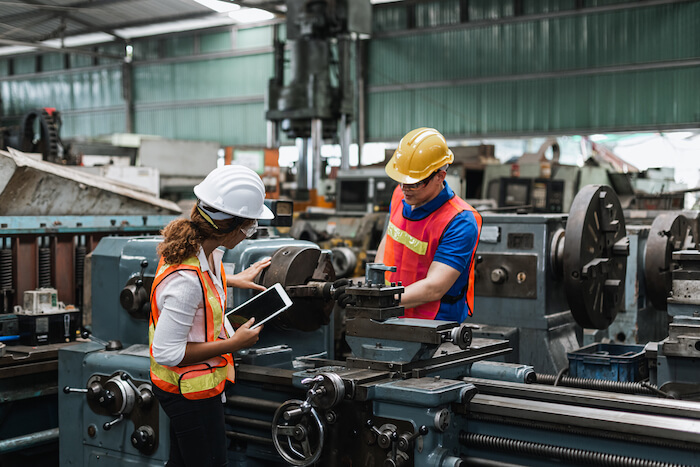
Los Angeles logistics jobs range from small courier projects to large warehouse projects. Your team will work together to ensure your shipments are delivered on time.
Find the best supply chain and logistics companies in your area with GoodFirms.
Using our database and extensive research, we'll help narrow down Los Angeles supply chains and logistics providers. Our team will tell you what companies to steer clear of.
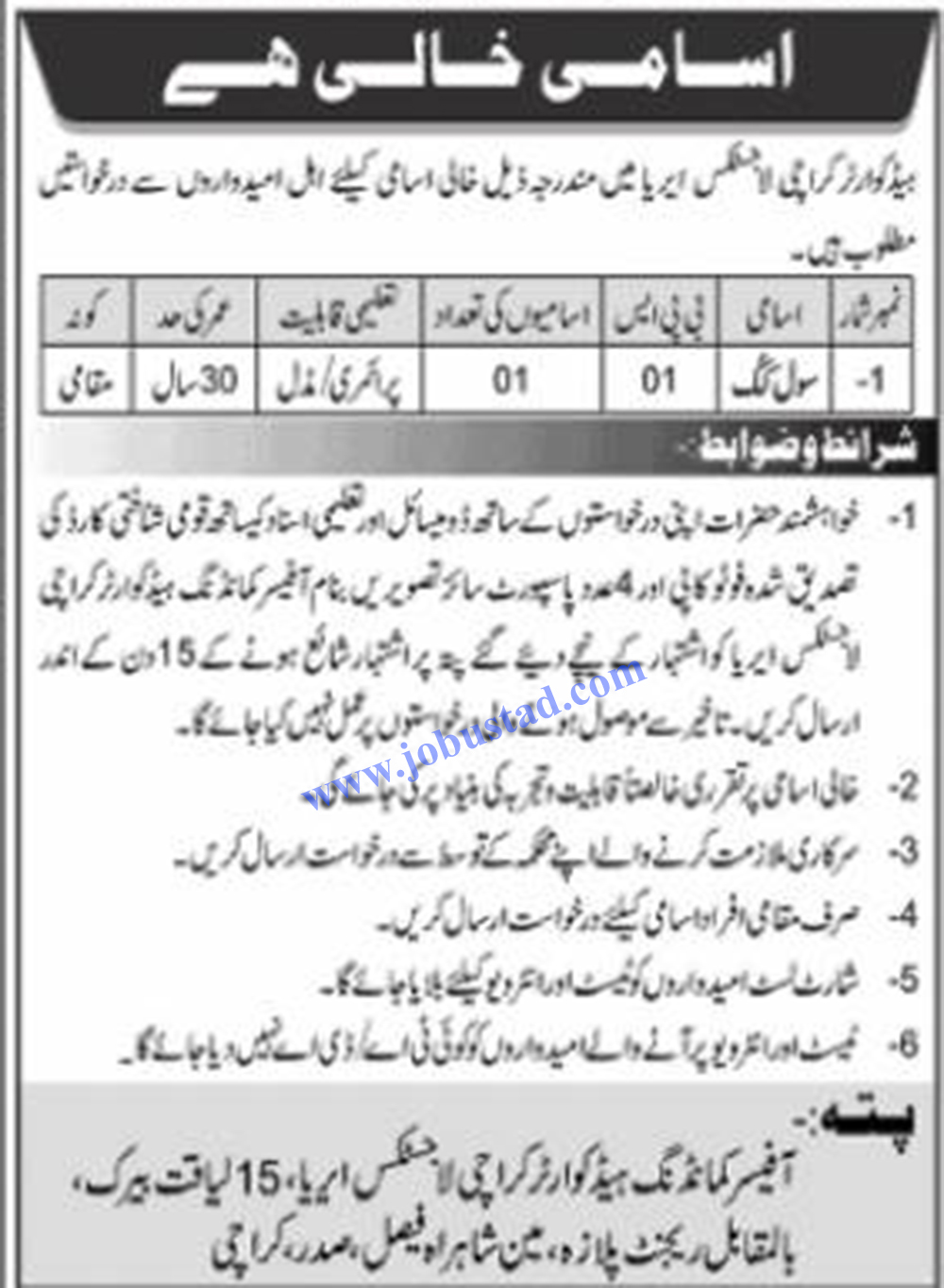
Optimum Supply Chain Recruiters is your one-stop shop for logistics and supply chain recruitment in Los Angeles. If you need a VP in Logistics or an experienced sales representative to fill a position, our team will connect you with the best candidate.
