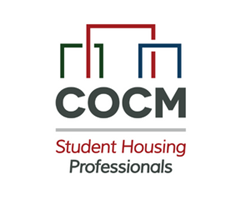
Strategic supply chain management requires a firm's ability to adapt to market demands and remain competitive. It is important to consider many factors when choosing the best strategy. These factors include cost-effectiveness, competitive positioning, customer service, and cost-effectiveness. Additionally, the company must be ready to invest to improve its manufacturing infrastructure in order to adapt to changes in the marketplace.
Competitive positioning
To be competitive in a marketplace, a brand must have a competitive positioning. It involves paying attention to customer preferences and needs, and current trends. Competitive positioning is a way for a brand to stand out from its competitors and increase its sales. Moreover, it helps a brand to solve customer's problems, which helps it to increase its value.
The first step in a successful positioning strategy is to do thorough market research. The first step is to estimate market size and opportunities. This can be accomplished by collecting data from various sources, such as industry reports, external market data, and the company's own experiences in the market. This information allows you to estimate the number of customers and potential sales. It can also help determine the market's growth and stability.
Cost-effectiveness
A strategic supply chain can help retailers as well as manufacturers become more competitive. It allows firms to see their entire supply chain and develop data-driven demand forecasts. It will allow companies to calculate the cost of investment and look at different "what-if" scenarios.
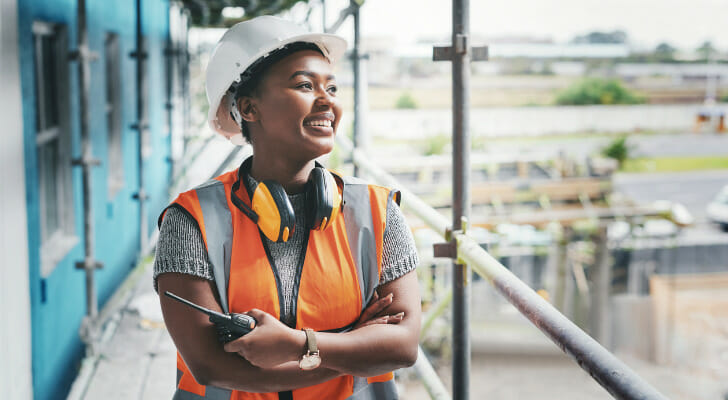
It can also help businesses make more informed decisions and increase ROI. As such, it is an essential tool in today's data-driven economy. It helps decision-makers identify opportunities and assess their impact to ensure that they can balance costs with benefits, and help them thrive in the global economic system.
Customer service
Maximizing customer services is one of the key aspects of strategic supply-chain management. This aspect is essential to the success your business. It is essential to your success. Your competition will have an advantage. Only a very small percentage of companies reach the top in satisfying customers' needs. Recent studies have shown that customers are dissatisfied with their service experience and the concept of customer service is often misunderstood and poorly defined.
Customers are satisfied when they receive excellent customer service. These key elements are product quality, price, and speed of customer service. In short, customer service involves planning both in the transactional and pretransaction stages.
Manufacturing infrastructure
The critical component of strategic supply chain management is the manufacturing infrastructure. It helps ensure the availability of local industrial resources. This infrastructure includes all products and personnel that are part of a company’s supply system. This infrastructure allows for both vendor-managed as well as on-hand inventory. It also ensures there is sufficient manufacturing capacity.
Numerous studies have shown significant savings from improving manufacturing infrastructure. Improved logistics, materials sourcing and manufacturing capabilities can improve the efficiency of supply chains. Many companies don't know that supply chains are much more than operational processes.
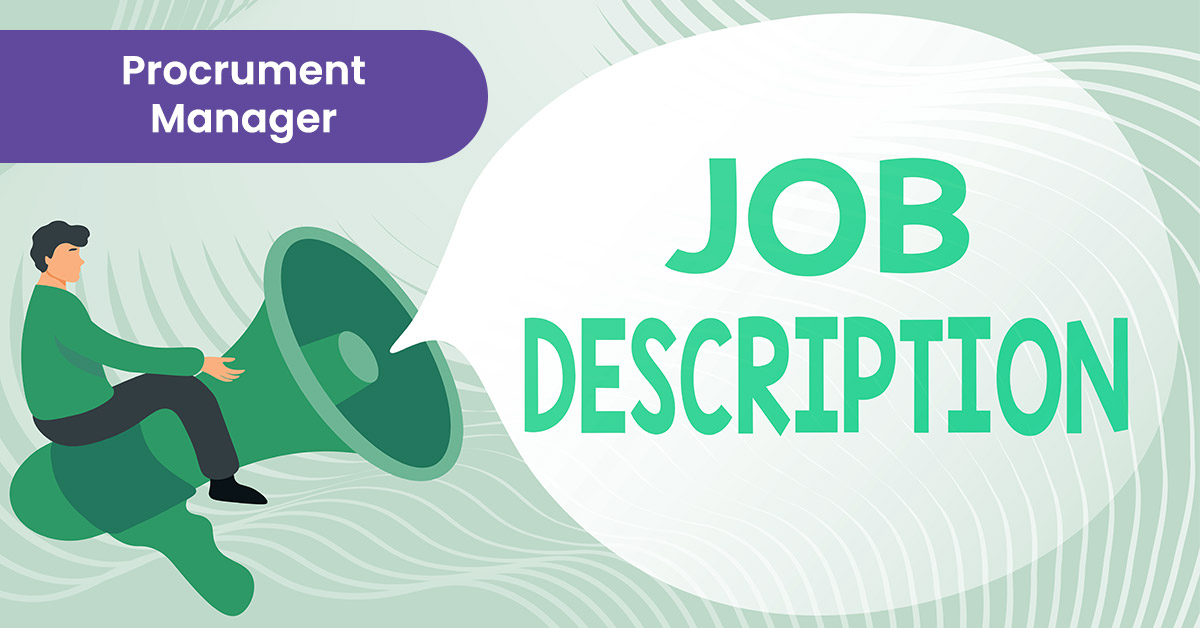
Technology
It is becoming increasingly clear that technology is a crucial part of a business's success. A more flexible and resilient supply network is essential in an uncertain business environment. Technology-enabled supply chain management can lower costs by up to 20%, increase EBITDA by upto 10%, and improve customer service by upto 30%. These new approaches to supply chain management are at the heart of new business models.
