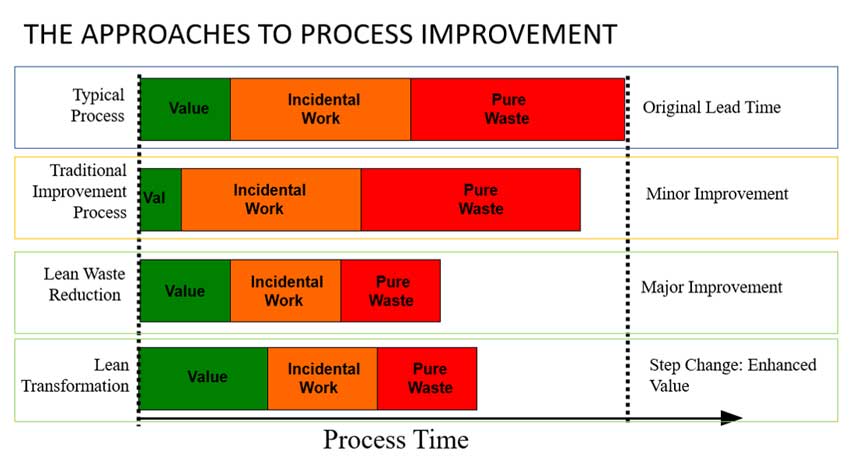
A drafter is someone who has a good understanding of technical details and can translate designs into drawings. They must also be able work well with others to achieve the best results. They may also need to learn how to read engineering plans and how to work with specific software programs. They might also need an understanding of engineering formulas that can be used to calculate measurement.
Drafters usually work for engineering and architecture firms. They are responsible for creating plans for buildings, structures, as well as other products, using computer-aided engineering (CAD) software. These professionals often work independently on projects, but they also work in teams to produce innovative designs. They often work full-time, but they also can take on a variety of jobs. Depending on the company they work for, they may be required to work overtime to meet deadlines.
Most drafters obtain an associate's degree from a technical or community college in drafting. A university can offer a 4-year program that will allow them to continue their education. You may be able transfer your degree depending on what course you take.
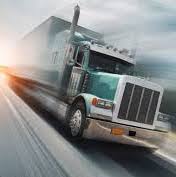
Drafters may need to have a degree and professional experience. In order to gain real-world experience, they may be required to do an internship at a company. This experience can help drafters land a job. To demonstrate their drafting abilities, they may be required to submit a portfolio.
Also, drafters can earn certifications. American Design Drafting Association, (ADDA), offers certification tests that test drafting knowledge. These tests can be used to evaluate your ability to tolerate and design geometrically. Many certifications are valid for three years and require candidates to pass updated exams. The ADDA certifies a variety of drafting specialties.
Drafters usually work in construction, engineering, or manufacturing companies. They might also be employed in factories or with electricity. They may also work on a regular schedule, but some drafters work more than 40 hours a week. They should also know how to manage their time and use computer-aided design (CAD).
Drafters can take advantage of a trend where more businesses are using technology to improve efficiency. To stay competitive, they may need to learn CAD and other programming languages. Those who are interested in becoming a drafter may want to consider earning a master's degree. A master's degree gives you an edge over other candidates for getting hired. They will also be better qualified to present technical information for clients.
