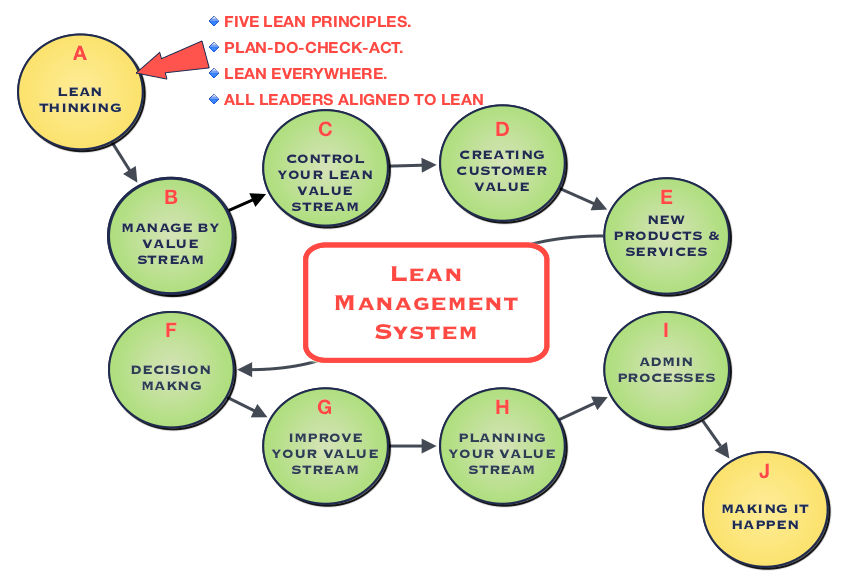
It is important to include the core qualifications section in your job description for environmental engineer. This will set out the minimum requirements required for the job in order to attract qualified candidates. This will streamline the process of recruiting and help to avoid applicants who are not qualified. A skills section is also a great way to keep the hiring process as smooth as possible. Continue reading for more information. This job description should be written in a professional, formal language to make the position stand out from others.
Qualifications
You might be considering changing careers to environmental engineering. Here are some details. This job involves the design and implementation of systems to control water and air quality, site remediation, as well as using pollution control technology. Often, this position requires collaboration with other professionals such as hazardous waste technicians and environmental specialists. They are often required to offer technical assistance in environmental litigation or remediation projects. They also monitor the progress of environmental improvement programs and contribute to the development of environmental journals.
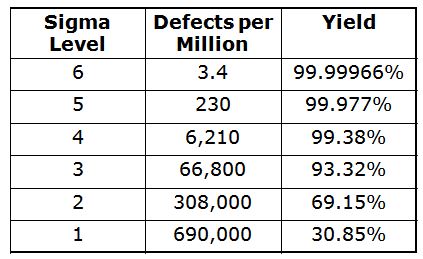
An environmental engineer's job requires extensive field work and office work. An environmental engineer may be responsible for field inspections, characterizing and evaluating materials, or working with subcontractors on site. Their job also requires extensive knowledge of environmental regulations and practices. They may also be required to maintain spreadsheets or other elements of reports. They can be involved in a variety of different projects and can progress from related occupations into their own field.
Responsibilities
An environmental engineer's responsibilities can be varied. Engineers may develop technologies to manage pollution or make recommendations about clean-up procedures. They may also be able to work with other experts such as lawyers or business professionals. They may also be responsible for administrative tasks, such as creating spreadsheets or other components of reports. Environmental engineers may advise federal, regional, and local government agencies in matters of environmental protection.
The role of an environmental engineering assistant includes the design and implementation plan and program development for conservation and management. They are responsible for assessing the impacts of any proposed commercial activity on land or other resources. They can also help with general administrative tasks like preparing project documentation, training staff, and budget implementation. An environmental engineer could also offer advice on environmental issues and best practice to policymakers.
Perspectives on employment
Positive employment prospects are available for environmental engineers. There is a strong demand for engineers who can help companies comply with environmental regulations, develop alternative methods to remove pollution, and manage the waste they produce. Environmental engineers will see a rise in demand due to the growing population and emphasis on prevention. As workers leave and move into other fields or retire, job opportunities will increase. This job is not for everyone. Here are some future jobs you might be interested in.
