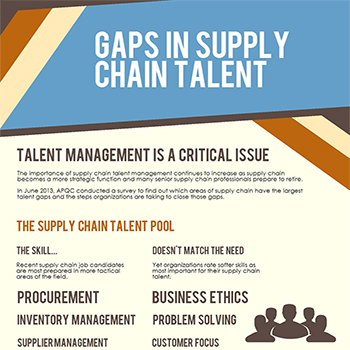
Founded in 1898, the National Association of Manufacturers (NAM) is a trade association that represents nearly 14,000 member companies from every industrial sector in the U.S. NAM works to ensure the success of 12 million American manufacturers. It works to promote new industries and increase awareness of manufacturing. NAM has offices throughout the United States.
NAM is the nation’s most prominent advocate for manufacturers. Its members are small and medium-sized manufacturing businesses. It promotes new industries and advanced manufacturing. NAM is also a key player in Washington's policymaking. Its executives strive to reduce regulatory burden and promote trade and export. Washington, D.C. is the headquarters of NAM. The NAM's executive team is skilled in developing and researching products and services that increase the manufacturers' competitiveness.
Texas Association of Manufacturers (TAM), praised the 84th Legislature's passing of SB 1. The bill will provide broad tax relief to Texas businesses, which will help them grow. Senator Bill Nelson is the sponsor of the bill, as well as Representative Bill Bonnen. The legislation also addresses the state's tax code, including Chapter 312, which allows temporary tax exemptions.
Texas' aerospace and aviation manufacturing sector makes up a significant part of its economy. It contributes almost 49 billion dollars to the state's economy and creates nearly 200,000 jobs. To maintain its strong state position, the industry must be competitive. TSCA reform is essential to help the sector remain competitive and grow. AMT's USMTO program offers assistance to its member companies to establish Brazil operations. Its USMTO program reported more than $400 million in manufacturing orders in May.
The Texas aerospace and aircraft manufacturing sector needs to remain competitive in order to continue to generate revenue and create jobs in Texas. The sector's efforts have been important in strengthening Texas' manufacturing sector.
Texas Association of Manufacturers is in favor of Chapter 312 of Texas Tax Code being renewed. The Association also supports payments under the Operating Reserve Demand Curve (ORDC). These payments enable manufacturers to pay dispatchable generation. This is vital for the safety of the electric grid. The ORDC payments have been expanded after Winter Storm Uri and because of changes to the Public Utility Commission's "phase one" operations.
AMT is one among the top trade associations in America. It has offices in more than 30 cities across the United States. Its senior executives have extensive experience in both public and private policy. Its mission is to promote advanced manufacturing and technology. It supports regulatory convergence between the U.S. and the European Union. It promotes and protects industrial manufacturers. It has created several industry-specific committees including one for small- and medium-sized companies. It promotes technology, innovation, and entrepreneurship.
AMT's new video introduces "MT Ambassadors," young professionals who educate others about manufacturing careers. The USMTO program is promoted by the organization, which allows member companies to visit Brazil. The Top Shops conference, and Top Shops programs, help manufacturers to benchmark their business and find opportunities. The Association for Manufacturing Technology works together with the association to promote interoperability among manufacturing systems. Its MTConnect Program improves the ability for manufacturers to gather and transmit data across all manufacturing technologies.
FAQ
What is the role of a production manager?
Production planners make sure that every aspect of the project is delivered on-time, within budget, and within schedule. They make sure that the product and services meet client expectations.
How can we reduce manufacturing overproduction?
In order to reduce excess production, you need to develop better inventory management methods. This would reduce the amount of time spent on unnecessary activities such as purchasing, storing, and maintaining excess stock. This would allow us to use our resources for more productive tasks.
One way to do this is to adopt a Kanban system. A Kanban Board is a visual display that tracks work progress. In a Kanban system, work items move through a sequence of states until they reach their final destination. Each state represents an individual priority level.
For instance, when work moves from one stage to another, the current task is complete enough to be moved to the next stage. If a task is still in its beginning stages, it will continue to be so until it reaches the end.
This allows you to keep work moving along while making sure that no work gets neglected. With a Kanban board, managers can see exactly how much work is being done at any given moment. This information allows them to adjust their workflow based on real-time data.
Lean manufacturing is another way to manage inventory levels. Lean manufacturing focuses on eliminating waste throughout the entire production chain. Anything that does nothing to add value to a product is waste. The following are examples of common waste types:
-
Overproduction
-
Inventory
-
Packaging not required
-
Exceed materials
By implementing these ideas, manufacturers can improve efficiency and cut costs.
What are the 7 Rs of logistics?
The acronym 7R's of Logistic is an acronym that stands for seven fundamental principles of logistics management. It was developed by the International Association of Business Logisticians (IABL) and published in 2004 as part of its "Seven Principles of Logistics Management" series.
The acronym consists of the following letters:
-
Responsive - ensure all actions are legal and not harmful to others.
-
Reliable: Have faith in your ability or the ability to honor any promises made.
-
Reasonable - use resources efficiently and don't waste them.
-
Realistic - consider all aspects of operations, including cost-effectiveness and environmental impact.
-
Respectful – Treat others fairly and equitably.
-
Resourceful - look for opportunities to save money and increase productivity.
-
Recognizable - provide customers with value-added services.
Statistics
- According to a Statista study, U.S. businesses spent $1.63 trillion on logistics in 2019, moving goods from origin to end user through various supply chain network segments. (netsuite.com)
- (2:04) MTO is a production technique wherein products are customized according to customer specifications, and production only starts after an order is received. (oracle.com)
- Job #1 is delivering the ordered product according to specifications: color, size, brand, and quantity. (netsuite.com)
- You can multiply the result by 100 to get the total percent of monthly overhead. (investopedia.com)
- In the United States, for example, manufacturing makes up 15% of the economic output. (twi-global.com)
External Links
How To
How to Use 5S to Increase Productivity in Manufacturing
5S stands as "Sort", Set In Order", Standardize", Separate" and "Store". The 5S methodology was developed at Toyota Motor Corporation in 1954. This methodology helps companies improve their work environment to increase efficiency.
This approach aims to standardize production procedures, making them predictable, repeatable, and easily measurable. This means that tasks such as cleaning, sorting, storing, packing, and labeling are performed daily. These actions allow workers to perform their job more efficiently, knowing what to expect.
Five steps are required to implement 5S: Sort, Set In Order, Standardize. Separate. Each step requires a different action, which increases efficiency. For example, when you sort things, you make them easy to find later. When you arrange items, you place them together. Once you have separated your inventory into groups and organized them, you will store these groups in easily accessible containers. Finally, when you label your containers, you ensure everything is labeled correctly.
This requires employees to critically evaluate how they work. Employees must understand why they do certain tasks and decide if there's another way to accomplish them without relying on the old ways of doing things. They will need to develop new skills and techniques in order for the 5S system to be implemented.
The 5S method not only increases efficiency but also boosts morale and teamwork. They are more motivated to achieve higher efficiency levels as they start to see improvement.