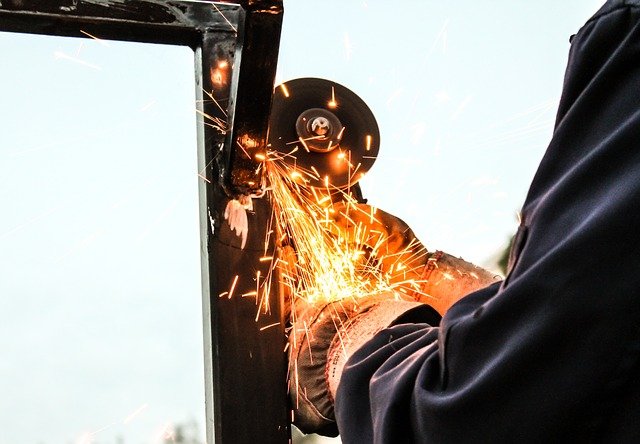
Among all the jobs in the health care industry, biochemist salaries are the highest, at $84,365. These professionals are involved in research into drugs and how they impact organisms. They also develop new chemical compounds and formulations. They might work for a company or teach at a college.
Biochemists have different education requirements depending on their job. Most employers require candidates to have an advanced degree. Some companies will only require a bachelor's. A master's degree might be required for positions in biophysics. This is the study and analysis of biological phenomena and laws.
Biochemists research new chemical compounds, and create them. They also devise quality control methods for materials. Biochemists often collaborate with biophysicists. They study the relationship between physical laws, biological phenomena, and how they relate to each other. They may also be associated with chemical biologists, who are responsible to prepare samples and develop medicinal-chemistry strategies.

Biochemists can work in either the pharmaceutical or manufacturing industries. Pfizer and GlaxoSmithkline are the top employers. These companies have high salaries and it can be difficult for employees to get jobs. Genentech and other companies are difficult to secure even though the salaries are comparable. Eurofins, Siemens Healthineers, and other companies have 10 openings for biochemists.
A biochemist could also work as a faculty member in a college. These professionals educate students about biology, and other organisms. The restoration of the environment may also be a concern for biochemists. They may develop new chemical compounds or formulations to address environmental problems. Biochemists also may study the effects that hormones and other drugs have on living organisms.
Many biochemists advocate the study of biochemistry. Advocates could be awarded degrees from Western Illinois University or Kean University. They may also get internships at research laboratories. These internships are a great opportunity to meet people in the field and get practical experience. They can then apply for positions as research associates or lecturers.
Biochemists often have a master's degree and a PhD. These degrees are necessary for entry-level biochemistry positions. If a biochemist does not have a college degree, they may need to obtain a license. Licenses may be required for positions that involve direct contact with patients. For some positions, such as those of a medical assistant, a license may be required. These positions might be part of a small group, but there may be opportunities for advancement.
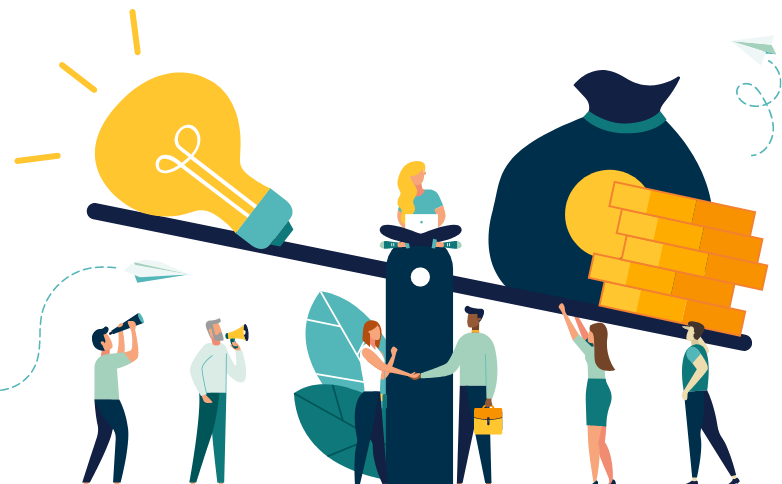
The salaries of biochemists can be very varied. The median annual salary is $76,806 with an average salary of $95,998. Biochemists are paid a salary that is expected to rise by 2020. Pfizer and Eurofins are some of the most prominent employers in the healthcare industry. Amgen, Amgen, and Eurofins all pay high salaries. GlaxoSmithkline is another employer that pays biochemist salaries that are comparable with those of other professionals.
Some biochemists work in pharma companies as chemical biologists. They analyze and report on samples. They also oversee lab operations. These individuals have strong experimental skills and must be able to prepare samples and present findings to stakeholders.
FAQ
How can we improve manufacturing efficiency?
