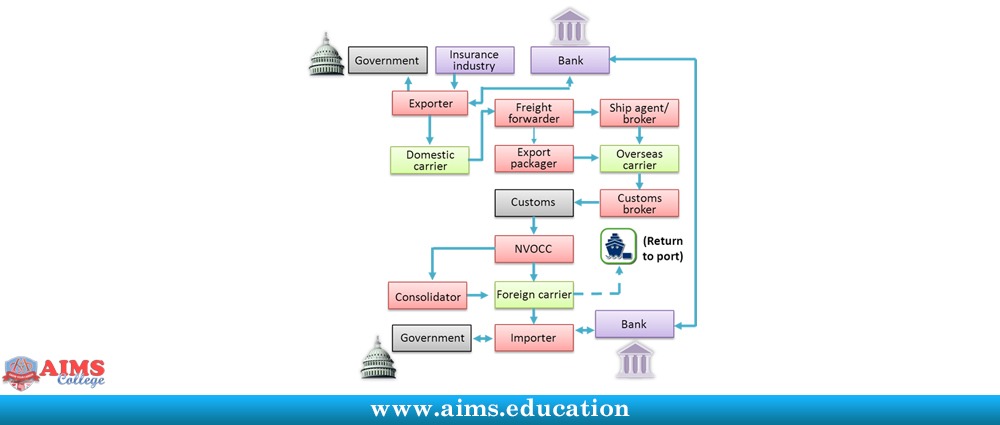
The employment sector offers many jobs for individuals as well as businesses. Due to the fact that many employers prefer using outside agencies to screen prospective employees, the employment sector is expected to continue growing. Many of these agencies work online, which reduces their administrative overhead and staffing requirements. They are also vulnerable to competition from job postings found on employer Web pages and job-matching websites run by educational institutions and professional associations.
The employment services sector has many jobs
A variety of occupations make up the employment services industry. These professionals have specialized knowledge in many areas, including executive search, placement, recruiting, and placement. They also provide temporary staff for clients. In addition, these professionals can provide human resources services. Companies located in different regions of the world dominate employment services.
This industry employs millions, with a wide range of education, experience, as well as skills. Occupations range from secretary to computer systems analyst, and from general laborer to nurse. Some of the positions in the industry can be permanent, including those as job interviewers, office managers, and marketing representatives.
Labor market
The labor market is a place where the supply and demand of jobs meet. Employers pay employees to perform services. The worker can be either an individual or an organisation, while the employer could be any person looking for workers. In this way, workers and employers are like sellers and buyers.
There are several federal agencies that collect and analyze data on the labor force. For example, the Bureau of Labor Statistics collects and analyses data on unemployment, wages, and employment. It also analyzes data regarding industrial relations, occupational safety, family expenditure, and other related topics. These data can be used to help economists analyze trends in the labor marketplace.
Size of industry
The number of workers employed in an industry determines its size. There are approximately 6.1 million employers in the United States. Large companies are the biggest employers. The number of employees employed by small businesses is lower. According to the U.S. Census Bureau 99.7% percent of total businesses are smaller than 500 employees. Even though smaller industries may not employ a lot of people, they could be able to create new jobs.
Industry's impact on recession
When the economy is in recession, the employment industry will experience a decline in numbers of workers. As a consequence, unemployment rates are likely to rise. Also, the duration of unemployment will rise. There will be a loss of employment in every sector. However, these losses will vary in severity. Every sector lost jobs during the Great Recession. However, the extent of these job losses varied for different sectors.
The resulting reductions in payroll will be reflected in the premium. In the Mild recession scenario, the increase in premiums will be 1%. The increase in premiums will be greater in the Severe recession. The decrease in payrolls from Goods & Services will be about half as big as the other industries. As a consequence, premiums for Goods & Services should increase.
Impact of COVID-19 pandemic (coronavirus), on the industrial sector
Industries that have a high proportion of older workers were most affected by the COVID-19 (coronavirus epidemic) on the employment industry. The largest percentage of job losses were seen in professional and business services, followed by health care and social assistance, and manufacturing. Younger workers suffered more job losses, but not in a significant way. It was more likely that younger workers would be employed in industries that had more face to face contact.
Both high-paying and lower-paying jobs were affected by this pandemic. Despite most people losing their jobs due to the virus, there were fewer people working in these areas than other sectors. Many workers in information and management could work from home, which helped them recover most of their lost jobs. The worst impact on employment was felt in higher-paying industries. In the second quarter of 2019, the number of people working in those sectors was 15% lower than in the same period in 2018.
FAQ
What skills should a production planner have?
Production planners must be flexible, organized, and able handle multiple tasks. Also, you must be able and willing to communicate with clients and coworkers.
What are the responsibilities of a logistic manager?
Logistics managers are responsible for ensuring that all goods arrive in perfect condition and on time. This is done using his/her knowledge of the company's products. He/she must also ensure sufficient stock to meet the demand.
What is the job of a production plan?
Production planners ensure all aspects of the project are delivered within time and budget. They ensure that the product or service is of high quality and meets client requirements.
Statistics
- Job #1 is delivering the ordered product according to specifications: color, size, brand, and quantity. (netsuite.com)
- [54][55] These are the top 50 countries by the total value of manufacturing output in US dollars for its noted year according to World Bank.[56] (en.wikipedia.org)
- Many factories witnessed a 30% increase in output due to the shift to electric motors. (en.wikipedia.org)
- According to the United Nations Industrial Development Organization (UNIDO), China is the top manufacturer worldwide by 2019 output, producing 28.7% of the total global manufacturing output, followed by the United States, Japan, Germany, and India.[52][53] (en.wikipedia.org)
- In 2021, an estimated 12.1 million Americans work in the manufacturing sector.6 (investopedia.com)
External Links
How To
How to Use the 5S to Increase Productivity In Manufacturing
5S stands to stand for "Sort", “Set In Order", “Standardize", and "Store". Toyota Motor Corporation created the 5S methodology in 1954. It allows companies to improve their work environment, thereby achieving greater efficiency.
The idea behind standardizing production processes is to make them repeatable and measurable. This means that every day tasks such cleaning, sorting/storing, packing, and labeling can be performed. These actions allow workers to perform their job more efficiently, knowing what to expect.
Implementing 5S involves five steps: Sort, Set in Order, Standardize Separate, Store, and Each step has a different action and leads to higher efficiency. For example, when you sort things, you make them easy to find later. Once you have placed items in an ordered fashion, you will put them together. After you have divided your inventory into groups you can store them in easy-to-reach containers. Labeling your containers will ensure that everything is correctly labeled.
Employees will need to be more critical about their work. Employees must understand why they do certain tasks and decide if there's another way to accomplish them without relying on the old ways of doing things. In order to use the 5S system effectively, they must be able to learn new skills.
In addition to increasing efficiency, the 5S method also improves morale and teamwork among employees. They feel more motivated to work towards achieving greater efficiency as they see the results.