Supply-chain technology adoption was a long-term, multimillion-dollar investment that required drastic changes throughout an organization. However, three new technologies are making it easier for companies to experiment with new strategies in an affordable, fast-paced environment. These technologies enable companies to quickly test new ideas, improve processes and make a difference. They allow businesses to reduce their risk by implementing them more precisely and in smaller areas.
FAQ
Is automation important in manufacturing?
Automation is essential for both manufacturers and service providers. It enables them to provide services faster and more efficiently. They can also reduce their costs by reducing human error and improving productivity.
What jobs are available in logistics?
There are different kinds of jobs available in logistics. Some of them are:
-
Warehouse workers – They load, unload and transport pallets and trucks.
-
Transport drivers - These are people who drive trucks and trailers to transport goods or perform pick-ups.
-
Freight handlers – They sort and package freight at warehouses.
-
Inventory managers: They are responsible for the inventory and management of warehouses.
-
Sales representatives: They sell products to customers.
-
Logistics coordinators - They plan and organize logistics operations.
-
Purchasing agents - They buy goods and services that are necessary for company operations.
-
Customer service representatives - Answer calls and email from customers.
-
Shippers clerks - They process shipping order and issue bills.
-
Order fillers: They fill orders based off what has been ordered and shipped.
-
Quality control inspectors – They inspect incoming and outgoing products to ensure that there are no defects.
-
Others - There is a variety of other jobs in logistics. These include transportation supervisors and cargo specialists.
What makes a production planner different from a project manger?
The main difference between a production planner and a project manager is that a project manager is usually the person who plans and organizes the entire project, whereas a production planner is mainly involved in the planning stage of the project.
Statistics
- According to the United Nations Industrial Development Organization (UNIDO), China is the top manufacturer worldwide by 2019 output, producing 28.7% of the total global manufacturing output, followed by the United States, Japan, Germany, and India.[52][53] (en.wikipedia.org)
- It's estimated that 10.8% of the U.S. GDP in 2020 was contributed to manufacturing. (investopedia.com)
- In the United States, for example, manufacturing makes up 15% of the economic output. (twi-global.com)
- Job #1 is delivering the ordered product according to specifications: color, size, brand, and quantity. (netsuite.com)
- According to a Statista study, U.S. businesses spent $1.63 trillion on logistics in 2019, moving goods from origin to end user through various supply chain network segments. (netsuite.com)
External Links
How To
How to Use Just-In-Time Production
Just-intime (JIT), a method used to lower costs and improve efficiency in business processes, is called just-in-time. This is where you have the right resources at the right time. This means that you only pay for what you actually use. The term was first coined by Frederick Taylor, who developed his theory while working as a foreman in the early 1900s. He observed how workers were paid overtime if there were delays in their work. He then concluded that if he could ensure that workers had enough time to do their job before starting to work, this would improve productivity.
The idea behind JIT is that you should plan ahead and have everything ready so you don't waste money. It is important to look at your entire project from beginning to end and ensure that you have enough resources to handle any issues that may arise. You will have the resources and people to solve any problems you anticipate. This way, you won't end up paying extra money for things that weren't really necessary.
There are many JIT methods.
-
Demand-driven: This is a type of JIT where you order the parts/materials needed for your project regularly. This will allow for you to track the material that you have left after using it. It will also allow you to predict how long it takes to produce more.
-
Inventory-based : You can stock the materials you need in advance. This allows one to predict how much they will sell.
-
Project-driven: This approach involves setting aside sufficient funds to cover your project's costs. Once you have an idea of how much material you will need, you can purchase the necessary materials.
-
Resource-based JIT: This is the most popular form of JIT. You allocate resources based on the demand. For instance, if you have a lot of orders coming in, you'll assign more people to handle them. If there aren't many orders, you will assign fewer people.
-
Cost-based : This is similar in concept to resource-based. But here, you aren't concerned about how many people your company has but how much each individual costs.
-
Price-based: This approach is very similar to the cost-based method except that you don't look at individual workers costs but the total cost of the company.
-
Material-based is an alternative to cost-based. Instead of looking at the total cost in the company, this method focuses on the average amount of raw materials that you consume.
-
Time-based JIT: A variation on resource-based JIT. Instead of focusing solely on the amount each employee costs, focus on how long it takes for the project to be completed.
-
Quality-based: This is yet another variation of resource-based JIT. Instead of looking at the labor costs and time it takes to make a product, think about its quality.
-
Value-based JIT: One of the most recent forms of JIT. In this instance, you are not concerned about the product's performance or meeting customer expectations. Instead, you're focused on how much value you add to the market.
-
Stock-based. This method is inventory-based and focuses only on the actual production at any given point. This is used to increase production and minimize inventory.
-
Just-intime (JIT), planning is a combination JIT management and supply chain management. This refers to the scheduling of the delivery of components as soon after they are ordered. It's important because it reduces lead times and increases throughput.