Top-rated Los Angeles Logistics Company
We design and operate global supply chains and logistics solutions as a leading 3PL provider. Our services cover shipment consolidation, deconsolidation and global freight, customs and warehouse management.
Logistics & Shipping Specialist Jobs Los Angeles, CA
We have thousands of job vacancies available for warehouse staff, logistics managers and logisticians. Our free job board features the most recent openings within the transportation and logistic industry. We're proud to partner with the top employers in the country and are dedicated to finding you the best possible job.
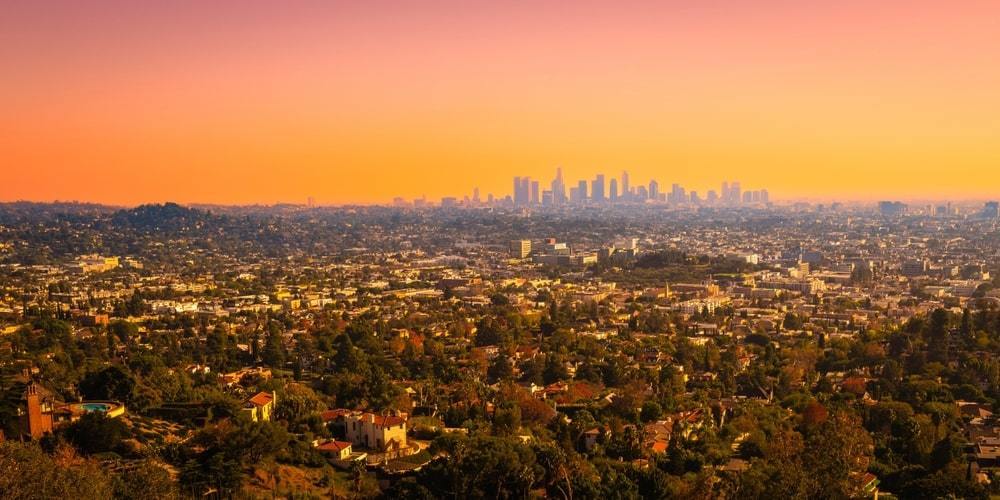
Los Angeles, CA: Logistics Manager
Los Angeles' average salary for a Logistics Manager is $57K. There are 1,240 logistic manager jobs available in the city. However, to stand out you'll need an unique set of abilities. The most impressive logistic managers are those who are meticulous and have a passion for their team. Along with a proven track record, you must have leadership, problem-solving and customer service skills.
FAQ
What are the 7 Rs of logistics.
The acronym 7Rs of Logistics refers to the seven core principles of logistics management. It was developed by International Association of Business Logisticians (IABL), and published as part of their "Seven Principles of Logistics Management Series" in 2004.
The acronym is composed of the following letters.
-
Responsible - ensure that all actions taken are within legal requirements and are not harmful to others.
-
Reliable - You can have confidence that you will fulfill your promises.
-
It is reasonable to use resources efficiently and not waste them.
-
Realistic – Consider all aspects, including cost-effectiveness as well as environmental impact.
-
Respectful - show respect and treat others fairly and fairly
-
Be resourceful: Look for opportunities to save money or increase productivity.
