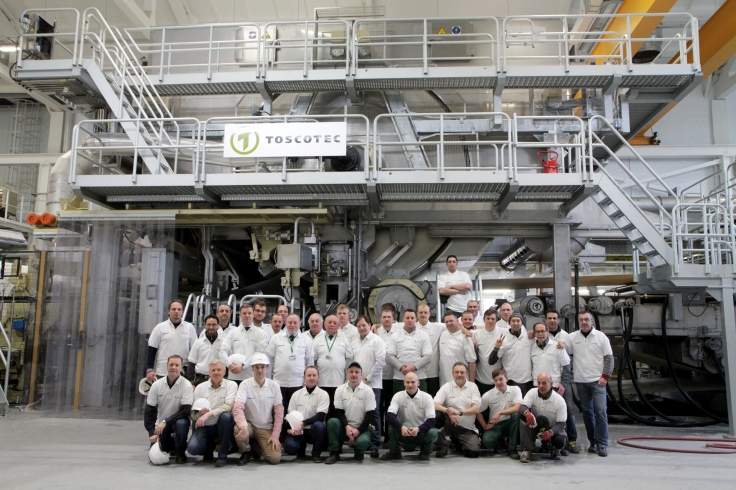
Planning demand is the process of predicting what future demand will be for a particular product or service. It's a crucial part of managing the supply chain as it helps companies meet their customer's needs, while also maximising profit and efficiency.
What Is Demand Planning?
To forecast demand for a product or service, data is analyzed, including sales information and inventory information. It's a complex task that may involve multiple departments.
What is a demand planner?
A demand planner works as part of an organization's supply-chain team. This person uses his or her knowledge of the industry to predict market trends. Then, they create a demand strategy that includes the ideal inventory levels, shipping deadlines, and steps needed to meet demand.
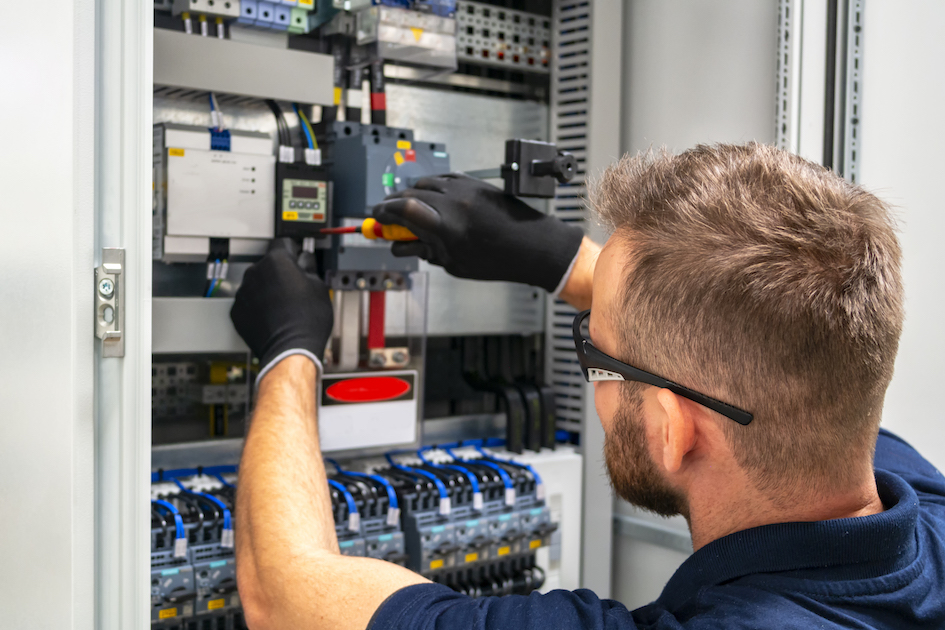
What Are the Best Tools for Demand Planning?
The most efficient demand planning tools provide full visibility of the company's supply chain. This allows demand planners to analyze and track demand in real-time.
How can I predict demand the most accurately?
Analyzing sales data that is provided by sales teams is one way to predict the demand. These data can be used to pinpoint any problems that your sales team may have with their clients, which might lead to changes in demand planning.
Another method is to use statistical analysis to determine the relationships between sales and inventory. Using analytics to find these relationships can significantly improve the accuracy of a demand plan.
What Are the Most Common Pitfalls of Demand Planning?
Demand planning can be a daunting task, as it requires a lot of time and effort to get right. If your demand plan is inaccurate, a lot of things can go wrong, such as excess inventory which locks up working capital and increases inventory carrying costs. This can lead to a loss in money for the company or negatively impact its customers.
