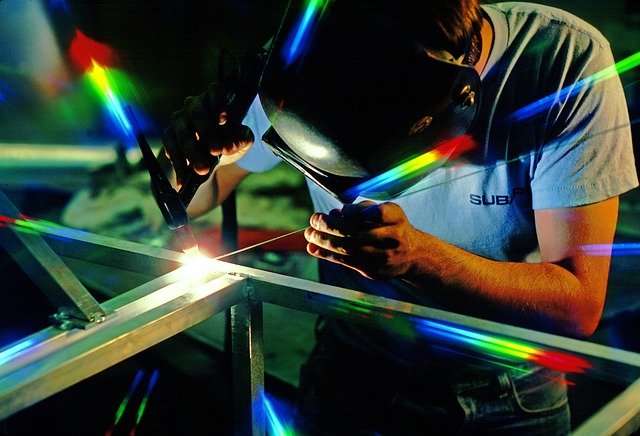
You will study microscopic forms and life processes as a microbiologist. This includes studying the inter- and intra-organism interactions. You'll be studying bacteria, fungi and parasites as microscopic organisms. These life forms are what make up our food, our bodies, and it's not surprising that microbiologists have such an important role.
Education necessary
Microbiologists study microscopic organisms and their processes. These microorganisms are bacteria, fungi, parasites, as well as algae. Microbiologists investigate how microscopic organisms behave and how they interact.
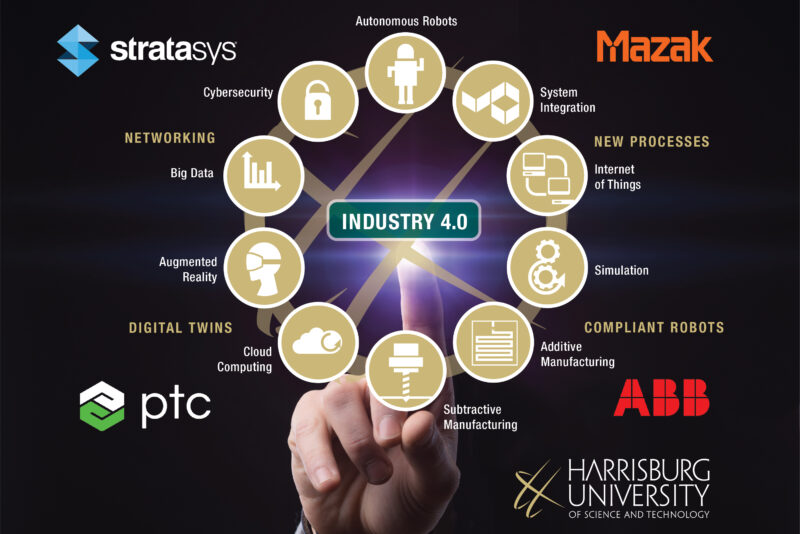
Microbiologists must be detail-oriented, able to present and write research findings and have the ability to organize them. They must also have the ability to manage and motivate their team. They often use complex mathematical equations to calculate results, so having a strong math background is necessary.
Job duties
Microbiologists are responsible for the identification and tracking of microorganisms within diverse environments. Their work may also aid in developing new medicines, vaccines, as well as ways of preventing disease. They oversee lab work, research, and create reports. To collect and analyze data, they use specialist microscopes and computer software. They are required to pay close attention to details, and must be able coordinate large research teams.
Microbiologists study microbes using a variety of analytical methods. Their work can be in a clinical laboratory or in an environmental setting. Environmental microbiologists research the interactions of microorganisms with soil and water. Industrial microbiologists investigate how microbes can help with crop growth and industrial processes. They may oversee the production of cheese or study the growth of bacteria in pipes.
Salary
In 2004, the median salary of a Microbiologist stood at $81,668. In 2021, this figure will rise to $121,130. Microbiologists have the option of working in traditional research or in scientific publishing, patent work, and pharmaceutical sales. There has been a steady rise in employment for microbiologists across the United States due to increased demand.
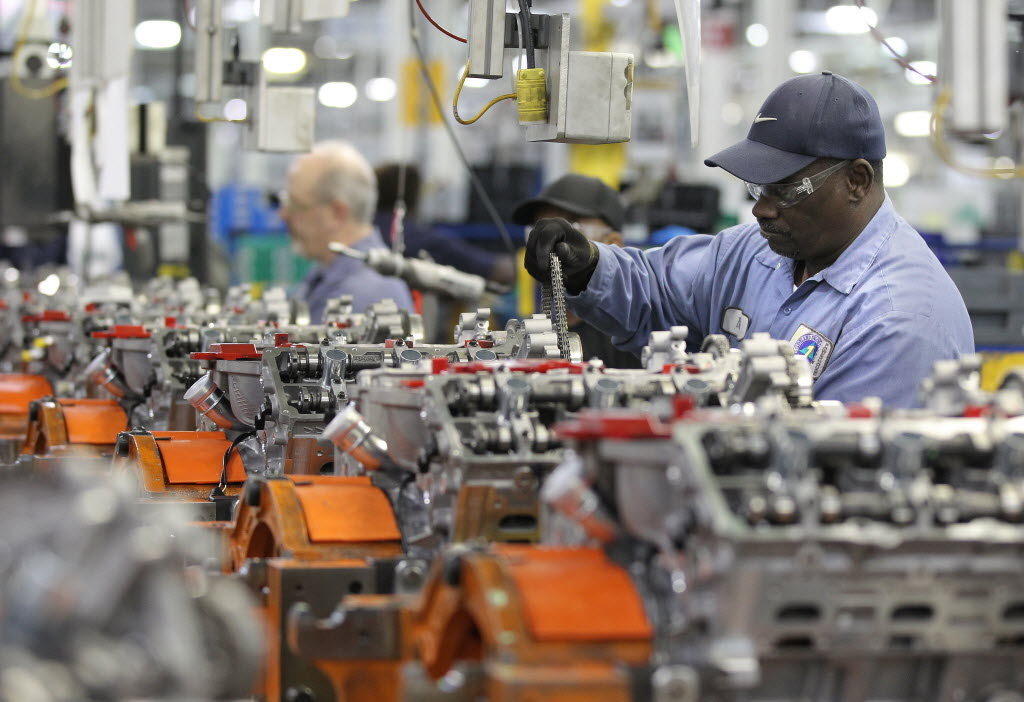
Most microbiologists work in research or labs, whether in an industrial setting or in academic institutions. Many of them work with dangerous organisms, so they must follow strict safety procedures to prevent contamination. Others visit work sites and environments to collect samples. Some people may even travel to collect samples.