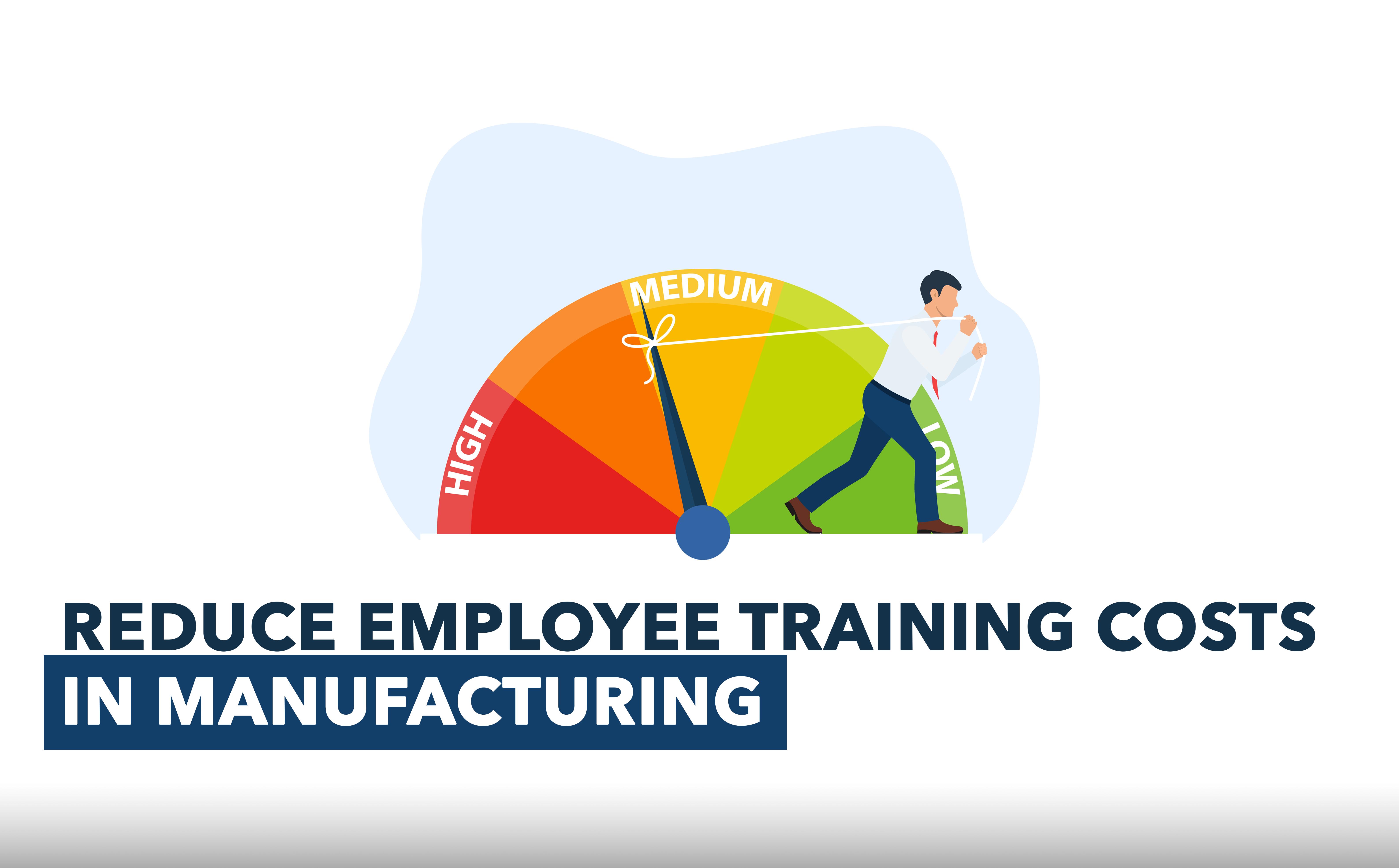
Assisting professional drafters is another option for drafters. To gain experience, drafters may volunteer to help with community projects. Before you sign up for courses, make sure you know what kind of projects you are interested. Some clients prefer drawing in pencil while others prefer drawings that are computer-generated.
Draft technicians can gain practical experience after graduating high school. They can enroll in drafting classes at technical institutes to get professional experience. They should also pay special attention to math and computer classes.
FAQ
What is the difference between manufacturing and logistics
Manufacturing refers the process of producing goods from raw materials through machines and processes. Logistics manages all aspects of the supply chain, including procurement, production planning and distribution, inventory control, transportation, customer service, and transport. As a broad term, manufacturing and logistics often refer to both the creation and delivery of products.
What are the 7 Rs of logistics management?
The acronym 7R's of Logistic is an acronym that stands for seven fundamental principles of logistics management. It was developed by International Association of Business Logisticians (IABL), and published as part of their "Seven Principles of Logistics Management Series" in 2004.
The acronym is made up of the following letters:
-
Responsible - ensure that all actions taken are within legal requirements and are not harmful to others.
-
Reliable - Have confidence in your ability to fulfill all of your commitments.