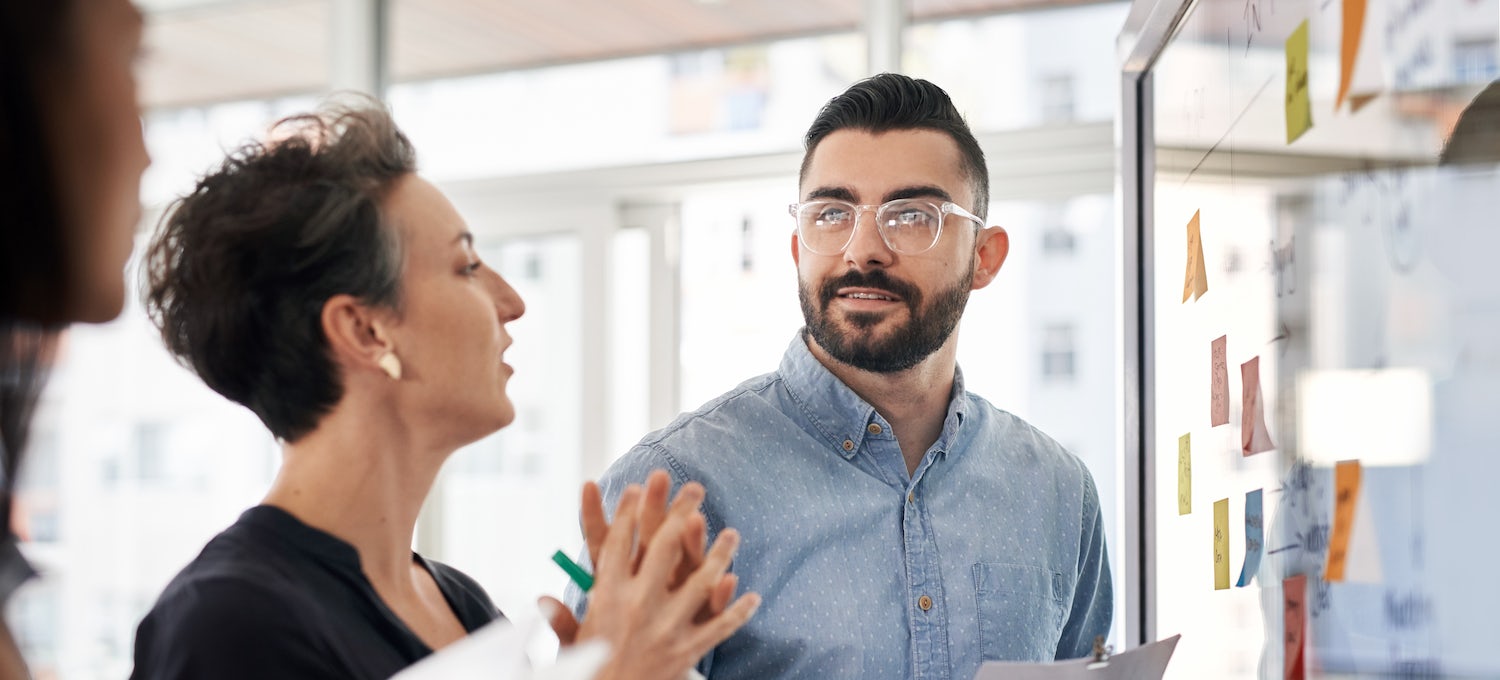
Many environmental engineers work in laboratories or offices. Many environmental engineers work indoors but some prefer to be outdoors or travel to construction sites. These professionals usually work a forty-hour week. Travel is required for some jobs, so your schedule could vary. It can be difficult, especially when deadlines are involved. As the environment is their primary concern, environmental engineers must be aware their limitations. This job is highly stressful and can require long hours.
FAQ
What are the goods of logistics?
Logistics are the activities involved in moving goods from point A to point B.
These include all aspects related to transport such as packaging, loading and transporting, storing, transporting, unloading and warehousing inventory management, customer service. Distribution, returns, recycling are some of the options.
Logisticians ensure that the right product reaches the right place at the right time and under safe conditions. Logisticians help companies improve their supply chain efficiency by providing information about demand forecasts and stock levels, production schedules, as well as availability of raw materials.
They coordinate with vendors and suppliers, keep track of shipments, monitor quality standards and perform inventory and order replenishment.
How important is automation in manufacturing?
Automating is not just important for manufacturers, but also for service providers. It allows them to offer services faster and more efficiently. They can also reduce their costs by reducing human error and improving productivity.
Can we automate some parts of manufacturing?
Yes! Yes! Automation has existed since ancient times. The Egyptians invented the wheel thousands of years ago. Today, robots assist in the assembly of lines.
Robotics is used in many manufacturing processes today. They include:
-
Robots for assembly line
-
Robot welding
-
Robot painting
-
Robotics inspection
-
Robots that create products
There are many other examples of how manufacturing could benefit from automation. 3D printing, for example, allows us to create custom products without waiting for them to be made.