First, determine which factors have the greatest impact on production time. We then need to figure out how to improve these variables. If you don't know where to start, then think about which factor(s) have the biggest impact on production time. Once you've identified them, try to find solutions for each of those factors.
How can manufacturing prevent production bottlenecks?
You can avoid bottlenecks in production by making sure that everything runs smoothly throughout the production cycle, from the moment you receive an order to the moment the product is shipped.
This includes planning to meet capacity requirements and quality control.
This can be done by using continuous improvement techniques, such as Six Sigma.
Six Sigma is a management system used to improve quality and reduce waste in every aspect of your organization.
It seeks to eliminate variation and create consistency in your work.
What are the four types in manufacturing?
Manufacturing refers to the transformation of raw materials into useful products by using machines and processes. Manufacturing can include many activities such as designing and building, testing, packaging shipping, selling, servicing, and other related activities.
What is meant by manufacturing industries?
Manufacturing Industries are businesses that produce products for sale. Consumers are the people who purchase these products. These companies use various processes such as production, distribution, retailing, management, etc., to fulfill this purpose. They produce goods from raw materials by using machines and other machinery. This includes all types of manufactured goods, including food items, clothing, building supplies, furniture, toys, electronics, tools, machinery, vehicles, pharmaceuticals, medical devices, chemicals, and many others.
How can I find out more about manufacturing?
Hands-on experience is the best way to learn more about manufacturing. However, if that's not possible, you can always read books or watch educational videos.
Statistics
- Job #1 is delivering the ordered product according to specifications: color, size, brand, and quantity. (netsuite.com)
- According to the United Nations Industrial Development Organization (UNIDO), China is the top manufacturer worldwide by 2019 output, producing 28.7% of the total global manufacturing output, followed by the United States, Japan, Germany, and India.[52][53] (en.wikipedia.org)
- It's estimated that 10.8% of the U.S. GDP in 2020 was contributed to manufacturing. (investopedia.com)
- Many factories witnessed a 30% increase in output due to the shift to electric motors. (en.wikipedia.org)
- [54][55] These are the top 50 countries by the total value of manufacturing output in US dollars for its noted year according to World Bank.[56] (en.wikipedia.org)
External Links
How To
How to Use the Just In Time Method in Production
Just-intime (JIT), which is a method to minimize costs and maximize efficiency in business process, is one way. It is a process where you get the right amount of resources at the right moment when they are needed. This means that your only pay for the resources you actually use. The term was first coined by Frederick Taylor, who developed his theory while working as a foreman in the early 1900s. After observing how workers were paid overtime for late work, he realized that overtime was a common practice. He realized that workers should have enough time to complete their jobs before they begin work. This would help increase productivity.
JIT is an acronym that means you need to plan ahead so you don’t waste your money. The entire project should be looked at from start to finish. You need to ensure you have enough resources to tackle any issues that might arise. If you expect problems to arise, you will be able to provide the necessary equipment and personnel to address them. You won't have to pay more for unnecessary items.
There are many JIT methods.
-
Demand-driven: This JIT is where you place regular orders for the parts/materials that are needed for your project. This will allow to track how much material has been used up. It will also allow you to predict how long it takes to produce more.
-
Inventory-based: This is a type where you stock the materials required for your projects in advance. This allows one to predict how much they will sell.
-
Project-driven: This approach involves setting aside sufficient funds to cover your project's costs. Once you have an idea of how much material you will need, you can purchase the necessary materials.
-
Resource-based: This is the most common form of JIT. You allocate resources based on the demand. For example, if there is a lot of work coming in, you will have more people assigned to them. If you don't receive many orders, then you'll assign fewer employees to handle the load.
-
Cost-based: This is a similar approach to resource-based but you are not only concerned with how many people you have, but also how much each one costs.
-
Price-based: This approach is very similar to the cost-based method except that you don't look at individual workers costs but the total cost of the company.
-
Material-based - This is a variant of cost-based. But instead of looking at the total company cost, you focus on how much raw material you spend per year.
-
Time-based: This is another variation of resource-based JIT. Instead of focusing solely on the amount each employee costs, focus on how long it takes for the project to be completed.
-
Quality-based: This is yet another variation of resource-based JIT. Instead of focusing on the cost of each worker or how long it takes, think about how high quality your product is.
-
Value-based JIT : This is the newest type of JIT. In this scenario, you're not concerned about how products perform or whether customers expect them to meet their expectations. Instead, your goal is to add value to the market.
-
Stock-based is an inventory-based system that measures the number of items produced at any given moment. It is used when production goals are met while inventory is kept to a minimum.
-
Just-in time (JIT), planning: This is a combination JIT/supply chain management. It is the process that schedules the delivery of components within a short time of their order. It's important as it reduces leadtimes and increases throughput.