-
Recognizable is a company that provides customers with value-added solutions.
How does a Production Planner differ from a Project Manager?
The difference between a product planner and project manager is that a planer is typically the one who organizes and plans the entire project. A production planner, however, is mostly involved in the planning stages.
What is production planning?
Production Planning refers to the development of a plan for every aspect of production. It is important to have everything ready and planned before you start shooting. This document should include information about how to achieve the best results on-set. This includes shooting schedules, locations, cast lists, crew details, and equipment requirements.
First, you need to plan what you want to film. You may have already decided where you would like to shoot, or maybe there are specific locations or sets that you want to use. Once you have determined your scenes and locations, it is time to start figuring out the elements that you will need for each scene. For example, you might decide that you need a car but don't know exactly what model you want. If this is the case, you might start searching online for car models and then narrow your options by selecting from different makes.
Once you have found the right car, you can start thinking about extras. You might need to have people in the front seats. You might also need someone to help you get around the back. Maybe you'd like to change the interior from black to a white color. These questions will help guide you in determining the ideal look and feel for your car. It is also worth considering the types of shots that you wish to take. Do you want to film close-ups, or wider angles? Maybe you want to show your engine or the steering wheel. These factors will help you determine which car style you want to film.
Once you have made all the necessary decisions, you can start to create a schedule. You can use a schedule to determine when and where you need it to be shot. The schedule will show you when to get there, what time to leave, and when to return home. This way, everyone knows what they need to do and when. You can also make sure to book extra staff in advance if you have to hire them. There is no point in hiring someone who won't turn up because you didn't let him know.
Also, consider how many days you will be filming your schedule. Some projects take only a few days while others can last several weeks. While creating your schedule, it is important to remember whether you will require more than one shot per day. Multiplying takes in the same area will result both in increased costs and a longer time. It's better to be safe than sorry and shoot less takes if you're not certain whether you need more takes.
Another important aspect of production planning is setting budgets. Setting a realistic budget is essential as it will allow you to work within your means. Keep in mind that you can always reduce your budget if you face unexpected difficulties. It is important to not overestimate how much you will spend. If you underestimate how much something costs, you'll have less money to pay for other items.
Production planning is a detailed process. But, once you understand the workings of everything, it becomes easier for future projects to be planned.
What is the responsibility of a logistics manager?
Logistics managers are responsible for ensuring that all goods arrive in perfect condition and on time. This is done using his/her knowledge of the company's products. He/she should ensure that sufficient stock is available in order to meet customer demand.
Statistics
- (2:04) MTO is a production technique wherein products are customized according to customer specifications, and production only starts after an order is received. (oracle.com)
- [54][55] These are the top 50 countries by the total value of manufacturing output in US dollars for its noted year according to World Bank.[56] (en.wikipedia.org)
- Many factories witnessed a 30% increase in output due to the shift to electric motors. (en.wikipedia.org)
- You can multiply the result by 100 to get the total percent of monthly overhead. (investopedia.com)
- According to a Statista study, U.S. businesses spent $1.63 trillion on logistics in 2019, moving goods from origin to end user through various supply chain network segments. (netsuite.com)
External Links
How To
Six Sigma: How to Use it in Manufacturing
Six Sigma can be described as "the use of statistical process control (SPC), techniques to achieve continuous improvement." Motorola's Quality Improvement Department developed it at their Tokyo plant in Japan in 1986. Six Sigma's main goal is to improve process quality by standardizing processes and eliminating defects. Many companies have adopted Six Sigma in recent years because they believe that there are no perfect products and services. Six Sigma's main objective is to reduce variations from the production average. This means that you can take a sample from your product and then compare its performance to the average to find out how often the process differs from the norm. If this deviation is too big, you know something needs fixing.
Understanding how your business' variability is a key step towards Six Sigma implementation is the first. Once you have this understanding, you will need to identify sources and causes of variation. You'll also want to determine whether these variations are random or systematic. Random variations happen when people make errors; systematic variations are caused externally. For example, if you're making widgets, and some of them fall off the assembly line, those would be considered random variations. However, if you notice that every time you assemble a widget, it always falls apart at exactly the same place, then that would be a systematic problem.
After identifying the problem areas, you will need to devise solutions. It might mean changing the way you do business or redesigning it entirely. Once you have implemented the changes, it is important to test them again to ensure they work. If they didn't work, then you'll need to go back to the drawing board and come up with another plan.