FAQ
How can manufacturing avoid production bottlenecks
To avoid production bottlenecks, ensure that all processes run smoothly from the moment you receive your order to the time the product ships.
This includes planning for capacity requirements as well as quality control measures.
The best way to do this is to use continuous improvement techniques such as Six Sigma.
Six Sigma can be used to improve the quality and decrease waste in all areas of your company.
It's all about eliminating variation and creating consistency in work.
How does a Production Planner differ from a Project Manager?
The main difference between a production planner and a project manager is that a project manager is usually the person who plans and organizes the entire project, whereas a production planner is mainly involved in the planning stage of the project.
What is meant by manufacturing industries?
Manufacturing Industries are those businesses that make products for sale. Consumers are those who purchase these products. This is accomplished by using a variety of processes, including production, distribution and retailing. They make goods from raw materials with machines and other equipment. This includes all types manufactured goods such as clothing, building materials, furniture, electronics, tools and machinery.
What type of jobs is there in logistics
There are many jobs available in logistics. Some of them are:
-
Warehouse workers – They load and unload pallets and trucks.
-
Transportation drivers: They drive trucks and trailers and deliver goods and make pick-ups.
-
Freight handlers: They sort and package freight in warehouses.
-
Inventory managers: They are responsible for the inventory and management of warehouses.
-
Sales representatives: They sell products to customers.
-
Logistics coordinators are responsible for organizing and planning logistics operations.
-
Purchasing agents - They buy goods and services that are necessary for company operations.
-
Customer service representatives are available to answer customer calls and emails.
-
Ship clerks - They issue bills and process shipping orders.
-
Order fillers - They fill orders based on what is ordered and shipped.
-
Quality control inspectors – They inspect incoming and outgoing products to ensure that there are no defects.
-
Other - Logistics has many other job opportunities, including transportation supervisors, logistics specialists, and cargo specialists.
Are there ways to automate parts of manufacturing?
Yes! Yes! Automation has existed since ancient times. The wheel was invented by the Egyptians thousands of years ago. Today, robots assist in the assembly of lines.
Robotics is used in many manufacturing processes today. These include:
-
Assembly line robots
-
Robot welding
-
Robot painting
-
Robotics inspection
-
Robots that create products
There are many other examples of how manufacturing could benefit from automation. 3D printing, for example, allows us to create custom products without waiting for them to be made.
What is the best way to learn about manufacturing?
The best way to learn about manufacturing is through hands-on experience. However, if that's not possible, you can always read books or watch educational videos.
Is automation important for manufacturing?
Automation is important not only for manufacturers but also for service providers. They can provide services more quickly and efficiently thanks to automation. It reduces human errors and improves productivity, which in turn helps them lower their costs.
Statistics
- (2:04) MTO is a production technique wherein products are customized according to customer specifications, and production only starts after an order is received. (oracle.com)
- [54][55] These are the top 50 countries by the total value of manufacturing output in US dollars for its noted year according to World Bank.[56] (en.wikipedia.org)
- Job #1 is delivering the ordered product according to specifications: color, size, brand, and quantity. (netsuite.com)
- In the United States, for example, manufacturing makes up 15% of the economic output. (twi-global.com)
- You can multiply the result by 100 to get the total percent of monthly overhead. (investopedia.com)
External Links
How To
Six Sigma: How to Use it in Manufacturing
Six Sigma can be described as "the use of statistical process control (SPC), techniques to achieve continuous improvement." It was developed by Motorola's Quality Improvement Department at their plant in Tokyo, Japan, in 1986. Six Sigma's basic concept is to improve quality and eliminate defects through standardization. Many companies have adopted Six Sigma in recent years because they believe that there are no perfect products and services. Six Sigma seeks to reduce variation between the mean production value. If you take a sample and compare it with the average, you will be able to determine how much of the production process is different from the norm. If it is too large, it means that there are problems.
The first step toward implementing Six Sigma is understanding how variability works in your business. Once you have this understanding, you will need to identify sources and causes of variation. These variations can also be classified as random or systematic. Random variations occur when people make mistakes; systematic ones are caused by factors outside the process itself. You could consider random variations if some widgets fall off the assembly lines. It would be considered a systematic problem if every widget that you build falls apart at the same location each time.
Once you have identified the problem, you can design solutions. It might mean changing the way you do business or redesigning it entirely. You should then test the changes again after they have been implemented. If they didn't work, then you'll need to go back to the drawing board and come up with another plan.