What do we need to know about Manufacturing Processes in order to learn more about Logistics?
No. No. Knowing about manufacturing processes will help you understand how logistics works.
What are the 7 Rs of logistics?
The acronym 7R's of Logistic is an acronym that stands for seven fundamental principles of logistics management. It was developed by the International Association of Business Logisticians (IABL) and published in 2004 as part of its "Seven Principles of Logistics Management" series.
The acronym is composed of the following letters.
-
Responsible - ensure that all actions taken are within legal requirements and are not harmful to others.
-
Reliable - Have confidence in your ability to fulfill all of your commitments.
-
Be responsible - Use resources efficiently and avoid wasting them.
-
Realistic - Take into consideration all aspects of operations including cost-effectiveness, environmental impact, and other factors.
-
Respectful – Treat others fairly and equitably.
-
Responsive - Look for ways to save time and increase productivity.
-
Recognizable is a company that provides customers with value-added solutions.
What is meant by manufacturing industries?
Manufacturing Industries refers to businesses that manufacture products. Consumers are those who purchase these products. These companies employ many processes to achieve this purpose, such as production and distribution, retailing, management and so on. They create goods from raw materials, using machines and various other equipment. This includes all types manufactured goods such as clothing, building materials, furniture, electronics, tools and machinery.
Statistics
- In 2021, an estimated 12.1 million Americans work in the manufacturing sector.6 (investopedia.com)
- Many factories witnessed a 30% increase in output due to the shift to electric motors. (en.wikipedia.org)
- [54][55] These are the top 50 countries by the total value of manufacturing output in US dollars for its noted year according to World Bank.[56] (en.wikipedia.org)
- According to a Statista study, U.S. businesses spent $1.63 trillion on logistics in 2019, moving goods from origin to end user through various supply chain network segments. (netsuite.com)
- It's estimated that 10.8% of the U.S. GDP in 2020 was contributed to manufacturing. (investopedia.com)
External Links
How To
How to Use the Just In Time Method in Production
Just-intime (JIT), which is a method to minimize costs and maximize efficiency in business process, is one way. It allows you to get the right amount resources at the right time. This means that you only pay the amount you actually use. Frederick Taylor developed the concept while working as foreman in early 1900s. After observing how workers were paid overtime for late work, he realized that overtime was a common practice. He decided that workers would be more productive if they had enough time to complete their work before they started to work.
JIT is about planning ahead. You should have all the necessary resources ready to go so that you don’t waste money. It is important to look at your entire project from beginning to end and ensure that you have enough resources to handle any issues that may arise. You will have the resources and people to solve any problems you anticipate. This will prevent you from spending extra money on unnecessary things.
There are many types of JIT methods.
-
Demand-driven: This type of JIT allows you to order the parts/materials required for your project on a regular basis. This will allow for you to track the material that you have left after using it. You'll also be able to estimate how long it will take to produce more.
-
Inventory-based: This is a type where you stock the materials required for your projects in advance. This allows you to forecast how much you will sell.
-
Project-driven: This method allows you to set aside enough funds for your project. Once you have an idea of how much material you will need, you can purchase the necessary materials.
-
Resource-based JIT: This is the most popular form of JIT. You allocate resources based on the demand. For example, if there is a lot of work coming in, you will have more people assigned to them. If there aren't many orders, you will assign fewer people.
-
Cost-based: This is similar to resource-based, except that here you're not just concerned about how many people you have but how much each person costs.
-
Price-based pricing: This is similar in concept to cost-based but instead you look at how much each worker costs, it looks at the overall company's price.
-
Material-based: This is quite similar to cost-based, but instead of looking at the total cost of the company, you're concerned with how much raw materials you spend on average.
-
Time-based JIT: This is another variant of resource-based JIT. Instead of focusing on how much each employee costs, you focus on how long it takes to complete the project.
-
Quality-based JIT is another variant of resource-based JIT. Instead of thinking about how much each employee costs or how long it takes to manufacture something, you think about how good the quality of your product is.
-
Value-based JIT is the newest form of JIT. In this scenario, you're not concerned about how products perform or whether customers expect them to meet their expectations. Instead, your goal is to add value to the market.
-
Stock-based is an inventory-based system that measures the number of items produced at any given moment. This method is useful when you want to increase production while decreasing inventory.
-
Just-in-time planning (JIT): This is a combination JIT and supply-chain management. It's the process of scheduling delivery of components immediately after they are ordered. It is essential because it reduces lead-times and increases throughput.