in automotive. It has many advantages. These benefits include increased customer satisfaction, reduced inventory levels and lower operating costs.
Any aspect of an enterprise can benefit from Lean manufacturing. It is especially useful for the production aspect of an organization, as it ensures that every step in the value chain is efficient and effective.
There are three main types:
-
Just-in Time Manufacturing: This lean manufacturing method is commonly called "pull systems." JIT means that components are assembled at the time of use and not manufactured in advance. This approach aims to reduce lead times, increase the availability of parts, and reduce inventory.
-
Zero Defects Manufacturing (ZDM),: ZDM is a system that ensures no defective units are left the manufacturing facility. You should repair any part that needs to be repaired during an assembly line. This is true even for finished products that only require minor repairs prior to shipping.
-
Continuous Improvement (CI: Continuous improvement aims to increase the efficiency of operations by constantly identifying and making improvements to reduce or eliminate waste. Continuous improvement involves continuous improvement of processes and people as well as tools.