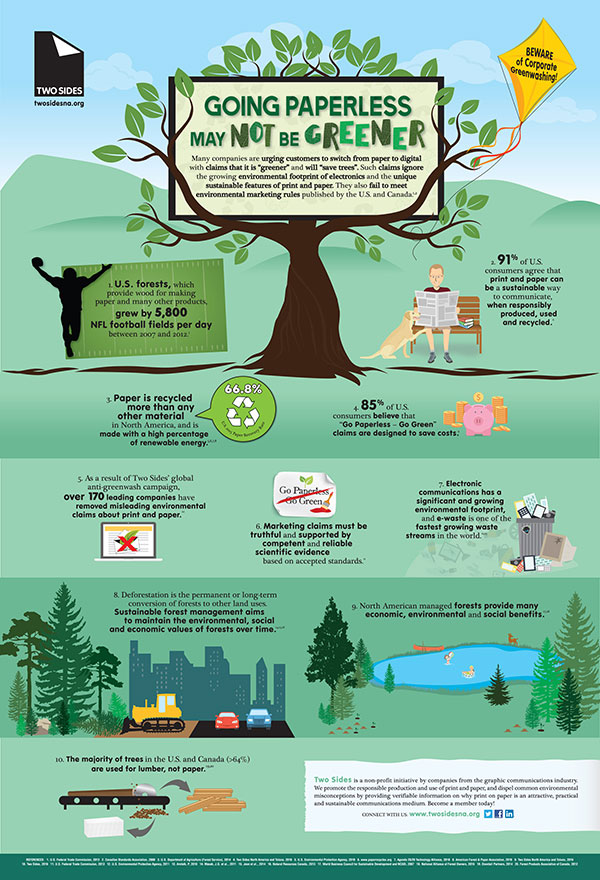
What Are Some Common Skills That a Demand Planner Needs?
A demand planer must have solid analytical and management skills. They must be able analyze large data sets, and then make informed decisions. Also, they should be able work with other people and reach consensus.
What Are Some of the Most Valuable Skills in Demand Planning?
A great demand planner should be skilled with both people and technology. As they will be working closely with different teams on developing a forecasting tool, they should be able effectively communicate with them.
In addition to analyzing a wide range of statistical data, a demand planner should be skilled with the Delphi method, which allows them to solicit feedback from outside experts or facilitators who are not inside the company. This method is particularly useful when limited data are available and you want to hear more opinions on a certain issue.
FAQ
What is the difference between a production planner and a project manager?
The major difference between a Production Planner and a Project Manager is that a Project Manager is often the person responsible for organizing and planning the entire project. While a Production Planner is involved mainly in the planning stage,
What is the difference between manufacturing and logistics
Manufacturing refers the process of producing goods from raw materials through machines and processes. Logistics manages all aspects of the supply chain, including procurement, production planning and distribution, inventory control, transportation, customer service, and transport. Logistics and manufacturing are often referred to as one thing. It encompasses both the creation of products and their delivery to customers.
What is the role of a production manager?
Production planners make sure that every aspect of the project is delivered on-time, within budget, and within schedule. They also ensure the quality of the product and service meets the client's requirements.
What jobs are available in logistics?
There are different kinds of jobs available in logistics. These are some of the jobs available in logistics:
-
Warehouse workers - They load trucks and pallets.
-
Transportation drivers – They drive trucks or trailers to transport goods and perform pick-ups.
-
Freight handlers – They sort and package freight at warehouses.
-
Inventory managers - These are responsible for overseeing the stock of goods in warehouses.
-
Sales representatives - They sell products to customers.
-
Logistics coordinators – They plan and coordinate logistics operations.
-
Purchasing agents - They buy goods and services that are necessary for company operations.
-
Customer service representatives - They answer calls and emails from customers.
-
Shipping clerks: They process shipping requests and issue bills.
-
Order fillers - They fill orders based on what is ordered and shipped.
-
Quality control inspectors are responsible for inspecting incoming and outgoing products looking for defects.
-
Others - There are many other types of jobs available in logistics, such as transportation supervisors, cargo specialists, etc.
What is the difference between Production Planning and Scheduling?
Production Planning (PP), also known as forecasting and identifying production capacities, is the process that determines what product needs to be produced at any particular time. This is done through forecasting demand and identifying production capacities.
Scheduling is the process of assigning specific dates to tasks so they can be completed within the specified timeframe.
What are the four types of manufacturing?
Manufacturing is the process by which raw materials are transformed into useful products through machines and processes. It includes many different activities like designing, building and testing, packaging, shipping and selling, as well as servicing.
Statistics
- (2:04) MTO is a production technique wherein products are customized according to customer specifications, and production only starts after an order is received. (oracle.com)
- [54][55] These are the top 50 countries by the total value of manufacturing output in US dollars for its noted year according to World Bank.[56] (en.wikipedia.org)
- According to a Statista study, U.S. businesses spent $1.63 trillion on logistics in 2019, moving goods from origin to end user through various supply chain network segments. (netsuite.com)
- It's estimated that 10.8% of the U.S. GDP in 2020 was contributed to manufacturing. (investopedia.com)
- In the United States, for example, manufacturing makes up 15% of the economic output. (twi-global.com)
External Links
How To
How to Use 5S to Increase Productivity in Manufacturing
5S stands as "Sort", Set In Order", Standardize", Separate" and "Store". The 5S methodology was developed at Toyota Motor Corporation in 1954. It assists companies in improving their work environments and achieving higher efficiency.
This approach aims to standardize production procedures, making them predictable, repeatable, and easily measurable. This means that tasks such as cleaning, sorting, storing, packing, and labeling are performed daily. This knowledge allows workers to be more efficient in their work because they are aware of what to expect.
Implementing 5S requires five steps. These are Sort, Set In Order, Standardize. Separate. And Store. Each step involves a different action which leads to increased efficiency. You can make it easy for people to find things later by sorting them. When you arrange items, you place them together. Then, after you separate your inventory into groups, you store those groups in containers that are easy to access. Finally, label all containers correctly.
Employees must be able to critically examine their work practices. Employees should understand why they do the tasks they do, and then decide if there are better ways to accomplish them. To implement the 5S system, employees must acquire new skills and techniques.
The 5S method not only increases efficiency but also boosts morale and teamwork. As they begin to see improvements, they feel motivated to continue working towards the goal of achieving higher levels of efficiency.