-
Use resources effectively and sparingly.
-
Realistic - Take into consideration all aspects of operations including cost-effectiveness, environmental impact, and other factors.
-
Respectful - show respect and treat others fairly and fairly
-
Resourceful - look for opportunities to save money and increase productivity.
-
Recognizable provides value-added products and services to customers
What does warehouse refer to?
A warehouse is an area where goods are stored before being sold. You can have it indoors or outdoors. In some cases it could be both indoors and outdoors.
How can manufacturing efficiency improved?
First, determine which factors have the greatest impact on production time. Then we need to find ways to improve these factors. You can start by identifying the most important factors that impact production time. Once you have identified the factors, then try to find solutions.
How does a Production Planner differ from a Project Manager?
The major difference between a Production Planner and a Project Manager is that a Project Manager is often the person responsible for organizing and planning the entire project. While a Production Planner is involved mainly in the planning stage,
Statistics
- You can multiply the result by 100 to get the total percent of monthly overhead. (investopedia.com)
- It's estimated that 10.8% of the U.S. GDP in 2020 was contributed to manufacturing. (investopedia.com)
- (2:04) MTO is a production technique wherein products are customized according to customer specifications, and production only starts after an order is received. (oracle.com)
- According to the United Nations Industrial Development Organization (UNIDO), China is the top manufacturer worldwide by 2019 output, producing 28.7% of the total global manufacturing output, followed by the United States, Japan, Germany, and India.[52][53] (en.wikipedia.org)
- Job #1 is delivering the ordered product according to specifications: color, size, brand, and quantity. (netsuite.com)
External Links
How To
How to Use Just-In-Time Production
Just-intime (JIT), a method used to lower costs and improve efficiency in business processes, is called just-in-time. It's a way to ensure that you get the right resources at just the right time. This means you only pay what you use. Frederick Taylor developed the concept while working as foreman in early 1900s. After observing how workers were paid overtime for late work, he realized that overtime was a common practice. He decided that workers would be more productive if they had enough time to complete their work before they started to work.
JIT teaches you to plan ahead and prepare everything so you don’t waste time. Also, you should look at the whole project from start-to-finish and make sure you have the resources necessary to address any issues. You will have the resources and people to solve any problems you anticipate. This will ensure that you don't spend more money on things that aren't necessary.
There are different types of JIT methods:
-
Demand-driven: This type of JIT allows you to order the parts/materials required for your project on a regular basis. This will allow you to track how much material you have left over after using it. This will allow you to calculate how long it will take to make more.
-
Inventory-based: This type allows you to stock the materials needed for your projects ahead of time. This allows one to predict how much they will sell.
-
Project-driven: This means that you have enough money to pay for your project. You will be able to purchase the right amount of materials if you know what you need.
-
Resource-based JIT: This is the most popular form of JIT. You allocate resources based on the demand. For example, if there is a lot of work coming in, you will have more people assigned to them. You'll have fewer orders if you have fewer.
-
Cost-based: This is a similar approach to resource-based but you are not only concerned with how many people you have, but also how much each one costs.
-
Price-based: This is very similar to cost-based, except that instead of looking at how much each individual worker costs, you look at the overall price of the company.
-
Material-based: This is quite similar to cost-based, but instead of looking at the total cost of the company, you're concerned with how much raw materials you spend on average.
-
Time-based JIT: This is another variant of resource-based JIT. Instead of focusing only on how much each employee is costing, you should focus on how long it takes to complete your project.
-
Quality-based JIT: Another variation on resource-based JIT. Instead of thinking about the cost of each employee or the time it takes to produce something, you focus on how good your product quality.
-
Value-based: This is one of the newest forms of JIT. In this scenario, you're not concerned about how products perform or whether customers expect them to meet their expectations. Instead, you are focused on adding value to the marketplace.
-
Stock-based. This method is inventory-based and focuses only on the actual production at any given point. It is used when production goals are met while inventory is kept to a minimum.
-
Just-in-time planning (JIT): This is a combination JIT and supply-chain management. It is the process of scheduling components' delivery as soon as they have been ordered. It's important because it reduces lead times and increases throughput.